Assistance with Attic Mold on my clients’ home

Let me start by saying that I am sorry this is going to be such a long post. But I have spent countless hours over several winters now trying to assess this problem. And I guess I feel that for any of you to be able to give me an informed opinion as to the cause(s) of my problem and any subsequent suggestions/solutions, I have to give a thorough explanation of the project background and site conditions. I’ve also attached a few photos to help visualize the situation. And so I come to you GBA experts, on bended knee, in the hope that you can generously impart some of your wisdom. Here goes….
As you see from the post subject, a client of mine informed me a few weeks back that they’ve discovered mold in their attic. Back in 2009, we did a pretty major remodel for my clients’ home, here in Boulder County, Colorado. Primarily, it was a “pop-top” with a re-configuration of their split-level home. We removed partition walls on the Main level to create a Great Room (Kitchen/Dining/Living Room). Over this space, we then added the new second story Master Suite (800 SF). The old, existing second level over the garage (3 Bedrooms and 1 Bath) was only moderately reconfigured. Two of the Bedrooms were combined into one, with the walls reworked, primarily to accommodate the new stairway up to the Master Suite.
The East half of the new second level Master Suite incorporates a large Bath, a walk-in closet, and a Laundry Room. The West half is the Bedroom sleeping quarters. The North side of the Bedroom quarter also contains a small walk-out Balcony, 4 feet or so of which is carved out of what would otherwise be “Interior Space” – meaning inside the North load bearing wall. T &G Cedar comprises the soffit over the balcony. Over the Bedroom Quarters/Balcony we used scissor trusses to create a vaulted ceiling. Standard (fink) trusses span the East half. Both are a 3:12 pitch. Gable truss on the West end; on the East, a stick-framed hip roof comes off the new ridge, ties into the existing, lower roof, creating a small attic space in this frame-over area. Access to this new attic space is through a 3’x3’ door in the East Wall of the Laundry Room, which itself is on the North side of the addition, adjacent to the Closet and east of the Balcony.
It is in this new attic area that we installed a new Carrier 80% efficient furnace, dedicated solely for the new 2nd story addition (Master Suite). Its insulated ducts run throughout the webbing of the trusses. We also installed a dedicated Aprilaire humidifier for the Master Suite. Because we couldn’t run any water lines into the attic for the humidifier, we instead framed an insulated chase adjacent to the furnace into which we installed the unit. A dedicated supply duct runs from it into a register on the wall of the Master Bedroom, its return air duct terminates on the ceiling of the Bedroom Hallway.
Other pertinent construction facts:
• We installed 28 LF of GAF ridge vent, with a 3”-4” gap between the sheathing at the ridge (2.17 SF of NFVA); no additional passive vents on the roof or western gable wall.
• 7 soffit vents along the North eaves; 6 soffit vents along the South eave (1.36 and 1.16 SF of NFVA, respectively).
• 3’ roll of OC Weatherlock-G installed along all new roofing eaves.
• Steam Shower in the Master Bath. Just outside the shower, we installed a 80 cfm Panasonic Fan, with a dedicated 4” duct, terminating through the roof.
• Several feet away is the WC, with a pocket door; it has its own Panasonic fan that terminates through the roof via flex ducting.
• The attic is insulated with kraft-faced R38 batts; the trusses all possess energy heels.
• Insulation chutes/baffles are installed in each truss bay with a soffit vent.
• The dryer, in the laundry Room, vents directly outside through the exterior North wall.
• The access door from Laundry Room to Attic has two doors, with a gasket lining the attic side door to help better seal it off.
• Air-tite recessed cans in the Master suite – not particularly well-sealed however.
• 3 return air grilles in the Master/Master Hallway ceiling (2 for the new furnace – one inside Master Quarters, one in the Hallway outside; 1 for the humidifier) – none particularly well-sealed.
• There is a 1.5 ton a.c. unit for the Master Suite outside; its line-set runs through the attic space to reach the furnace.
