Are code-breaking BPI builders causing trouble for unvented roofs?

I have a flat unvented roof on my 100-yr old rowhouse in Philadelphia, climate zone 4. There is about 18″ between the top of the ceiling and the bottom of the roofdeck. I’m looking at my options for air sealing and insulating this roof–there is currently no insulation at all. I’m getting different answers from different folks: some say filling the cavity with dense-packed cellulose (DPC) is a good option, others say this will cause condensation problems and that I need to remove the ceiling and put several inches of air-impermeable closed-cell foam against the bottom of the roof deck before filling with DPC or other insulation.
I’ve decided to ignore opinions and follow IRC code, which says in sec. R806.4:
5. Either Items 5.1, 5.2 or 5.3 shall be met, depending on the air permeability of the insulation directly under the structural roof sheathing.
5.1. Air-impermeable insulation only. Insulation shall be applied in direct contact with the underside of the structural roof sheathing.
5.2. Air-permeable insulation only. In addition to the air-permeable installed directly below the structural sheathing, rigid board or sheet insulation shall be installed directly above the structural roof sheathing as specified in Table R806.4 for condensation control.
5.3. Air-impermeable and air-permeable insulation. The air-impermeable insulation shall be applied in direct contact with the underside of the structural roof sheathing as specified in Table R806.4 for condensation control. The air-permeable insulation shall be installed directly under the air-impermeable insulation.
I don’t need a new roof, so I don’t want to put insulation over the existing roof. Instead I’m going to put air-impermeable insulation in direct contact with the bottom of the roof deck.
The IRC definition of Air Impermeable is
An insulation having an air permanence equal to or less than 0.02 L/s-m2 at 75 Pa pressure differential tested according to ASTM E 2178 or E 283.
And according to Building Science Corp, the air permanence of DPC is between 0.2 and 1.0 L/s·m2 at 75 P. So, at best, DPC is an order of magnitude worse than code.
The question is, given that flat-roof rowhouses are the dominant form in Philly, and that DPC DOESN’T count as air-impermeable, would it be as disturbing as it seems to me that many local BPI-certified contractors and other members of the Philly green building community tout the DPC solution for roofs like mine?
GBA Detail Library
A collection of one thousand construction details organized by climate and house part
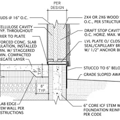
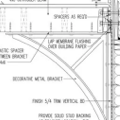
Replies
Andrew,
You're right that the least risky option -- and the one that clearly meets code -- is for you to install closed-cell spray polyurethane foam directly on the underside of your roof sheathing, followed by any desired thickness of air-permeable insulation. That method is one of the methods I recommended in my recent blog, Creating a Conditioned Attic.
Although not code-approved, many insulation contractors have had good success with the installation of dense-packed cellulose in unvented roof assemblies. The method is controversial; however, if done carefully, it seems to work. Here's more information on that option: How to Install Cellulose Insulation.
Andrew,
Here in the SW where most houses have “flat” roofs, the correct way is to install open cell under the decking AND rigid foam over the decking. If you are going to install closed cell under the roof sheathing, you better pray that your roof never leaks; you will have a very hard time finding where the leak is from bellow and I would not chance it with an old roof and probably poor water management detailing.
Another option you may have at this point is to install blown-in insulation, cellulose or fiberglass, but you need to install roof venting; this application is the most common here in the SW.
Armando and Andrew,
Never try to vent a flat roof! Take it from me -- I used to be a roofer.
Martin, you will not pass inspection if you don't have roof venting. It can be on the roof or it can be in the parapets, but either way, it has to be there.
Armando,
The vast majority of flat (low-slope) roofs in this country are unvented. Almost all commercial buildings have unvented low-slope roofs.
The best way to insulate a low-slope roof is to install rigid foam on top of the roof sheathing. That's the way commercial roofers do it.
If you try to install vents in a flat roof, they'll leak. Plenty of researchers have studied attempts to ventilate flat roofs -- such ventilation attempts are ineffective (there is no air movement) or counterproductive (they leak).
Thanks for the comments on vented/unvented. Additional thoughts on the unvented DPC solution in climate zone 4? Given the need to take down the ceiling for a proper air-impermeable solution (e.g., CC foam), a DPC solution will be around 4x cheaper. Is it just risky, or is it gambling?
