Air and Vapor Control Layers in Cold Climate

Hello,
I am getting ready to build a home in western Montana (Climate Zone 6).
The house is a little unique as it has a main floor featuring an ICF foundation, with a conditioned crawlspace, hung floor joists, and traditional framing with ZIP sheathing and Rockwool insulation in the walls, mono trusses (shed roof) with blown in ceiling insulation.
That section of the house then transitions to a monolithic slab where the garage is. There is second story living space above the garage. The garage (sealed off from the upstairs) and second story are also traditional framed with ZIP sheathing and Rockwool insulation in the walls and scissor trusses with blown in ceiling insulation.
Then, on the other side of a demising wall in the garage/upstairs, there is a pole barn structure (attached) on a monolithic slab. This area has fiberglass bats in between the girts and blown in insulation in the scissor trusses.
On the main floor, I plan to seal the bottom plate with a sill seal and flexible caulk. I plan to do the same thing on the garage/upstairs. I also plan to tape the joint between the foundation and the bottom of the sheathing. Then, the ZIP sheathing will be air tight (tape/etc.).
What I’m trying to decide from there is what the best way to air seal the ceiling is, since we have a vented attic? I have seen people tape an air barrier material to the top of the sheathing, going over the top plate, hanging a bit inside the interior wall and then adhering drywall or their vapor barrier to that piece of overlapped material. I am open to that approach. I have also been researching the air tight drywall approach, which seems the most economical but, in many ways, the most challenging to pull off.
Since we’re in Zone 6, an interior vapor barrier is recommended. However, I am siding the house with corrugated steel (over ZIP) so I’m thinking I’ll get good drying to the outside (with the channels in the siding allow for air flow) and I’m wondering if I’m better off just going with no vapor barrier on the inside and using a Class II primer on air tight drywall plus paint to allow for dying to the inside as we will have AC and summers get hot?
If not, I could do a smart vapor barrier on the interior that doubles as an air barrier.
I just don’t want to duplicate efforts and cost.
Lastly, when it comes to the pole barn/post frame section, I was thinking of either doing the vapor/air barrier on the inside OR putting up osb and taping the seams on the interior (not very visually appealing, IMO). I could also opt for ZIP sheathing on this section but the cost somewhat defeats the purpose of going post frame style (but wouldn’t be much different than putting up OSB on the inside). This area won’t be heated to the same degree as the rest of the structure but I still don’t want to be losing a bunch of heat. Any recommendations on the most efficient way to do this section would be greatly appreciated.
Thanks!
GBA Detail Library
A collection of one thousand construction details organized by climate and house part
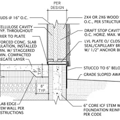
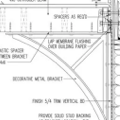
Replies
Are you 6A or 6B? I'm in 6B in Idaho. Did the foam block foundation plus membrane plus drainage mat. My garage steps down 6 steps and is a monolithic slab. Our house roof is vented but portions of the garage/shop are flat roofs. We used rockwool insulation between the studs and 2" on the exterior, and completely covered the house (sides and top) in Blueskin before building the garage. We've been intense about sealing all the penetrations. I wanted maximal drying in both directions, and no vapor barriers other than latex paint. I am not concerned about internal moisture because we are 2 people most of the time in a large house and have a Zehnder whole house ventilation system. I didn't allow any OSB in the house (mold food) so no zip though.
qofmiwok,
It sounds like using monolithic slabs for garages is common in some places. It's not something I've seen, and I'm curious about two details:
- How do you slope the slab to drain and still have the walls at the same height?
- How do you transition from the flush slab at the entry to get the required 6" to 8" separation from grade to framing on the rest of the garage?
Sorry my mistake. I have a regular slab with stemwalls.
Thanks. I had a potential client from Alberta who wanted to do it. Maybe Kosto or someone else knows how it's done.
Hey Malcom,
Typically, we have the edges of the slab level and then slope from the edges to the center and then put a long drain at the low point in the center. That has always worked well.
As for the 6-8 inches, we are having a concrete sidewalk that buts into the slab/foundation all the way around the house (just below the bottom plate - no steps anywhere) and then slopes at about two degrees away from the house, then the landscaping will sit a few inches below the edge of the sidewalk. Thus, we aren't really meeting the 6-8" per se.
We're 6B.
How's your home performing so far?
Kosto, drawings would help, and/or narrowing your question down to 1-2 specific things. There are a lot of different ways to build a good house. Pole barn construction makes it significantly more difficult.