Unsafe Guardrail Post

Balcony on my new construction is getting finished up. They completed the railing this past weekend, so my wife and I went up to check it out. Got up there, leaned lightly against the railing, and the railing and post moved. I then wiggled it some with my hand (see video https://photos.app.goo.gl/W1V4yUfDbQxZxkLaA). It gives a good 1-2″ I’d guess with very lightly applied pressure. The decking is Trex, and there is a rain collection system (the name has escaped me) underneath the Trex that drapes over the joists and funnels water out of a gutter to keep the front porch underneath dry.
How are the guard rails attached you ask? Well, there is a Simpson Strong-Tie of some sort (can’t tell exactly which one) attached to the Trex decking, which the cedar post sits in. The Simpson Strong Tie is attached to the cedar post with deck screws (see attached image). What else is going on? There is also a MiTek angle bracket to resist lateral forces pushing out on the post. I believe it is the MiTek A3-TZ. It is also fastened with deckmate deck screws. That’s really it. There are two small pieces of cedar that they have fastened over the MiTek bracket on the inside (see red circle in picture 3).
Is it at all safe for the guardrail posts to be top mounted using only the setup shown? I thought they should be attached with a bolt or structural screw (like a Spax PowerLag) to the rim joist. I can’t imagine the current setup holding the weight of a 300# person tripping and falling into the railing (not likely, but also should hold up to it).
When I talked to my builder this afternoon, he says that they were mounted this way in order to keep from puncturing the water collection system (which implies to me that the screws in the angle brackets are pretty short). The only options he really gave me were to leave it as is (and in his words “watch your kids when you’re out there.”) or to use a longer screw (I asked if he meant something like the Powerlag and he didn’t specify) in the angle bracket to screw into the joist. Is this sufficient for a top mounted post like this? Advice greatly appreciated since this is a safety issue.
GBA Detail Library
A collection of one thousand construction details organized by climate and house part
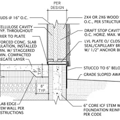
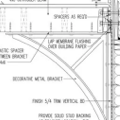
Replies
Matt,
No that doesn't meet the lateral resistance requirements of any building codes I'm aware of, and not wanting to puncture the waterproofing is no excuse. The attached link shows what meets the IRC for deck post attachments on page 19. https://www.awc.org/pdf/codes-standards/publications/dca/AWC-DCA62015-DeckGuide-1804.pdf
Thanks, Malcolm. That is helpful.
The posts for the railing need to tie into the framing. They should feel like solid pieces of the structure if you lean on them, not really moving at all. The way your builder did it, the entire length of the post is acting as a big lever on those screws. Ever use a hammer to pull out a nail? Imagine how much easier it would be with a 4 foot long handle on the hammer. That will give you an idea of what that post is doing to those screws, and the screws will NOT hold if a few people lean into, or fall against, that railing.
As Malcolm mentioned, trying to avoid puncturing the waterproofing is no excuse. Framing goes in first, then water proofing goes around that. You never compromise structural integrity for any reason, structural safety is always first, everything else is secondary.
Bill
Thanks for the feedback. I'm a physicist/engineer by trade, so have a pretty good understanding of what's going on. But am not a builder (just a savvy consumer? Ha), so wanted to run it by the knowledgeable folks here before I really pressed the builder. The whole build process has felt like a series of events like this.
We are in the county, so there are no inspections and I have often felt like it is on me to catch things like this. And that's ok occasionally, but it shouldn't happen regularly, and I don't feel like when I bring it up I should get a "you can leave it and just watch your kids when you're out there" response. A big lawsuit waiting to happen if someone goes off a balcony railing.
If that is how the posts are attached I would also be worried about the structure of the deck. Is it tied properly into the structure of the house? Proper flashing to prevent rot of the rim board and ledger?
This is a good read:
https://www.nachi.org/deck-inspections.htm
There are some deck mount post attachments that might work in your case. These still require a fair bit of structural lumber underneath which might be hard to add if the rainscape channels are already installed.
Thanks for the resource, Akos. Reading through it right now. Your comment about worrying about the structure of the deck is exactly what I told my wife when we found the posts that way over the weekend. It made me go back and look at some of the pictures I took back at that stage of construction. I'm attaching one (I don't have a ton of pictures of it). I've circled one area that stood out to me in one of the pictures. Toward the corner of the picture I've circled an area where there is a butt joint in the rim joist about 6-10" left of the post. Is that ok?
I've attached a second picture that is one of the better ones I have (maybe my wife has more on her phone) of the balcony during framing. Appears all band joists are attached w/nails to the 4x4 post in each corner. Is that standard or should the post be notched and the band on the post?
Thanks for taking time to answer. There are some things dealing w/the performance of the house (insulation, air sealing, etc) that I can let go if not done perfectly. But, I'd prefer not to sacrifice my family's safety.
Looking more closely at the pictures, it looks like the band joists (or is the proper word girder?) are also fastened with nails only. Should there be some sort of bolt, lag screw, or structural screw (like a Spax powerlag)?
Sorry you're having to deal with all of this, but your background should make it somewhat easy to understand the severity of the situation.
Major problems from these latest photos:
1. There are no joist hangers. Looks like the joists are toe nailed (and there's some 2x2ish thing on the ledger side). Yea, not acceptable. Maybe they were installed after the fact, but the presence of that 2x2 makes me think this was intentional.
2. I see no hardware to laterally connect the deck to the house. Particularly without joist hangers, you run the risk of that whole assembly pulling away from the house. To visualize, think of people running out the house onto the deck and loading the deck in the direction of their running. It's going to create tension at the joist/ledger intersection and a moment about the post footings. No way the post and its footings will resist that moment, so the tension needs to be resisted at the joist/house intersection or the whole deck will fly away. This is not a crazy scenario. Many decks have failed this way which is why the code now requires such ties. The higher the deck, the more reason this is needed.
