Attic Insulation & Sealing

Having read the article in FHB, May 2008 by Pettit which recommends R-60 for the roof & R-40 for the walls, I am considering following these specs. using closed cell sprayfoam on a 2-story circa 1970s home in Alexandria, VA. Insulators think this is extreme and caution that I should go with less spray foam
thickness to get any reasonable return on my investment. While I’m still considering R60 & R40 using closed cell sprayfoam insulation, I’m perplexed by their universal response (They do make money selling more foam, right?).
I’m also planning to seal the attic(roof, side walls and knee walls and close all exterior vents) to treat this area somewhat like conditioned space (without heat or a/c)as my a/c airhandler and duct work is in the attic (and between floors 1 & 2) but my concern is the possible moisture accumulation in the attic specifically against the under roof. However, I can’t image greater moisture in the attic than our summer humidity in the DC area. Should I invest in an energy recovery ventilator system to monitor the air quality and moisture level?
William
GBA Detail Library
A collection of one thousand construction details organized by climate and house part
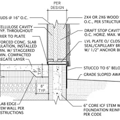
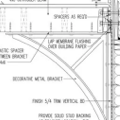
Replies
I've been building R-40/R-60 homes for 20 years, but in New England not DC and with cellulose not foam. I would agree that level of insulation is excessive in your area. R-20/R-40 would be more appropriate.
Because spray urethane foam is the most expensive insulation system and many customers balk at the price, installers try to sell the "less is more" line, claiming that the "effective R-value" is higher because of foam's air-sealing qualities. This is misleading. While air-sealing is critical to an efficient structure, conductive heat loss and gain is dependent only on R-value (and for summertime heat gain reduction, reflective materials are often as important).
Since you have air-handling equipment in your attic, it makes good sense to incorporate it into the conditioned space, but the level of air-tightness you'll likely create will require a mechanical ventilation system for fresh air exchange (minimum 0.35 air changes per hour). You should consider an HRV with defrost or ERV for your climate.
William,
I do not think that an R-40 wall is such a bad idea...I am curious about how you plan to create an r-40(overall) wall with spray foam?
How do you plan to deal with all of the thermal bridges at the studs,plates,rims and headers? The Pettit project used outsulation.
William,
I'm a home energy consultant based in Charlottesville, VA. If you're going for a "deep energy" retrofit or Passive House type retrofit, the R-40 walls is in the right ballpark. The R-60 roof is going to be excessive for our climate. Regarding solid closed cell spray foam - it will get you the R-value, but there are likely a few other ways to get the same R-value and reduced air leakage, at a much lower cost. Also, as John Brooks mentions, it becomes very important to start eliminating thermal bridges when you move into the territory of "Super Insulation."
I'd also like to suggest that you set specific target goals for overall energy use and/or heating/cooling energy use. Once you have a goal you're working toward, then you can work out the best balance of wall, roof, foundation, and slab insulation, as well as as air sealing, window package, HVAC package, etc. that will get you to your energy goal at the lowest cost, while providing a safe, healthy and durable building.
Hi John Books
I am exploring an areoseal product to place on the studs, plates, rims and headers to stop the thermal bridging.
To your second question, I am not yet sure, but I plan on replacing my exterior siding and will address at that time.
Hi John Semmelhack!
I am interested in hearing about your lower cost alternatives. My goal is to get the utility bill as low as possible. Sorry, but I am not sophicated enough to yet. My current goal is to seal the air conditioning duct work and seal up the attic with houses the air conditioning unit.
I have read an article by University of Toronto professor, Danny Harvey, which shows the net climatic impact of using foam insulation:
http://faculty.geog.utoronto.ca/Harvey/Harvey/papers/Harvey%20(2007c,%20BAE,%20Climatic%20Impact%20of%20Insulation).pdf
I see now why the Europeans are favoring more natural materials like cellulose.
Kathy,
For many other reasons, I use natural low-embodied energy insulation (primarily cellulose), so I would be glad to see strong evidence that the all-too-popular spray foams are climate-negative. But the study you cite is far too limited in scope to be useful.
It calculates the marginal climate impact of increasing levels of spray foam, but only in a mild 4,000 DD climate and only considering reduction in conductive heat loss - not reduced infiltration or reduction in cooling load. Those limitations make his conclusions all but worthless.
Closed cell foam reaches maximum effectiveness at about 3 1/2". R-value doesn't have anything to do with resisting heat and cold, I wish they would ban the term or correct the the system.
