Any recommendations on new house plans?

My family is in the process of our first new home build and I’ve been lurking on GBA for the last few months gathering as much information as I can. We recently got the first round of plans for our home and I was hoping that some of the experts here might be willing to take a look at them and provide suggestions for improvements. We’re not going for anything like a Passivhaus but are definitely interested in green improvements that would improve the quality of living and/or offer a short to medium term payback.
Thanks in advance!
GBA Detail Library
A collection of one thousand construction details organized by climate and house part
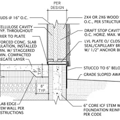
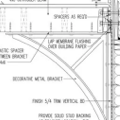
Replies
Probably should have mentioned that the build is in climate region Dfa
Ryan, can you give us more of a hint where you are located? If in the US, select a climate zone from this map: https://www.greenbuildingadvisor.com/blogs/dept/building-science/all-about-climate-zones.
What direction is north on your plans?
Can you be more precise with your energy and other goals? When designing homes for clients I use simple return on investment numbers for energy items, because if you aren't investing that money into your home, you would be either investing it elsewhere or spending it on something without lasting value. To me, a 10% ROI is a no-brainer, a 5% ROI is likely a smart investment, and even as low as 2-3% can make sense when you consider the associated benefits, such as environmental stewardship and living in a comfortable, durable home that promotes health for its occupants.
At first glance, your floor plans look like they will be nice to live in. It's big house by green standards but you probably know that. Regarding construction details, your wall insulation is skimpy, the heel height on your trusses is not very high, and your foundation interior detail is going to result in mold. There is a lot of glazing on the front and rear.
Michael, thank you for your response! Here are the details you requested...
The house will be located near Minneapolis, MN. 6B region on the provided climate map.
The top of each floor plan is due East and the large amount of glazing on the rear elevation (the East side) is to take advantage of a lake view.
With regards to our building goals, we came up with the following items when trying to define our vision:
Relaxing views
Easy entertaining (friends & family)
Open / Bright (natural light) / Airy
Right-sized house
Long term house
Priced reasonably for area (resale)
Timeless / Not-trendy
Welcoming / Comfortable
Natural Materials
Privacy
I think some simple high-level ranked priorities for us would be:
1. Build quality
2. Living space comfort (items from our "vision" list + general climate control)
3. Energy conservation / cost savings
The budget issue is very up in the air at the moment as we haven't yet received the project bid but I'm willing to guess we won't have a ton of head-room once the bid does come in. That said, we certainly want to make sure any potential problems are addressed up front and if there are items that would have a short to medium term payback (probably the 5%-10% yearly ROI you mentioned) we'll do our best to stretch our budget to accommodate them. If there are other items with a longer term payback (the 2-3% yearly ROI area) or that would have a profound impact on quality of life, we'd certainly entertain them but they may be harder to work into the budget. We'd also be keen on any green improvements that could be planned for without a great deal of up-front expense and might allow us to upgrade in the future.
In response to your initial comments, we are aware that the house is large by green standards. We did our best not to let the square footage get away from us but there were certain items (my theater space *cough* *cough*) that naturally increase the footprint.
We are working under a city code imposed height limitation which I'm guessing may account for the truss heel height you mentioned. Is there any particular concerns we should be aware of on this item or improvements we could make without increasing the structure height?
As for the wall insulation, do you have any suggestions for beefing it up? What might get us the most bang for our buck?
I'd also be extremely interested to hear any suggestions you have regarding the foundation interior detail and preventing mold! That is something I want to make sure we address up front.
Finally, any insights regarding the two provided "Envelope Air Sealing" options would be very much appreciated. Is one preferred over the other? Are either sufficient?
Thank you again for being so generous with your time and assistance!
Ryan,
I agree with Michael concerning the lack of room for insulation at the eaves, and the need for raised heel trusses. This would be a deal-breaker for me in your climate. It's essential that you find a way to get R-49 at the eaves. The architect specified R-12 at the eaves, and that just won't do -- especially in a region of the country subject to ice dams.
.
Ryan,
Concerning the wall insulation: Again, Michael is right. Most areas of the U.S. have adopted the minimum R-value requirements of the 2012 IECC, which require walls in Climate Zone 6 to have a minimum R-value of R-20 insulation between the studs plus R-5 continuous exterior insulation, or R-13 insulation between the studs plus R-10 continuous exterior insulation.
I'm not sure why your architect isn't willing to meet this code requirement -- possibly because Minnesota has an idiosyncratic code with a lower bar. Just because it's legal, though, doesn't mean it's a good idea.
.
Ryan,
If I were you, I would get more information on the stucco and stone cladding details. An air space between the stucco and the WRB is essential, and I don't see a mention of that. For more information, see To Install Stucco Right, Include an Air Gap.
