Attic HVAC and Radiant Barrier

As part of a major renovation/addition to our 1970 2 story colonial house, we’re isolating the 2nd floor HVAC and adding a second zone for it, and the contractors want to place the equipment in our unconditioned attic. It get’s pretty hot up there in the summer (even though I live in NJ), and I want to do what I can to maximize the efficiency of the HVAC equipment in the attic.
The insulation in the attic right now is awful, so the plan is to remove the crappy old stuff up there, spray-foam the attic floor with 1.5″ of closed cell foam and then put R-38 batts on top of that (after replacing some old non-insulation rated pot lights from the second floor ceilings). Ventilation in the attic is a bit of a challenge since it is a hip roof (the main house is about 42ft x 26ft), so we’re also going to be opening up the soffts as much as possible and putting in a new fan with humidistat/thermostat.
After all that, the HVAC equipment is still sitting in an unconditioned space. I was thinking of installing a perforated radiant barrier foil underneath the rafters in the attic to help reduce heat-transfer into the space. I’ve read a lot about radiant barriers, and I know that Martin doesn’t typically recommend them. I’m thinking that the hot attic in the summer is worse for the equipment efficiency than the cold air in the winter. What’s your opinion on whether or not radiant barrier makes sense here?
GBA Detail Library
A collection of one thousand construction details organized by climate and house part
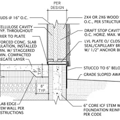
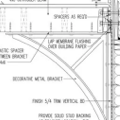
Replies
Have you explored insulating the sloping parts of the attic, rather than the attic floor? Especially if you use the spray foam. Described here:
https://www.greenbuildingadvisor.com/blogs/dept/musings/creating-conditioned-attic
That would create a conditioned space and make the radiant barrier question moot.
Eric,
I agree with James. A conditioned attic is the way to go if you must place mechanicals in that space. "Pretty hot" is an understatement - I routinely see 130 - 140 degrees in a climate very similar to yours - and keeping that heat out will do wonders. Efficiency will improve and you will reduce the risk of melting all the snow off your roof in the winter.
Thanks for the pointer James. It seems that whatever choice I make, it will be a compromise. Given that it's a shallow hip-roof, it would be a challenge to get proper air channels and a good amount of insulation underneath it. I can only imagine what my contractor would charge me for fabricating all the necessary venting.
Now, we are planning on replacing the sheathing anyway. So are there any reasonable pre-fab insulated roof panels that are readily available in NJ that would make sense? Something like this perhaps: http://www.thermocore.com
Eric,
I agree with the other respondents: if you are going to the trouble of contracting for spray foam, then put the foam where it belongs. In your case, the contractor should be spraying the underside of your roof sheathing, not your attic floor.
It sounds like you are now considering replacing your roof sheathing with SIPs. That will certainly work, and it will mean that your HVAC equipment and ductwork end up inside of your home's thermal envelope.
Thanks again to everyone for responding.
Ok - my budget has its limits, but I'm trying to do the right thing here. I'm finding it difficult to find a qualified person in my area who has experience working with SIPs. If I can't find one, my other option is to spray foam under the roof deck. I'm pretty sure the roof is supported by 2x10's, so there ought to be enough space to get a good R-value. I have some questions though:
Ideally, can anyone recommend someone in my area (Somerset County New Jersey) who can do a proper SIP installation on my roof?
If they were to spray under the roof, would I need a ventilation channel between the foam and rood deck (or other separation layer), or would I just close up the soffits and ridge vent and not worry about it?
Should I worry about air exchange? It's still a 1970's house with original 1970 tar paper and cedar shake siding, but...
We are also planning on removing the old cedar shake siding and tar paper on the existing house and try to improve the insulation envelope in the walls. Ideally I would put some kind of layered foam panel system, staggered and taped, etc. followed by a WRB, drainage plane and siding.
The reality is a bit harsher though - I'm running out of time (and budget) to plan the project (we're already a month late on the expected break-ground), and I've already chosen a contractor, so I'm trying to work within his limits and capabilities to avoid further delays. I was thinking of putting on Tyvek house wrap and Crane Board siding. The newer Crane Board has diagonal drainage channels and a protruding ridge molded on the back of the foam to help the system breath and drain.
I know this is not ideal, but I'm be happy to entertain other suggestions that would fit within a similar budget and time structure (assuming that either my contractor or someone in my area who can do the work!). I'd also like to hear opinions on if I'm just wasting money with the Crane Board and whether regular vinyl siding and house wrap or single layer taped foam board would achieve the same thing or better.