Thanks, Patrick. Yeah, I have a pretty good understanding of the physics of it. At the point in the build when the balcony was getting framed, I hadn't lost total confidence in the quality of the work that was being done generally, and so honestly didn't pay a massive amount of attention at the time. I'm going through my old pictures and my wife's to see if I have any better pictures, or ones from the end of framing. I'm attaching another one I dug up that shows a view from the side (same day as the previous images).
I assume you mean in point 2 above (no hardware to laterally connect deck to house), you mean that there should be some sort of hangar/hardware that connects the rim joist to the ledger board? If you look at the picture on this post, it looks to me like the only connect between the rim joist and the ledger board are nails shot into the ledger.
Ok...here's a picture from after the decking went on (but before they put the ceiling on underneath) w/no joist hangars. And a screenshot from directly underneath from a video that I accidentally took (sadly the video itself is of no use).
Matt,
That looks like an awfully long span for a 2 ply beam made from dimensional lumber.
The more I look at this, the more concerned I get. All of my previous comments still apply. Now let's turn our attention to the piece of wood that the joists land on away from the house. For the sake of disambiguation, we'll call that the flush beam. In a typical design, that flush beam would have bearing directly on posts. If that beam is instead through fastened to the posts, that connection needs to be adequate to support the loads and is much less common than the beam simply resting on the posts.
Similar to the ledger side, all the joists should have hangers onto the flush beam. The flush beam should not have a random splice in it mere inches from a support post.
In the second picture it looks like there is a bolt head with washer between every joist. So long as those bolts go into something appropriate on the other side of the sheathing that looks OK.
There is a bolt/washer on the ledger between each joist.
It's somewhat hard to track what's being responded to what here, but just want to call out that the ledger being laterally attached to the house *is not* [typically] sufficient attachment for the whole assembly.
The prescriptive solutions rely on attachments from joists to the house with no intermediary connection. See here for Simpson hardware examples: https://embed.widencdn.net/pdf/plus/ssttoolbox/z4eaffenlu/T-C-DECKLAT21.pdf?u=cjmyin
Typical solutions are two 1,500 lb connectors or four 750 lb connectors.
*Theoretically*, one could meet the lateral requirements by tying the ledger to the house and then the joists to the ledger, but this would have to be designed and stamped by an engineer. Joist hangers are not typically used to be loaded in tension.
DC,
Hard to say. Bolting the ledger to the rim-joist isn't sufficient to meet lateral load requirements in the IRC. It needs to be tied back to the joists.
Page 18 in this link: https://www.awc.org/pdf/codes-standards/publications/dca/AWC-DCA62015-DeckGuide-1804.pdf
If they put the deck together and then put the joist hangers on, the 2x2 could just be to hold the joists up temporarily. It's so ridiculously undersized I hope that is the case.
As I look through pictures, I'm pretty sure there are no joist hangars. I highly doubt they would've put joist hangars on after the rain catchment system was up. Shouldn't there be joist hangars for the joists both at the ledger and at the rim joist?
A lot of times guys will nail a deck together and then come back with reinforcements, so it's hard to tell from progress pictures. But framing that relies solely on nails isn't kosher. The joists should have joist hangers and the rim joist should be attached to the post with through bolts.
Then you have to ask if all of the framing members are sized properly, if the deck is properly attached to the house and flashed, and whether the posts have appropriate footings.
Decks are deceptively complicated.
Think of nails as fasteners that keep wood in position, but don't take load themselves. An example is nails keeping studs in place on the top and bottom plates of a wall, but the top and bottom plates REST ON the stud, so vertical load doesn't get carried by the nails, vertical load is the wood setting on the next piece of wood.
You have nails carrying load in shear here, that's a Bad Thing. Bolts would be better (there are tables for how many and what size bolts you need for a given load), but best is a proper hanger or a notch the beam rests in on the post (or sits on top of the post).
Based on the things you've shown so far, I would be VERY CONCERNED about the ledger connection where the joist ties into the wall. This is a classic place for balconies to fail and detach from the structure, and many people have been seriously injured from that type of failure. One thing I would double check is that the ledger should NOT be tied through any kind of insulation -- it should be bolted directly to structural materials. In my own home, during a renovation, I found a ledger-type connection for a roof tied through 1/2" polyiso by nothing more than a bunch of nails. ALL of the nails were bending in shear, it was dangerous. I had to engineer a fix by bolting in a piece of steel angle to create a sort of linear hanger.
If your crew is cutting corners due to no inspection, that's a really bad thing. The code is there for safety reasons, and even if you're not being inspected, you really should still follow code for your own safety. There are a lot of errors here, many of them classic "this is why the deck failed at the party" kinds of problems. I just noticed no joist hangers too. Scary stuff.
Bill
Thanks, Bill. I think I understand well what you're getting at here. At the ledger, with no joist hangars, the joists are connected to the ledger only with framing nails toe nailed to the ledger board. Even if the ledger is bolted securely, framing nails aren't sufficient to provide resistance to lateral forces exerted on the joists and can lead to the balcony pulling away from the wall.
On the side away from the house, there are two major issues. First, the joists are (again) toe-nailed to the band/girder (Or as Patrick called it, the "flush beam"). The second problem is the spliced piece through fastened to the corner post with 4 nails and then fastened to a 2-ply beam with 4 nails. This means that all load transferred to that 2-ply beam is then being carried by those 4 nails that the spliced end piece is fastened to it by.
Do you have any suggestions on the best way to approach this issue with my builder? I think I understand (generally) how things should've been done and understand (at least the physics) of the issues with the way it currently is. I suspect he'll say, "it's fine, we always do it that way" or "it'll be a lot of work to get back in there and fix it." Like I said in another post, I don't want to put my family (or guests) at risk.
