Attic conversion – modified cut and cobble

I would really appreciate any assistance can provide me with my unvented attic.
I have a modular house in climate zone 5:
The sealed plans for the house specify attic truss construction:
I somehow ended up with something more like this:
At any rate, I’m going to restore the structure to the original plan. As you can see, the roof doesn’t feature a ridge. The pitch is 9/12 and the rafters are 2×8 (truncated to 2×4 at the top, but I’ll fur that part out to 2×8).
I’m planning the following roof assembly:
-synthetic slate tiles (existing)
-synthetic underlayment (existing)
-plywood sheathing (existing)
-2″ XPS foam sealed to the rafters with 3M All Weather Flashing Tape
-2″ polyiso foam (perhaps sealed at the edges with one-part foam?)
-R-30 fiberglass batts removed from the ceiling joist bays and compressed into the remaining 3-1/4″ inches of space (i’ll strip off the excess as necessary)
-1″ of XPS foam adhered to the underside of the rafters to create a thermal break. Joints and penetrations sealed with canned foam and taped with 3M All Weather Flashing Tape
-3/4″ painted T&G pine
Thanks for reading. What do you think about this approach?
GBA Detail Library
A collection of one thousand construction details organized by climate and house part
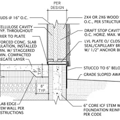
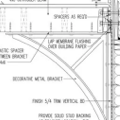
Replies
Here are the image files I was referencing. I had to remove the linked pictures to satisfy the spam filter.
Hi Ben,
I have a few concerns with this plan:
1. The amount of time and effort required to cut and detail 4 distinct layers of insulation.
2. The fact that, for all this effort, you only get to a center-of-cavity R value in the low 40s. (15 for the 3" of XPS, 10-12 for the 2" of polyiso, 14 or so for 3.25" of high-density fiberglass) and a whole-roof R value of 37 or so, not counting sheathing or T&G.
3. The "foam sandwich" effect. Although XPS has a little vapor permeability, the interior layer will limit the ability to dry to the inside.
One alternative to consider would to use 5" of closed cell foam against the roof deck, then fur out the rafters with 2 x 2s, filling the remaining space with repurposed fiberglass and installing Intello or MemBrain as an interior air barrier. This would get you R-49 in the center of the cavity and an overall R value in the low 40s.
Ben,
You are proposing the "cut-and-cobble" approach for an unvented roof assembly. This approach has been associated with moisture accumulation and rot, so I don't recommend it.
For more information on why you don't want to use cut-and-cobble for an unvented roof assembly, see Cut-and-Cobble Insulation.
For more information on the various ways to insulate this type of roof without getting into trouble, see How to Build an Insulated Cathedral Ceiling.
(By the way, you wrote that your roof doesn't have a ridge. Actually, it does. I think you meant to write that it doesn't have a ridge vent.)
To meet code in zone 5 in an unvented assembly needs at least R20 (out of a total R49) to be impermeable (Class-II vapor retardency or tighter) foam exterior the fiber insulation layer for dew point control a the exterior side of the fiber layer,, and that impermeable layer needs to be reliably air tight for the duration, which rules out cut'n'cobble approaches.
HFO blown 2lb foams are typically ~R7/inch (and a heluva lot greener than most 2lb foams or XPS, which are blown with HFC with extremely high global warming potential), so you can get there with 3" of foam + R30 batts.(or R28 rock wool batts.) A "cathedral ceiling" R30 is manufactured at a loft of 8.25". so the total depth would be 11.25", but an R28 rock wool or "standard" R30 batts are 9.5", making the total cavity depth 12.5".
A 2x8 is 7.25" deep, so you'd need 4" of additional depth do do it with R30 cathedral ceiling batts. One method would be to cut 1.5" rigid polyiso and cut it into 2.5" wide strips and glued them to 2x2s with foam board construction adhesive for a 4" wide assembly, then screw them edge-wise to the rafters with 5.5-6" bugle heads.
If that's too deep and awkward, 4" of HFO-blown foam would give you R27-R28, which combined with R23 rock wool (5.5" deep) means it only takes 9.5", so it would only need 2.25" of edge strip on the 7.25" 2x8s. Cutting 1.5" wide strips of polyiso and rip 3/4" plywood into 1.5" strips for the fastening surface of the strip assembly., screwed to the rafters 3" screws can get you there. With the majority of the R being the exterior foam, with high-density batts such as R21 fiberglass or R23 rock it would not need an interior side air barrier to perform well (but putting something there to control airborne friable fiberglass particulates would be a good idea if fiberglass is used.) This is probably the better solution.
HFC blown foam could be used, but it has to be installed in lifts no greater than 2" at a time to be fire-safe during the exothermic curing period and to not have shrinkage & adhesion issues. All HFO blown foams can be installed in lifts of 4" or greater. Some even claim that R49 can be done in single pass.
If the trusses haven't already been built it's possible to specify 2x10s for the top chords (the "rafter" element). If the roof deck isn't already on it's possible to specify R20+ nailbase panels above the structural roof deck. If you do both it's a much simpler (and probably cheaper) build.
Thanks Jon, Martin, and Dana.
