ARXX ICF versus Durisol ICF in a Mixed Humid Climate?

I’m trying to evaluate the pros and cons of using ARXX ICF versus Durisol ICF in a mixed humid climate. I’ve used ARXX here in North Carolina and definitely like the system. I’m considering Durisol because I would like to direct-apply a stucco finish. I’m familiar with a Durisol – type system built in a cold dry climate (Innsbruck) and it seems ideal still many years later. However, i have heard concerns about moisture in the wall assembly as well as thermal bridging in the Durisol product. I’m grateful for any help…
GBA Detail Library
A collection of one thousand construction details organized by climate and house part
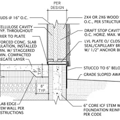
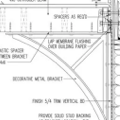
Replies
The Durisol has a lot of air space built into the block, and the blocks dry readily. If you want to stucco right on to it, it's a no-brainer.......
Randy:
There are some who feel you still need to use a lathe for stucco on ICFs. For a level-headed discussion of those reasons, I encourage you to contact Terry Collins (of PCA) at (847) 966-6200.
Take care.
I am writing this to “set the record straight” about the concept of thermal bridging in wallforms made of cement/wood-chips. I’m a homeowner doing research on what to use for my own house. And I’ve noticed a few places on GBA where there exists this notion that the webbing material of Faswall is a thermal bridge. This is a pretty serious claim, but it turns out that it’s not true, and I’d like to offer an explanation. Both for my own benefit, and also for the benefit of other homeowners doing their own research in the future.
Faswall is on the opposite side of the continent from me. However,a comparable product, Durisol, is located close to us. So my data and research comes from looking at Durisol. They both use a mix of petrified wood chips, recycled from softwood lumber production (pallets, off-cuts, scrap). I believe the webbing material for both products is very similar, but I could be mistaken. Let’s assume it’s similar.
I’ve seen the lab report that tested the webbing material to have an R-value of 1.75 per inch.
It is fair to say that a material with an R-value of 1.75 per inch is a fairly poor insulator. Especially when compared to XPS at R-5.0 or mineral wool/Roxul boards at R-4.0.
However, it’s NOT fair to say that a material with an R value of 1.75 per inch automatically becomes a thermal bridge in a wall assembly. It depends on what else is going on in the wall assembly.
A thermal bridge is an area in a wall assembly that is RELATIVELY or COMPARATIVELY conductive to heat energy when compared to the other areas in a wall assembly. The classic and notorious example is wood or steel studding. A softwood lumber stud has a value of around R-1.25 per inch, and it’s typical fiberglass batt neighbour is around R-3.1.
A 2x4 wall has some of it’s surface area represented by a 3.5” deep piece of wood, for an R-value of (3.5* 1.25 =) R-4.4. Then it has a greater surface area represented by 3.5” of insulation material, say fiberglass batt (3.5”*3.14=) R-11. Yes, there is sheathing and siding and drywall, but I’m trying to isolate the concept of thermal bridging and keep it simple.
Part of the wall is R-4.4 and the other part is R-11. That represents a huge disparity in the relative insulating value of each. So thermal energy finds it much easier to flow through the weakest link in the chain, being the studding, and you therefore have a wall assembly with tons of thermal bridges. It performs nowhere near R-11 when you look at the whole wall assembly.
Let’s pretend for a moment that we had the option of building a wall of ONLY softwood lumber. And that we could get it 12 inches thick, using really big, perfectly square logs. Rather like a log home. Such a wall would have an R-value of 12 * 1.25 = R-15. But because the wall assembly was all the same material, across the whole surface area and depth, there would be NO relative bridging. There is NO relative weak spot. So the relatively poor insulator, wood, can be a thermal bridge in ONE assembly, but definitely NOT a thermal bridge in another assembly.
If you look at a typical Durisol wallform – let’s look at the 12” thick form – see the photo attached. It has 4 dimensions in the photo:
T – total thickness of the form, being approx. 12”
t- thickness of the webbing on the inside (and the outside) in the area where the concrete goes, being 1 ¾”
I – thickness of the insulation insert, being 3”
H – thickness of the concrete fill, being 5.5”
Across the wall’s surface area, you will have places where there is a sandwich of webbing-insulation-concrete-webbing. Or you will have webbing only.