The first winter after we completed construction, we noted some condensation drips coming out of the soffit vents, primarily over the Balcony. I examined the attic and noticed frost on the roofing nails and the underside of the roof decking along the North side. I felt it was possibly just a result of all the new wood framing/truss members and OSB sheathing releasing their moisture. Also, because it was most noticeable in the area of the Balcony, I felt that much more cool air was getting into the attic in this area due to the inevitable gaps between the cedar T&G boards in the soffit area over the balcony.
We monitored the situation over the next weeks but noticed that they were experiencing significant ice damning along the north eave/gutters of the addition. I checked my venting calculations and confirmed what I believed to be sufficient venting for the attic area: approximately 4.69 SF of NFVA for 960 SF of attic area, or a 1:220 ratio.
In the late spring, I consulted with my roofer. Per his suggestion, we decided to install a solar-powered GAF intake booster on the North West corner of the roof, hoping it would draw more cool air into the attic, increase air movement, and aid the convection process, so that the air would more effectively work its way out through the ridge vent. I was ambivalent about this, particularly given that with the low pitch of the roof, and the winter sun as it is, the fan wouldn’t really work until well into the morning – probably too late to impact the condensation process at the most critical times of day. A year and a half later, I have no reason to believe this intake booster has helped one iota.
We didn’t really check the attic last winter – but we also had a mild winter and didn’t have significant snow/ice damning so we assumed all was reasonably well. Then we hit a bad stretch just after Christmas this year. A big snow, a big stretch of warm weather, melting much of the snow, and then a deep freeze. Ripe conditions for ice damning. My clients went into the attic, where they store Christmas decorations and other odds & ends, and found the mold. I immediately went over to look and saw the bad news. The mold is growing primarily on the OSB roof sheathing, down close to the eave along the North side of the house. Some of the truss tails have also been “colonized”. Some mold has crept some 3-4 feet up towards the ridge.
I immediately kicked into high gear and called an environmental air specialist to assess and test the mold. The result was good in as far as we didn’t have any elevated spore levels inside the living quarters. But we obviously have to remediate the mold. But I first need to determine and remedy the cause. The air specialist felt sure that the primary cause of the moisture/mold was due to the humidifiers. I say humidifiers plural because, in addition to the dedicated unit for the Master, they also have one for the main furnace in the basement as well. That unit supplies the rest of the house and, given the new open floor plan we created, its humidity surely works its way upstairs as well.
My clients have told me that they have the dedicated humidifier for their Master turned way down to a setting of 20% causing it to rarely turn on. The one for the rest of the house is set upwards of 45% RH.
I started meeting with all the pertinent subs (Roofing, Insulating, Gutters, HVAC) on site to discuss possible causes/options. Some were subs involved in the remodel, some had never been on site before. I wanted both perspectives, as you can image there might be some biased input…
From my own knowledge and experience, as well as the input of the varied subs, the causes could be many. Some of my colleagues believe, like the Environmental Air Specialist, the primary culprit to be the humidifiers. A few have felt it is the fact that we have located a furnace in the attic. Others, including another HVAC company that didn’t do the install, don’t feel the furnace is at all a likely culprit. Some posit that it is the ice-dams that have started to saturate the decking, by working their way up and under the flashing and Ice & Water. Perhaps it could be the low 3:12 pitch along with all the supply/return ducts running through the tight attic space, clogging air flow. It could be that we should have more passive vents on the roof. Perhaps I should have eave vents/chutes in every truss bay along with a continuous soffit vent. Maybe the lack of better sealing around the recessed cans and air supply registers/return air grilles have been allowing the humidity from the humidifier(s), the Laundry Room, and the steam shower to escape up into the attic. Perhaps, as I have started to believe, it is that the total is greater than the sum of the parts…
As for solutions, there have been many suggestions that include:
• Shutting off the humidifiers to stop the humidity – something that by most accounts we shouldn’t really have installed here in our climate, particularly now with a remodeled and tighter home. Seems like an obvious, good solution and they have since turned them both off. Of course I feel bad that we spent the money to install it in the first place, because they love having humid air in winter, and I didn’t really try to dissuade them of adding the new humidifier to their Master Suite. I don’t yet know if that has helped alleviate the situation.