If you install 31/2" of closed cell Fire Resistant 2# density foam, you will reist heat and cold from -60F to 180F.
Darin, I'm not sure why you wrote that "closed-cell foam reaches maximum effectiveness at about 3 1/2 inches." The effectiveness of any insulation, including closed-cell foam, has to do with its ability to slow down the transfer of heat. The thicker the insulation, the more effective it will be at slowing the flow of heat.
Doubling the thickness of the insulation will cut the heat flow in half. Increasing the thickness of closed-cell foam from 3 1/2 inches to 7 inches will slow down the transfer of heat and therefore make the insulation more effective.
R-value is a useful way to describe a material's resistance to heat flow. To learn more, see "Understanding R-value."
In researching how to stop the thermal bridging resulting in the roof rafters, I've come upon a product called Aerogel (http://thermablok.com/) It runs about a $1/foot, comes in 4 feet strips by 1.5 inches and has an adhesive backing. Does anyone have any experience with this product?
My wife in I are in Seattle. We just purchased a foreclosure that was gutted and we're putting it back together. Our intent is to be a deeply green as possible within our budget. To do a good job, this means a tremendous amount of research. I have found that deep green is a series of tradeoffs, and most critical is to make sure the job is done well. While I've done a lot of research, there is still more to do, and the field is still emerging. Enough about me and my "qualifications"...
The statement above about loosing effectiveness on thicker applications of foam is correct. There is a good article on Fine Home Building (that I can't reprint here) that is a good overview of the pros and cons and strategies of spray foam. Some Googling on your own can turn up a lot of useful info. As the thickness of the spray foam increases, there are diminishing returns on performance. Spray foams often quote a certain R-value per inch, but it isn't actually a linear relationship.
Going with spray foam, I recommend getting several quotes. The reason is 2 fold. First reason is cost. There are a lot of options, and there can be several thousands of dollars in difference between quotes. Second reason is knowledge. There is a LOT of wrong information out there, estimators will often be absolutely convinced of what the best solution is without actually understanding building science or how the different systems in a house make up the larger system of the house itself.
We're still in the process of figuring out our insulation solution. Something we are considering, which my be of interest to you, is going with a hybrid approach: closed cell outer coating with a conventional "inside", coved with air-sealed drywall (a bead of a particular kind of calking before the panel goes on). We have open walls, so basically: apply a layer of foam, then add a layer of cellulose or fiberglass, then the drywall. Closed cell foam is a great vapor and air seal, and the first inch has a great R-value. The next layer of insulation has smaller embodied energies, less destructive to the environment (emphasis on less, nothing is perfect), is more familiar to installers, etc. The overall effect will likely be a cost effective approach that blends the best aspects of the different approaches.
We're also considering thermal breaks, if you're really going R-40 you definitely shoud. I've not used the Thermablock but it looks like it would be great in our walls because many spots are shimmed out 1/4" - 1/2" due to shear walls. Something else I've seen is TheraRock. I've not used it so I can't say much about it. If you have the cash, it could be a good boost to your project.
One last point, building science isn't exact either, so be careful about putting too much stock in it. There are certain things science knows very well, such as how things work in isolation, or how heat is conducted. How things work in concert is still being discovered, particularly how these things work in the "real world" where things nothing is "ideal". Sometimes solutions that work really well in one application won't do so well in another because it is still extremely hard to take every variable into account. If this is important to you, either find a really good performance consultant or be prepared to do a lot of research yourself. Personally, I've been doing both as even the best consultants I've been able to find still don't know everything that I want to know.
Daniel,
You may be spreading a misunderstanding when you write that "Closed cell foam is a great vapor and air seal, and the first inch has a great R-value." Actually, the second inch has an almost identical R-value. If one inch of closed-cell foam is R-6.2, then two inches of closed-cell foam is R-12.4. The issue of "diminishing returns" doesn't have to do with diminished R-value per inch; it has to do with energy savings.
The first inch of ANY type of insulation gives you the most bang for the buck. But every subsequent inch of insulation still saves you money -- just a little bit less money as the insulation gets deeper.
This "diminishing returns" issue applies to all types of insulation. The only reason that it is emphasized more by spray-foam salesmen than by cellulose salesmen is that spray foam is so expensive that achieving code-mandated R-values with spray foam costs an arm and a leg.