> At the ledger, with no joist hangars, the joists are connected to the ledger only with framing nails toe nailed to the ledger board. Even if the ledger is bolted securely, framing nails aren't sufficient to provide resistance to lateral forces exerted on the joists and can lead to the balcony pulling away from the wall.
To be clear, the current attachment method suffers from both insufficient resistance to lateral loads but also insufficient resistance to gravity imposed dead and live loads. Hangers are meant to transfer the dead and live loads to the ledger. Lateral connectors are meant to transfer the lateral load to the more stationary framing of the whole house.
>"it's fine, we always do it that way" or "it'll be a lot of work to get back in there and fix it."
I work as a consulting engineer on specialized electrical systems (critical facilities like datacenters and telecommunications sites). A lot of my work is fixing things that someone "always did that way" that failed, or things that "would be too hard to fix" that failed. Many times the failure involves fire. Often much fire.
In your case, the failure could kill someone. Structural failures can and do kill people, and balcony failures are probably the most common type of residential structure that fails -- usually at a party with a lot of people on the deck. DO NOT TAKE CHANCES HERE.
I think one of the reasons for all the posts on your thread in a very short period of time is that there are a lot of professionals on here, and safety issues jump out at us so you get a "WHOA! STOP!" kind of response. You need to get these issues corrected. Talk to your builder, if you have to you can always get an engineer to come out and come up with a solution (although that will cost money). For those 4x4 columns, you might be able to build them out with 2x4 and/or 2x6 members to make the column bigger in an architectural detail style, but also provide a solid piece of framing for the beam to rest on. The ledger is much more complex, and we'd need to see more to know how to deal with that one.
To come up with a good fix, you really need someone who knows what they are doing to come out and look at the site.
Bill
First off, for everyone who has commented. Thanks so much. Not sure exactly how to process through this with the builder at this point. If anyone has advice on the best way to bring these issues up, I'm all ears.
Second, it looks like we've gotten far enough into nested comments that I can't reply to Malcolm and Patrick. So, let me reply here and kind of "reset" the replies.
Replying to Malcolm's Post #17 ("That looks like an awfully long span for a 2 ply beam made from dimensional lumber.") -- The span there is about 16'
Replying to Patrick's Post #18 -- I get what you're saying. I have seen way more balcony's built where the post is notched and the flush beam (to use your term) rests on the notched post. How concerned should I really be about the splice near the support post? Best I can tell from the picture I have there are 3 or 4 nails fastening that spliced piece to the post, and then 3 nails fastening that spliced piece to the other 2 plys of the flush beam. Am I correct in saying that the 2-ply beam spanning from the two posts carries the load that transferred to it from the joists. Then that load is transferred to that tiny little spliced piece near the post?
> Not sure exactly how to process through this with the builder at this point. If anyone has advice on the best way to bring these issues up, I'm all ears.
This is a super tricky thing in an area with no code enforcement. I can tell you right now if I brought this to my local inspector prior to an inspection, they would 100% back me and fail the contractor at inspection time. Then your remedy is clear; the contractor has to fix it.
In the absence of statute mandated inspections, what does your contract say? If it stipulates that construction will follow some standard, a third party should be able to show that this does not. But now we're quickly in confrontation mode. This contractor needs to be made to understand that he's built something substandard and is taking on a liability. Let's remember that this thread started about the railing and he made a comment about being careful around the railing. That's insane! Just to level set: no one should be worried about their kids interacting with a properly built railing.
> How concerned should I really be about the splice near the support post?
If it's a multi-ply beam, I couldn't see a good look at the final product, so it's hard to say. The unfortunate part is these things needn't be complicated, but this particular construction seems to be overly so.
Who drew the plans for the deck/balcony? Does the construction reflect the plans?
I did go back and look at our plans. They do not call for specific fasteners on the balcony (it says things like "ledger bolted minimum 16" o.c. (typical)". The one area that is definitely not per the drawings is the beam (the one you call the "flush beam"). The plans specifically call out (2) 1.75" x 11.25" 2.0E LVLs which they obviously didn't use. So I suppose since the contract states that they will build the house per the plans and specs, that's not per spec.
We've run into the code issue once before on something way more minor (outlet in the kitchen). Electricians left an outlet out that left us with a really long run (~7 ft) on the kitchen counter w/out an outlet. I asked about it. "Electricians couldn't fit one where it was on the plans." I said something to the effect of, "I thought code requires one w/in 2' of a countertop edge, and then every 4' after that?" Got the "you're in the county where there is no code" answer. They did finally get a couple of countertop outlets put in, but it was a battle. Similar things w/HVAC. HVAC sub has been terrible to the point where he refused to install our ERV (long story, search old posts by me). I ended up finding a separate guy to do the ERV (and he's awesome, wish he would've done the whole system), but the original sub is finishing the HVAC. The guy who did the ventilation has talked me through some things that I should be on the lookout for as the original (bad sub) finished up the HVAC. He said something to me to the effect of, "They think that just b/c they're in the county they can get away with doing work that is substandard. It's not how it should be, but that's how it is a lot of times."
Your balcony has too many issues to simply fix. This is not a case if it will fail, but when. The simplest is to pay an engineer to come on-site, inspect the structure and draw up fixes. Most likely everything will have to come down and be re done.
This will be a bitter pill for contractor, but 2nd floor balcony is not something you can just throw together.
Major issues:
-looks like a single ply spanning between the two columns. The 2nd ply looks to be decorative. I've never seen an engineer spec anything less than a two ply beam. If that is indeed a two ply, than the 2nd ply can't be made from two pieces.
-2ply of 2x12 is not enough to span 16'
-4x4 is not structural lumber (unless stamped, which I've not seen), normally these columns are built from 2x. The columns also seem a undersized.
-columns are not braced to the house. This needs to be done with hardware not just some toe nailed joists.
