Attic is hot after closed-cell spray foam was installed

Finished attic with 4 foot knee wall , duct located in knee wall to support 2 floor,extremely hot, BASF spray tite 2 inches with spray foam wraped around rafter in knee wall but with Sheetrock on ceiling just 2 in foam In cavity . Suggestions to handle heat issue. Richmond Virginia all attic seal very well thinking heat coming from rafters under Sheetrock. Thermal convection coming from rafters. Worked done in the winter, crawl space also done, house built 1994 colonial 2 story with garage with room above with dormer. Also in crawl space does it really need supply vent and return vent
Thanks
Mark
GBA Detail Library
A collection of one thousand construction details organized by climate and house part
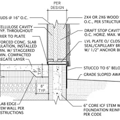
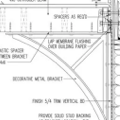
Replies
It sounds like you have only ~20% of the Rvalue required by current international building codes. Other than increasing your airtightness and insulation levels its hard to suggest improvements without more detail. Not surprising results when you get skimped by spray foam contractors.
https://www.greenbuildingadvisor.com/blogs/dept/musings/it-s-ok-skimp-insulation-icynene-says
Brian is there anyone I can consult with to help solve this issue, fee paid
The contractor has suggested in the slope ceiling with sheet rock to add blown in cellulose in the 2 by 10 rafter with a 2 by 2 nailed to give it a true 10 in , would that help. So 2 in of closed cell foam and 8 in of blown in insulation
This is a picture without the Sheetrock with close cell foam
Attic
Pictures of finish Sheetrock
Ductwork in knee wall
Duct work above room above garage
Last picture opening between Sheetrock and foam in ceiling suggesting filling with cellulose
I would suggest an evaluation on-site by a reputable home performance contractor or builder. Someone familiar with the big picture who can include foundation and combustion considerations. But yeah going higher than R14 might be a good idea here.
Didnt mean to sound harsh to the spray foam contractors. Industry and owners needs to get better about meeting code minimums with it. Even if it means yet another pass with the wand.
This is a large company that serves Virginia, the contractor suggest also to add a vent to the knee wall area to help condition this space. This is suppose to be a reputable company that last year sprayed 1 million gallons of foam last year in central Virginia
Most spray foam installers/companies lie to make the sale. They tell you only 5" of open cell spray foam is needed to meet R-38 code. That is a lie. They will get around by stating "it performs like R-38" which is how they spin it.
5" open cell = R 3.5 per inch = R 17.50
2" closed cell = R 5.5 per inch = R 11
So when they (spray foam company) tells you "it performs like", that is marketing nonsense. 5" of open cell is R17.50 and that is a pathetic R-Value in a modern new home. Even Zone 2 climates require R-38 in the attic.
So if you have 2" of closed cell that is basically R-11
Big and busy do not necessarily mean they are the best or even good . I just received a list of Century Club HP contractors from my local gas utility . It reads like a veritable who's who of the very same guys whose jobs I end up consulting and repairing . Financial success and name recognition are not a proper metric for quality and know how .
So what do I need to get R38 on the attic, will blown in cellulose do the trick between the Sheetrock and 2 in and blown in over the duct work, I want to correct this issue, can someone tell me by looking at my picture what would work
R38 is what they are SUPPOSED to be enforcing locally. R50 is the international attic/roof minimum for your climate. That's not an easy situation to comment on the specifics by looking at the pictures.
If you have another 8 inches of space between the spray foam and the drywall, filling that with cellulose will give you another R-25 or so. Adding that onto the R-14 from the stay foam and you're atR-39. However, this is only between the rafters; the rafters themselves are only R-12, so the total R-value for the entire assembly may be only R-34 or so. Better than what you've got, but still not amazing. Ideally you would be able to thermally break the rafters by putting a couple inches of foam or mineral wool under then before drywalling.
Mark,
It's always expensive to fix a job when the job was done wrong in the first place, and finishes (like drywall) are already installed.
You are in Climate Zone 4, where the 2012 IRC calls for roofs to have a minimum insulation level of R-49. Right now, your roof assembly is at R-14 if you are lucky -- possibly less.
You might want to point this fact out to your spray foam contractor. In some states, this type of work would be considered a code violation, and a contractor might be responsible for doing a job that complies with the code. That said, litigation is expensive and unsatisfying.