The description of the sill pan in the window rough opening is unacceptable. Folding over the building paper isn't enough. You need a water-tight sill pan in every window rough opening. Here is a link to a video on sill pan installation.
.
Gentlemen,
I can't thank you enough for these recommendations, I regard them as absolute gold! I intend to investigate each and every critique myself and then take these concerns to the builder.
With regards to the insulation at the eaves, is there a resource I could use to determine the R-value of different configurations? I see you referenced the current eave design at R-12 Martin but I'm not sure how you arrived at that value (not questioning it, would just like to understand). Am I correct in thinking that the truss heel detail diagram (attached) already portrays a raised heel truss? If so, is the issue that the heel is not currently large enough? Because we are height restricted on the building I assume any truss heel increase would take away from ceiling height on the 2nd floor. If that is the case, I would like to minimize the heel height but certainly not at the expense of proper insulation. Are there high R-value insulation materials I should consider for the eaves that may allow us to minimize the necessary heel raise?
As for the wall insulation, if I'm understanding your post correctly Martin, it would appear that the specified R-21 in-wall insulation would be sufficient to meet 2012 IECC code given the addition of a continuous R-5 exterior insulation. Is that correct? If so, would that be a reasonable approach or simply a bare minimum?
The cladding section of the design document appears to be at least partially boilerplate as we do not have any stucco surfaces on our design but we do have a few areas of stone cladding. I read the article you linked about stucco installation (which was very informative) but I couldn't tell if the same recommendations would apply to stone cladding. Any thoughts?
The recommendation about the need for sill pans (and the associated video which was incredibly helpful for a novice like myself) is great! I will absolutely be talking with the builder about adding this requirement to the plans.
Ryan,
Thank you for the additional information. Hopefully you know that subjecting yourself to an online design critique can be a blow to the ego. Conscientious design is not something that is easy to apply after the design is already completed, but you at least still have a chance to get the details right, even if the building itself is not designed to be very green.
I understand the desire for lots of windows on the east. Much of the year you will get blasted with morning sun, giving a welcome dose of heat on some days, and on many other days you will want to block the unwelcome heat gains.
You have very little glazing on the south. Perhaps those views are not desirable, or windows don't work in the floor plan. In any case, you are giving up on free energy there.
Relatively large windows on the west. Again, you'll get a blast of heat in the late afternoon. You can deal with the heat with an air conditioner, but there is a large energy penalty.
The windows are specified as Anderson 100's. Those are about the worst windows available. My old Andersen window salesman wouldn't sell them to me. Andersen has decent windows, but their 100 series is their bottom-of-the-barrel option. The U-factor specified is 0.32. That is the same as R-3, pretty bad, considering it's not hard to get double-glazed windows that are U-0.28 or below, and triple glazed windows are available at U-0.20 or lower. It's not just an energy thing; the large expanses of glass will be extremely uncomfortable to sit near on even moderately cold days. Triple glazing greatly raises the temperature of the interior surface so you get much less radiant heat loss--in other words, less heat is pulled from your skin. Your architect lists an STHC of 0.35. I'm sure they mean SHGC; STHC isn't a thing. 0.35 could be lower for your east and west windows, to control overheating to some degree, and it could be higher on the south windows if you want to gain a few free solar BTU's. It doesn't matter much on the north, where U-factor rules.
As for style, the overall shape looks fairly classic for your location, with prarie-style heritage. The vertical siding accents, particularly the fake stone at the corners, do not meet your desire for a timeless look, however. They are very trendy right now, but that is not how buildings have been traditionally built, so there is a good chance that the detail will not stand the test of time. If you want some stone or fake stone, I would suggest placing it where it would have made sense traditionally--perhaps at the basement level, or to wrap a chimney.
There are numerous articles and Q+A's on GBA about how to properly insulate a foundation. You have a significant thermal bridge where the slab meets the frost wall, and a vapor barrier on the warm side of a framed wall in front of a concrete wall. Even with R-10 exterior insulation, there will be significant moisture accumulation behind the vapor barrier--basically a guaranteed mold factory.
Most builders find it much easier to use the exterior sheathing as the airtight layer, rather than the drywall, so your option #2 is a better approach. They do not show a good detail at the mud sill, which is a common location for air leaks, the rim joist detail is not clear, and they do not show a specific detail for transitioning the air barrier from the exterior sheathing to the second floor ceiling, another common source of air leaks.
You have 10' ceilings on the first floor. You don't have a maximum height issue at the raised heel; you (or your designer) have decided that extra-high ceilings are more important than energy efficiency and ice dam prevention. If you are limited on height, I would bring your ceiling down to 9' (still very high) and put another foot of insulation in the attic.