-beam needs to rest on the post or on hardware, not just nails
-floor joists are notched on the bottom.
Somewhat squishy:
Our code allows for ledger to support floor joists, but I've never head of it being used outdoors. It is asking for trouble as water can sit there, and quickly rot.
Ledger bolts to the house should be staggered, less chance of splitting the ledger.
https://www.jlconline.com/deck-builder/ledger-strips-and-the-code_o
Here is a link talking about the ledger strip that was used for your deck. The ledger strip is not an acceptable alternative to joist hangers.
I w
Posted this below, but thought it was relevant here in light of your link (which I appreciated). On the right hand side, the last 16-20" of the ledger strip appears to be split. I suspect that makes a bad situation worse.
Just to confirm: Are you in an area truly with no building code, even at the state level, or just an area with no local code enforcement?
No local code enforcement
Deleted
If there is state code, you might still have a case that they have to follow it, even if it's not enforced locally. Another things: do your plans or contract reference a specific building code or standards of workmanship?
If they framed with 2x8s instead of 2x12s, to me it sounds like you're already in lawsuit country, to be honest. Your contractor is taking you for a ride.
I agree with all the earlier responses, there are many serious errors in the construction of the deck.
It only makes me wonder about the entire house.
What do the building plans show? any specific details/drawings showing proper construction?
If so, why would the builder deviate from the construction drawings?
Code enforced or not, your builder is a moron or just hot on moonshine.
What sort of details would you expect? Our plans were drawn by a reputable architect and from plans I've seen, we have at least as many construction details on our drawings, and probably more details when it comes to things like wall details.
Why would he deviate from drawings? I wish I knew. Two examples of deviation from our drawings that I know of (and that I didn't bother to challenge too hard at the time). Plans call for 2x12 rafters, they put in 2x8s. When asked about it, they first set the lumber supplier ordered the wrong ones, and the framers just used what was out there since they normally use 2x8s (one of the first of quite a few times I have asked, "But shouldn't you be communicating to the subs things that are different on our house, like 2x12s for the roof?"). Instance number two...our plans call for structural blocking between each rafter at the top plate. The framers also did not do that. I can't remember the reason they gave for it not getting done. Again, in retrospect, I should've pushed harder on that, but didn't because I'm thinking (at the time), "I need to save my bullets for more important things."
"Why would he deviate from drawings?"
Cheap, stupid, lazy, predatory, has bad subs, hasn't looked at the drawings, doesn't care as long as you pay, etc. There are a lot of possible reasons, and none of them are good.
Do you know the lumber company they used? Ask them directly what was ordered. I give good odds the contractor ordered 2x8s because they bid your job too low and lumber prices skyrocketed.
Also, using proper hardware is almost always more expensive than winging it, so if your contractor underbid, that could be why they're skipping joist hangers and proper attachment details.
Our contract is cost plus, so I'm on the hook for materials. No loss to him if he goes over on materials (same with the rafter issue). But yes, none of this is good.
OP isn't the customer of the lumber company. I'd be mad if one of my suppliers shared information about my orders with third parties.
It may vary with the company, but people aren't particularly careful with information like this. If you sound like you deserve the information when you ask, they don't question it. "Hi, I'm OP calling about the order for the roofing lumber for Y contractor at X jobsite. Was the order for 2x8 or 2x12 rafters?"
But my real question is, why should the OP worry about making their contractor mad when the contractor is actively compromising OP's safety?
Matt,
The absence of a specific detail on the drawings or something not being being called out in your contract, still means the builder must default to following the building code. That's non-negotiable. The only way you can deviate from the code is if you instead use alternate details or assemblies stamped by an appropriate engineer.
It's generally not a good idea to cast aspersions of builders based on a few photographs posted on line, but I have no qualms about doing it in this case. Your builder has no idea what they are doing.
> What sort of details would you expect? Our plans were drawn by a reputable architect and from plans I've seen, we have at least as many construction details on our drawings, and probably more details when it comes to things like wall details.
Typically things like beams and ledgers will have detail drawings and fastening schedules.
> Plans call for 2x12 rafters, they put in 2x8s.
So they've either undermined the structural capacity of the roof, or the insulating capacity (if insulation is between rafters rather than between ceiling joists.
My coworker and I actually ran some quick load calcs for the 2x8 rafter and it seemed ok. And since they had already sheathed the roof by time I realized it, I guess I didn't push it (nor do I think they would've). It did cause insulation problems, though. Originally plans called for either all open-cell or 2" closed cell + dense pack cellulose. Well, that wouldn't get us to R38+ (Climate Zone 3). So, solution ended up 5" closed cell + 2.5" open cell. I always wondered whether we actually got 5" of closed cell.
Roofers came in and cut a whole to run the ERV out of (don't ask why it wasn't done earlier....HVAC is a whole other story). They left the piece they cut out sitting in the attic, which I picked up. Looks like I have 2-3" of closed cell w/an average of ~2.5" (see picture).
I have been extremely active in watching the build, bringing up issues, etc. I can't imagine what would happen for folks who aren't actively involved or who don't educate themselves about building.
Also, I found this picture. It appears that the ledger strip is split for the rightmost 16-20".
You've hit on the problem with people making on-the-fly substitutions, they may not know the whole story. Framer looks at the roof and says, "No need for 2x12 rafters, 2x8's will hold fine." And he's right. But he doesn't know that the 2x12's were specced for the desired insulation thickness. And so it causes problems down the road.