To read about all of the different ways you can fix this disaster, see this article: How to Build an Insulated Cathedral Ceiling.
To read about other spray foam contractors who practice the scam that you were victimized by, see It’s OK to Skimp On Insulation, Icynene Says.
Thanks for the feedback, so what would be the most cost effective way to get R38 to R49, with the Sheetrock up , the best sounds like R34 dealing with thermal bridging of the rafters , blowing in cellulose and from the knee walls roofing down to the soffits maybe add 2 in rigid foam board with blown in cellulose to fill in cavity or spray more closed cell foam out to the 2 by 10 rafters(expensive). Will this do or maybe something better?
Thanks for your input
If you don't want to remove the drywall (or the roofing materials...), I don't think there's any way you can get to whole-ceiling R-49. If you're willing to remove the drywall, you can add 4" of EPS foam boards under the rafters, blow cellulose into the cavity between the new foam boards and the old spray foam, and then install new drywall under the foam boards. If space is at a premium, 2" of polyiso will be almost as good.
Mark,
I suggest that you read the article I linked to. There is no "best" way.
If there are no budget constraints, I would advise you to put a thick layer (or multiple layers) of rigid foam above the existing roof sheathing, followed by a new layer of sheathing and new roofing.
Most jobs have budget constraints, however, so this approach won't be "best" if you can't afford to do it.
Thanks for all the feedback, without taking down all the Sheetrock what material can be used to get the highest R value between Sheetrock and 2 in closed cell foam, 2 by 12 rafters
Thanks for your patience
That would be Spider insulation, a form of blown fiberglass. It's about R-3.6 vs 3.2 for cellulose and a tad less for regular fiberglass. I thought you said you had 2x10 rafters? 2x10s with 7.5 inches of Spider in the space = R-37. 9.5 inches of spider and 2x12s = R-43.
Nate,
Your R-value for cellulose is either out of date, wrong, or both.
At nominal settled density, the R-value of cellulose is 3.6 to 3.7 per inch; at wall density (dense packed) it is 3.7 to 3.9 per inch.
I'm sorry 2 by 8 with 2 by2 added giving a 2 by 10
How far can open cell foam be shot in cavity or is spider the best option for this issue
My mistake Martin.
Martin writes: "At nominal settled density, the R-value of cellulose is 3.6 to 3.7 per inch; at wall density (dense packed) it is 3.7 to 3.9 per inch."
It varies by manufacturer, but I've yet to see a spec for cellulose at any density that hits anywhere near 3.9/inch. The R-value of most cellulose dense-packed to 3.5lbs or higher tends to be about R3.5/inch, slightly less than a peak of R3.7+ /inch somewhere between 2.8-3.2lbs. But the higher density is usually "worth it" for guaranteeing that it never settles when installed in wall cavities. At 6-8" in a sloped cavity with 2" of exterior foam to minimize winter moisture accumulation you'd be fine at ~3lbs.
Open-blown cellulose at ~1lb density could be as low a R3.2/inch, but as it settles it's R/inch rises to R3.5+ per inch. Assuming R3.5/inch settled or dense-packed is conservative.
Spider at 1lb density is R3.7/inch, but at 1.8-2lbs density its R4/inch.
A really good open cell foam installer can shoot 6-8' in a 2x4 cavity, but one small slip creates an obstruction and a potentially large void. It's a lot better/ safer to go with 1.8lbs fiberglass or 2.8-3 lb cellulose (minimally dense-packed- it won't slough or settle at that thickness in a sloped installation.)
In a Zone 4A climate as long as 30% or more of the R-value is closed cell foam on the under side of the roof deck with the rest as fiber you won't have much wintertime moisture accumulation risk at the foam/fiber boundary. BASF SprayTite 178 is specified to be R6.7/inch when installed at less than 4" ( http://www.spf.basf.com/DOCS/ST_178-BASF-020613.pdf ), so if they gave you an honest 2" it means you have at least R13 closed cell foam, which means you can install up to R30 of fiber without an interior side vapor retarder tighter than standard latex paint. So if you have 2x10 rafters with 2" of foam you have 7.5" of depth remaining.