• Installing 1 or 2 electric-powered roof vents near the ridge that would forcibly draw the warm air out of the attic. This could help the problem if we are indeed too “socked-in” due to long runs of ducting and the low pitch. Moreover, it could help draw out heat from the furnace if that is indeed a primary cause. But this plan concerns me because it could merely create positive pressure in the attic, drawing more air from the living space below and/or drawing air instead from the nearest location: the ridge vent, thereby entirely short-circuiting the eave vents allowing that cool air to remain and condense.
• Converting the entire attic space to a conditioned one, by installing closed-cell SPF insulation and closing off all vents. This was an option I offered to my clients at the outset of the project. They didn’t want to spend the additional money, though it wasn’t as though I warned them that if they didn’t opt for this route they would inevitably wind up with mold. At this point, given the design of the trusses and the ducting, it would be VERY difficult and VERY costly to attempt an SPF retrofit. So not really an option at this point.
• Separating the furnace from the rest of the attic, by framing a partition wall. This might alleviate some of the heat – assuming it really is kicking in that much heat, but it would be, practically speaking, very difficult to do at this stage, with minimal access and all the furnace ducting. Moreover, we’d then have to condition the space where the furnace sits and that would be difficult and very costly to spray foam the roof deck and walls.
• Install heat cable to prevent ice dams. This is something that several subs felt was the best solution. My clients had long been asking about installing heat cable. The dams and icicles have been a concern of theirs for the past couple winters. So in fact, we went ahead and installed about 100 LF of Raychem’s 240 V WinterGard Wet in the gutter/downspout along the North eave of the Master. To me, this may help but it also seems that it could simply be an expensive band-aid – not really addressing the problem. But as some colleagues have felt, including the heat cable installer, Colorado simply has unique conditions, ripe for ice dams. That perhaps because of the snow/ sun/heat/freezing cycles we get here along the Front Range, along with a low-pitch, North facing roof, this is an exterior issue, first and foremost, and that the roof deck has been compromised as a result.
• Install a 14”/16” Aura vent on the roof above the furnace, and perhaps several more along the North ridge. And then installing either a continuous soffit vent or adding larger (16”x8”) vents to each truss bay. Together, they could help with air flow. But would I then need to block of the ridge vent to avoid short-circuiting?
Of course whatever the best course of action is, the major concern is remediation of the mold. Because it is so tight in the attic, particularly in the scissor truss half, the cost of working from inside the attic makes it a very difficult and expensive proposition. And of course my liability insurance has the standard mold exemption and I honestly had never thought twice about adding a mold rider to my policy. We live in Colorado for God’s sake!
To better help the mold remediation process and save some money, my initial plan is to remove the first course or two of sheathing and roofing on the North side, thereby removing the vast majority of the mold. That should then allow better access – from the outside – to clean the remaining mold off the trusses and sheathing. It would then be an easier time to install additional soffit vents and chutes, and close off the ridge vent, if that is deemed the best plan.
But I can’t justify doing the remediation until I know that I’ve solved the problem and eliminated the cause of the mold in the first place. And that is my conundrum. Whither which way do I go…? I should say that, fortunately, my clients had long ago become friends, so there isn’t any contentious energy between us (so far…..) They know that I am working diligently to come up with a solution to remedy this situation. But come up with a solution, I must. And so I turn it over to you and thank you in advance for your input. And again apologize for the size of this post.
Sincerely,
Chris
GBA Detail Library
A collection of one thousand construction details organized by climate and house part
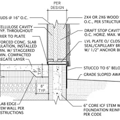
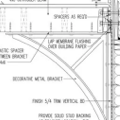
Replies
Some photos from the project. More available if requested. Thanks
Turn off your humidifiers and I suspect it will do the trick. That's exactly what I did in my house years ago and it worked.