Oh, sure. You're right. And I've had that conversation w/my builder throughout the build over some of our high performance features: "Hey, I really need you [the GC] to help synthesize the vision of the build across the different subs. If you don't tell them what they need to do, it's going to affect the next guy down the line." Guess I thought going in, I wouldn't have to have that conversation:-/
Matt,
This is the kind of thing that ends up on the nightly news when it collapses during a party. You need to get this fixed. There are so many things wrong here that frankly would have gone unnoticed (until after it collapsed) if you did not takes those pictures before the trim was put on. Based on the responses your builder has given you so far ("watch your kids when you're out there"), he probably has no intention of fixing it unless he is compelled to. I would suggest you get your architect involved and have him put together a punch list of the issues and the required fixes and then the 3 of you meet to discuss. My guess is he will walk, especially if you don't have a hold-back, but regardless, it needs to fixed by someone.
Matt,
This is a long thread, so maybe I missed this one. Does your contract with the builder include a warranty? Most put in a year.
Yes, a one year warranty, though I don't remember the exact warranty language (it seemed standard boilerplate at the time we signed).
I've been slow to the party, but will pile on anyhow. I have investigated deck failures and they are not pretty. People can get hurt, very bad. Your deck will not support the weight of even a reasonable sized party. As others have said above, the defects are too numerous to even document in a forum like this. The DCA-6 deck guide (link in #19 above) is an excellent reference, and easy to read. Going through it will help you to understand just how far from acceptable this deck is.
Your builder clearly doesn't have a clue and/or doesn't care about your safety. That's never good. Making him fix this will not be easy, and could jeopardize the project. That may or may not be a bad thing, considering. You should go back to your contract to see if there are any codes or quality standards cited. You can also check to see if there are state level codes that must be followed, even in the absence of code enforcement. If you hired the Architect, s/he can be your friend in this. The Architect should know what codes and standards apply by regulation in your county. You should engage the Architect to perform a detailed inspection of the entire project and provide a written report of any significant deviations between the as-built and the plans. They might also be willing to review your photographs taken before things were covered up. This might cost you $1k-$2k, but will be well worth the investment. If the builder hired the Architect, then find an independent Architect or Engineer that specializes in residential construction inspection. If the builder doesn't fix all of the issues, you are in attorney land, unfortunately. This is the sort of thing that you can't just ignore.
Matt,
I would call the builder and explain the issue. He may evade, or he may decide to eliminate his long-term liability. (He may/might pressure the framer to fix this issue on his own dime. That seems to be the way it normally works.) It might be worthwhile to have a structural engineer create a remediation plan to guide the work.
Steve,
Thanks for the input. I tried to set that up this morning. They (builder and his partner) sent me out to talk to the on-site super. I told them I was happy to go explain the problems to the super, but this was a conversation that needed to happen in-person between me and him. I've yet to hear back since then and am currently working on some written documentation outlining not only the balcony problem but other issues (some noted in this thread, like the insulation issues, and others not, like hvac issues that have been ongoing for months). I would prefer to not get into attorney land and would prefer to work it out with the builder. We'll see what happens.
Everyone,
Thanks again for all the input. Today I wrote up a document outlining the balcony and guardrail concerns (and also included a section on hvac, which is a separate issue that's been ongoing). Included figures, references to documents shared here, etc. I had asked for a face-to-face with my builder, but he couldn't do it today. So, I went ahead and sent over the document and asked for a face-to-face.
Builder replied and said we didn't need a face-to-face. Here was the reply:
"Your hvac will be installed how they install it. Not how you read it to be. They have done this for 25+ years. They require the system exactly the way it is.
Your balcony is installed correctly. It has a ban board and ledger. bolted to studs of house. This deck is strong and done correctly."
I have a feeling we're headed towards a parting of ways here based on that reply:-/
That is unfortunate. It is amazing how often this sort of thing happens, how many "builders" just don't have a clue how things should be built, and how resistant they are to learning/change. In unregulated areas, of course, things are even worse.
Have you tried to get the Architect involved yet, or a third party? Builders are far more likely to take advice from a licensed professional than a customer. If an attorney is the only option left, make sure to hire one that has residential construction defect experience. This is a specialty that is not taught at Law School.
Regarding the comment on the HVAC system, that response is basically "you don't know what you're talking about, so we're going to do it how we always do it". That's not the way a competant contractor would respond. A competant contractor would explain WHY they are doing whatever they are doing. I have often told my crews that anyone who won't explain the why probably doesn't know the why, and doesn't want anyone to see that they don't know. There are right and wrong ways to do things, and just because it's been done a particular way for years doesn't make it right.
The balcony has obvious, major, defects. The beam connection to the columns is probably the most obvious, as are the attachments for the posts supporting the railing. Neither is "strong", and neither is "done correctly". Your builder doesn't know what they're doing.
I second Peter's comment about trying to get a professional such as an architect or engineer involved here. If the builder still won't budge, the work of that architect or engineer will be a big help for your lawyer when dealing with the builder on your behalf.
Bill
I don't disagree with Bill's advice, but I think you have to weigh your costs and rewards on this. For example, would it be better to fire the GC or walk away from the house? Would it cost less to accept the house as-is and then hire your own contractor to fix the critical issues?
I've done a couple of projects where my frustration level with the "construction professionals" led me to seek legal advice. Both times I was told that the legal avenue was going to be very expensive and probably unsatisfactory. Even if I prevailed, the other party might not pay. Because I had hired small-time builders/contractors, it would be very easy for them to ignore the payment demands or simply declare bankruptcy and reincorporate (either locally or in another market).
Not sure the picture will look any better if you are dealing with a larger company. While consumer protections may be better where you are located, I suggest doing some research before you have any further conversations with the builder.
I would concur with this. Getting compensation through legal means comes at a huge cost, so unless your potential award is also huge, it doesn't make a lot of sense. I would guess that just tearing the whole deck off and hiring someone else to do it would make more financial sense. He already mentioned the possibility of parting ways with the GC, so if that is an option I'd be looking pretty hard at that. From the response the GC gave, the odds of getting them to do anything properly from this point on seem pretty slim.
