Fastening Rigid Foam Over Vapor Barrier

Hello everyone,
I have a foundation in Climate zone 6 and have just installed 2″ of XPS foam horizontally in preparation for the slab pour (side note: tried to source both used and new Type II EPS but with no luck). After the house is built I intend to insulate the interior basement walls but for now I would like to attach at least a 6″ tall perimeter band of rigid insulation vertically along the bottom of the wall to thermally isolate the slab from the exterior walls, as in this article https://www.greenbuildingadvisor.com/article/183793
In diagrams that I have seen (such as the attached) the vapor barrier extends up the wall and behind the vertical insulation. My question is:
Does anyone have any advised methods for attaching this 6″ band of rigid insulation on top of the polyethylene vapor barrier without it floating around? I’m having a hard time visualizing how to keep it in place on top of the poly. Alternately, if I intend to fully insulate the wall in the future, is it fine from a thermal and vapor standpoint to attach it to the wall first and then run the poly over it? Thanks,
Eric
GBA Detail Library
A collection of one thousand construction details organized by climate and house part
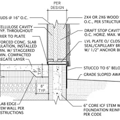
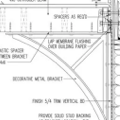
Replies
symphotrichum,
If you are doing your drainage work correctly, I do not think there would be much value in running the plastic vapor barrier up the wall. You should be sealed and drained on the exterior side such that your greatest remaining moisture load problem will be from wetness transferring up the wall from the footing. (and cold wall tops - later) The issue of "rising damp" can be reduced with a capillary break/sealing barrier on top of the footing (or other methods) before the walls are cast. Search the GBA site for references if you have not already addressed this and have not poured walls.
Regarding the wall perimeter foam - I have been using Fuze-It by Liquid Nails on interior ceramics and other materials with success. It dries slightly rubbery. The label specifically excludes polyethylene and polypropylene from the "many plastics" it can adhere to. However, if you are planning on a 6" band that should allow you to tack along above the poly vapor barrier sheeting. Unfortunately, some XPS foams have a film skin (likely poly) on one or both faces to improve water resistance. Inspect the stock you have and run a test. Fuze-It grabs immediately, but can take at least 24 hrs to cure fully if both surfaces are plastic. Others may have suggestions as to what doesn't dissolve foam and will also stick to concrete. You are in CZ 6, so you might want to check on your sub-slab R and wall R requirements. In my state for CZ 6 I need R15 for walls - R10 slab though R15 does help. Other wall details ahead.
To secure the edges of your plastic vapor sheet, consider the very sticky (albeit pricey) tapes with acrylic adhesives. Might be a good bet and cost effective if used in small bits. There have been recent Q&A threads about tapes that will seal rim boards to foundation and really stick. Also consider the "as seen on TV "- Alien tape, available at Amazon. And just to say it, the plastic barrier goes on top of the foam.
It does however, sound as though that you already have footings and walls completed, since you are speaking of setting the slab. I do hope that your exterior footing drain is set by the side of the footing and NOT onto the footing's top next to the wall. Again, this important detail has been addressed many times on GBA. Drainage lines are meant to prevent collected water or the natural water table rising up to the slab. And to keep water levels below your footing/wall capillary breaks.
The detail you linked to shows a slab/foam placement on top of footing with a full depth profile of rock to inside bottom of footing with drainage.(pipe too high, holes wrong side) The outside drain line should look similar, only with the addition of what is sometimes called the "fabric burrito" method of keeping your drainage pipes un-silted. Filter socked drainage pipe is not going to last on its own although under a slab there will be no soil above the drain line to infiltrate downward. The extension of the rock capillary break under the slab is called out at 4". This is adequate if you know the water table prospects and that the exterior drainage goes to daylight and is capable of keeping up with rain and snow inputs. Stepped footings and different slab/footing profiles will of course be different. However, keeping the exterior drain lines at the sides of stepped footings will help protect the value of footing to wall moisture break details.
