Attic with mold — spray foam solution?

Long description, so please bear with me:
House in Northern Illinois, built in 1962.
Major house fire in 2015…all but the attic and top floor bedroom/office were gutted and rebuilt in 2016.
Windows replaced with modern windows.
Doors replaced with modern doors.
Exposed insulation replaced with modern insulation.
Attic had 2 gable vents, a few pot vents and a humidity-and-temp controlled powered attic vent fan.
In 10+ years we never had any issues with mold.
When doing the rebuild, the old wood siding was replaced with vinyl and the gable vents were covered up (error by the siding company).
—
Fast forward to almost 2 years since the rebuild was finished.
Found major mold all over the attic (on the underside of the roof)..also major mold in 2 closets that adjoin the attic.
Mold is being re-mediated and I’m working with contractors to rebuild and re-insulate.
The gable vents were re-installed and a ridge vent was installed but the contractors both tell me that because my attic lacks soffit vents (because my house essentially lacks any soffits), they feel that the attic still isn’t getting ventilated enough due to how much tighter the house is now than when it was built in 1962.
They are proposing re-insulating the entire roof/attic space with spray foam and sealing off the gable vents/roof vents/power attic vent etc.
So..now to the questions:
Should I be looking at open or closed cell?
(open cell is going to cost me around 2.5K over what insurance will cover, closed cell will cost me around 7K over what insurance will cover)…I’ve heard so much debate on open vs closed…if closed is truly the better solution for my house I’d go with it..I just want to be sure…
Secondly….am I still going to have issues due to the house being tight (and I am going to either have humidity issues unless I spend a lot on some kind of ventilation system) or am I likely to be ok given that a 1962 house still wont be as tight as a modern-built one?
If it matters, I have forced-air hvac..no units or ductwork is located in the attic space.
Thank you…this is all so confusing.
GBA Detail Library
A collection of one thousand construction details organized by climate and house part
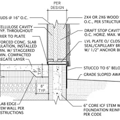
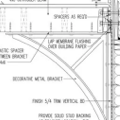
Replies
> they feel that the attic still isn’t getting ventilated enough...$7K
Instead of proceeding based on feelings, I'd measure attic humidity (over a year) to see if you have enough ventilation. Even if not, there are cheaper ways to reduce humidity/prevent mold.
I can't measure it now... The old insulation has been removed, the vents covered in plastic with a industrial-strength dehumidifier running... old insulation gone, something sprayed on the mold to kill it but we are awaiting the remediation contractor to spray encapsulation on areas where the mold was...
then the rebuild/re-insulation and the need to make my decision.
Both contractors, and an analysis done by an architect say that we would need additional ventilation to prevent mold (if we go with standard BaTT/blown-in insulation. It sounds like that would be much more expensive than foam...that's why foam is looking interesting.
Open cell foam only would present a risk to the roof deck. Don't do it.
Closed cell foam would protect the roof deck from interior moisture drives, but used twice the polymer per R of closed cell foam, and the cheaper closed cell foam uses climate damaging HFC blowing agents.
In zone 5A (northern IL) as long as at least 40% of the total R is closed cell foam, the rest can be filled in with fiber or open cell foam, as long as there is a class-III vapor retarder (eg interior latex paint on gysum board) or tighter on the interior.
To hit IRC code minimum R49 with a greener stackup would take 3" of HFO blown (much more benign than HFC,. but ~$4.25 per square foot @ 3") closed cell foam for about R21, plus 7.5" of half-pound open cell foam (~R28), or an R30 rock wool batt compressed to 6.5". If you have 2x10 rafters (9.25") that fits perfectly with the cheaper rock wool batt option- nobody is going to argue the other ~R1 from the tighter compression.
To do it with HFC blown foam isn't really a lot cheaper, since it takes 4" (R24) of closed cell at about $4 per square foot, plus R25 fiberglass batts (8", full loft) or R30 rock wool compressed to 6.0". Neither the R25 fiberglass or compressed R30 rock wool fits standard milled lumber rafter depths very well.
If the rafters are only 2x8s (7.25") the letter of the code can be met with 7" of HFO blown closed cell foam, but it's not "worth it" either environmentally or financially. With 4" of HFO blown foam (R27-R28, ~$5.25 per square foot) and an R15 batt compressed to 3.25" (R14-ish) it would be over R38 (indeed over R40), which was the IRC 2009 minimum for zone 5.
One advantage of HFO blown closed cell foam is that it can be installed in much thicker lifts. HFC blown closed cell is limited to 2" per pass, which is both a quality issue and a fire-hazard-while-curing issue. Some HFO blown foams can be applied in 7" thick per pass, all can be applied in at least 4" lifts without problems.
If this spray foam is going to be applied directly to the sheathing, then you can’t use open cell foam.
Sprayroam has the added advantage of completely encapsulation any mold that may have heen missed by the remediation people. The spray foam material won’t support mold growth, either, which is another benefit. When I had spray foam installed in a mold-remediated roof (a vaulted ceiling), I had the installers flash the sides of the rafters with a thin (maybe 1/8-1/4” or so) layer of spray foam just to make sure all the old wood was thoroughly encapsulated. That was two years ago now and no problems.
Bill
Hi Willy -
In all the details you provided you don't mention blower door testing. For anyone to offer contractor to offer bids/packages without this basic information is not right.
The building code and industry rules for what constitutes adequate ventilation rates/ratios is not based on actual building science or investigation/research. We do know that high to low works better than gable-to-gable but the impact of the 3-D geometry of the soffit and ridge vents, the pitch of the roof, the type of cladding, the depth of the vent chutes--we simply don't know how they improve/degrade air movement.
What we also know is that you can't vent your way out of a thermal bypass (combined air--convective--and insulation--conduction faults).
One more thing: many parts of the country had an unusual late summer/early fall involving overnight temperature very near dewpoint, extended cloudy days, etc. In New England, there have been a rash of attic mold and moss and lichen growth on exterior claddings. I THINK that much of this is a one-time phenomenon but we shall see...
Peter