All good points. But the OP will still need to protect himself from the builder coming after him for the remainder of the house profits, even if he's thrown off the site. Big caveat here that this is not legal advice and possibly not even relevant in OP's jurisdiction. This is why he needs a lawyer. In my old stomping grounds and several others, once you sign a contract with a builder, he has a legal expectation of earning the profits embedded in that contract. If you throw the builder off the project he can prevail in a lawsuit claiming those profits unless you can show that he was thrown off for good cause. Builders also frequently claim that you were behind in payments and that you owe that money in addition to the profits. In order to proactively defend against this sort of suit from the builder, there are necessary steps to take, and an attorney must still be involved. There are probably requirements in the contract for dismissal. The OP will probably also still require the services of an Arch/Eng. to document the entire spectrum of defects in case the builder files one of these suits anyhow. The cost of correcting the defects would offset the money owed on the project. It gets very complicated. In many cases, the best possible outcome for all parties is that they walk away with no harm, no foul agreements. Unfortunately, it is rare that both parties understand this.
All of this is great to consider. It seems to me (but what do I know?) that in an ideal world, a mutual parting of ways might be the best possible outcome, even though it means me eating the cost of fixing the balcony. Given the response I got, I'm not sure I'd really want it fixed by the builder anyway. The only outstanding items on the house (besides the balcony and punch list items) is the septic and hvac. I'd be pretty happy at this point to have someone else come in and finish the hvac (and have someone who would), which would just leave getting the septic done. The rest could be dealt with as needed.
But, to Peter's point, I don't want to put myself in a bad spot, so figure it's worth at least a call to a lawyer to hear what s/he thinks the options are.
Bill,
I think you're right on some level that they think "I don't know what I'm talking about," though I really think it is more to the effect of "I don't care whether you know what you're talking about it, we are just going to do it our way and be done." The long and the short of the HVAC issue is that they want to install a bypass duct on a 2-zone Carrier Infinity system, everything fully variable, even though Carrier's own literature says things like "a bypass duct must not be used." They claim they need it because "Zone 1 might call for 1200 cfm and the ductwork can only handle 800 cfm." Even though Carrier literature says that the Infinity system does a duct assessment daily to ensure airflow maxes aren't exceeded (nor should Zone 1 call for more air than it can handle from my understanding).
Working through the "proper" channels today to see what the options are. Have talked to the bank w/the construction loan, the folks providing permanent financing, and have calls in to a couple of lawyers. We'll see what comes of it.
Matt -
Since you don't have any building code enforcement, you may not need to worry about this. But before you throw the builder off the project make sure:
a. You have a sub who can pull the required permits and get any required sign off for anything that needs to be signed off - electrical, mechanical, plumbing, building final, etc.
b. You get all the documentation you possibly can from the builder. You mentioned it was cost plus - so do you have copies of all the invoices from subs & suppliers, etc?
c. You find out what documentation will your insurance company require to insure it. and make sure you have a way to obtain that.
Is the inside complete? I share the concerns others have posted about the deck, so I am now concerned about how your house was framed, how the inside stairs were framed, etc. If everything really is complete except the punch, the septic and HVAC (and from the looks of your first photo, the landscaping), I'd be quiet for awhile and push the builder to fix all the punch items. One less thing to worry about. Part ways after that, and pay builder what they are owed AFTER deck is fixed and after an engineering assessment of the balance of the home.
It is also possible the bank won't fund the draw that involves that deck....
Yeah, you really want a lien release from the builder. Ideally, you would have one from each of the subs as well. Don't release any more funds without these documents.
An easy solution then: have the contractor put a damper in the bypass duct. I doubt they'd fight you on that. Then when you take posession of the house, close that damper and be done.
Sometimes the path of least resistance is the way to go.
Bill
I've thought about that.
My worry, I suppose, is that the way the sub doing the HVAC describes the operation of the variable speed system ("If zone 1 is calling for cooling and zone 2 isn't, the air handler will supply all 3 tons [it's a 3-ton system] even if zone 1 only needs 1.5") makes me think (or at least wonder) if they have any idea how to properly design zones and install an Infinity/variable speed system.
I hate to keep this thread going any longer than it needs to. While I try to sort out the best route forward, the builder has come up with a "fix" for the balcony railing. He's put some sort of structural screw (can't tell what it is exactly) at an angle through the post, through the decking, and (I suppose) into the band joist. I think everyone here will agree that that is not sufficient, and doesn't really solve any of the original problem with the posts (and that's reflected in the fact that I can still move the posts basically the same amount as before). Picture of the "solution" attached.
He couldn't even put screws in all the holes in the bracket?
Those are decking screws, used to hold decking to the joists. They're not structural.
It also looks ugly.
Matt,
There isn't a municipal inspector who wouldn't red-tag that deck and probably insist the door was sealed until it was fixed. Your builder wouldn't be in business anywhere with enforcement. This isn't something subjective. Building codes have specific lateral load requirements for railings. The number and angle of screws he adds doesn't help anything.
I think of a friend of mine who went to refinance his mortgage and when the appraiser saw his deck the bank made him screw a 2x4 over the door until it was fixed. Not everyone is that proactive but there are lots of people with an interest in your home.
The bottom of the post will split if someone falls against it, and the screws will come out through the splits in the wood. You could probably easily demonstrate this by pushing against the post. If I was the engineer on the project, and I was getting the go around on this, that's what I would do -- demonstrate the failure. It's hard for anyone to argue with that. What will the builder say? "don't lean on the railing"? Sometimes lessons can only be learned the hard way.
As Malcolm has now mentioned several times, the code details the acceptable ways to make these type of connections. Sometimes there is an exception for something that has been "approved". "Approved", in this context, means by an engineering firm or ratings agency (in the electrical world that means UL or similar). It doesn't mean the builder approved it. Codes are pretty specific about these kinds of things for good reason.