If the webbing is R-1.75 per inch, and there is 12” of it, then its R-value is about R-21.
The concrete sandwich part is: 3 ½” of webbing (R-6.1) plus 3” of Roxul board (R-12) plus 5.5” of concrete (R-0.5) for a total of about R-18.6.
This makes a wall assembly that is relatively FREE of thermal bridging, because the different areas of the wall have relatively similar R-values. There is no obvious place where the heat is going to tunnel out, like with a highly conductive steel stud, or a typical softwood stud. And when you look at the webbing in isolation, you actually see that it’s the strongest part of the wall, at least thermally speaking in R-values. So an R-21 web inside a wall that’s rated R-21 is definitely NOT a thermal bridge in that wall assembly.
Plus, once you get into relatively thick walls, the “rules” about thermal bridging get more obscure. Because thermal energy doesn’t just take straight paths, but rather it interacts and dissipates inside a wall – especially a thick one. The bottom line is that “thin” walls like a standard 2x4 or 2x6 wall are vastly more susceptible to obvious bridging.
The thermal imaging photos also show a distinct lack of bridging.
Zenon,
You've done a good job of explaining thermal bridging. You understand the principles well.
However, your analysis of heat flow through a Durisol wall is incomplete. You haven't made a 2-dimensional analysis, much less a 3-dimensional analysis. You have made a modified one-dimensional analysis, which is of limited use.
Your analysis would be a pretty good way to estimate the R-value of a Durisol wall if the voids were filled with air. Once the voids are filled with concrete, however, your analytical method becomes incomplete.
I don't know whether Durisol expects the insulation insert to face the interior or the exterior; but for the purposes of thermal analysis, it doesn't matter much. Let's assume the insulation inserts face the interior.
There is 1.75 inch of material (wood chips plus additives) between the concrete and the exterior. (I'm ignoring the stucco). That material has an R-value of about R-3. That's not much. That's all there is separating the concrete from the outside world. When the outdoor temperature is cold, the concrete will be fairly cold too -- definitely colder than the indoor temperature (although not, of course, as cold as the exterior air).
The interior heat will leak through the Durisol block and be absorbed by the cold concrete. The maximum heat flow will occur at the inside corners of the cold concrete. At those points, there is only 4.75 of Durisol material between the cold concrete and the interior. That's something -- and it may be enough to avoid cold stripes on your wall. But analyzing these two-dimensional heat flows is tricky. You need a good software program like THERM to see the isotherms created by this type of heat flow.
Once you introduce three dimensions into the equation, with details at the bottom of the wall and the top of the wall, the thermal analysis becomes still more complicated.
Most building scientists find the the best way to determine the thermal performance of this type of wall is to measure heat flow through a completed wall assembly measuring 8 feet by 8 feet or 8 feet by 12 feet. Oak Ridge National Laboratory has a calibrated hot box that is large enough for this type of measurement, but as far as I know, no one has ever performed this testing on a Durisol wall.
Zenon and Martin, this is one of the most elucidating exchanges on all of GBA. There are so many treasures hidden here... the only way to find most of them is that little search box in the upper right hand corner.
ICFs like Arxx, Nudura, etc (2.5" foam x 6" concrete x 2.5" foam) have already been tested by Oak Ridge National Laboratory's hot box and have been rated around R-22 average. Unlike Durisol which has not been tested in a hot box so it's all theory and conjecture about the efficiency of the Durisol units.
In addition, ICF like Nudura can accept stucco directly to the EPS surface WITHOUT the need for a metal lathe or any skim coats. Synthetic stucco products like StuccoMax adhere directly to ICF without the need for metal lathe. It is a one coat/two-pass system that adheres directly to the EPS in ICF and uses a plastic mesh that is embedded prior to the second pass. StuccoMax contains ZERO Portland cement so it won't crack due to freeze/thaw cycles and it is non-combustible with a rating of 2,500 psi.