Jon:
This is a very low budget endeavor, so I can't incorporate enough SPF to make a difference. I'm willing to try the Intello, but I'm concerned about detailing around penetrations. What if I substituted 1" unfaced EPS for the XPS? Would it allow the roof to dry to the interior while providing an adequate air barrier?
Martin:
One of the reasons I considered the "cut and cobble approach" is this line from your Cut and Cobble article:
" . . . if you are a fanatic for air sealing, you may prefer to invest in a European tape to seal these cracks."
I was under the impression from your Backyard Tape Test that the 3M 3067 adhered quite well to EPS. For this reason I was contemplating both sealing the edges with polyurethane foam and going over the top with the 3M tape. If you think the Siga Sicrall tape would make the difference between a failed and a successful installation, I would use that instead of the 3M tape.
On a different note, I don't have what I consider a ridge. The rafters and the sheathing do not actually meet in the middle. The gap is covered only by the synthetic slate ridge pieces.
Dana:
I really appreciate the thought you put into your answer. The trusses are built, and the synthetic slate tiles are already installed. Even if I could find a cheap spray foam applicator, I couldn't afford 3" of spray foam, which would be 6000 board feet (not including the gable ends).
As far as code compliance is concerned, the engineer for the house provided a performance-based compliance certificate with only R-30 batts in the ceiling joist bays. My primary aim is to install our air handler inside the building envelope, while adding habitable space within the buliding footprint. I would be very pleased to achieve a 1/3 increase in the cavity R-value. I'll have to determine if we can get away with furring out the rafters a little more. You've given me some good ideas to work with.
My concern with going the vented route is that I'm not sure how to reliably vent the dormers, the copper ridge vent would be pricey, and I'd lose at least an inch of space for insulation.
I guess the whole success of this endeavor rests on whether or not I can reliably air seal a cut-and-cobble installation through redundance or some other means, e.g., a 1" skim coat of professionally applied spray foam.
Ben,
The ridge is the segment (in geometric terms) representing the highest elevation of a gable roof -- where the two planes meet at the top.
It's a ridge whether or not the sheathing extends all the way to the top, and whether or not it has a ridge vent.
.
Ben,
I stand by the recommendations in my article, How to Build an Insulated Cathedral Ceiling.
There are two reasons that I don't recommend the cut-and-cobble approach for unvented cathedral ceilings:
1. Because of the stack effect, cathedral ceilings are at much greater risk of moisture accumulation than walls. Physics is conspiring to destroy your roof sheathing.
2. Rafters and trusses are always changing size and shape, in response to changes in humidity and temperature. These forces cause rafters and trusses to shrink, expand, and twist, and these forces act to undermine your attempts at air sealing.
I guess I meant a ridge board. Thanks for the explanation.
If I added a full layer of spray foam on top of the XPS and polyiso, how much do you think I would need to add before I elminated the risk of a compromised seal?
Ben,
As my article notes, if you want to create an unvented cathedral ceiling with spray foam:
(a) Use closed-cell spray foam, not open-cell spray foam;
(b) Install the closed-cell spray foam directly against the underside of the roof sheathing;
(c) In Climate Zone 5, make sure that the closed-cell spray foam has a minimum R-value of R-20 (meaning about 3.5 inches of closed-cell spray foam).
Forget cut'n'cobble for your project. COMPLETELY forget it- it's too risky, and it buys you nothing!
A mere inch of some closed cell foam is sufficient for protecting the roof deck, but 2 would be better. Then it's a matter of protecting from moisture accumulation in the fiber layers. That's where air tight Intello (might) come in handy. Read and understand this set WUFI analysis reasearch:
https://buildingscience.com/sites/default/files/migrate/pdf/BA-1001_Moisture_Safe_Unvented_Roofs.pdf
If you look at Table 3 you'll see that 2" of ccSPF is good enough to be protective of the roof deck at a total R of R49 even in zone 7A.
But that doesn't mean the fiber insulation would stay dry.
With 2" of closed cell (R12-R14) with 2" of closed cell foam encapsulating the top chords too, then and 8-9" of open cell foam under that encapsulating the top chords the risk would be pretty low. The open cell foam may accumulate moisture in the winter, and it may be prone to humidity-cycling in the attic during the summer, but the roof deck would stay dry enough. Painting the top chords with an anti-rot treatment prior to the foam would be cheap mitigation, but with 2" closed cell foam encapsulation they won't accumulate too much wintertime moisture .
Ben,
Q. "I'll install full-length baffles and place a 1.5-inch layer of XPS foam below the rafters. (Anything magic in that 1.5 inch number?)"
A. No, it's not a magic number. You can install 1-inch rigid foam, or 2-inch rigid foam, if you want.
Q. "With this type of vented assembly, should I still avoid placing rigid foam between the rafters?"
A. As long as you have a vent channel between the top of the insulation and the underside of the roof sheathing, and as long as the vent channel connects with a soffit vent at the eave and a ridge vent at the top, the cut-and-cobble approach is safe.