Bill
This thread seems to have taken a somewhat gentler direction and that's probably a good thing. Matt seems to have been involved in the process enough that he is (somewhat) satisfied with the construction so far except for the deck and the HVAC. If the house is past the 90% mark, go ahead and let the builder finish. Perhaps negotiate a discount on the deck and the HVAC because of the defects. Once the dust settles and the builder is out of the picture, tear down the deck and replace it and have the ERV guys fix the HVAC. That will cost you extra money that you should not have to spend. But it will cost far less than lawsuits. Depending on your agreement with the builder, you might consider deducting the cost of the replacement deck from your final payment, but again, you'll need to defend yourself with actual data if you do this.
I think the bottom line here is that every professional on this list has told you that the deck can't be saved. There are simply no fixes for all of the bad things the builder did to this deck. It is unsafe for use and must be replaced. That's the direct answer to your original question.
Depending on the cost of replacing it and your contract provisions, there may be some way to extract some of the cost of replacement from the builder. If so, great. If not, bummer but that's the way it is.
Peter,
Thanks for the summary. We certainly don't need to continue to beat a dead horse here. The replies have helped give me confidence to move forward in replacing it (whatever form that takes). The replies have been helpful and are the reason I love reading GBA. Thanks, everyone, for all of the input.
Matt
Matt,
Sorry y0u have had to deal with this. Best of luck going forward.
Sorry to chime in here late, but it looks like you've gotten some good advice and taken it to heart. But I would have some concerns beyond the HVAC and deck. You mentioned the reduced sized rafters...done without notice. As an architect, I expect a builder to stick to my plans. If they have a problem or a better idea, I'm happy to hear it and arrive at a solution that works for everyone. But it looks like this guy just went his own way and until you noticed something, he did it his way. In some cases, that may not matter, but in others it might well matter in terms of structural integrity, energy efficiency, protection from water being in the wrong place, and on and on. I would suggest that before you part ways wit the builder, you ask the architect to do a thorough inspection, and have the guy fix anything you deem important. In some ways, you're lucky that he did the worst possible solution for fastening the deck post....even the traditional way of though bolting to the rim joist, which you probably would not have questioned, is considered an unsafe practice now. The rim board is just nailed into the end of the joists and nails don't have that much holding ability. That's why there's now hardware to tie the post back to the joists, or construction details where the post is locked into place by cross blocking,
I prefer the guard post detail, where the post is bolted directly between two joists. I use 1/2" galvanized bolts for it. You really get the sense of "That's really not going anywhere" with that detail.
Dead horse? Where's my stick?!?! Where's my stick?!?! But seriously, the deck issues are bad but at least they are now known and can be fixed. The HVAC can be fixed too. As far as the house itself, the bare minimum of acceptable wood framing is so redundant that I doubt even the worst case scenario here would be in any real danger of collapse. Cracked plaster? Maybe. Sorry you have to have any level of doubt persist after the deck fiasco, but I think the advice to get the house done rather than drag it through court is sound.
Let the guy finish, write him a lousy Yelp review, then fix the deck, get a good railing system installed and enjoy your new home.
Bouncy floors are annoying too. The big issue I see is if the builder is cutting all these corners that you can see, what other hidden issues might there be?
Bill
I don't think it's as much an issue of cutting corners as it is just "doing it the way we've always done it". I'd peg this builder's technique as 1980's. Decks used to be built with 4x4s and nails until a few fell down and the code caught up. The basics of house framing from the 80's may not be as efficient as now, but the house built in the 80's will still stand just fine. Houses from the 1880's wouldn't pass code inspection now, but a lot of them are still standing.
This isn't to excuse the builder in any way. That deck is a mess and the other issues are genuine as well, but I don't think the build in total is necessarily as bad as some would imagine. Take a look at most tract homes and there's plenty of sloppiness, but they're not collapsing.
This sounds about right. I was able to get a face-to-face with him this morning. Tried to get him to walk through concerns point by point (even brought the AWC guide with me so we could have pictures to look at). He had no interest and wouldn't touch my "Do you think the deck meets code?" question. His answer was always "We've always done it this way and I've never had a balcony fail. The guy who built this has built more decks than anyone else in the city" [note that despite being in the county w/no code, I'm really just 15 minutes outside a 500k metro area).
As for the railing, he continues to insist it's fine and "won't get any better." In fact, he said, "I could chain one of these posts to my truck and wouldn't be able to pull it down." I offered to bet him the cost of my house on that, but he didn't seem interested:-)
Anyway, I have a couple of structural engineers looking at photos; have talked to a lawyer about the best recourse, and have let our architect know what's going on and will talk more to her when she's back from vacation.
Andy,
I agree with a lot of what you've said, but there is a fundamental difference between decks and the rest of house construction. Wood framing usually has enough redundancies built in that deficiencies almost never cause structural collapses, as sheathing or other elements of the structure take up the slack. That isn't true of most decks which rely on one or two elements for their integrity - and certainly isn't of this one. It's an accident waiting to happen.
Malcolm, I think we are saying the same thing, just that you're saying it more succinctly and clearly than I am.
The house won't fall down, but the deck might fall off.
Andy,
There is a deck on one of my neighbour's houses I keep an eye on while walking by that has the beam at the mid-span! So far the attachment to the house seems to have kept it from capsizing, and luckily it's only about four feet above grade. It's just biding its time waiting for the right sized family gathering.
"Houses from the 1880's wouldn't pass code inspection now, but a lot of them are still standing."
And a lot of them are not. People are often talking about how construction was better in the past but forget that what are we are seeing today are the survivors :-)!
So sorry to hear all this...
I'd look to go over everything with a fine toothed comb (with your architect). As noted, going off-script on the house's structural components isn't likely going to compromise safety (my head is hurting from shaking it over the poor details on that deck!), BUT, can you live with things like large deflections in the floors? I've had one house where I hated the floor deflection: not going to be a factor in my slab-on-grade single level house! (opposite issue- real stiff, but I digress).