Andrew,
I doubt if your cellulose contractors will be able to dense-pack your ceiling; after all, dense-packing an 18-inch cavity is tricky. You also need to calculate whether your ceiling will resist bulging, and whether your ceiling joists can handle the weight.
If you are truly interested in the feasibility of dense-packing an 18-inch-deep cavity, you should probably ask Bill Hulstrunk, the technical manager at National Fiber, for advice. He can be reached by e-mail: bill [at] nationalfiber [dot] com.
I think you are under a mis-impression. Philly rowhouse roofs slope down from front to rear and it is only in the rear portion that the cavity is too small for crawling around and using barriers for air sealing. That rear section is dense-packed, but it is open to the front section.
There isn't much concern about condensation because the vast majority of these houses are quite air leaky and have very low indoor RH during the winter. The low RH and fairly mild winter conditions mean that you don't have to worry about interior moisture migration into the roof cavity. If you moved this same house to Montreal and cut the air leakage rate in half, then you should worry.
The bigger concerns with dense-packing the rear portion are things like roof leaks (which cause damage no matter) and knob and tube wiring (for which the circuits can be tested pre and post retrofit).
The weatherization programs in Philly have been using this approach for many years with a good track record. I wrote a guidebook on this approach back in 1993.
The cost for a foam-based approach is prohibitive- at least for weatherization-type programs that need to show a reasonable payback for the program measures.
Michael,
Thanks for the local perspective! I have a peculiar circumstance in that the ceiling is high in the front and low in the back, so despite the slant there are no points with a large cavity. There are a couple of holes in the ceiling that I can peek into to confirm this.
I'm doing this work together with substantial air sealing in the rest of the house, so air leakage should be cut more than in half.
Since I'm not in climate zone 2 or 3, code writers deemed winter conditions to be cold enough here to require air-impermeable insulation. Are you disagreeing with code in saying that climate zone 4 can get away with less air impermeability and still avoid condensation problems even in a optimally air-sealed house?
Thanks!
-A
Andrew-
You have an unusual rowhouse -- at least from my experiences having lived and worked in Philly rowhouses for 15 years. It would be challenging to dense pack such a large cavity and I would be concerned about the structural integrity of the ceiling.
But in terms of moisture build up and code, I think that code, by necessity, is based on a variety of assumptions and CYA requirements, If I were you I would look at your specific house. It isn't the climate zone as much as the combination of how cold the roof deck will get vs. how moist the air will be in your home. If you seal your home very well and don't provide much ventilation and end up with high RH in the winter, then I'd be a little more concerned. Of course, you could just install an exhaust only ventilation system and you'd pretty much remove the potential for moisture migration into the roof.
In addition, those old roofs are really built -- thick rough-sawn board sheathing with several layers of built-up roofing can add up to fair amount of R value above the inside surface of the deck. There's also a tremendous capacity for seasonal moisture storage in that deck -- it's much more forgiving than plywood. In my research, I tried to create moisture problems in Philly rowhouse roof decks and we couldn't get the moisture content much past 9%.(although the homes didn't have very high RH).
I'm still not sure what you should do with your 18 inch roof cavity -- dense pack doesn't seem viable to me.
Michael-
That's good reasoning, my house definitely has an old thick roof deck, plus maybe some extra roof decks on top of that.
What is your concern about DPC? I have all new wiring, so knob and tube isn't a problem. And I imagine roof leaks would be a problem no matter what. Is the concern that 18" is too much or too little space?
My concern is that 18 inches is too much cavity to fill with dense pack properly and that the resulting resulting weight may also be an issue for your ceiling.
Michael:
I like your Philly flat-roof cellulose approach, and it looks like you have good data to back it up. So I'll suspend my concern about the approach of local green builders.
As far as my house goes, I've had some contractors take a look and they haven't raised any concerns about using dense-packed cellulose. Still, I guess I'll just go with a spray foam solution, it sounds like there's a lot of different kinds of risks with the cellulose.
-Andrew
Andrew- Much credit to you for actually looking up the code! Let me first say i am a spray foam insulation business owner. You are very correct in your finding that DPC is not an air barrier so it is not allowed by code in your non-vented roofline situation.
