Another cut and cobble question

Hi, I see this has been covered before but, my situation is a little different. I am currently remodeling our downsized retirement home. It is an older manufactured home with 2×3 studs. The outside has 7/16 osb sheating and 1 inch t&g owens corning xps with the t&g caulked and vinyl siding. I am now remodeling the inside I have fitted the stud bays with 2 inch xps owens corning rigid foam. Cuts are precise with limited gaps. This is about the only way to get enough r value for our area (n. Indiana). Do you think this will be acceptable? Sould I go ahead and seal all gaps? Should I use a poly vapor barrier? You’re thoughts would be greatly apprciated! I’m about ready to hang drywall and I want to get it right! Thanks!
GBA Detail Library
A collection of one thousand construction details organized by climate and house part
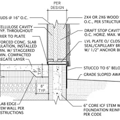
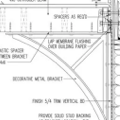
Replies
Hi Chevyss.
It is not ideal to have your sheathing sandwiched between two low-perm materials, but it is not necessarily a problem if the exterior is detailed well and the walls are not going to get wet from rain or snow melt. The XPS is a vapor retarder, but will allow some drying in either direction, depending on the weather. So, do not use an additional interior vapor retarder.
Seal the rigid foam into the wall cavities with a flexible caulk or air sealing tape. Canned spray foam has proven to be a poor choice for this application as it is too rigid to withstand seasonal framing movement.
Thanks a bunch Brian! That was the direction I felt would be the right choice but I really needed some expert advice confirming it. Barry
>" That was the direction I felt would be the right choice but I really needed some expert advice confirming it."
Was the cut'n'cobble the right choice? I don't think so.
Not to be a wet blanket, but a cut'n'cobble is the WRONG choice, on a number of different levels, even though you will likely get away with it (assuming window & door flashing was implemented properly.)
Why do I think that?
With the OSB detailed to be air tight, the performance of R13 fiberglass stuffed into the 2.5" deep 2x3 cavities would be a reliable R10 for life. Compressing an R15 batt into 2.5" would raise that to R11. See:
https://sites.google.com/site/miltonbuildingsupply/_/rsrc/1535666743062/insulation/insulation-compression-chart/INSULATION%20COMPRESSION%20CHART.jpg
At 2" XPS is only warranteed for R9, or 90% of labeled R-value. See:
https://www.royalbuildingproducts.com/sites/rbp/files/2018-03/dow-50-year-thermal-limited-warranty.pdf
...and:
http://insulation.owenscorning.com/assets/0/428/429/464/c8fb7b76-244f-4f88-b3fc-548908c8843c.pdf
Even if the R10 foam was truly R10 @ 2" , R10 fiberglass at 2.5" depth is also higher performance than R10 foam at 2". The half inch longer path through the thermally conductive wood lowers the heat loss through the framing by 20%.
A compressed batt solution offers a MUCH higher drying rate than the XPS, and with R5 (or R4.5 warranteed) sheathing on the exterior there is more than adequate dew point control at the OSB, no interior side vapor retarder (other than standard interior latex paint) is needed:
https://www.greenbuildingadvisor.com/article/calculating-the-minimum-thickness-of-rigid-foam-sheathing
And there is more.
The carbon footprint of the 2" XPS is an order of magnitude higher than a compressed R13 batt:
https://materialspalette.org/wp-content/uploads/2018/08/CSMP-Insulation_090919-01.png
"Contractor Roll" kraft faced R13 fiberglass are dirt cheap compared to 2" XPS, and take a lot less time to install, even for fussy perfectionist batt installers, and it's a BETTER solution by almost every measure.
If you can find some other, more appropriate use for the 2" foam, yarding it out and replacing it with R13 fiberglass would make it a much more resilient (and slightly higher performance) assembly. But if you want to just seal it up and live with it since it's already done, it's not a super high risk assembly.