The second thing I would do is look at the steam shower. I think an 80CFM fan on a 4 inch duct is way too weak for a steam shower area. Do you know for a fact they use the vent fan every time they use the steam shower and leave it running for say 15 minutes after? Are the ducts restricted or vent opening clogged?
Tell us about the basement or crawl space. Is it finished? Insulation under slab? Some basements can be real water generators, even in Colorado.
Billy
In addition to what William says, I suspect you have a lot of warm, humid interior air leaking into the attic. Some of it is leaking out of the furnace and ductwork, and some of it is leaking through the can lights and other holes in the ceiling. Get someone with a blower door, a duct blaster, and skills in pressure diagnostics and air sealing, and have them do everything possible to create an air barrier between the house and the attic. They'll need to move all the fiberglass out of the way and get at everything. They'll need to seal the ductwork and the other mechanicals in the attic.
After that's done, get yourself several dataloggers and put them in various places around the house, along with one outside and one in the attic. Collect data for a week or two here and there, and you'll likely figure out if there is still an issue, and what's contributing to it (i.e. there may be a room or area where the humidity is typically higher than elsewhere). I see a fair number of problems with humidity that are caused by people showering without the fan running, and/or fans that don't move enough air.
I believe that your NFVA is the problem. Awhile ago when figuring venting on a remodel project, a ventilation expert warned me about having larger capacity for venting at the top than at the bottom. A reverse ventilation can occur, with cold air being pulled down through the ridge, and thus trapping warm moist air in the attic. You need CONTINUOUS SOFFIT venting if you have continuous ridge venting. It should be equally balanced or greater at the bottom side. Do not close that ridge vent off!
Chirstopher,
I'm just guessing, but this project seems to include a collection of factors that fall into the "what not to do" category -- and they could all be contributing to the problem. Ideally, this project needed:
1. A well-defined air barrier separating the conditioned space from the attic space. This air barrier should have been tested with a blower door during the construction.
2. This air barrier should not have been penetrated by recessed can lights. The presence of utility chases and kneewall access doors sets off alarm bells.
3. All ducts should have been located inside the home's thermal envelope.
4. The furnace should have been located inside the home's thermal envelope.
5. There was no need to install humidifiers; in fact, humidifiers are dangerous.
6. Great care should have been taken to assure a very tight air barrier in the area of the steam shower and the steam shower equipment -- this may or may not have been done.
At this point, the key problem is the air barrier between the conditioned area of the home and the attic. Now it's almost undoubtedly full of holes; duct leakage may be contributing to the problem.
There is no magic wand to solving problems like this one. All of these are design and construction problems; all could have been easily solved at the design and construction phases, but are very difficult to solve after the project is complete.
You have two choices:
1. Get a blower door and a Duct Blaster on site, along with a home performance contractor experienced with these problems, and go through the painful, slow process of trying to plug all the holes in your home's air barrier and the duct leaks. Corrections may involve opening up drywall. While this work is going on, take the humidifiers and put them in a Dumpster.
2. Install spray foam on the underside of the roof sheathing and create an unvented, conditioned attic. While this work is going on, take the humidifiers and put them in a Dumpster.
That is like rebuilding the place, Martin! You are right about there being so many factors, but if this were an older home(MORE LEAKY), there would not be the mold problems. The problem is that this house is tight enough to have problems when things are not detailed fastidiously, which is a common problem with buildings today. I really recommend getting rid of the humidifiers, increasing some exhaust only ventilation, and installing CONTINUOUS venting in the soffit. If vapor is getting through the drywall and traveling with the moist warm air leaking into the attic, then it is sticking around long enough to cause mold because the ventilation chute is NOT flowing up at a reasonable rate. Vented roofs are dangerous when not vented correctly! Then remove the fiberglass and blow in the maximum possible amount of cellulose given the eave depth. It will manage the moisture. Forget about bandaids with the weatherization guys. Venting, dehumidification, and the right insulation will fix this, everything else is too "normal" to be causing such problems.