Again, I don't mean to be negative, but my business is designing houses that are efficient and durable, so I don't have a lot of patience for designers and architects who don't learn details to meet those goals.
Some thoughts:
Energy related:
I see a lot of plumbing fixtures on exterior walls, which leaves less room for insulation and poses a higher risk for pipes to freeze. With the continuous exterior insulation you might be OK, but if it were me I wouldn't leave it up to chance in MN.
One potential way of saving on electrical costs -- think about having a dual pronged strategy for lighting (ambient / safety lighting for night vs. primary lighting).
We have a series of evenly spaced amber LED night lights (0.8W each) throughout our house to eliminate the need to have the primary lighting on during most evenings / nights. To get even lighting, that means careful placement of additional outlets in areas like halls, stairways, and bathrooms -- we had to add multiple outlets to make it work.
With the basement theater room -- think in advance about where you're likely to want to run wiring for thinks like speakers and plan ahead for dedicated channels for wiring that don't require making holes in the building envelope (particularly if you think you may consider built-in speakers).
Design / comfort related:
If you're going to have a dedicated exercise room in the basement, why not sacrifice a few square feet and include a small walk-in shower and second door to the bathroom down there to make it easy to clean up after working out?
Timothy,
Thanks for the response! A great point on the plumbing in exterior walls, I'll look into the possibility to move them inward.
With regards to lighting, I'm actually exploring automated centralized low-voltage lighting solutions but I'm not yet sure if we'll be able to fit them into the budget. If not, I'll definitely take your recommendation into consideration.
The theater space will have to wait a bit to be finished but I will be spending a great amount of effort planning! I'm a long-time member of avsforum.com and am very excited for the eventual theater build.
The suggestion for a small walk-in shower in the lower level is a great one but we are somewhat limited in our ability to add plumbing to the lower level due to the site geography and the need for a lift pump. We will, however, likely have an outdoor shower on the lower level that could be utilized during the brief temperate months in Minnesota. :)
Michael,
Thank you for another informative response and please don't worry about my ego, it can take a backseat to my desire for a better home! Like any endeavor undertaken on a budget, compromises will have to be made. My main goal is to be aware of the compromises we end up making and ensure we've made them knowingly.
As you posited, the relative lack of windows on the South side of the home is due to a less desirable view on that side of the lot. The non-ideal orientation of the lot is actually a compromise I have been aware of from my reading on GBA but one that we are comfortable making due to the dearth of properties available in the area.
While I was aware that the Anderson 100s were the bottom range of their offerings, I had not noticed the poor U-factor ratings. From what I can tell, the 100 series are available with a range of glass and coating offerings. It would appear that a 100 series picture window, for instance, can range anywhere from .34 down to .23 depending on the options chosen. In any case, it sounds as though it would be a good idea to make sure a lower U-factor is specified in the plans. I know the builder offers other window options as well, do you know of quality issues with the 100 series that we should take into account?
With regards to styling, we prefer a mix of prairie and contemporary. While it isn't represented properly in the drawings, I'm working on sourcing composite/cement siding with a natural wood finish in a ship lap profile which I believe will punch up the contemporary aspect. From our perspective, the timelessness is achieved via good execution of the chosen styling but I will gladly concede that is up to personal interpretation.
Thank very much for the specifics regarding the foundation, I will begin researching and see what I can find. Mold is something that we absolutely want to avoid and a point we're not willing to compromise on.
Very helpful to know that option #2 is a better bet and I will also begin researching the potential air leaks you mentioned. If you have an example of properly documented mud sill, rim joist, and/or external sheathing detail I would love to check it out. I've also entertained the idea of adding a blower test target to the eventual build contract.
A clarification on the main floor ceiling height, it is only 10' over the great room, the rest of it being 9'. That said, I did not intend to imply we are unwilling to sacrifice ceiling height to properly insulate the roof. Quite the opposite, in fact. What I would like, however, is to make sure the eave insulation is done as efficiently as possible to minimize the amount to which we need to adjust ceiling heights. Any suggestions for materials to explore would be greatly appreciated. If an extra foot of R-49 fiberglass is the best/only option then so be it.
I definitely do not take your comments to be negative and I am very appreciative of your willingness to share your expertise!
Douglas,
Thanks for the reply! The Zip wall system and Andersen A-series windows are great recommendations and I will check out both. Due to the recommendations here on GBA it seems like I should probably place window upgrades in the high-priority bucket.
With regards to the roof, we explored both a flat roof as well as a low-pitch standing seam metal roof (each of which would have been great for contemporary styling) but ended up compromising due to cost. The non-ventilated foam-filled roof is another great suggestion and I'll definitely explore that as an option.
