Airtight Drywall Approach

I have been thinking about a strategy for improving the ADA. This may not be a new, but the idea is to install all exterior wall and ceiling drywall BEFORE any of the interior partitions are even framed. One could carry this further and tape, finish, and apply primer (VB primer in heating climates) as well. This strategy might best be used by custom builders.
Advantages
-drywall boarders should love this…think of the speed and ease of installing nothing but large sheets without any obstacles. Tapers and finishers should also love this.
-should result in an almost perfect air barrier…rim joists areas in two story homes would require some additional air sealing.
-might result in less wasted drywall cutoffs.
Disadvantages
-requires two trips for the electrical and plumbing rough ins and also requires some extra thought and planning…I think that they would get used to this after a couple of jobs.
-also requires two trips for the boarders, tapers and painters but the speed of the first visit might offset this additional cost?
-may result in some butt joints ending up in less than optimal places…good workmanship should compensate for this.
-also may require extra trips for inspections…
Your thoughts??
GBA Detail Library
A collection of one thousand construction details organized by climate and house part
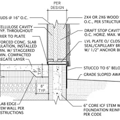
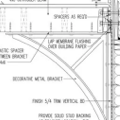
Replies
1. The modular manufacturers have another advantage in that they can seal the penetrations from both sides of the drywall. They can work from the outside of the house because the siding isn't on yet.
This may not be practical in the field, but it is food for thought.
2. Most general contractors don't enjoy swapping trades in and out like that. As you say, the inspectors will be a little annoyed and probably tack on some reinspection fees.
But I've been thinking ADA is impractical in the long-term. The reason is that homeowners are continually putting holes in the drywall. After 30 years you have a swiss cheese house with no airtightness. A "homeowners manual" would not change this bad behavior.
Garth,
I think the difficulties of electrical rough-in are a deal-killer. If you can't run your Romex from one box to another because one of the boxes hasn't been installed yet, how do you run your Romex?
The argument against an interior air barrier based on holes in the drywall is actually an argument FOR ADA. The most long-lasting and durable air barrier will be one that is permanently visible and easy to patch when punctured. If the air barrier is buried in the structure, there's no way to inspect it or repair it. A few picture-hanger nail holes is not going to dramatically change the air leakage in a house.
But I agree that no builder is going to use a system which requires doubling the scheduling problems with subs and inspections, though that may work fine for an owner-builder doing most of the work themselves.
In a small addition I built years ago, I hung the ceiling drywall before building the partitions. This is particularly useful with roof trusses to avoid the problem with uplift cracks creating openings into the attic. If you design for no lights in the top floor ceiling (I use wall sconces and switched receptacles for the bedroom floor), and bath exhaust fans in dropped soffits, then you don't have to worry about obstructing the electrician by rocking the ceiling before rough-in.
The trick to making ADA work is for most of the work to be done at the framing stage, with acoustic caulk or gaskets installed between each framing assembly. If you're concerned about the additional work of sealing every partition take-off, then use poly gaskets like we used to do when air/vapor sealing with bad ole polyethylene.
I have not found electricians unwilling to use Lessco polypans. The primary issue may be to get your rock hangers to apply caulk (they won't want to do it). So you can either stay ahead of them with it or staple up drywall gaskets and use gasketted electrical boxes - or have your own crew hang the drywall.
In a cold climate, where the air-sealing should be on the inside to prevent exfiltration and consequent condensation issues, I continue to believe that the ADA is a viable and often preferable system.
Robert, I grant you some of your arguments for ADA, but over 30 years you get PLENTY more holes than just for picture hanging nails. The cable and satellite guys are the worst, 1" holes, usually 6 per house. New electrical outlets and light fixtures here and there, etc., etc.
I'm sure the homeowner penetration debate has occurred before, could someone direct me to it?
Kevin,
If we're talking ADA, we're talking new, quality construction. A well-designed house has telecom outlets in every room, and sufficient electrical receptacles and lighting such that additional outlets are unlikely to be required.
