Finding the Right EPS Foam Insulation

Hi,
I’m in zone 6.
I am currently renovating exterior walls adjacent to a non conditioned garage for soundproofing and improve insulation and I need a few pointers.
The plan was to remove exterior Gypsum, fiberglass batts and polyethylene from the exterior then have:
Soundproofing gypmsum
3 inches EPS (R13to 15)
r22 rockwool in the 2X6 cavity
Interior Gypsum
Vapor retardant paint to satisfy the canadian code
My issue right now is we were able to remove most of the polyethylene from the exterior, but there is a small amount left between 2×6 studs and interior gypsum that I cannot get to. I presume it’s a minor issue, but I would like your thoughts.
I’m also hesitant about the EPS foams. I was about to use silverboard SB 35, but realised it’s not optimal as it’s quite the vapour barrier. My current thought is to go for styrorail SRP400 EPS or GRP at 2,27 perm for 1 inch, but they have no data on air permeability.
Is there any type 3 EPS which is air permeable?
Thank you for your help!
GBA Detail Library
A collection of one thousand construction details organized by climate and house part
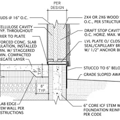
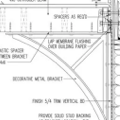
Replies
Your assembly should work great. You don't want air permeable foam, you only want it to be moisture permeable, unfaced EPS is perfect for this.
You can hang drywall with long screws through that much EPS, but not the easiest. Make sure to mark out the stud location on the floor and ceiling before putting the foam up.
The soundproof drywall won't do all that much extra, regular 5/8 type X will get you most of the STC value of that assembly. More important is to air seal the drywall on the inside, so caulk around all studs and cover device boxes with putty.
If you want even more sound insulation, since this is not exposed to weather, I would go with this instead of EPS:
https://sonopan.com/wp-content/uploads/2020/06/SONOpan_technical_details.pdf
I've used a single layer before and works pretty well, you can use multiple layers for more R value.
Thanks Akos,
I guess I wasn't clear. I actually wanted to make sure the EPS was air impermeable as it wasn't specified with an ASTM rating. If all unfaced is fine as an air barrier, I'm happy then.
I actually am using sonopan and resilient soundclips for the ceiling, but I had no idea Sonopan had R value. I'll look into it for the wall.
I have a follow up question. I've been looking at the soundproofing part from another angle:
Would something like this work. https://www.hushframe.com/why-it-works
I'm thinking of using an eps for with integrated 1x3 such as this https://styrorail.ca/wp-content/uploads/2017/03/STYRORAIL_SRI_Fiche_technique_201805.pdf
and use the 1x3 in the foam as the furing strips.
Would the gap of 0.5 to 1inch between the hushframe and the layer of foam cause a significant issue for the insulation performance of the assembly? I'm tight on space on one of the walls because of a door. I would be looking at something simpler otherwise
I think you are over-complicating this. For high R value and good sound isolation, the cheapest is a double stud wall with a gap between the batts (this is important for STC, you don't want the batts touching, you can put a smart vapor retarder over the 2x6 batts to keep them in place).
So in your case, I would caulk the interior drywall, cover outlets with putty, install 2x6 batts+vapor retarder, build a 2x4 wall 1/2" from this, insulate with batts and cover with as many layers of 5/8" drywall as you want.
This is a significantly higher STC value assembly than anything you are proposing that can be built with commodity supplies for any box store.
P.S. Most of the decoupling clips don't do a good job with low frequency sound such as a car starting. Double stud walls are much better for this.
I agree that the double stud wall would be the best soundproofing method. Unfortunately, it's just not an option with the configuration of the wall that I'm asking advice for.
I have a little over 4 1/2 inches from that wall to a door frame which has already been reduced to accommodate a smaller door with stairs leading to that door. A double stud wall won't fit.
What made me revisit the issue is that we found 1/2 osb behind the gypsum wall.
So to get as good soundproofing as before I started, I need an equivalence to drywall+osb or double drywall on top of a minimum of 2,5inche of EPS to get to R 11,25 to add my exterior foam.
From my readings, 1 layer of sonopan + drywall would be inferior to double drywall for soundproofing and I wouldn't get enough R value from layering sonopan.
If I want to improve the initial soundproofing, then it gets even more of a puzzle, which lead me to the complicated solution I proposed today.
If there is any easier way to get to r 11,25 + improve on my initial soundproofing within the 4 3/4 inches of thickness I have, I'm open to suggestions.
P.S. If it helps, it's mostly the sound from the garage door that wakes me up when I work night and evening shifts. Our car is electric.