Good luck Chris. Lots to learn. You need to have eyes onsite. Mold=moisture. Stop the moisture.
>>The problem is that this house is tight enough to have problems when things are not detailed fastidiously
I don't agree, or at least I don't think the OP states anything that leads to that conclusion. The house could be leaky at the ceiling plane, enough so to allow a lot of humidity into a cold attic where condensation then occurs. The HVAC could be leaky enough to put a lot of humidity from the interior and from the humidifiers into the cold attic. There may be issues with the roof venting but I bet there are much bigger issues with air and duct leakage.
The furnace that is currently in the attic is for the Master Suite only correct? If so, it sure seems like finding an alternate way to heat that room and getting the furnace out of the attic would be a very good thing. Vented attic, furnace in attic, cold climate, not a good thing IMHO.
Thank you all for your input, advice and expertise thus far. I really appreciate it. What makes this particularly frustrating is that there simply are quite a few varied opinions about causes and possible courses of action. Not that I expected, as Martin stated, some “Magic Wand”. Because of course each suggestion you’ve all made has validity.
I was looking forward to your input in particular, Martin. And I acknowledge that there are many aspects of the design of this project that were not optimal. I guess I’m a believer, like you and William, that as much as the envelope isn’t evidently as tight as it could or should be, the humidifiers had to have been a major contributor. As I stated before, I should have discouraged their installation and/or continued use. But I didn’t truly expect this would be the result or else I would have given them a strong caveat or disclaimer. I guess that may have been my biggest oversight. A very tough lesson, if not entirely my “fault”.
I do think that a conditioned attic would be/would have been the best way to go. But as I mentioned in my original post, my clients didn’t want to spend that extra money at the time. And it’s not as though a blown or batt-insulated unconditioned attic can’t function efficiently, because we’ve all seen them and they still are prevalent. That said, something is preventing the unconditioned space from working efficiently.
Martin, I have to agree with Matthew’s point that in order to pursue your Option #2, spraying foam insulation and creating a conditioned attic, I might as well re-build half the house. I’ve no doubt that your prescription would work or that it would have been the way to go from the outset. But whatever I do, the cost will be borne primarily by me. And so even though I won’t take a short-cut, I’m surely looking for the most cost-effective plan that will remedy the problem. And I guess I’m still hoping to find more “conservative” solutions.
As to your first point about a well-defined air barrier, I’m curious if you could expand on what precisely you mean or would have done, given the plan for kraft-faced batt insulation? I’m assuming you wouldn’t have preferred a poly vapor barrier? I suspect you and Dr. L are on the same page with regards to that?
I have to state that as much as I wish I could incorporate all the best Green Building techniques on the projects I am contracted to do, I’ve just found that it isn’t always financially feasible – particularly since remodeling is my focus. I have found that, despite my attempts to educate and encourage, when it comes right down to it, most of my clients aren’t willing to spend the extra dollar for greater efficiency and down-the-road benefits. Of course I wish they were. And, bit by bit, as we know, general public awareness is expanding and costs are coming down.
I’ve no doubt the furnace is adding some moisture/heat to the attic. Not probably the best design, but I wasn’t the architect. Of course the buck stops with me and I didn’t protest this plan. Perhaps I should have and I surely would in the future. And though this project is in Boulder County, it’s within an incorporated City that, unlike the City of Boulder’s latest code, did and does allow ducting in unconditioned spaces. So surely that isn’t optimal either. But are they the main culprit or just a contributor? And as I stated in the first post, I had a well-established HVAC company based in Boulder come to assess things. They are a company that didn’t do the original work and would have every competitive incentive to denigrate the installation - and they didn’t feel that the main issue was the furnace in the attic. They also felt that the insulated ducting was as well-sealed and installed as could be expected. They also, I acknowledge, could flat out be wrong.
But even if the furnace/ducting is a main culprit, it would require another major and costly remodel to figure out a new way to locate either/both of them. And so, I’m still hopeful that other options exist to counter whatever negative effects are being contributed by the furnace and ducting and that will allow them to remain. That is why I’ve considered installing an Aura vent directly above the furnace, where there currently is no passive venting. Because the ridge vent begins some 3 feet to the West of the furnace, it seems that this might be very helpful.
