Are polyisocyanurate materials considered vapor barriers and to be avoided for insulating basements?

Hi,
I live in Central Minnesota. Our home was newly built roughly 3 years ago. It was not insulated on the exterior, but foil-faced DOW Thermax Sheathing was installed on the entire basement interior. This has a permeability rating of 0.03. This is basically an impermeable material. If we want to avoid moisture problems when finishing our basement, do we need to take this down and put up something with more permeability like EPS? We do try keep the humidity below 50 or 55 degrees in the basement.
GBA Detail Library
A collection of one thousand construction details organized by climate and house part
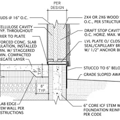
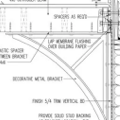
Replies
No, the Thermax is the right choice, for a couple reasons. (They're explained in depth here: https://www.greenbuildingadvisor.com/blogs/dept/musings/how-insulate-basement-wall)
Impermeability in this location is what you want. Concrete will always be damp, no amount of inward drying will ever change that, and you don't need or want the moisture in your basement. There is a basic assumption, though: hopefully your basement does not have a bulk-water entry problem. That is, if your walls leak, ANY wall insulation strategy is in trouble.
It's best if the Thermax is installed directly against the concrete with joints taped or foamed for airtightness. It should not be in direct contact with the floor; even a quarter inch gap is enough to prevent wicking moisture from the slab below.
A couple code issues: your climate zone requires R-15 of total insulation for a basement wall, so 2" thickness or less of Thermax is not quite sufficient. But for what it's worth, Thermax is one of the few products that many jurisdictions may allow to be left uncovered in a basement, since the facing meets code requirements for fire safety. Lesser brands of foil-faced polyis-type insulation do not have this benefit. But always check with your code official if in doubt. Sounds like your plan is to finish the basement, so you've got the perfect opportunity to add a bit more R-value if necessary, seal up any air leakage, and cover the foam. Hopefully the rim joist area above is properly insulated and sealed, too.
IIRC three years ago exterior foundation insulation was already required by MN code- I wonder why they didn't? MN code varies from the IRC prescriptives for foundation insulation (by quite a bit), and even puts limits on how much of the R-value can be on the interior side.
But with the above-grade exposed concrete you have a reasonable drying path for the concrete or CMU, it doesn't need to dry inward to the basement to keep the foundation sills dry, since it dries readily to the exterior. The major source of moisture is groundwater and direct wetting of the exposed foundation by rain/snow, not moisture from the interior.
Can we assume it was built with at least a foam sill gasket between the top of the foundation and the foundation sill?