Think about how you will be able to (or not) overcome these issues mentally. If you can't come to a vision of peace now it might never happen.
NOTE: I spent a lot of time researching code for building a replacement deck on my current home. It's no place where sloppy ought happen. I decided against building a new deck (there were other, significant factors also) and have opted for building a new house with no raised deck!.
Mark,
I'm with you. When I become world dictator elevated decks are one of the first things I am going to ban (along with Kale). Apart from the potential structural problems, they deteriorate from the day they are finished, and claim a valuable weekend or two to maintain during the nice weather you want to be enjoying each summer.
Well, I figured folks deserved an update after a week or two of suspense building. My builder is actually a two man team. The other partner has gotten involved and wants to make an attempt to make things right (in the meantime, I have talked to a structural engineer and have a draft report that more or less points out the code violations that have been highlighted numerous times).
It turns out that the beam situation was even worse than we all originally thought. See the annotated picture on this post...what we all thought was a "3-ply" 2x12 actually isn't. What I/we thought was a 2x12 on the inside is actually a 2x2 that the joists are sitting on. So the beam is really just a single ply butting into the 4x4 post nailed to the little short piece that is nailed to the post (then w/the "decorative" 2x12 on the outside of the beam).
I suggested 4 fixes.
1. Replace the spliced beam with (2) 1.75"x11.25" LVLs and cut the 4x4 posts back so that the LVLs bear on the beam.
2. Add joist hangers at all joists/ledger and joist/beam intersections.
3. Add lateral tensioning devices per code (probably 4 DTTZ1)
4. Fix the balcony guardrail so that they are affixed to the deck framing per code.
He was originally pretty amenable to them. He went out this morning and met w/the guy who built the balcony and has come back with the following proposal. He's agreed to joist hangers and lateral tensioning devices. He's countered my proposals with the following.
1. In order to avoid having to cut joists back (and the rain catchment system), he suggested a 2-ply LVL beam. He would notch the 4x4 post so that ONE of the LVLs beared on the beams. The other would run on the outside of the 4x4 posts. He would then through fasten the LVLs to the 4x4 (this certainly seems better...is it good enough to have a single LVL bearing on the beam and the other LVL through fastened?).
2. The balcony guardrail seems to be a bit of an impasse. As a refresher, the rails currently sit on top of the band joist and is fastened with 2-4" screws at a diagonal into the band. There are then small angle/l-brackets at the bottom of the post that go through the decking. They all really do seem to believe that this is more than sufficient and that it is really sturdy as is. I told him I generally agree that I'm not going to go out there and just blow it over by breathing on it or anything, but that repeated stress where the screws go through the end-grain of the post and into the band can/will eventually lead to the wood splitting and potential failure.
Again, their main reason for not wanting to fox the guardrails is (besides really thinking they're good as is) is damaging the water catchment system under the deck. They don't want to cut/disturb it (and obviously they don't want to have to replace it b/c that's $$).
Anybody have thoughts on the beam solution (one ply of the LVL bearing on the beam, the other ply--obviously nailed properly to ply #1--through fastened to the post? Or on the guardrail? To me, the guardrails seem like a "must do".
To clarify, their proposed fix for the beam is a 2-ply LVL affixed similarly to the attached picture, but instead of both plys bearing on the beam as shown, the notch is only wide enough for one LVL to bear on the post (and the other would then be pushed out to the outside of the post.
Since the 4x4 is already undersized for a deck, I think the better solution would be to upsize the column so that it is 6" wide (four ply 2x) which would allow the LVL to be supported directly.
You can also look at a column cap (ie Simpson ECCQ3-4SDS2.5), but I don't think any allow for an offset.
Jacking up the deck and removing that column is a pretty simple operation compared to the other fixes.
Make sure the LVLs are treated for outdoor use, lot of times triple ply of PT 2x is a cheaper solution for this type of deck.
The handrail posts do need to be fixed properly, the current install is way too flimsy.
For this type of deck, a side mount steel post might be a better solution. Search for " Side Mount Post Bracket". Many options out there for both wood and glass railings. These can mount to the outside face of the new beam and won't interfere with the rain collection on the inside.
Thanks for the feedback. I actually suggested to him after posting that we affix a 2x4 to the existing 4x4 for the 2nd lvl to bear on. He is worried about messing up the stonework and capstone that's done around the post. I say suck it up. The capstone only cost $50. Tear it out if you need to.
I'd thought about an outside mount for the post. An option...will need to think about aesthetics for that, but definitely an idea.
Since you have paid the engineer for his opinion I think doing anything the engineer has not approve would be foolish.
Note can we assume you and the contractor will agree in writing before any more work is done?
If so make sure the word “treated” is the word preceding the word LVL every time the word LVL appears. The last thing you want is a rotting LVL.
Walta
Yes, I've asked for a written agreement on the fix before work is done (several days ago told the less cooperative builder to stop repairs without an agreement in place....he was just going to through bolt the existing beam to the 4x4).
Good point on the treated LVL. I had thought about it, but I didn't mention that when I talked to him.
All I have from engineer at this point is a draft report. But yes, my ask is to fix the code issues that he has pulled out in the draft.
For whatever reason, builder and carpenter are super fixated on damaging the gutter system underneath. Told them I'd way rather have to replace the tongue and groove ceiling in 5-8 years from a small leak vs hanging out drinking a beer with a bunch of friends on the balcony and have the railing give way. Structure above all else.
Matt,
Good to hear you seem to have broken the impasse with your builder. I agree with all of Akos' suggestions.
Sometimes with all sorts of projects, we end up screwing around trying 'save' money or material or whatever, and it rarely ends up working out.
How much does this catchment system cost?