I have no doubt that some of the upgrades being discussed here (maybe most) will prove unattainable within our budget but I'm the type of person that sleeps better at night knowing exactly where the compromises have been made (perhaps a bit masochistic). At least I'll know we made an informed decision. I certainly hope not to receive derision from our builder, who has been pretty good to work with thus far, when presenting these ideas but I have certainly come to expect sticker shock throughout the entire new home build process.
With regards to priorities, I absolutely understand where you're coming from and realize that one person's priority is another's frivolity. For me, a home theater is truly one of my sources of joy but I have no delusions about ever recouping the money that will go into it. Everyone has to have a hobby though, right?
I've read and listened to a lot of building science professionals, and a constant refrain is the difficulty they have in in getting buy-in from builders and contractors. If they can get bids at all they are often far higher than the reasonable cost of the proposed energy upgrades. Be prepared for a fight and sticker shock.
The Zip wall system is a way of achieving an air tight barrier at the sheathing level (preferred over air tight drywall) in a manner that is familiar to builders and part of a well developed system. Just make sure that the Zip sheathing is sealed to the frame as it is installed. Zip-R sheathing has foam applied to the interior side that can provide some continuous insulation, again in a manner familiar to builders. Be warned however, the foam layer changes the structural properties of the wall, while the preferred method of foam outside the sheathing does not.
During the recent cold wave I've taken to looking at windows, (zones 5 and 6). I have yet to see one that doesn't have some condensation. Upgrading to triple pane will prevent this but even more importantly will improve comfort. I think this is essential in a house with this much glass. If you are enamored of Anderson windows their A-Series offers triple pane options with 100 Series style composite exterior frames.
Of all construction processes installing air shuts and insulating roof heels is my least favorite, lying on my belly with my head poked by protruding roofing nails as I strain to reach into that space is my idea of what hell must be like, and the lowest pitch I've dealt with is 8" in 12". I can't imagine which of Dante's circles a 4" in 12" would put me in. The hip roof doubles the pain. I want to meet the guy who has to spray foam those heels. One option consistent with prairie/modern design and your building height restrictions is a flat roof on deep floor trusses. Another is a 2" in 12" pitch using raised heel trusses and a double locked standing seam metal roof. Incidentally, the design calls for about 500 sq. in. of high roof venting. I don't know if that is achievable using ridge vents on your hip roof design. An unvented roof, insulated with closed cell spray foam would solve this and even help the heel situation should you choose to retain the current roof design, but it would take a lot of foam to make it suitable to your climate.
Ryan, I fully expect you to go to your builders with information gleaned from this thread and be met with derision. You will be shocked when you price out some of the options we have presented. You will be talked out of most of them and surely any significant improvements will completely blow your current budget. You shouldn't have come here. You are now cursed. This is the most expensive journey you have ever embarked on. Every time you write a check to your energy provider or feel the cold Minnesota winter night pouring through your twin pane windows you will remember GBA. Buyers remorse on a car is terrible. Buyers remorse on a home is devastating.
I love prairie design. Your house is beautiful. Clearly it is all of your and your family's dreams made manifest, but at what cost? Your are concerned with payback times for energy improvements, but what is the payback time of a home theater? Perhaps you should take some time to reassess your priorities. A home should bring joy to its occupants and part of that joy should come from the satisfaction in having met your responsibility to the planet and the future.
Douglas Higden
I like your plan's style, I know I just started posting here randomly recently so if it helps my credentials I am a general contractor who builds new and remodels residential and commercial not far from you and I do a fair amount of insurance claims, structural changes and diagnosing and reconstructing failures on the border of zone 6 and 7. Im a BPI Building Analyst and own a home performance insulation company, Ive been practicing these concepts since 2003 and lurking on here since this site started.
My own house is hipped out like yours and has some areas that have an "energy heel" which in the truss world starts out with the top chord above the bottom chord at around 7" like your spec and goes up in height from there based on spec and Ive built lots of houses with the standard 7" energy heel. I also have some gables with a 16" heel at my place. I dont spray foam like your details show, I just foam seal the drywall framing joints in the attic, and use exterior sheathing as my air barrier and I never get ice dams. (My air sealing goes way beyond that but Im talking that attic exterior detail) I've been involved in lots of "common" construction that has no air sealing with the 7" energy heel and they dont ice dam except in some obvious spots.
Andersen 100 series is hands down the best value window out there, I have had the opportunity to use vinyl, fiberglass, roll form wood clad and extruded wood clad from all kinds of manufacturers, Andersen, Pella, Alliance, Simonton, Kolbe, Semco, Lincoln, Weather-shield, JeldWen, Marvin and more. You wont be disappointed in the value you get with the 100 series, thats my go to. Very few issues and a great price point. Marvin is my Cadillac, 100 series is my Toyota and 100 series is what I put in my house.