Filling that 7.5" with 1.8lb Spider would bring the fiber layer up to R30 exactly, and you'd be at R43-R43.5 center-cavity, which isn't terrible. If you fill it with 2.8-3.2lb cellulose you'd have about R28ish in fiber, and a center-cavity R of about R41-R41.5. If your state & local codes are based on IECC / IRC 2009, that would beat the code requirement of R38, but it would be a bit shy of IRC 2012's/ R49 prescriptive.
If you added 2x2 stringers for more depth you'd need a Class-II interior side vapor retarder. That's more cost & complexity than it's worth. Stopping at R41-R43 is already plenty for dealing with the attic overheating issue. The next time you re-roof you can add an inch or two of exterior rigid foam under the new shingles.
Adding foam board on the interior would work too, but you have to be careful not to create a moisture trap, since the foam is vapor retardent. Even getting the sheets of foam into a kneewalled attic space is a major PITA, and air sealing it can be a lot of work too. If you have 2x10 rafters and room for 7.5" of fiber it's better to stop there for now.
I just had a heavy discussion with my foam contractor and he sent this reference
Your foam guy is an idiot if he thinks that document would fly in court. Just presenting that to you might be grounds for a fraud case. (Do you think your building department inspectors would accept that?) It's crap.
IRC code prescriptive R values are based on ASTM C518 performance tested R-values of the insulating materials, not some fanciful "equivalent R" comparisons to random straw-man sub-code assemblies.
Mark,
Wow! That is the most bald-faced, lying, blatant violation of the Federal R-Value Rule I have seen in some time! Source, please! Let's bust this company. We'll send a copy to the FCC.
.
Dana,
I'll admit that R-3.9 is on the high end, but the number is for real. The testing was performed by R&D Services and was sent to me by Dan Lea at the Cellulose Insulation Manufacturers Association.
Newer versions of fiberized cellulose achieve higher R-values per inch than the old hammer-mill cellulose.
R-3.7 is safer for most calculations -- it's better to be conservative -- but newer versions of cellulose insulation often achieve higher R-values per inch than R-3.7.
Ok I'm crying now, so what Martin wrote is the best I can do, also the BASF product is spray tite 158 which has less R factor I think, Is there anyone I can trust to talk to rather then texting back and forth, this foam guy is sincere but uninformed
Mark,
I'm not sure what you mean by "what Martin wrote." I'm also not sure what "the best you can do" is.
If you want to blow some type of air-permeable insulation like cellulose or Spider into the cavity between the drywall and the spray foam, you can. If you have a rafter space of about 9.25 inches (the dimensions of a 2x10), and 2 inches are filled with spray foam, you have about 7.25 inches of space, which if filled with cellulose or Spider will give you a total R-value (including the spray foam) of about R-39.
You're in Climate Zone 4A, though. Building codes require this type of spray foam + air-permeable insulation sandwich to have a spray foam layer of at least R-15 in your climate zone.
Your spray foam layer is R-13.2; that's because SprayTite 158 has an R-value of R-6.6 per inch (read about it by clicking here), not the crazy value of R-20 per inch that your installer invented.
The code calls for R-15, but you have R-13.2 -- not ideal or strictly legal, but if you keep your interior relative humidity levels reasonable, I'd say you can probably get away with it.
There are many more options, however -- but all other options are probably more expensive.
SprayTite 158 product is also R13+ @ 2":
http://www.polyurethanes.basf.us/files/pdf/SPRAYTITE_158_techSheet.pdf
If you have 2x10 rafters, blow the rest of the cavity full of cellulose or fiberglass and don't sweat the rest. It'll perform just fine, and won't create a moisture problem.
The difference in thermal performance between R41-R43 and R49 is somewhat academic, not even 10% after the thermal bridging is factored in. But the difference between R13 and R40 is huge. R49 is cheap and cost-effective if open-blown onto the attic floor, but hasn't much economic rationale in a zone 4 climate if much of the R value is clo$ed cell foam.
