Are there more cost-effective ways to dry an old basement?

I have a 100 year old 21″ thick fieldstone foundation in region 5 that has cracks and leaks water into the basement in the rainy season. I have read the above manual mentioned above,
https://www1.eere.energy.gov/buildings/publications/pdfs/building_americ…
as well as a fine home building article by Joseph Lstiburek as well and is there a way to use any less expensive product to allow for an interior drain plane such as dimple mat backed up with taped XPS or EPS foam instead of just closed cell spf? The cost of 3″ spf is around $5 and will price me out of being able to do my home.
The top of the insulation and dimple mat could be sealed airtight to the foundation wall as well as the dimple mat terminated and taped to a floor drain mat in one version of this drainage system or sealed within the concrete drain tile trench ( with no floor drain mat) as shown in others so that no interior air would be able to contact the stone wall.
Any ideas of water control with insulation to allow for a conditioned basement would be greatly appreciated
GBA Detail Library
A collection of one thousand construction details organized by climate and house part
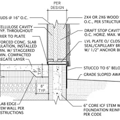
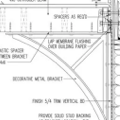
Replies
John, I've been trying to come up with an alternative to spray foaming stone foundations for a long time; in the past, for clients, and now for my own home with a damp basement and beautifully done, 190 year old stonework that I'd rather not permanently cover.
It's not easy to beat the effectiveness of sprayed foam in this situation. The best work-around I've come up with is to skip the dimple mat (what's it actually doing for you?), frame a stud wall (studs can be pressure treated 2x lumber on the flat) and run continuous EPS or polyiso behind the framing, with all seams taped. It would take some creative logistics but it could work, if you build the wall in sections or panels.
The most vulnerable spot is at the top--you don't want to sandwich your mud sill and/or rim joist (which is probably a single, big chunk of wood, if yours is like most old homes) on the cold and wet side of the assembly. A small horizontal shelf of rigid foam could be sealed to the bottom of the mud sill and the top of the vertical foam. The whole thing could be made removable for occasional inspection of the foundation wall interior.
You would only save money going this route if you do the work yourself and don't count your labor, and you would probably need to get used insulation, which is better for the environment anyway. Speaking of the environment, the reason to use EPS or polyiso and not XPS is that the blowing agents in XPS are potent, persistent global warming agents.
If you want to leave the foam exposed it will need to be Dow Thermax. Otherwise you will need to cover the framing and insulation with either a thermal or ignition barrier, depending on how you plan to use the basement.
Thanks for the input. So what would you prefer the facing on the used/ reclaimed 3 to 4" EPS/XPS/ Polyiso? Foil? Are we wanting a very low perm rating to keep the system drying outward?
Understood about not entombing 8 X 8 wood sill so to dry inward.
Lastly, how would you deal with the floor drainage and also how to terminate the foam as I need to either dig an inside drain tile and flash the system to allow all water coming off/ thru wall will need to go into IT or possibly the second idea ( shown in attachment on original post) that has a 3/4" tunnel/ dimple mat as a drainage plane to an airtight sump.
Understtod about dimple mat wall mat being a redundant item though it can be taped and detailed to become the primary air/ water tight layer with insulation doing just the thermal part?
The wall surface undulates maybe in 3/4 " waves maximum so the air gap between the foam sheet and stone wall would go from 1/16 to almost 3/4 or more, is that amount of air gap a problem if the joint taping, detailing and foaming keep it for the most part airtight?
All of your input appreciated.
Fieldstone foundations don't wick moisture nearly as much as poured concrete or CMU.
Foundations NEVER dry outward into the soil. They can dry outward on the above grade sections though. Foundations are tolerant of high moisture content. Mortar only deteriorates when moisture is moving through it, taking dissolved minerals with it. Sealing it from the interior reduces that moisture flow.
An air space or dimple mat and a perimeter drain can manage bulk water leaks through the foundation. Dimple mat isn't designed to be easy to detail as an air barrier.
A 1- 1.5" deep exterior-grade steel stud/furring studwall with foam board mounted to the interior side (seams taped) can be detailed as an air barrier with a bulk-water drain space behind it. You'll have to figure out the details of air-sealing the top of the wall to the foundation sill, etc.
Any recommendations for a preferred facing for foam as well as type of foam board?? Used xps, foil faced iso and eps is avail locally . Looking to put the correct foam/ facing type first time in so as not to regret bypassing the SPF method.
As for the drainage system to accept the water off the wall, the least amount of work for me ( solo) would be a product like "superseal tunnel mat- 3/4" thick laid directly on the existing concrete floor, taped and sealed airtight feeding into an airtight sump pump. Would love to not have to perform the labor intensive job excavating a trench for stone,drain tile and a concrete covering, again as a solo workman. Has anyone installed or have field experience in this setup?
My final question is how would you detail where this steel furring strip/ insulation described above meets the concrete and drain mat? Could one roll the tunnel drain up the outside face of the steel studs( towards the heated space a certain amount, maybe 8-12" and remove a 3/4" x 8" portion from the bottom inside of the foam product and then attach foam to studs and seal all joints, bottom and top ( sealing top as described above as a foam board to seal the sill to foam drain plane over the stone wall top). Sealing bottom with already purchased denarco foam gasket (SureSeal is a saturated open-cell polyurethane foam), elastomeric sealent or spf foam bead on the bottom but looking for field proven advice if possible.