I do wish the call-out specified WASHED stone, as you might not get clean stone if you don't spec it. I also sometimes see gravel specced under slabs, which seems to mean rock to some, but to me refers to a very coarse sand. Gravel would not be acceptable to me. You do not want a sponge under your foam. Whatever you do have, compaction of existing soils before placing the washed stone is good engineering practice at minimum and code many places. Planning sufficient depth of stone for placing radon mitigtion piping in advance of need is also a wise practice. Do you know your local radon risk?
Vertical basement wall insulation details are extensively covered in various GBA threads. The referenced diagram specs Thermax, a polyiso sheet with two aluminum skins. If properly taped the impermeable insulation will control for room humidity condensing on the cold concrete walls. How you intend to stick it to the walls is another matter. I have yet to see a wall as perfect as a diagram. Fuze-It might be good here, too. Hard to say. Your inspector may require sheet rock despite the aluminum skin or you might want to frame in front of the Thermax for additional fluffy insulation space and easy wiring. That said you will want to detail the Thermax (or other) at the top near the sill plate as much as the bottom and seams.
The wall at sill plate level and down to 2 feet (or more if sloping grade) will be very, very cold during the winter. This region will be at greater condensation risk than the wall near the floor. Here will be a good place to spend the time and money using quality sealing tape. The gaps behind the insulation sheets will cascade the cold air gap and interior humidity down behind if not sealed off. This is one reason why I opted for exterior insulation on my own foundation. I didn't need drywall for code and my basement is a shop not a living space. Less work inside, more work outside, take your pick when designing. A bit late for you I am guessing.
I personally would not select a more permeable alternate foam insulation. The vapor pressure will more often be toward the cold wall, not out of the wall. If you really are drying to the inside, I would say your foundation walls are too wet. I would work to control whatever is keeping your wall wet before moving ahead. Permeable is a two way street, so no sense making your dry but cold foundation wall wetter from interior humidity. Sealing the seams, fastener points and the top will be true for all types.
Do be prepared for the slab to pull back from the perimeter foam. I used the shrinkage to my advantage. I placed thin sill sealer foam on the walls, poured the slab and after shrinkage pulled out the sill sealer foam and then sealed the slab edge for radon control. With perimeter foam in place you will need to seal the foam to the wall and to the slab to control for radon.
Good luck and I promise I won't tell anyone you are part of the Astor family. They will think you are rich.
Onslow,
Thanks for your detailed reply. As a botanist I appreciate your botanical humor at the end!
I did apply a capillary break between the footer and the foundation walls and applied 3 coats of elastomeric waterproofing on the exterior walls. I have an interior drain system and radon system (very low risk at my location but just in case) in an 8" bed of crushed stone, and my exterior drain is to the side of and below the top of the footing in the fabric burrito style. I had extra fabric and so did a complete double-wrap around the first burrito! Thanks for the details on various adhesives, I appreciate you taking the time to respond,
Eric
Hey Eric,
Not sure if you've already poured, but I think you would be fine to place the poly inboard of the foam, especially since it's only for 6" and it would be in-line with the stack-up of the horizontal portion (poly over foam). I assume the slab is getting poured against this, so around 2" of foam will stick up above the slab to tie future insulation into?
With this order, you could tack the foam to the concrete wall with an adhesive (I've used great stuff pro construction adhesive, but there are many tube based products available as well), then the poly can be lapped up over this foam and taped to the concrete (if wanting an air-tight seal for radon). I might consider running the poly long before the pour, because it might get pulled around, then after the pour trim it and tape it or seal it with a sealant to the concrete.
If you're planning to use more rigid foam later (such as for the roof) you might want to check out this thread https://www.greenbuildingadvisor.com/question/sourcing-eps-foam
Tyler,
Thanks for the response. I haven't poured yet but did end up already placing all my rigid insulation down, with the poly on top and all taped. Looking at other threads on this site (especially comments by Martin Holladay) I decided to not run it up the wall. I actually ran up a few inches just so I could tape it so it wouldn't pull away when we were walking on it. You are correct in that I will have about 2" sticking up above the floor to tie future rigid insulation into. Thanks for the link to the sourcing EPS discussion! I think my major error was just not giving enough lead time to source and stockpile EPS. I think I'll start looking and buying now for my spring 2023 roofing needs.
-Eric