Aluma flash

Another important question as I am getting closer to framing.
I live in zone 2, just north of Austin. I have been planning on 2×6 framing, 1/2 sheathing (plywood or advantech), covered with an adherent wrap (Delta Vent SA), 1″ rigid foam insulation. The cladding will be Austin stone in some areas, metal panels in others. I plan on using a rain screen where metal cladding is used
I have recently come across poly wall aluma flash product. I always thought that in my zone, although bulk drying is to the inside, it was good to have some ability to dry to the outside and thus products like aluma flash were not optimal. Now I have seen it done on several high end homes and I must say it looks superb. I understand that it is not cheap. I was hoping to have an answer to a few questions before I make my decision.
1. Is this a good product for Zone 2 climate or is a product with some permeability preferred?
2. What would be the preferred method of attaching rigid insulation through this? Would it be better to use taped Rmax instead of the aluma flash?
3. Does a rain screen system exist which automatically allows for attachment of metal cladding to it? This would minimize the number of penetrations through the air/water barrier.
Thank you
GBA Detail Library
A collection of one thousand construction details organized by climate and house part
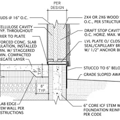
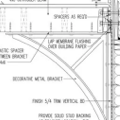
Replies
Deerefan,
The things that seems to distinguish Aluma-flash for other self-adhered membranes is its resistance to exposure - which I'm not sure matters on your build.
Much more important than whether you choose it over Henry Blueskin, Grace I&W, or other similar products, is whether it makes sense to cover your exterior with an impregnable membrane at all. I don't know enough about your climate to say.
Agree with Malcolm - Aluma Flash only needed for builds that have long weather exposure before cladding (can take up to a year for complicated custom builds - far longer than most homes require - most WRBs are only rated 90-120 days UV exposure)
I have to wonder why you wouldn't simply use Zip-R system? Advantage of Zip-R is the WRB and exterior insulation goes up when you sheath the house - applying self-adhered WRB and rigid insulation on top of OSB/Plywood is labor-intensive (expensive- essentially 2-3x the labor)
And I'd use a rainscreen on all exterior claddings, regardless of what they are.
Go watch YouTube to see how Matt Risinger is building his Austin home (from your AlumaFlash comment, you probably already are). He's attempting near-passive-house tightness but Zip-R doesn't provide enough R value for what he wants (he's using 4" rigid on top of regular Zip - personally, I don't think it makes sense for that climate considering all the other air-sealing/energy-efficiency measures he's taking - but it's probably good marketing for his business and provides content for his channel)
Well, I am the general contractor on this house and each step has taken a lot of time as it is hard to find quality trades. So it is possible that I may exceed the UV exposure limits of some wraps. I really like the Delta Vent SA product but it is only rated for 50 days. I would probably have to do a section of the house at a time to be sure I don't exceed this timeframe.
As far as ZIP sheathing, I am concerned that my framer has not used this product. I would prefer that his crew uses regular sheathing rather than try to learn on this project. I plan on applying the WRB and rigid foam myself with a helper to ensure the details get done correctly. Also, it seems that having the rigid foam on the inside of the sheathing takes away some of the reason for using this in our climate zone - decreasing condensation by keeping the frame warm.
So my question would remain, is it better to use impermeable WRB, such as aluma flash, in our zone 2 hot-humid climate, or is it better to leave the WRB with some permeability allowing for some drying to the outside when needed? Also when using such impermeable WRB is it critical to use something like DPC or blown in roxul between the studs to help with the drying or is 5.5" of open cell foam still Ok? Thank you.
I believe a vapor open is technically better, but Alumaflash is definitely used in the Austin area on high end homes. With respect to your aversion of zip system sheathing: Zip sheathing is just OSB with a fluid applied WRB. It is installed just like OSB, because it is. You can have your framers put it up without the tape and then you go in and inspect the nailing pattern, detail it with the tape, roll it, and flash the rough openings. That is what I would do. I see a lot of it here, but it seems like framers never roll it. I would never trust a new framing crew to do it right.
Zip seems difficult to get the nailing correct. Matt Reisinger's recent videos on his own home show over driven fastener everywhere(in the field & boundary nailing).
If his crew can't get it correct - then who can?
The other potential concern about zip is how is the shear strength of the wall affected when you have thicker foam in between the sheathing panel and stud frame assembly.
If vapor permeable is better, which peel and stick membrane would you recommend. Is there one in particular that is more resistant to UV light for a longer period of time.
If this was your forever home and money was not the main deciding factor, which WRB would you choose? Is there a particular window flashing detail that you feel works best?
You are confusing zip with zip R. There is ZIP System Wall Sheathing and ZIP System Insulated R-Sheathing. The first is just OSB with WRB applied. The latter is the one with the foam. There is technical data available on both. For the Insulated sheathing they give you wind loading and fastening engineering data.
Huber has all the info you could want on their website:
https://www.huberwood.com/zip-system
What did you ultimately decide to use on this project?
For the walls, I ultimately used Delta Vent SA as my WRB, 3" cascadia fiberglass spacer-hat track system to create an insulation cavity and 1" air gap, and 3" rockwool cavity rock insulation, snap lock standing seam metal cladding.
For the roof, I used WIP300ht, 4" cascadia fiberglass spacer system, 4" rockwool cavity rock, gap deck armor, standing seam metal cladding. All of the clips screws were sealed with polyurethane sealer.
This was definitely a very detailed and labor intensive part of the project. In my area, certainly not anything for a contractor crew. I think it does have advantages, however. The house scored <0.4 on a blower door test and is very comfortable on hot days even without any AC on (during construction). I really like the idea of drying able to happen in either direction.