And this brings us to overall NFVA of the attic. Matthew, you’ve hit on a point that I’ve been considering first and foremost. Whether I do or don’t install additional venting near the ridge, it seems that more air coming in at the eaves would be a good idea. It surely couldn’t hurt. But even in the bays where there is a soffit vent and chute, mold is evident – though significantly less than where those bays that contain no vent or chute. And as of now, there isn’t any evidence of mold on the South eaves. The Southern sun radiating through the roofing/decking is evidently warming/drying the Southern half of the attic sufficiently to prevent mold from growing there. So does that then mean it might be that the ice dams on the North are a major factor?
In any case, one of my next steps, David and Martin, has surely to be to get an energy audit to assess how “leaky” the Master ceiling penetrations are and, subsequently, better seal them.
And to answer/comment specifically on a few of your posts:
William, the home has a full basement 4/5 of which is finished. Given the age of the house 1978 and the techniques that were used around here at that time, I highly doubt there is any insulation beneath the basement slab.
As for their Steam Shower, we didn’t use any poly vapor barrier but the backer board was taped at all seams and a liberal coating of Laticrete water-proofing membrane was applied. The shower is entirely 3/8” glass enclosed with the fan installed just outside the door. It is in fact a Panasonic 150 cfm unit. And there is a second unit, 50 cfm, merely 6 feet away in the WC. Each unit has its own dedicated duct that terminates through the roof. My clients insist that they always turn both fans on when they have a steam shower, and let them run (on timers) for a good 15-20 minutes after they finish. And they say that, on average, they use the steam unit maybe 4-5 times per month. So I’m not thinking that, overall, the Steam Shower is a significant contributor of moisture….
AJ Builder, I don’t know what you mean by “eyes on site”…? Mine are there, if not constantly. I’d rather not move in to the attic…
Aaron, as I stated earlier, though it might be ideal, relocating the furnace and its ducting is not really a viable option. I guess if there was some Omniscient Voice that told me this was the one and only issue, I may have no choice. But it seems, I hope, that there are other contributors and options than your costly, if valid, suggestion.
And finally, Matthew, as I’ve said, I agree that more ventilation could be a good start. I’d like you to let me know what you specifically mean by exhaust-only ventilation? And I guess I’m not sure about the ridge/soffit balance in favor of the soffits, that you allude to. But you may well be correct. And I’m also not sure that the cost of re-placing all the R-38 batts with cellulose is justified. Though again, you may well be right. Anyone else have a comment on that? (I will say that some of the batts will have to be removed because of the mold. So this would be the time to do it, if that would be a significant benefit.)
So there we are. Again, I appreciate all your input and advice and welcome more input and comments. Thanks again.
Chris
Christopher,
First of all, a disclaimer: there is no way I (or anyone else responding on these pages) can diagnose a problem in this house in Boulder, Colorado without visiting the site. Much of my advice will be based on hunches and incomplete information. As a result, my advice is worth exactly what you pay for it.
Clearly, insulating the rafter bays with spray polyurethane foam would be cheaper than relocating the furnace.
I have no idea whether you need to perform more air sealing work on your ceiling, but further money spent on air-barrier diagnostic work will be money well spent. The results of the diagnostic work may be reassuring. On the other hand, if you find major air leaks, then correcting those leaks will certainly lead to improved building performance.
I would recommend that the house be depressurized and the ceiling be examined with a smoke pencil. I also recommend that the house should be pressurized and the interior of the house should be filled with fog (using a theatrical fog machine), with someone looking for fog in the attic.
That said, the cheapest approach would be to physically remove the humidifiers and wait for a year. Perhaps that's all it will take to solve the problem.
Q. "As to your first point about a well-defined air barrier, I’m curious if you could expand on what precisely you mean or would have done, given the plan for kraft-faced batt insulation? I’m assuming you wouldn’t have preferred a poly vapor barrier?"
