Baffle material for cathedral ceiling in Seattle (4C)

I recently purchased a renovated 1906 Craftsman Bungalow in Seattle (4C), and it has an enormous unfinished attic that I’d like to convert to living space. The roof is a simple gable, 8:12 pitch with a 9.5’ height at the ridge. The roof assembly is composition shingle, tar paper, and plywood decking, which were all newly installed as of 2021.
Rafters are the original true 2×4, so not much depth to insulate, and the people who owned the house before only put 4” blown cellulose into the ceiling of the main level, then installed can lights throughout the whole house so lots of air movement and heat/moisture transfer in general due to poor sealing between the main floor and attic.
Based on my research here, I’m planning on doing the following:
- Sister new 2×10’s to the original rafters to get depth, since there’s not much to scab to and I’m also concerned about the added weight of insulation and drywall to only a 2×4 rafter alone.
- 2” air channel with baffles
- 7.25” R-30 Rockwool, which gets me to the bottom face of the sistered rafters.
- 2” R-7.7 EPS foam board across bottom of rafters, taped at seams
- Furring strips
- 5/8” Gypsum
- Latex Paint
My main question is, given my wet climate, should I make the baffles for the air channel from a vapor-permeable or non-permeable material? Seems like this can go both ways, I was going to either:
Option 1: rip some plywood to 1-7/8” strips, then install and cap the channel with 1/8” fiberboard (vapor-permeable)
Option 2: make an air baffle with faced 1/2” EPS board and foam sealer at edges.
I want to do this right, and it seems like there’s just a lot of moisture to handle, so I’m leaning toward the fiberboard, assuming that some might move through, in which case at least it can dry, to the exterior, rather than get trapped between two layers of EPS. Is there anything I’m missing? Thanks!
GBA Detail Library
A collection of one thousand construction details organized by climate and house part
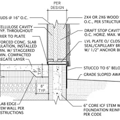
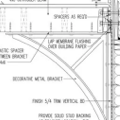
Replies
You're probably overthinking those baffles a bit. You don't need to seal them, since there is a vent channel right above. What I like to do for baffles like this is to tack furring strips to the inside edges of the rafters with a finish nailer, then use 1/4" waferboard to make the baffles and tack that in with the finish nailer again. 1/4" wafer board is like a lightweight OSB sheet, and works great for this -- and it's also cheap. 1.5" is code minimum vent channel depth, and a 1x2 furring strip easily makes this for you. You can certainly make deeper vent channels though, which is a good idea for long spans and/or shallow pitch roofs.
I see no problem with mineral wool under the baffles.
I would use polyiso on the interior, with seams taped. This gets you more R per inch than EPS, and the foil facing gives you a vapor BARRIER. You don't really need that vapor barrier since you have vent channels above, but the foil facing gives a very nice vapor AND air barrier that is robust and easy to seal. Taping to EPS can be trickier, since EPS has a tendancy to "chunk apart", whereas the foil facer on polyiso is much more durable to tape to. Remember that ideally you want the vapor barrier on the "warm in winter" side of the assembly.
You don't really need furring strips under the rigid foam, you can fasten the drywall directly to the rafters through the foam using long screws. You're going to be lining up screws through the foam regardless (either through the drywall or through the furring strips), so I don't think you really gain anything using furring strips here.
Bill
If you have the height, I would nail the 2x10 slightly dropped from the 2x4s, this way the bottom edge of the 2x4 can form one side of the vent channel.
Thin baffle material needs to be something permeable, as long as moisture can move through it the material doesn't matter. I've used housewrap before for this (take a smaller roll and cut it into say 14" wide jellyrolls with a miter saw, unroll and staple as you go to the blocking.
The interior rigid does increase the assembly R value a fair bit, but you are not in cold enough climate where big R values are needed and snow melting from thermal bridging is an issue. If you want more R value, bump up the new rafters to 2x12 and install thicker batts. The air barrier can be air tight drywall or one of the variable perm membranes under the drywall.
I would use a permeable baffle material like the plywood (Class 2-3) you mentioned. In the heating months if you are using a class 1 vapor barrier this would be a 'cold side' vapor barrier and you could get condensation on the bottom side from the warm, moist interior.
Also, I would use EPS (at 2" that is 2.5 perms, so class 3), rockwool board or wood fiber board on the bottom side of the rafters (all vapor retarders, not barriers). If one was to use a foil faced polyiso, in the cooling months (assuming you have AC or will in the future) this would create a 'cold side vapor barrier' and could lead to condensation on the backside of the drywall. Admittedly, the PNW climate zone has a pretty forgiving absolute humidity (especially in summer), so if you used the polyiso it would probably work in reality... If it was me, I'd use a vapor retarder insulation board in lieu of a barrier to gain the extra peace of mind. I would use either an air tight drywall approach for the air barrier, or better yet, use a membrane such as Siga Majrex or ProClima Intello. Beyond that, your assembly looks great for 4C here in the PNW.
>"If one was to use a foil faced polyiso, in the cooling months (assuming you have AC or will in the future) this would create a 'cold side vapor barrier' and could lead to condensation"
It's an insulating material though, so the foil faced material looks like foil/insulation/foil. The vapor barrier becomes whichever side of the polyiso is the condensing side, with the insulation between the two sides regardless of the season. With sufficiently thick polyiso, you avoid condensation on either side during any season this way. From a practical matter here, with 3/4" or thicker in that climate zone, I doubt there would be any issue under any reasonably conditions.
BTW, I have an assembly in my own home here that is 1/2" polyiso on the interior (as an air barrier behind a T+G ceiling), with about R40 worth of fiberglass batts above it. There has never been any issue with condensation on this in any season in Northern CZ5 very near CZ6.
Bill
Bill,
The side of the foil facing the cool conditioned air in the summertime would be cold, irrespective of how thick the foam is behind it. The first surface the cold, air conditioned air would "see" is the foil pointing towards the interior of the home. Any interior latent loads could condense on it.
It's not a hill worth dying on in Seattle, 4C assuming bcallahan isn't building a natatorium or pasta cooking factory. In summer the absolute humidity is pretty low and the cold coils on the AC will strip some of the latent loads, anyways. I would just hedge my bets and go with a material that will allow some vapor through.
Thanks everyone for the helpful feedback.
Bill, I tend to overthink a lot of things, so thanks for the feedback. I like the simplicity of 1x2s plus 1/4" wafer board for the baffles. I'll also lose the interior furring strips since I see what you mean about needing to hit the rafters anyway, so they are unnecessary.
I will eventually add AC via a mini-spilt, but I've got one on the main floor, and when it's hot enough here to run, it's fairly dry, so condensation has never been an issue. I'm mainly worried about humidity in the winter months when it's the long dark wet.
Joshua, thanks for laying out the differences between EPS vs polyiso in this setup, super helpful.