The folks at BSC suggest R45 (whole-assembly, not center cavity) as the financial-rationality starting point for a "compact roof" (= insulated roof deck) in a zone 4 climate. See Table 2, p.10:
http://www.buildingscience.com/documents/bareports/ba-1005-building-america-high-r-value-high-performance-residential-buildings-all-climate-zones
If you have only R41-ish center-cavity in an air-tight roof your whole-assembly R is about R30-R35-ish (depending on actual framing fraction), but that's still decent performance. The cost of taking it much higher than that working from the interior right now is high (too high, and not "worth it") compared to taking it higher later with exterior rigid foam when it's time to re-roof. Going with 2-3" nailbase panels above the structural roof deck later is modest compared to getting comparable performance on the interior right now. But the cost of completely filling the rafter bays with blown fiber now is small compared to the 2" of closed cell foam you already installed, and fixes the majority of the problem.
Martin: I'm liking the sound of R3.9/inch cellulose- but is it commercially available right now (and from which vendors), and at what density?
Martin: "You're in Climate Zone 4A, though. Building codes require this type of spray foam + air-permeable insulation sandwich to have a spray foam layer of at least R-15 in your climate zone."
That prescriptive is predicated upon R49. It's the ratio of foam-R to total-R that determines the average temperature at the foam/fiber boundary, which in turn determines the moisture accumulation potential. R15 is about 30% of R49. (R34 of fiber to R15 of foam.)
For an R40-ish center cavity value you'd be fine with only R12 foam (=30% of R40) and have some margin with R13.2. If you later add some rigid foam above the roof deck you buy even more margin.
It's not a problem at all if the fiber layer here is R30, with R13 of foam, which you can get with 7.25" of Spider. Using cellulose instead of 1.8lb Spider the somewhat lower R of the fiber layer gives you a more favorable R-ratio, and lower moisture accumulation potential, at a small cost in whole-assembly R performance. (Personally I'd go with whatever quote comes in cheaper if contracting it out. As a DIY I'd go with cellulose. YMMV.)
Does it make any sense where there is no Sheetrock to add 2" fiber board and add cellulose above it in the cavity, so Sheetrock area r value would be lower but where my duct is located the 2 " fiber board would give higher R value
Mark,
If you want more R-value in your roof assembly, 1/2 inch fiberboard will give you about R-1.3. That's not much. It would make more sense to add a layer of foil-faced polyiso; 1 inch gives you about R-6 or R-6.5, while 2 inches gives you R-12 or R-13.
You'll have to check with your local code authority to see whether foil-faced polyiso can be exposed (or needs to be covered with drywall) in the location you are thinking of.
With a little Googling, I found at least one spray foam contractor guilty of promoting R-value exaggerations using the bogus document called "US Department of Energy, National Laboratory System, Science and Technology Information" (which, the more you think about it, is rather a funny heading for a document -- like something that might be dreamed up by a 7th grader, or might perhaps appear in a Superman comic book).
The guilty company is:
Southeast Spray Foam, Inc.
P.O. Box 2683
Blairsville GA 30514
706.745.8685
[email protected]
Here is the URL of the document, posted on the web site of Southeast Spray Foam:
http://www.sesprayfoam.com/wp-content/uploads/2013/04/USDeptofEnergyRValueComps.pdf
I found another guilty company peddling the document with false claims. This problem seems to be centered in Georgia.
Here's the name of the guilty company:
Foametix (I love their slogan: "Our foam is green")
100 Enterprise Drive
Cartersville, GA 30120
And here is the link to the lying document on their web site:
http://www.foametix.com/resources/pdfs/Engineering-And-Foam.pdf
To see the lie Martin is talking about in the Foametix document, scroll down to page 20 of the 32 page pdf.
How does Fi Foil product for the open roofing area
Mary,
EarthCraft Va. is on Broad St. in Richmond. I recommend you call and see if one of their TAs can help you.
Fi-Foil is a company that makes many products. Most of the company's sales are for radiant barriers and foil-faced bubble-wrap. Their marketing materials are notoriously misleading -- trumpeting "assembly R-values" including air spaces and air films, while disguising the fact that the products have R-values of R-1 or less.
Neither product is a good investment. You're better off installing real insulation with R-value rather than either a radiant barrier or bubble-wrap.
For more information, here are links to two relevant articles:
Radiant Barriers: A Solution in Search of a Problem
Stay Away from Foil-Faced Bubble Wrap
You guys/gals have been great for all the advice, thanks for all the in depth engineering
Today I reported this blatant violation of the R-Value Rule to the FTC. I'm glad to know that my old friend, attorney Hampton Newsome, is still in charge of enforcement at the FTC. (He emailed me back.)