A. Here's what I would have done: once the drywall work was complete, I would have tested the envelope of the house with a blower door and a fog machine. At that stage of construction, it would have been easier to correct any air leaks in the ceiling air barrier.
Polyethylene is not a very good air barrier. Gypsum drywall makes a perfectly acceptable ceiling air barrier, as long as it isn't penetrated by recessed can lights, as long as all access hatches are carefully weatherstripped and sealed with cam-action latches, as long as there are no utility chases between the conditioned space and the attic (or all utility chases are meticulously air sealed), and as long as all duct penetrations, plumbing vent penetrations, and electrical penetrations are carefully air sealed.
In the post some things that stuck out.
1 The use of batt insulation thet combined with trusses makes me wonder on the qaulity of the install.
2 canned lights that may not be well installed
3 attic used for storage
4 HVAC in attic
He mentions a tight house but was it tested and what steps were taken to make it a tight house. My comments ,1 & 2 make me think it is not tight.
For attic access is there a well sealed and insulated hatch. Is there a platform above the insualtion to keep stored items out of the insulation or is stuff placed on top ofthe insulation.
What is the source of mositure in the attic. Is it the ice dams or coming from the inside or both. I think ice dams would lead to more local water issues.
Have vent chutes been placed between each of the trusses or every 3 or 4th. What is the gap between the chute and bottom of the roof, should be 1 1/2-2 inches. It does little good to have venting if there is not good airflow from the bottom to the top.
The HVAC system is contributing to the heat load in the attic and the ice damming. Good venting hill help minimize the effect. I am not a fan of RB's but I wonder if a RB foil could be used in some areas to redirect the heat away from the sheathing and provide air flow channels.
I think the best starting point is a blower door test to identify the amount and location of leaks. Pull the batts out and install blown in insulation, my preference is cellulose.
Tell it, brother! I think most of us have one or two somewhat similar and expensive lessons in our past.
But the issue that you're rightly taking responsibility for here is not energy performance, it's the mold and if you've had the attic ducts and furnace thoroughly checked out by a knowledgeable third party I seriously doubt they are a contributing cause. Nor are ice dams likely to be the issue unless you're also seeing liquid water on the interior of the sheathing - the absence of mold on the south slope is just an indication that condensates burn off under the daytime sun before they have a chance to cause problems. The presence of the two humidifiers is a clue that the core of the problem is humid air leaking from the house to the attic and dry air leaking into the house from outside to replace it: humidifiers are typically installed to reduce occupant discomfort in those conditions. I doubt if your clients will be happy with their removal if no steps are also taken to retain naturally higher humidity levels in the home. The real lesson here is that eliminating those air leaks at the construction stage is not just good construction practice, it can also avert a major liability issue.
When I referred to NFVA balance, I believe it very important to have ventilation at top and bottom be equal, or offset to advantage. If your wood stove was up on your roof above a cold pipe, it would not draw very well. The warm air comes from below, and needs to flow efficiently upward, and although this is usually not an exact science to perform adequately, sometimes physics can bite us in the ass. The grill vents you have at the bottom would not be enough NFVA to balance with a continuous ridge vent even if it were continuous. You need to use screen or a coravent product like raftavent. These will be more NFVA per foot. In this case you may need to get creative. As far as the cellulose goes, why not just blow it on top of the fiberglass, getting higher than R-38(not counting the leaks) would help you tremendously given this situation, and cheap to boot. And last, the ventilation issue. Are your bath fans on timed ACH(air changes per hour)?
My suggested remedy: clean up the existing mold, air seal the ceiling/attic structure as much as possible, increase your roof ventilation to meet the guidelines developed by the CRREL both for area and thoroughness (http://www.crrel.usace.army.mil/library/booksnongovernment/MP02-5778.pdf), spray the underside of the roof deck and trusses with a non-toxic mold proofer.
Not an ideal solution, but a reasonable start that may not break the bank.