As an aside, just knowing how much of a problem an air gap of between 0.5 and 1 inch between the fluffy insulation and the rigid insulation is would really help me in choosing what to do.
Sorry if I am being difficult.
Sound is not an easy topic, there is way too much information (and misinformation) out there. This makes one second guess every decision.
Before focusing on the walls and ceiling, you need to decouple the tracks. Most of the noise from the garage door is carried through the framing, no amount of wall soundproofing will stop it.
What I would do first is hang the tracks and the motor off something like these:
https://www.mcmaster.com/threaded-rod-vibration-dampers
Make sure to check the weight that each needs to hold up, for best isolation you want them close to the rating of the hanger.
Once that is done, you can see how much more soundproofing you need.
Going nuts on walls and ceiling might also not be worth it if you are not beefing up the door. Doors tend to the weak point in any assembly. This is mostly wh high STC assemblies are not worth it, it is just too costly to put in a matching door.
Given your space, I would install the rigid and cover with either two layers of 5/8 Type X or 5/8 TypeX+OSB. Make sure you install backer rod+caulk all edges. Backer rod is PIA, but is important and can't be skipped. Green Glue sealant (not compound) is your friend. Getting everything well sealed is more important than trying to aim for higher STC.
Check commercial drywall suppliers as they sell very long drywall screws. I've installed drywall directly over 2.5" foam without issues, you just have to mark out where the studs are ahead of time. This would also save you a bit of space.
Don't forget to move your outlets out to the surface of the new drywall. Usually best to replace these with air tight boxes while at it or even better, go with all surface mount with MC wires.
Thanks for the very detailed response. Where exactly does the backer rod go? I've never heard of this before. I tried a web search, but I mostly found information on its use to air seal windows.
It is the same stuff used around windows. Box store sells it small lengths, if you don't have a lot of wall.
The backer rod goes between the drywall and the floor or between the drywall on the ceiling and drywall on the wall.
Key to a good install is getting a consistent gap between them so that you can use one or two size backer rod. Once this is pushed into the gap, you caulk over it to seal it up. A quality joint should look like this:
https://i.ebayimg.com/00/s/NDUwWDUwMA==/z/0n0AAOSwr81UR9AP/$_1.JPG
You can then mud and tape over the joint. You want to prevent flanking around the perimeter of the wall, any gaps there can transmit a lot of sound. This is also why it is also important to caulk the inside drywall sheet from behind.
I agree with Akos about the double stud walls. Way back when I worked in a recording studio, where double stud walls were common, we used double doors too -- one in each "side" of the wall. The walls were around a foot thick. Real "I can't hear anything through this wall" sound proofing is not easy, and not cheap.
Akos already recommended what I would do with the double layer of 5/8" type X. That's the easiest and cheapest first step to cut down on sound, and it gets you a very solid wall too. You need to tape and mud both layers, but you don't need a pretty finish on the inner layer -- just good enough to seal the gaps.
For the garage door, can you detail exactly what type of door you have? Hanging the drive motor from vibration isolators will help (I've done this before for annoying things like air pumps on preaction fire systems and certain types of mechanical lines). Y
You can also sometimes help by limiting the number of attachment points between the operating mechanism and the structure. This would mean framing out some support structure for the tracks and the motor, then connecting that structure to the main garage structure at only a few points, and using vibration isolators at each point. This works on the same principle as a double stud wall, but on a mechanism instead of a wall. If you have the typical roll-type over head door, I'd frame out a 2x4 structure attached at the bottom and top of the door opening, and to the ceiling above the motor. This would be three attachment points on each side. You need a vibration isolator rated for the load for each point. Ideally you want the load to be around 50% between the rated high and low loads for the vibration isolator you select. The goal is to decouple the noise source from the main structure so that the sound doesn't get transmitted through the framing of the main structure. Any rigid coupling has the potential to conduct sound, so the goal is to minimize those rigid couplings and but something squishy (the vibration isolator) in each one.
I don't know if it will work in your application, but another trick commonly used with large motors on pumps in commercial buildings is to mount the motor to a large mass (usually a precast concrete base slab), and suspend that mass with vibration isolators. I doubt anyone makes such an assembly for a garage door motor, but you could accomplish something similar by taking 3-4 pieces of 5/8" drywall, stacking them, and mounting the motor to that. The mass helps to damp vibrations, but it only works if it is also mounted with vibration isolators.
A last option is to look into other types of garage door operators. There are worm drive, chain, and belt type units. Some are made specifically to be smooth and quiet. If you can find one with a soft-start feature too, that would probably be the quietest overall option for you. The less noise you're starting with, the easier it will be to block that noise from getting into your home enough to be a problem.