Lastly with the basement poly and mold farm comments, dont put poly over the underground portions, your inspector shouldnt allow it anyways, but it will not suddenly morph into a "mold farm." Id ask Maines how many basements with poly he has torn apart and of those how many were full of mold under normal conditions, ie no basement fish ponds. Ive pulled apart quite a few almost hoping to find mold to justify the hysteria just once and I havent found one yet. I have found lots of mold, just never behind basement poly.
As for your plan, how bout that master closet? Yikes, could be a spare bedroom. Your drop zone is going to be hard to drop stuff on with the door in the way. The kitchen layout is clunky. Put your furniture in the house ahead of time and then look at flow or how you would move around the house. It will make problem areas that might need an extra 6" or maybe can give up a foot or two. It helps tremendously. If you can give that upstairs bath even 2 more inches of width it will help get rid of that cramped feeling.
Man you have alot of beams in your floor systems. Engineer that part carefully and have your builder preplan HVAC runs with the sub and check with plumber as well, preferably together. Ive been invlolved with construction in minnesota and you guys love floor trusses with flex ducts and pot vents. Ill usually submit for quotes from 2 different truss/floor system vendors and pick the best design, on houses like yours there isnt always an obvious way and you'd be surprised how much you can improve by getting someone to think outside the box. All those beams is when performance goes south because all of a sudden you got goofy elbows and scrunched up flex to manuever around all the structural components you have in your way and then flow gets restricted, the system isnt balanced or comissioned cause that costs too much and you get comfort issues, happens alot.
So, thats a lot of post for dont worry about ice dams, 100 series is great, basement poly mold is overblown but dont do it, and plan/design as a complete system. Good luck with your new place, exciting and stressful. Make the best of it.
I like your prairie stile home it looks a lot like mine.
When I built my house I found I difficult but necessary to control your costs at the design stage. It is all too easy to design a dream home that you can’t afford please be careful.
If you are even considering resale value most of the stuff in this site will only frustrate you as it add costs and that will not increase the appraiser’s market value number when go for your construction loan, so you will need a large down payment to cover the things you value that the market does not.
Consider asking for a variance for an extra 12 inches of height. Some jurisdictions are more flexible than others.
If you want to understand ROI for your options, there is a government paid for computer program free to users called BEopt that will model your home and compare costs vs. benefits of every conservable option. It will take about 40 hours to watch the instructional videos and model your home.
I insisted that we redesign until we could find a way to keep all plumbing out of exterior walls.
Consider adding extra support under the washing machine and avoid front loaders.
Putting the HVAC equipment in the corner of the basement will make it difficult heat and cool the house.
Walta
Here's a thought on your roof height v. heel height vs. ceiling height issue. This is coming from someone who is not a professional building scientist or builder. I won't be surprised if some of those types that frequent this forum point out problems with this suggestion.
You could put in a sloped ceiling along the outside edges of the house. Your ceiling height would be the same as your current plans in most places, but 12"-18" shorter along the exterior wall. The space above the sloped portion is filled with insulation such that the R-value is at least as much as the middle of the attic. The amount of sloped ceiling required could be reduced if you put some rigid foam with higher R/inch under the drywall of the sloped portion, as shown in the recent article here: https://www.greenbuildingadvisor.com/blogs/dept/building-science/kingspan-kooltherm-phenolic-foam-rigid-insulation
HVAC: Having the furnace in a corner of the basement leads to long duct runs for some rooms. As someone else pointed out, make sure your HVAC sub-contractor reviews the floor truss design to ensure that these duct runs are not impossible. Consider alternatives to central forced air. There are a lot of articles on GBA about ductless and ducted mini-splits. Consider water-based distribution with floor coils, radiant ceiling units, fan-coils, or some combination. Plan for ventilation.
Plumbing: The location of your hot water heater will probably give you OK wait times in the master bathroom. However, the wait time would be excessive in the other second floor bathroom. That is both an annoyance and it waste energy. A recirculation system addresses the wait time issue. With attention to controls, a recirculation system doesn’t substantially increase the energy waste. If you end up with fixtures along exterior walls, route the plumbing up from the floor as opposed to in the walls.
Rear Entryway: Having a bench is great. I would move the drop zone to the wall to the right of the pantry. Then, you could move the entry door over a little and make it 3’ wide. I would eliminate the door between the entryway and the kitchen. The corner separates the spaces enough. Eliminating the door means you don’t have to treat it as a separate room for heating.