I get the impression that his budget is too small to do his job properly, since there remain so many illegal R-value claims on the web. That said, Hampton Newsome's job is to enforce the R-Value Rule, so it's good to know his contact information so we can all report violations.
If anyone else likes to turn in scofflaws, here is where you send the information:
Hampton Newsome
FTC
202-326-2889
[email protected]
One more question, should the screwed in Sheetrock hold the blown in cellulose and what do you recommend to hold up the blown in insulation in the open rafter area
Thanks
Mark,
Here is a link to an article that tells you what you need to know about installing cellulose insulation: How to Install Cellulose Insulation.
Great thread unraveling here. While there is huge room for improvement in the attic R value situation, there could be other areas of your home's weatherization worth improving too. Many things could be more important than whatever R-value you end up with up there. Judging from the loose-fill insulation on the floor, your house is existing, not new. Was blower door testing performed before the spray foam? Have you had your crawlspace/basement evaluated? Are there any atmospherically vented appliances to have concerns about?
Thanks for the link since the open rafters have been foamed wrap how would you handle the stapling of the web material, some areas have 1" to 2 in of foam, maybe labor extensive 3in screws To hold up webbing
Screwed or ring-shank nailed sheet-rock can easily hold the cellulose insulation at any density.
For the roof area behind the kneewalls you have some options:
*Sheet rock works- it needs to be air sealed and painted with at least a primer coat to bring it's vapor permeance down to Class-III levels.
**If you use OSB or plywood instead it is already a class-III vapor retarder. and wouldn't need to be painted, just air-sealed.
***You could blow the cellulose in netting. Landcaping fabric works fine for this if DIY. It needs to be stretched tight and stapled every inch or so. The pros would use a similar but application-specific material. (In applications where ceiling smoothness is important you would work adhesive through the mesh into the rafter edges with a brayer to keep the mesh from pillowing out at the rafters, and would need to roll the whole thing flat to the rafters prior to putting up the gypsum, but that's probably not where you're going here, eh?) You would then air-seal over it with Certainteed MemBrain (a thin nylon sheet "smart" vapor retarder) taped at the overlaps and caulked at the edges. Seams between sheets have to occur at the rafters to keep the tape from failing over time. This approach is a bit fragile if the space being used for storage, but it works, and using flexible goods like mesh & sheet plastic is somewhat easier to manage in tight kneewall spaces than rigid board type materials.
Crawl space was also done and looks like it was done properly, duct work has been sealed in the past with blower door
Oops! Missed the encapsulated rafter detail.
Since the rafter edges are not exposed you're probably better off tacking the mesh to the closed cell foam then installing 1x3 or 1x4 furring through-screwed to the rafters 24" o.c. to support the mesh prior to blowing. That would be fewer (but longer) screws, but the furring would make it easier to hang the OSB or sheet rock or MemBrain.
The open rafter will stay open no storage just duct work, with 2 in foam and blown in cellulose in web why can't I stop there why use air seal over it??? Also will staples hold in closed cell web
Staple retention in foam is lousy, and would blow-out for sure. Even stapled into wood it needs to be stapled every inch, and even then it's also good to glue it, as previously discussed.
Cellulose (like all fiber insulation) is very permeable to both air and water vapor. To keep moisture from building up in the cold upper layer of cellulose in winter it has to be reasonably air tight toward the interior, and the vapor permeance needs to be brought down to under 10 perms (under 5 is even better).
A single layer of latex primer on wallboard runs about 5 perms.
Dry OSB & plywood is about 1-2 perms, higher when the humidity rises, making it a somewhat "smart" vapor retarder.
MemBrain runs less than 1-perm when the relative humidity is under 35-40%, but over 10 perms when the relative humidity is 70%. That means it dries a lot faster than OSB or painted wallboard, and it also allows less moisture through during the colder drier-air conditions of winter. (It's about $100 for an 8' x 100' sheet, purchased from online retailers. Local distributor pricing will vary.)
