Airsealing an attic

Hello, I have a 172 year old brick home and have some questions regarding attic venting. My attic is in poor shape. It was “finished” when the house was built, with plaster walls, a flat plaster ceiling and 1 partition wall. I’ve been in the house about a year and am just now deciding to do some work up there. There are sections of sagging plaster and a few holes in the ceiling. I decided to widen a hole in the ceiling to peek up into the very top of the roof. The timbers look like they’re in great shape but the masonry at the gable ends and chimney stacks are crumbling. In one spot there are bricks missing from the chimney and I can reach right in and touch the chimney liner connected to my woodstove 2 stories below. Also, many many wasp nests which explain their presence in the house. So technically with all the voids, the attic is kind of “vented”. I’m wondering if the roof timbers are dry and intact because of this. I’m afraid that if I repoint/repair the masonry, and possibly spray foam any random voids I find, I’ll be sealing the attic, eliminating fresh air movement and possibly trapping moisture there. By the way the roof is original cedar shakes directly on the rafters, with metal panels having been put on top probably some 100 years ago. I hope I explained everything correctly, if not please ask/tell me. Looking forward to some advice, thank you.
GBA Detail Library
A collection of one thousand construction details organized by climate and house part
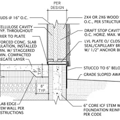
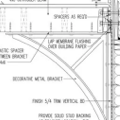
Replies
Dan,
Most attics are dry, as long as there are no air leakage paths from the interior space to the attic.
Air sealing the boundary between the conditioned space and your attic is always a good idea. This article will tell you what you need to know: Air Sealing an Attic.
Don't worry about venting. For more on this issue, see All About Attic Venting.
If you want to read still another article, here's a link to one more: All About Attics.
The condition of your chimney is quite dangerous and could easily lead to a house fire. It is important that you stop using your wood stove immediately and call up a chimney expert to have your chimney inspected and repaired.
Thank you for your response. I have additional questions regarding my attic I hope you can help with. As I said before there is a large hole in one of the lath and plaster walls (which is sloped with the roof angle). The hole was made by myself in order to inspect for moisture. When I opened the hole there was no moisture or mold on the original cedar shingles, but now there is mold starting to grow. Is this only because of warm air escaping my second floor into the attic and condensing on the underside of the cold roof? Can I patch the holes and seal the attic space from the roof and assume mold will no longer grow? There didn't seem to be mold there for 173 years and now there is, so it must be from myself opening the wall.
My next question is about insulating. I plan to repair the lath and plaster walls and ceiling just as it was when the house was built. Then frame out the walls and ceiling over the plaster with 2x3s, glueing/screwing rigid foam panels inbetween the studs. Then poly sheeting and drywall. I understand using only 1 1/2" or 2" foam wont be very effective but it will be better than it is now. Do I need poly as a vapor barrier behind the drywall or will the original plaster walls keep moisture away? Also, if the attic ceiling is insulated (only to R10 or so) should I remove the loose insulation under the attic floor or would that greatly decrease the insulation value of the rest of the house. The attic will only be a "heat-as-needed" space in the winter, possibly a craft room of somekind. Thanks - Dan
Putting high-R/inch foam between studs is a waste of good foam, since the thermal bridging of the R1.2/inch wood robs it severely of performance. Assuming a 20% framing fraction (= single top & bottom plates window headers, 24" o.c. stud spacing) the "whole wall R" of the layers that include 2x3s with 2" foam + 1/2" gypsum (and ignoring the any of the not fully defined exterior layers) come in at about:
2" EPS: R6.1 (Even though the foam is R8.4)
2" XPS: R6.6 (despite R10 foam)
2" polyisocyanurate: R7.2 ( despite R12 foam)
If you installed continuous 1.5" foam using 1x4 furring through-screwed *using fender washers to keep the furring from splitting) 16" o.c. to the pre-existing studs (or furring) you'd end up with a whole-wall- R for the new layers of:
1.5" EPS: R6.8
1.5" XPS: R8.0
1.5" polyisocyanurate: R9.5.
That's higher performance using less foam & fewer board-feet of lumber, easier to air seal properly (tape the seams of the foam), at a a total stackup 1/4" thinner than you'd have with 2x3 studs.
If you add split rockwool or fiberglass batts compressed to 3/4" between the furring it adds between R1-R1.5 to the whole-wall-R performance numbers, a double-digit percentage improvement over the 1.5" foam + furring solution, and more than 25% total improvement over the cut'n'cobbled 2" foam solution.
Patch any holes that you made, and patch any others that you find. Your suspicion that it's humid conditioned space air migrating to the roof deck is valid. A;lso, while air sealing the attic floor can be a laborious process it's worth it from both an energy use and resilience point of view. Use sheet metal and fire-rated duct mastic to deal with air-sealing flue chases. Most other air leaks such as electrical & plumbing penetrations can use can-foam/caulk, and even corrugated cardboard or cut up pieces of housewrap to cover bigger holes.
That sounds like a better idea. Are you suggesting I compress 3.5" fiberglass to 3/4" between the furring strips. I was under the impression fiberglass loses R value when compressed, is that why using say R-13 insulation would yield a R1 - R1.5 increase? Would it even be worth the cost?