Thanks to all for your advice and help.
Revisiting a design to drain, air seal, insulate the first floor and basement of a two story house in Rochester Ny, climate zone 5. Since the last posting I installed an interior drain tile instead of my proposed drainage plane on the basement floor. Attached is a drawing of proposed design. I also have a few questions if possible:
1.) The final design will have an a future exterior foam installed with thickness TBD ( 1.5"-2"?) but at this time there is no exterior foam insulation other than 3/8" foil faced foam under vinyl siding.
2.) Can fiberglass or cellulose insulation be used in the first floor service wall cavity. In the basement interior wall also?? If the insulation is able to be used in the service cavity of the first floor, what thickness should the exterior foam insulation be?
3.) The purpose of the 3/4" OSB adjacent to drywall interior drywall is for wall mounting heavy artwork. Will it adversely affect the drying properties of the wall.
If anyone could review and comment on the design I would appreciate it.
John,
There are several oddities about your wall assembly. For example, the wall has sheathing in three places -- exterior board sheathing, and OSB between the two rows of 2x4s, and then interior OSB as well.
The wall also has three layers of rigid foam -- EPS on the exterior, and then EPS as a cut-and-cobble layer, and then EPS in the middle of the wall. Phew! That's confusing.
Any chance you could simplify things?
Martin,
Thank you for the reply. All layers that I propose I think will provide benefits but would like your professional opinion on the proposed stack up especially in regards correct vapor transmission qualities once you know my reasoning. If I need to alter the design in order for it to perform better I am more than willing to do so. Answer to your questions are as follows.:
My house was built in 1901 and the air coming through the walls was quite a high volume even after newly installed windows that were flashed/ air sealed correctly. The 1" EPS cut and cobble insulation layer was to stop this outside air from entering the stud cavity at the outermost point. A 1" furring strip was added to the stud face to keep from compressing the R-15 batt from the additional 1" pf cut and cobble EPS withinin the stud cavity.
The taped layer of 7/16" OSB on the inside of the exterior wall framing is to act as continuous primary air barrier as well stiffening the creaky house walls of the old loosely nailed T and G 1" x 6" exterior sheathing. The 1" EPS layer on top of the 7/16" OSB air barrier/ wall framing stiffener is to act as a thermal break until I get the external foam installed in the future. I used eps in all rigid foam on the interior because of its vapor permiability. The interior most layer of 3/4" OSB on the service cavity is inside of gypsum is only for structural backing inside the wall to hold heavy wall art. The interior 2 X 4 service cavity wall is to allow for all services as well as deep splayed window jambs as well as giving me a flat plane in front of a very wavy and out of plumb existing exterior walls.
I am really trying to make sure that my proposed stack up does not alter/ degrade the vapor transmission qualities of the "vapor smart" layer of 7/16" OSB that acts as an air barrier/ wall framing stiffener. I understand that due to the existing 3/8" foil faced insulation below the vinyl on the exterior makes this wall an inward drying wall. I would like to keep the 3/4" OSB layer in the wall for the utility purposes stated but want to make sure it does not harm the stack up.
The XPS blue board rigid foam acting as a drain plane against the basement stone foundation is 2.5" thick. Is it advisable or of value to insulate with fiberglass the 2 x 4 wall in front this XPS in the basement prior to covering it with gypsum?
I plan on living in the house for the next 20 years and had the time, inclination to perform a deep energy retrofit while I am still physically able. Hopefully I have addressed your questions and I appreciate any and all feedback from anyone interested in any aspect of the design.
Thanks,
John
John,
It's hard to tell from your description how much of this plan has already been implemented, and how much is simply a plan drawn on paper.
In general, the most robust wall system will have a very thick layer of exterior rigid foam, with an optional layer of fluffy insulation between the studs. I don't know if you can follow such a conventional approach with your building. For more information, see "How to Design a Wall."
Martin,
The first floor wall is complete except for the installation of the 1.)service wall insulation, be it fiberglass or cellulose, 2.) the 3/4" OSB below the gypsum and 3.) the gypsum.
The exterior layer of thick rigid foam you speak of is NOT yet installed but hopefully will be in the forseeable future.
The basement foundation section is complete except for the addition of fluffy stuff ( fiberglass or cellulose) in the stud cavity and drywall to fire protect the XPS. The 2 1/2" rigid floor insulation is a future addition and has NOT yet been installed.
Do you see a problem in the first floor wall stack up in regards to drying inward correctly if I add the either fiberglass or cellulose insulation to the service cavity followed by the 3/4" OSB layer for wall hangings and gyp? I do not want compromise the wall drying inwardly with the 3/4" OSB layer. If it is felt that it might hinder the assembly drying correctly I could install wood blocking though it is much more work.
Do you see a problem in foundation wall stack up. I used 2 1/2 " blue XPS instead of sprayed closed cell foam due to the cost. It is foam sealed at all edges with foam taped seams. Can I safely install R- 15 fiberglass in the cavity against the XPS prior to gypsum insulation?
I have previously read the " how to build a wall" and just rescanned it tonight and think I have it correct but am looking to have someone check to see, if in their opinion, the wall is going to perform correctly especially in terms of vapor transmission and wall health, and function as I described in my intro and clarification posts as to why I added the elements that I have within the wall. Hopefully this info helps but If you need anymore clarifications I am at your service. I appreciate all of your input.
Thanks,
John
Bump