Main floor bathroom: Figure out how to include a 3’ door. If you ever have a guest in a wheelchair, it is good to have at least one bathroom on the first floor that they can get into.
Kitchen: I wouldn’t like having the fridge in the hallway. I would move it over next to the pantry. We have our sink in our island and we like that.
Master suite: That is an enormous closet! When I was designing our house, I found that once my wife saw a plan, she would never let me reduce the size of the master closet. Have you had discussions with a significant other about a “garden tub” in the master bathroom? I talk to some people that say they used in a few times when the first moved in and then hardly use it. I got talked into including one and I am glad I gave in on that point. I have had knee pain issues lately and soaking in a hot tub gives me more relief than anything else. Personally, I would give up some of that closet space for a tub.
Laundry: You will like having a big counter in the laundry room. It makes folding the clothes way easier. If you can find a place for a hanger rod, that is even better. Am I reading the plans correctly that there is a super narrow, relatively deep cabinet there? It seems like that is an exterior corner you could get rid of without adversely impacting the styling. Extend that wall over to add the space to bedroom #3 and the den. That would add square footage but likely reduce the cost.
T Carlson,
Your reply is incredibly informative and it is great to get the opinion of a professional with first hand experience in the area! It's also nice to hear that ice dams aren't necessarily a foregone conclusion with the truss system, as specified. Seems like it would still be worthwhile to explore alternatives or improvements to the eave insulation but it is helpful to know it doesn't necessarily have to be all or nothing.
Thank you also for relaying your experience with the Andersen 100 series windows! I'll likely explore the Andersen A series as well as the Marvin 'Cadilacs' you mentioned but it is a relief to know that if we end up with the Andersen 100 series (hopefully with a better U factor than specified currently) that we won't necessarily be disappointed by them.
Great to have another viewpoint on the basement poly as well. I will certainly be bringing up the question with our builder. Sounds like the consensus is that basement poly (at least on the walls with an exterior underground) is a bad idea or, at best, unnecessary.
You're right about the master closet being huge but in addition to the standard clothing storage and changing space we're also viewing it as a storage area. We will also give some serious consideration to your suggestion of expanding the 2nd floor shared bathroom. It would result in a little more "wasted" hallway space but if it isn't a large expansion it could be a good compromise. Great point about the drop zone in the mud room, perhaps it would be worthwhile to push the mudroom door to the South and move the drop zone to the Northeast corner of the room. That would also provide a bit more room for the bench.
Thank you for the tips about the HVAC / plumbing engineering with the complex beam configuration, I will request that the builder preplan for the HVAC and plumbing runs with both subcontractors present. This is a fantastic "no cost" tip that seems like it could have a big payoff.
Walter,
Thank you for sharing your experience. It has definitely been a challenge trying to strike a balance between dream home and budget. As I mentioned previously, as difficult as the choices can be I definitely find it helpful to understand where we are making compromises.
With regards to a variance, we have actually already received a 12" height variance for the current design. The reason the height is relatively limited is due to a quirk in the city code regarding riparian lots... long story and more than a little frustrating.
Thank you for the tip about BEopt, I will absolutely check it out. Great tips about the plumbing and washing machine support as well.
With regards to the HVAC equipment being in the corner of the basement, is the difficulty a product of needing more ducting to reach the rest of the house?
Ryan, I'm impressed with the feedback you've received! I offer mine with less credibility, but it is mostly personal experience:
I am building an updated Prairie Style as we speak. I decided the hip roof did not allow enough venting with a ridge vent alone, and I would have had to place vent holes in several places, so I opted to foam the bottom of the roof sheathing. I insisted on the full depth of foam to meet the code-required value.
I have 16" truss heels at the perimeter, and accepted a 9' ceiling in most bedrooms (with 8' headers) . I got a 10' ceiling in living room and dining room by adding a 2' soffit at the perimeter, effectively a 9' ceiling for the first 2'. Works well and contributes to the design by offering a location for wall wash and art lighting.
I have 4' eaves. One of the best surprises for me is how protective it is for all walls—even where the eaves are 20' off the ground the windows almost never see water! Means I don't have to rely on perfect flashing by tradesmen whom I am not directly supervising.
I am using EIFS for the exterior wall: 2" of foam with dense-packed cellulose in a 2x6 wall gives me about R-26 with a great look that is cost effective (in my area, finished product is about equal to material-cost-only of Hardi-plank).
I worked on a house in Excelsior that had three bathrooms in the basement that all had to be pumped. You can manage a shower downstairs. If you are thinking resale value, make sure those rooms all have egress, and provide bathrooms (with showers) so at least two can be used for guest rooms. Good design is like writing: it requires much much more effort in the editing than in the first draft. Now is the time to sweat the details.