Q. "What is the purpose of the furring strips under the drywall?"
A. The furring strips serve two purposes: they satisfy drywallers in the Northeast U.S., where drywallers insist that ceilings be strapped before they show up on the job (it's traditional, not logical), and they provide an air space which adds a little R-value to the assembly when foil-faced rigid foam is installed.
Q. "Would my T&G installation require anything different?"
A. You certainly need an air barrier between the fluffy insulation and the tongue-and-groove boards. If you tape the seams of the rigid foam, and seal penetrations in the rigid foam, the rigid foam can serve as your air barrier -- assuming, that is, that you aren't worried about the chance of foam shrinkage. For more on foam shrinkage, see Using Rigid Foam As a Water-Resistive Barrier.
If the "peanut brittle" option is not valid for cathedral ceilings, I'll bite the bullet and vent the roof to save myself thousands.
Since the areas of the roof with dormers represent only about 203 square feet, I'll do the closed cell foam on that portion and vent the rest of the roof.
Following one of Martin's diagrams for a vented roof (attached below) I'll install full-length baffles and place a 1.5" layer of XPS foam below the rafters (anything magic in that 1.5" number?).
With this type of vented assembly, should I still avoid placing rigid foam between the rafters?
What is the purpose of the furring strips under the drywall?
Would my T&G installation require anything different?
Using rigid polyiso instead of XPS for the interior side continuous layer is both ~25% cheaper and ~90% greener than using XPS due to the differing impact of the HFC v.s. hydroncarbon blowing agents used. Polyiso would also deliver higher performance per inch in a vented roof stackup.
Using reclaimed/reused rigid foam would be 65-75% cheaper than using virgin stock foam, and would be 99.9% greener, since no new polymer or blowing agent is being used. There are probably several square miles of reclaimed 2" roofing polyiso in foam reclamation and building materials salvage warehouses nationwide, at 25-35% the price of virgin stock foam.
R23 rock wool between the 7.25" deep top chords yields a healthy 1.75" of vent space. You don't really gain much by going with more expensive rigid chutes and compressing fatter batts.
Then, 3.5" of reclaimed roofing polyiso (R5.7/inch, or R20) would be enough to deliver code compliant thermal performance on a U-factor basis, but it takes at least 4-4.5" of foil faced new foam (R6- R6.5/inch) to do it on a total R-value basis. Using 3.5" foam and 1x furring requires 6" pancake head timber screws (eg: http://www.diyhomecenter.com/fastenmaster-headlok-heavy-duty-wood-screws-250-bucket?gclid=CLrpsN6iytQCFZKPswodsGgCFA ) for the furring, but 4" foam would require 6.5" or longer screws. If using reclaimed foam the screws become a significant fraction of the total cost.
So, in a cost-sensitive application cheap foam or corrugated cardboard vent chutes, R23 rock wool, and 3.5" reclaimed roofing polyiso is likely to be the cheapest path to code compliance. Nationwide Foam has regional depots for their reclaimed goods, but if you're hundreds of miles from a depot the deliver fees add up to something real. Searching the local craigslist for the terms [rigid insulation] will often find smaller local reclaimers, or one-off deals. eg:
https://eastidaho.craigslist.org/search/sss?query=rigid+insulation
https://denver.craigslist.org/search/sss?query=rigid+insulation
https://chicago.craigslist.org/search/sss?query=rigid+insulation
https://desmoines.craigslist.org/search/sss?query=rigid+insulation
https://hartford.craigslist.org/search/sss?query=rigid+insulation
Thanks again for taking the time to assist.
I corrected the "unvented" phrase.
If I pursue the cut-and-cobble approach, should I take extraordinary measures to seal the rigid foam layers in a vented assembly? Any problem with sandwiching fiberglass between rigid foam in this type of installation?
I think I'll use two layers of interior foam, staggering and taping the seams. Do you think the 3M 3067 tape fits the bill?
Dana:
Appreciate the suggestions. I live NYC metro area, so we have lots of salvaged board of every description. Thanks for the thoughtful low-cost suggestions. I imagine aged reclaimed product would be less prone to shrinkage. Will canned foam and tape behave in a similar fashion on polyiso as it does on XPS?
Tapes don't necessarily adhere well to all facer types, but if doing staggered layers it's worth taping the first layer, and letting the second layer clamp the tape in place. Taping both layers may make sense if it seems like the tape is adhering well, but if it's questionable there's not much point- just make sure the gypsum board layer hanging on the furring is air tight.
Can foam is more chemically similar to polyiso than it is to EPS/XPS, and does a decent job of filling in damaged corners, etc.
Thanks, Dana. I won't be using gypsum board. Would something like the Henry Blueskin product make any sense as an extra layer of insurance?
On a different note, do you think buying a used Graco proprotioner would be practical? Are they very difficult to operate and maintain? The 55 gallon drums of Corbond III are certainly cheap enough.
Ben,
Building codes require rigid foam to be protected on the interior with 1/2-inch gypsum wallboard for fire safety. The technical term for the drywall is a "thermal barrier."
If you are planning to substitute tongue-and-groove pine boards for the 1/2-inch drywall, you had better check with your local code authority before proceeding. My understanding is that 1-inch boards do not qualify as a thermal barrier.