There is a long history of failure due to DPC in these and similar situations. As a matter of fact i heard about these failures at a NESEA seminar in Boston a couple months ago given by one of the contributors right here in this thread! Even after the failures being noted and breezing over the code like it didn't exist the message was use cellulose but be careful. I could not believe my ears to be honest.
The code is written that was for a reason and you are the intelligent one for heeding the warning and avoiding an impending failure! Congrats and good luck.
I would ask what shape your roofing is in. If you will need a roof in the next 10 years[highly probably with BUR or torch down] you can do it in EPDM and insulate from the top as much as you like. Iso board is much cheaper than spray foam at around 50 cents a board foot. 4 inches 2 bucks a square foot
You will still need to do some air sealing no doubt.
Stuart-
You obviously misheard what was said in that NESEA session -- the message was definitely not "use cellulose but be careful". The message was that densepacking compact flat roof cavities in cold climates can cause a lot of trouble. The failures that Terry and I both talked about occurred in specific circumstances -- particularly in very cold climates and very wet sites. In addition, a distinction was made between fully dense-packing the entire assembly vs dense packing just a section. If you don't have a cold climate or a wet site, then there is a very long track record of successfully employing dense pack. Many thousands of roofs have been treated that way.in Philadelphia over the past 20 years and I have never heard of an instance of moisture migration from the interior creating any roofing problems. .
It's usually a good idea to try to follow code -- but due to a variety of factors (e.g., inertia, lack of data, desire to maintain simplicity), codes often end up with requirements that are unnecessary or are only really needed under specific sets of circumstances. Codes shouldn't be considered holy scriptures but guidelines that need to be continually challenged and re-assessed based on sound research and building science.
Michael,
What does Very Cold mean to you as relates to this recommendation?
Jesse-
Very cold means Minneapolis or Montreal -- where problems have been found in about 10% of the dense-packed roofs. Philadelphia is not very cold. Boston ...I'm not so sure.. a tight house or a wet site, I'd worry. When in doubt, don't take a risk. The Philadelphia approach is based on lots of research in that very housing stock and climate.
Michael,
Thanks again for your sage words. Any thoughts on alternatives I could look at aside from removing the ceiling and spray-foaming? I definitely don't want to take out the roof right now.
-Andrew
I have a sample size of one in climate zone 5b. I have a low slope (2%) unvented roof insulated with R-30 fiberglass batts in sloped trusses of depths 16" to 22". The roof is black epdm and it is believed that there is no insulation on top of the roof deck.
I removed about 250 sf of the ceiling. I found the the majority of the plywood deck without signs of moisture or mold. In the truss bays adjacent to the walls, which did not have truss end insulation blocks, I found some limited moisture damage (photo 1). This moisture damage did not carry into the drywall or stud bays below so I don't believe it represents a bulk water leak.
What I did find, in very minor quantities, was mold spotting on the top side of the insulation. The non-perimeter portions of the roof assembly were without mold primarily but a number of batts near the northern wall had small spots of mold that to my amateur eye represented condensation moisture drops falling off the plywood roof deck. These droplets probably contained microscopic amounts of dust, dirt, and wood that created little micro-colonies of mold. Because the fiberglass itself did not appear to be supporting mold, the mold colonies were modest. This was no horror show of black mold. I'm pretty sensitive to mold and this stuff didn't even set me off. (Photo 2) I do wonder what it would be like if the insulation was 30 year old cellulose.
While I'd welcome advice as I'm determining my next step, I'm mostly sharing to say: a) here is another scenario with an older unvented low slope roof with some mold problems that does not involve a white epdm roof in arizona b) the problems were surprisingly minimal though I'm guessing my black roof that is not shaded and relatively warm winters (for zone 5b) are probably key.
Michael Blasnik, you said "Codes shouldn't be considered holy scriptures but guidelines that need to be continually challenged and re-assessed based on sound research and building science.". That's all very well, but most building inspectors require a person to follow code, no ifs or arguments. What then?
Tony.
Hi! So. I've been following a variety of discussions here, on FHB, JLC, for, well over a year, probably closer to two. I'm finally going to do it: just step up and ask a question about this.