Similarly, 20' is a long hike between fridge and sink. Take vegetables to sink, wash, return remaining to fridge... maybe you don't need an exercise room after all! Minimally make island a work surface with an additional sink. Myself, I like to prep where there is natural light, i.e. near the sink, so I would make that window larger or install two, and move the fridge to that wall also. The generous pantry will allow for more wall space without uppers, especially if you have all drawers below.
10" is much too narrow for your stair treads—will make it feel like a tract house and will be difficult carrying things like suitcases. If you want the house to feel gracious, make the risers 7" or less, and the treads 12" (become 13" with a 1" nosing), and at least 4' wide. You will appreciate these every day, and you have the real estate for them.
I purchased Intus windows and doors. I chose the vinyl with the foil option in dark bronze inside and out. Custom sizes to the 1/8" cost no more, and the steel reinforcement allows huge windows where others would need an over-under mulled pair. Package priced out about equal to what I would have spent on Anderson or Marvin, once I added the cost of either painting or staining the interior sashes, muntins, and frames. They are very heavy so a bit of a pain to install, but they make the house feel like it is in the new century. I am amazed how in MN house prices are not knocked even for old single-glazed windows (nor is insulation often mentioned in sales literature); however, I know from experience that buyers will be enthusiastic about buying a house where you can sit near the walls and windows in winter.
RE: COST. If you are financing the house, compare the annual expense of mortgage combined with improvements such as those suggested here. Likely, you will have more money in your pocket at the end of each year if you invest in a great envelope. If I was building new in MN, I would definitely sacrifice some form for significantly better function (meaning human comfort). The expensive finishes like tile and fixtures can all be added later, and almost certainly will be done again if you live there long enough. The stuff that matters most is the stuff that cannot be done later. Do it now. It is an investment. Think of it like building a house on a very solid foundation, instead of one that is cheaper but cracks (speaking of which, I've never seen a CMU basement that was not problematic).
Wouldn't we all rather be the third little pig?
Reid,
Thanks for all of your thoughtful suggestions. I read the linked article and the Kooltherm insulation looks like an interesting product, I'll definitely look into it further.
With regards to hot water wait times and a recirculater, great suggestion and I'll check it out.
Another comment had also mentioned the obstructed mud room drop zone and I came to the same conclusion you reached, that it may make sense to move the drop zone and shift the entry door towards the wall. Elimination of the door between the mud room and the kitchen hallway is another interesting suggestion that we'll definitely consider. I tend to agree with your assessment that the corner already separates the area pretty well.
Great tip regarding the wheelchair accessibility of the main floor bathroom, I'll give it some thought and see if it is something we can accommodate.
I tend to agree that the current fridge placement is non-ideal and but have been trying to convince my wife that it would make more sense to push it further East along the same wall (swapping the fridge and that small portion of countertop). I feel like that would help improve the "kitchen triangle". The sink in the island is a no go for my wife, she hates dishes accumulating on the island... just a personal preference.
I think we would be in the group that wouldn't get much use from a tub, in fact, we replaced the master bath in our current home with a larger shower and I love it. Again, just a personal usage/preference thing I think.
You are reading the plans correctly with regards to the narrow area in the laundry room. It was originally represented as dead space in the wall in the first drawings. I wasn't a fan of the wasted space and while I also thought about adding it to the bedroom closet originally, I though it might be a great place for a pull-out cabinet to house things like laundry detergent or perhaps a clever fold-out ironing board.
David,
Great information and suggestions. It's impressive that a 4' eave provides so much protection from precipitation, not sure if we could accommodate the additional overhang but worth a look for sure.
With regards to insulating the roof sheathing, does that essential act like a cathedral ceiling and make the attic part of the conditioned space?
I've never seen the EIFS before and it looks like a really interesting solution.
Good thoughts regarding resale and the ability to convert at least on of the basement rooms to bedrooms. We'll have to give some more thought to a basement shower and decide if the resale potential is important enough for us.
I mentioned in a previous response that I am also not enamored with the current fridge position. I have been advocating pushing it all the way to the East along the same wall it is on now but moving it over by the sink is something else to consider. I think the suggestion of expanding the window by the sink is another good one and we'll definitely look into that.
As for the stairs, our current house has an exceptionally steep staircase so I can appreciate what you're talking about. I feel like extending the tread significantly may have a large impact on the design (especially in the basement) but I will certainly investigate further to see what options are available. At the very least, you've motivated me to make sure I confirm our minimum tread depth comfort zone.
I'll take a look at the Intus windows you mentioned as well, I had not heard of them previously. It would be interesting fo see if the steel reinforcement you mentioned might allow replacing the main floor East facing picture + awning combinations with single larger picture windows.