Most of the labor of blowing in mesh in this type of space is simply installing the mesh, and it's a significant cost adder. If you're contracting out for it rather than DIY, it would probably be cheaper to use open cell spray foam in the kneewall area where you have good line-of-sight with the foam gun, then spray-paint it with an intumescent paint (for fire hazard control) then come back and install MemBrain over it to limit vapor diffusion. For the finished ceiling area you'd still want to use blown fiber though.
Congrats on properly encapsulating your crawlspace, not an easy thing to do! Include a photo if you've got a good one and arent afraid ;) Iam liking that ductwork was sealed but hopefully they used a ductblaster to assist with that and used the blower door on your house. I only mention it as a poorly detailed crawl could be contributing to higher humidity, discomfort and moisture problems behind finished surfaces in the attic.
Dana I read the article about open cell foam in unvented attic and they do not recommend using this because of the humidity issues and retaining moisture, they recommend only closed cell in attic for condition attics, with the sheetrock area the only reasonable option is cellulose and the expose knee wall area ( open rafters) looks like it has to be closed cell if I don't want to missed around with humidity and moisture issues. Is this true?
Mark,
You can use open-cell spray foam in this location in your climate zone, as long as the attic is conditioned (air conditioned during the summer). Here is a link to an article with more information on the issue: Open-Cell Spray Foam and Damp Roof Sheathing.
With high humidity they recommend adding supply ac and return vent, if you have fiber installation installed on the floor of the attic ( batts and blown in), that fiber would be pulled to the whole house and make the air unhealthy for my family. How would you work around this?
Mark,
One way to handle it is to have a supply register in the attic, but not a return-air grille. Instead of a return-air grille, you could install a jumper duct or through-the-floor grille to connect the conditioned attic with the rooms below.
Mark,
One more point: you are asking a lot of questions, which leads me to believe that a lot of these issues are new to you. You probably aren't an architect or an experienced builder, and that's fine. But at this point, you need to hire a very experienced general contractor, an engineer, an architect, or a home performance contractor to provide guidance.
You got burned by an ignorant spray foam contractor. Now you need to hire an expert to guide you to a workable solution. If you try to find answers to all of the questions that are now swimming in your head, you are going to end up overwhelmed.
It's OK to hire an expert -- and it's time to do so.
I sorry to take up your time but I'm trying to get the spray guy to correct his errors and to protect myself from incorrect methods. I have shelled out 8k between crawl space and attic. I have talked to other misinform foamers and they preach the 2 in is enough . I'm finding my research will serve myself than to rely on foam guys, you have not try to sell me anything and are will informed, I have reached out to ya'll for fee paid discussion and no one replied, all I can do is to support your web site by purchasing a membership. It is very hard to find someone knowledgable without purchasing their products. Thanks for all your expert advice and articles
Mark- as long as you have the~R13 closed cell foam on the outside of no more than R30 open cell (or fiber) you're going to be just fine. This is very different from having open cell foam applied directly to the roof deck, where the roof deck becomes a moisture reservoir, and the higher permeance of the open cell foam allows moisture to move in/out of the roof deck, creating rot conditions in the roof deck and summertime moisture-pumping of humidity during the daily temperature cycling of the roof deck.
Without looking up the specs for the exact number, the vapor permeance of 2" of closed cell foam is something between 0.4 and 1 perm, a class-II vapor retarder. That keeps moisture from moving in/out of the roof deck, and is completely protective of the roof deck even if you had the full R49, with over R35 as fiber or open cell foam. The issue then becomes how much moisture is going into/out of the open cell foam:
With 30% of the total R being low-permeance closed cell foam on the exterior of the open/closed cell boundary, the average temperature at that boundary isn't low enough in winter to accumulate much moisture, even without ANY vapor retarder on the interior. There isn't any convective path around or through the open cell foam, and the vapor permeance of ~8" of half-pound foam is often close to (and sometimes completely within) Class-III vapor retardency.
eg:
http://www.icynene.com/fbdocs/LD-R-50-USAProductInformationMar2013.pdf
17 perms @ 2" is ( 17 x 2"/8"=) 4.25 perms @ 8", and would be fine without a vapor retarder.
http://www.icynene.com/fbdocs/ClassicMaxTechnicalDataSheetUSAJan2013.pdf
11 perms @ 5.5" is (11 x 5.5"/8"=) 7.6 perms @ 8"
http://www.demilec.com/wp-content/uploads/2014/05/Sealection-500-TDS.pdf
3.17 perms @ 7" is already WELL into Class-III territory, and you'd need 8" to hit R30-ish.