We are building a new home with a big, simple shed roof, slope of 1.5":12" There will be 3 skylights, which cut across the slope/plane of the roof, so they will block/interrupt some 15-20% of the rafter bays, I'd guess. We have been designing this thing for about 2 years now. Architects are hopeless for the roofing system, and even the SE isn't as strong on this as I think they should be.
We are just outside of Philadelphia, in A-4. Roof framing will be 2x10s. We plan to install a torch-down MB roof. Having spent more time than I care to admit reading and re-reading Martin's posts and discussions of them, reading Lstiburek, talking to our structural engineer, I decided that the best way to handle this roof is to go with an unvented, "hot" assembly and use 3" of ISO above the deck (code requires R-15 here), and either FG or dense cellulose (depending on the pricing we can find on the latter) in the cavities. No interior vapor barrier.
A substantial portion of the second floor is cathedral ceiling because there is little sense in framing in an attic floor due to the very low slope. At some upper portions of the shed slope, we plan to put in a smallish attic area with access (should end up between 4-5' high) where we will likely locate some HVAC. At the present time, the design calls for recessed fixtures on the second floor, rated for insulation ,etc., but I know Martin vigorously opposes this, and I am looking for a flush fixture I can live with the aesthetics of that is somewhat within our budget. It would help if I knew what the cost of the recessed fixtures would be with all component parts, but that seems to be some sort of closely held industry secret.
I have avoided asking questions, but I'm at the point where I still don't find one single case study combining low slope residential with torch down and no venting in this climate zone in a new construction, and we are at the final decision-making stage and there is no more time for me to research or waffle around here.
I guess my question is: is what we're planning good enough? There are 3' overhangs at the upper and lower ends of the shed, and 18" overhangs on the rake sides. Even with the below deck insulation continued out to the eaves, are we looking at real ice dam risk here with the transition from the hot roof to the eave through the long overhang (especially on the bottom)?
We are going to build this using a CM as Agent. The CM happens to have a very strong engineering background, and is encouraging us to consider venting the roof assembly. I think most of his reasoning relates to the cost of the ISO. I am reluctant to re-open this can of worms, and my gut says that the additional framing (would have to use 2x12s to achieve sufficient R-value with cavity insulation) and other labor that might be required to vent the roof won't save money anyway. But maybe I should be open to this, since it is true that a vented roof assembly is tried and true and a cold roof will last longer. After all, it is NOT a technically a "flat" roof. It is just a low slope one. There are no valleys or complicated structures, but there is the barrier of the skylights to consider. If we did attempt to vent it, what would be the right way to do it? The CM has suggested something like furring up over the deck for over-roof ventilation . . . I'm not sure this makes sense. But maybe it does. Could we avoid the problems of venting through the cavities between the FG and the underside of the deck (where the installers will almost certainly not leave enough room for sufficient air flow and there are obstacles in the form of skylights and possibly recessed fixtures) and just vent it ABOVE the deck? In my research, I never found a single reference to this method. The only thing I've seen that is close is Lstiburek's vented-unvented hybrid assembly which adds the vented air space above the exterior rigid insulation (so still uses the ISO in any event) in high snow load areas to avoid dams. I suppose that is something we could try to do, but is also sounds expensive. My thought was that the torch down could go right on top of the insulation with a cover board (maybe perlite) without the need for a second OSB or plywood type of decking, but I'm pretty sure in order to construct a vented air space over the insulation, another "deck" would need to be laid . . or maybe a perlite board could serve the purpose.
I'm sorry for too much detail here. I guess really I just wanted to "vent" (ha ha!) a little bit and see if anything that I write leads to fruitful discussion or any observation that we are making a big mistake here or failing to consider something important. I might also like to hear whether the recessed lights are still a colossal mistake even in a hot roof assembly such as the one we are presently planning.
And, no, I'm not really open to spray foam. We're not using it anywhere in the house. Sorry, I just don't have confidence in it.
Any thoughts could be greatly appreciated.
Michelle,
You should post this question on our Q&A page as a new question, not as a comment on the end of a 3-year-old thread. Here is the link to the page where you should post your question: GBA's Question & Answer page.
Thanks, Martin. I didn't want to start a new thread when it seems like variants of this question have come up so many times over the years. I will refine my question (as I now have a sketch from the builder of what he proposes to do) and most it.