Any technician making holes in a building who does not caulk, foam, flash or otherwise seal them should not be allowed to stay in business. And any homeowner who cares so little about their house that they leave gaping holes in their walls deserves the consequences (in experiential education, we call this "natural consequence").
The primary argument against ADA is that it takes some time and effort and attention to detail and oversight of subcontractors, which few builders are willing to invest. It's certainly easier to use ZipWall or taped exterior foam to create a continuous air barrier, but easier isn't necessarily better and those methods require expensive materials and (I will continue to insist) are on the wrong side for an effective cold-climate air barrier.
Robert R.
Robert does it follow then that ADA is on the "wrong side" in a Hot climate?
How about a Mixed climate?
The reason I say that an air barrier should be on the interior in a heating-dominated climate is because its primary function is to separate the high-energy, high vapor-pressure, high stack-effect pressure interior conditioned environment from the thermal and structural envelopes. The conditioned space, in other words, should stop at the drywall.
There is nothing in the ADA system which limits drying to the interior (other than the code mandated 1 perm retarder) or creates an interior condensation plane, so it is on the "right" side also in mixed climates and fine for hot climates. Defining the conditioned space at the drywall limits the volume to be conditioned.
In humid climes, whether mixed or hot, it is important to limit inward moisture drives by avoiding reservoir claddings without convective air gaps, dark colors that absorb solar radiant energy, and excessively vapor-permeable exterior layers (such as some of the polymeric WRBs). But there's nothing in ADA which exacerbates the dominant inward moisture drive in hot climates, as long as bulk moisture, vapor diffusion and radiant drive is controlled at the exterior. No modern house should be so air-permeable at the exterior plane to be problematic in normal climatic conditions.
Martin
To rough in the electrical would require leaving enough Romex out the wall to reach the next box (which of course is not in yet) The best way would be to stub out enough wire to do the job through a hole in the ladder blocking which lines up with where the interior partition will be. This hole through the blocking can be well sealed and gasketed or caulked before boarding. Same goes for plumbing stub outs. I also see and advantage to using drywall returns at the windows...saves money and is easy to seal to the window. Casing can still be used if the builder desires.
I agree that this is not going to appeal to most buiders, but for custom builders who might even have an electrician and plumber as part of the crew, this could work.
Th real beauty of it is that the only gaskets needed would be at the base plate and of course at electrical boxes and plumbing stub outs. One good swipe of caulk around the windows after the paint is done and voila...a very well sealed and totally inspectable and repairable air barrier.
I'm a custom builder who has plumbers as part of my crew and I would not use this system because we need to put a water test on all waste and vent piping and the effort to go through capping all the pipes, carrying and pumping all that water, draining the pipes, and then uncapping all the extensions, adding the missing pipes to the interior walls and re- capping, hauling, pumping, and draining. That's a deal breaker for little added benefit over just doing a careful job. We also have to do an air test on all water supply piping but that wouldn't be all that onerous.
Michael
Just out of curiosity, how often is there plumbing in an outside wall in the houses you build?
I often will put sinks under windows and we do run the drain and waste stacks behind the sinks in the outside walls. Here in NC we also put the supplies in the outside walls when we have toilets or sinks against outside walls and when we do double headed showers we will generally have the second, hand shower head in the outside wall though the valve will be in the interior wall. We also do outdoor showers here but have a new system that allows us to actually install a shower remote from the house, we're about to install a shower on a tree. (I should send a picture to Robert Riversong eh?)
So the answer to your question is every single house we build will have several places where we have plumbing in an outside wall.
I'll wait for the picture.
I've installed an outside shower with washing machine hoses attached to frost-proof hot & cold sillcocks, so that it is removable for winter. My most recent house design, a superinsulated lake cottage in Tinmouth VT, will have a summer outdoor shower under an entry deck that does not require seasonal disconnection.
I've also had hot & cold sillcocks on the driveway side of my house for quick de-icing of my windshield prior to winter emergency responses.
And, with my 12" thick double-wall system, I have no problem running PEX supply lines through the inner of the exterior walls.