As long as you're in the 5 perm range or lower at R30 with whichever open cell and don't go much higher than that, you won't have ANY moisture-pumping issues with your close-cell/open-cell ratio.
I'm calling back my MemBrain recommendation, which would only be called for if you go well over R30 on the open cell foam or you use an open cell product that is higher permeance than the examples above.
Mark,
It's perfectly OK to ask questions here on GBA. That's what we're for. The fact that you are doing your best to get informed on these issues is admirable.
However, in some cases the best person (or team of people) to devise a solution to a construction dilemma is not the homeowner. I'm not saying you can't do it -- I'm just advising you that at some point, you may want to hire someone to help you.
What if everyone you can find available for hiring is ignorant of this stuff? It's a major problem in many markets. If you have to hire an architect and a building scientist for big bucks just to make sure that a job was done (or re-done) correctly, something is terribly broken.
When you are shown a document showing 2 in of closed cell equals R 40 and you called another company and they expressed the same then the first hot day the attic real hot, I started researching, it's to the point to get someone unbiased to get accurate information than talk to a contractor to see if they know there product. You can't count on anyone you got to watch out for yourself
Nate,
There are competent architects and incompetent architects, just as there are competent builders and incompetent builders. Ideally, homeowners should seek out competent professionals. I agree that these people can sometimes be hard to find. I understand why many people have concluded that "something is terribly broken."
That said, I don't go into the operating room when I need an operation and explain to the surgeon what needs to be done. If a homeowner needs a major upgrade to the house, including transforming a vented crawl space to a sealed crawl space, and transforming a vented unconditioned attic to an unvented conditioned attic, and modifying the ductwork on the home's HVAC system, I don't think that the homeowner should necessarily sit down at the kitchen table and come up with a design, specifications, and work orders.
When a homeowner gets in that deep, it's often useful to have an architect or energy consultant.
Mary,
Please call EarthCraft Va. They are local to you and they have the knowledge to help you with these issues.
http://www.earthcraftvirginia.org/
You say that this attic room gets really hot.
Perhaps the heat is coming from the side attics via the knee walls and through the attic floor?
Is there blocking in each joist bay directly below the knee wall?? Or is attic air free to flow under the uninsulated attic floor?
Well spray foam contractor dodges me, so I have put up 4by 8 sheets 2in thick R10 and plan to blow in cellulose from big box store, so with cellulose between 2 in rigid foam and 2in sprayed closed cell, how critical is to make this super air tight to prevent moisture to get trapped
Mark,
When putting together an insulated roof assembly, airtight construction methods are always preferred to sloppier methods.
When you build a "foam sandwich" like the one you describe, there are risks. If the moisture content of the materials in the center of the sandwich is high on the day that the assembly is put together, those materials will stay damp for a long time. So choose a very dry day for this work. You might want to run a dehumidifier for 24 hours before installing the interior foam. And it would be good if the cellulose insulation were very dry too.
The vapor permeance of 2" of unfaced XPS is about 0.5-0.7 perms, which is pretty tight- about as vapor tight as a dry kraft facer on a batt, or "vapor barrier latex" applied to wallboard. While tighter than ideal in your stackup it'll be fine.
For blowing the cellulose cut the blowing holes with a hole saw and save the plugs. When replacing the plugs, squirt in a bit o' can foam into the kerf (& center drill hole, if your hole saw has a center drill), and tape over them with housewrap tape.
Taping the seams is also a good idea. There are some expensive tapes alleged to be good over the long haul for EPS and XPS, but housewrap tape painted over with duct mastic may be as-good or better.
Since (unlike spray polyurethane or polyiso) XPS melts & drips before it burns, you won't be able to just use intumescent paint for meeting fire code. A layer of half-inch gypsum would be a good idea when you're done.
Well I installed the 2in foam board and blown in cellulose, had to drill more 3 in holes in each cavity to get coverage. Should I remove the existing blown in fiberglass on the floor of the attic. Does it serve any useful purpose. Thanks again for all the support
Mark