Bill
Thanks Bill, especially for the garage door opener suggestion. I can't believe I didn't think about it. I added that to the project as we have an old chain garage opener that is really loud.
We're going to go with either a belt drive or direct drive (if it fits).
Things got a bit delayed but all should be done by the end of the month. I'll try to give an update once everything is finished.
Regarding the EPS foam-related portion of your question, Martin Holladay offers this resource: Choosing Rigid Foam (He addresses vapor permeability.)
Thanks for the response. Just wanted to point out it's a broken link. The article shows up with the search function though.
Here is a quick update on the renovations:
I had the garage door opener changed to a wall mounted unit and I had resilient clips + furring channels + 2 layers of 5/8 drywall for the ceilings. The change in noise transmission is great. I can now barely hear the door closing and I believe the sound is coming mostly from the window. At any rate, this won't wake me up, so I'm pretty happy with that part.
The walls were a bit more complicated, but the final result is:
R22 rockwool
1 3/4 layer of sonopan
2,5 inch GPS with integrated furring channels - my contractor wasn't keen on the idea of super long screws, so we compromised. It has the bonus of decoupling the drywall from the 2x6
2 layers of 5/8 drywall and we were above my R12 goal of added insulation.
Rigid insulation was lowered to cover the rim joist.
I also had the electric boxes changed to air tight boxes, added firestop putty and found a few holes in the walls that we were able to seal.
We're still waiting for a new door to complete the project, it was delayed due to the pandemic.
Akos, you were right, all we hear now comes through the door. We're changing it as we need a smaller door due to the bulked up walls, not for soundproofing though.
All in all, much quieter house as we can barely hear when someone opens or closes the garage door and also much more comfortable.
I actually wrote last year about humidifiers as we were having moisture levels in the 25% n winter and I was having issues with the dry air. This year, although we haven't had very cold weather, moisture levels are holding up in the 35-38% range when thes average temp is around -2C.
I'm really grateful for your help as I couldn't have done it without GBA. My next step is to continue air sealing and reinsulating the rim joist and adding an air exchanger. I'm hoping to do this this winter and then we will see. I have a few ideas for which I will no doubt need advice again.
That Styrorail SRP400 product looks outstanding. Is that what you settled on, the GPS version of it?
I've never heard of Type 3 EPS. Is that a Canadian standard? My usual reference: http://docserver.nrca.net/technical/9997.pdf
People here tend not to differentiate between types of EPS, but I hate the cheap Type II stuff because its R-value is so low, as well as its compressive strength. Your GPS is a lot better.
Does your assembly still have air gaps? I would be nervous about air gaps adjacent to any foam insulation layers, given the horrific results in that London fire. It was either the EPS or the polyiso that burned (the building had both) – there have been conflicting sources, and I haven't dug into it. The air gap they had created a chimney effect for the fire. I don't know anything about how GPS affects flammability. It's strange that we still build buildings that can burn down, given that we've known how to build buildings that can't burn down for ages.
I was a bit worried about the increased flammability, but I wanted to make sure we got over r12 in combination with the sonopan given the thermal bridging of the furring strips. It's not perfect, but we have minimal air gaps, not more than 1/2 cm, where they are present at all.
I taped all the seams between the panels and I also taped the panels to the concrete slab of the garage. I went so far as to buy extra pieces of 1/2 inch and 3/4 inch GPS to minimize the gap in the transition from rim joist to concrete in the garage. I actually did this mostly for insulation though, not so much for fire safety. My line of thought is that with the rockwool in the bays, minimal gaps and 2 layers of type x drywall, if there ever is a fire, it should be ok.
It would be helpful if someone more knowledgeable could address your concerns, but I hope my answer helps.
We went for the GPS version of the srp 400 with a twist - the sr.i series has integrated furring channels. It helped to reduce the bulk of the assembly as my contractor wasn't keen on the super long screws as i wrote earlier. It was the best compromise I could find. If we had gone for long screws, I would have used the standard sr400 without the furring strips instead of the sr.i GPS. It's much less expensive.
I would think most people here go for the type II as it is cheaper and that is what is most readily available. I spoke to styrorail technical department a few times to order the sr.i we used and they seemed rather surprised that someone would want their 400 series and even more so that someone wanted GPS.
We actually had a bit of an issue getting it initially because of a misunderstanding between the vendor and my contractor, but everything was solved rather quickly. It must help that their factory is within a 50km radius of my house.