I think you've explained our current line of thinking regarding cost quite well. We're doing our best to make sure we can incorporate the most important cost-savings and quality-of-life improvements up front as many of them cannot be performed easily after the fact. It is a balancing act and all of the advice we're receiving here is a tremendous help in assisting us in making informed decisions with regards to the many many compromises necessary.
Check out Nebraska-based Enerlux windows. I found that they have a very reasonably priced triple pane fiberglass window. My quote for triple pane was only 5% higher than the double pane Marvin Integrity, and the window is built far better. Downside? Small company,fairly new.
T Carlson and Ryan, I've done a couple hundred renovations as a carpenter/contractor, and have been the designer on roughly three hundred others. Most of the homes I work on have old, unfinished basements, but I can remember at least half a dozen with poly or paneling on the walls which was moldy. I was in a house in New Hampshire last Saturday that had a relatively dry foundation, but fiberglass in the ceiling with poly below--and mold on the top of the poly. T Carlson, how many of your projects have you gone back to after ten years to assess for mold? Mold usually takes about that long to show up. Sure, maybe you'll get lucky and your particular conditions won't result in mold. I'm in the business of providing clients with safe assemblies, and poly over stud framed, batt-insulated walls on the inside of foundation walls is a building science 101 no-no.
I've installed hundreds of Andersen 200's, and they were good windows for their day. My go-to for many years were Marvin Ultimates, and I now use Marvin Integrity regularly, when I can't talk clients into triple glazing. Ryan, try this tool: https://www.payette.com/building-science/glazing-and-winter-comfort-tool/. My current go-to for high quality yet affordable windows is this company: http://logicwd.com/, which makes windows in the US. They will cost more than Andersen 100's but they will save a lot of energy, and the difference in comfort (not to mention condensation) will be huge.
BeOpt is a good suggestion. I use it for most projects. There is a learning curve but if you work through it you can make relatively informed decisions, rather than relying on a bunch of strangers on the internet. Ryan, if you search GBA for the details I (and others) have mentioned, you will find a lot of information about how to do things properly.
Ryan
If your furnace is in the center half the air goes to the left and half goes to the right so that makes the largest duct 50% smaller than the system from the corner. (Often larger ducts equals lower basement ceiling height) The longer your runs the greater system losses will be, the designer often ends up making the ducts larger compensate for the losses. Also longer runs are likely to increase the back pressure the blower sees that means the blower must work harder and use more electricity so you get higher operating costs.
Walta
Walter,
Thank you for the clear explanation. I will do some additional research and try to figure out if anything can be done to improve the furnace location. At the very least, I will work with the builder to make sure the HVAC and plumbing routes are planned ahead of time to minimize issues.
Kevin,
Thanks for the Enerlux recommendation, I will definitely check them out as a possible alternative.
Michael,
Thanks again for another very informative reply. With regards to the poly on the inside of the foundation walls, I intend to make sure the developer removes that call-out from the plan. It certainly seems like that is the general consensus and the safest plan of action.
The Payette calculator you linked is a fantastic tool and is already helping me get a better feel for what kind of specs we'll need so thank you! I will also be checking out the Logic windows you linked as another possible Andersen alternative.
I haven't had the chance to get started on BeOpt yet but I'm hoping to do so soon. With a couple recommendations on GBA now it certainly seems like something worth pursuing.
Ryan, you're welcome. When you get to it, I'd suggest running BeOpt in Design mode, rather than Optimization mode, so you can see the raw results of changes to the building components. After setting up a baseline design, right click on the "design" tab and you can add up to 12 alternate designs, changing just one item for each design. If you have a very good sense of building costs you could run Optimization mode and it will tell you what mix of things is the most cost effective, but I am not convinced their built-in estimates are accurate.
Michael,
I havent been back to any clients house to fix mold issues I caused, so I havent caused any to my knowledge and Ive never put poly over basement stud frame walls, I think I made that pretty clear. Like you I make it my mission to build the best way possible.
Like you, I have also torn into lots of houses and commercial buildings remodeling, and performed energy retrofits on lots (I dont keep a count but probably over 1000) where we look for all defects and I have found mold but there was always an obvious moisture source, or defect. In dry basements I have never found mold, on newer PWF I havent found mold, so Ive come to the conclusion the scare tactics are unecessary. We can go back and forth all day, but in modern construction it isnt an instant mold farm as you alluded too, even 10 years down the road, but again doesnt mean its ok, why take the risk.
Id be more worried about exterior flashing details and proper cladding, proper transition from wall panel to lap, and trim bands and kick outs and sidewall flashings, ect. I still see reverse laps on housewrap if we are talking 101. Who tucks there raincoat in their pants?