Air tight drywall to prevent moisture in walls

Hello all,
A beginner’s question that many of you might roll your eyes over: If I tape my plywood sheathing seams, caulk the seams at the top and bottom plates, and have air tight drywall on my ceiling, is there any benefit to going to the trouble to air seal electrical outlets, etc. on the interior walls?
My concern is moisture entering the walls with the air from the interior if I don’t seal.
I read Martin’s article, “One Air Barrier or Two?” and it indicates builder sloppiness and wind washing as the reasons for a second air barrier.
I’m in zone 4A (almost zone 3), mixed humid.
Thanks, all!
GBA Detail Library
A collection of one thousand construction details organized by climate and house part
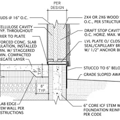
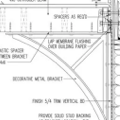
Replies
It depends on the type of wall you are constructing. For a foam sheathed wall, it is not very important: The foam itself is a pretty good air barrier, and mostly immune to the effects of wind washing; it also keeps the structural sheathing above the dew point if installed to an appropriate thickness.
For a wall without foam sheathing, especially a double-stud wall, I would advise two air barriers. The exterior sheathing is prone to condensation in the winter, and the interior drywall is prone to condensation in the summer, so air entering from the outside or the inside can be risky depending on the season. Having an air barrier on both sides is one sure-fire way to prevent moisture-laden air from entering the cavity and condensing. Such walls are also much more prone to wind washing.
One can limit the risks of a single air barrier in a double stud wall by placing towards the middle of the assembly, so that it is rarely cold enough to cause condensation and leaves only a portion of your insulation at risk for wind washing.
Aedi, thanks for the reply. The walls will be 2x6 cavities filled with mineral wool batts and will have exterior rigid foam (unless I can't source any re-claimed, then I will use exterior mineral wool board, like Comfortboard 80). From your reply, it sounds like I would not need to use airtight drywall if using exterior foam, but should consider it if using exterior mineral wool board, which is not a good air barrier?
Even with the mineral wool board, one air barrier will be fine. Your plywood sheathing should be between the mineral wool batts and the mineral wool board, and that puts your air barrier in the middle of the assembly. That'll keep it safe from condensation, assuming you follow the code guidelines for minimum exterior insulation thickness. Summertime condensation would not be an issue, since your WRB will be on the surface of the plywood. Plus the assembly is a lot more resistant to air flowing through it than, say a double stud wall filled with cellulose.
As a side note on your assembly, your water resistant barrier will likely be in different locations depending on if you use foam or mineral wool boards. With mineral wool it makes the most sense to place the WRB between the plywood and the mineral wool boards, whereas with foam it makes more sense to place the WRB on the exterior surface of the foam. While the WRB *can* be swapped in either assembly, it does not make much sense to.
Thanks! Concerning the WRB with exterior foam, what is the benefit of having the housewrap outside the foam rather than inside (or would you even need housewrap at all, since the foam is water resistive)? Thanks again!
If you place the WRB behind the foam, you would need to leave a gap between the foam and the WRB to guard against hydrostatic pressure, which can easily force water through screw holes or other openings (quite powerful stuff). You can do so by using a textured house wrap or similar material, but it complicates installation and adds needless expense.
While the foam is (usually) water resistant, the seams between panels are not. Some manufactures of rigid foam have gone through the trouble of getting their foam products certified as WRBs, but in order for that to work you have to tape the seams using a special tape. Since you are planning to use reclaimed foam, you probably won't have the luxury of being picky about getting a foam product that has been certified as a WRB.
KS,
All flashings at windows, doors an other penetrations have to go back to the WRB. If it is behind the foam that makes flashing more complicated.
Malcolm, I plan to do innie windows (similar to traditional window installation, so I am more comfortable with it), so it will actually be easier to flash to WRB at the sheathing level.
Aedi, is the hydrostatic pressure concern a recent discovery (last 7 years)? I just found a 2011 article from Martin Holladay (Where Does the Housewrap Go?) that does not mention it. Do you have any links to research about this issue? Would I be reasonably protected from that problem (water getting behind the foam) by the rainscreen, the foam, and proper window sill pan flashing?
>Aedi, is the hydrostatic pressure concern a recent discovery (last 7 years)? I just found a 2011 article from Martin Holladay (Where Does the Housewrap Go?) that does not mention it. Do you have any links to research about this issue?
Hydrostatic pressure is not a recent discovery, just a commonly underestimated one (I have been guilty of it myself). A narrow column of water one story high applies the same amount of water pressure to a point towards the bottom of it as a wall of water one story high would. Here is an overview of some of the dangers at Building Science Corporation:
https://buildingscience.com/documents/insights/bsi-057-hockey-pucks-and-hydrostatic-pressure
> Would I be reasonably protected from that problem (water getting behind the foam) by the rainscreen, the foam, and proper window sill pan flashing?
The rainscreen and the foam will help, but all of your flashing will direct water *toward* the WRB -- that is, behind the foam. That can quickly lead to issues.
Thanks Aedi, you have been a big help. I'm sold on the hydrostatic pressure - I don't want hockey pucks in my wall ;). So if I put the housewrap outboard of the rigid foam, that also requires outie windows, correct? And how would I attach the housewrap to the foam? Long nails that can get to the sheathing?
No problem, I am happy to help!
While I'm sure some clever person out there has probably found some way to make innie windows work, outie windows are the natural choice with outboard housewrap. Most people prefer them from an aesthetic/usability aspect as well (the deep sills are useful for displaying items or including built-in seating, and look nicer than regular windows IMO).
As for installing the housewrap over foam, I don't have much personal experience in that regard. However, you seem to be planning furring strips and a rainscreen gap, so I believe the best thing to do is to find a way to temporarily affix the housewrap to the foam (probably caulk), and then use the furring strips to permanently hold the housewrap down.
Hopefully someone else can shed some light on their preferred approach.
An exterior air barrier in a cold climate will allow some greater amount of moist air to enter the wall cavity, deposit moisture (even with exterior foam) and return to the interior. Similar to convective downward airflow over a cold window. There are advantages to interior and exterior air barriers (where you can't do middle of the wall).
Thanks Jon, I'm just barely in Zone 4A, close to border with Zone 3. Will I still have issues with moisture driving outward since so much of the year is warm (requiring air conditioning)? Also, with exterior insulation, would my assembly be nearing a middle-of-the-wall air barrier? Thanks!
A safe wall should dry to both sides and ADA is a good way to facilitate inward drying. It can be used in conjunction with some of the breathable membranes available today. This allows for the insulator to put in place the membrane in an airtight fashion so the airtightness of the home is not reliant on the drywall installers.
I will not get into the discussion of poly vapor barriers for a cold climate and drying with the flow of heat to the cold side only. A warm side vapor permeable membrane is the safe choice in cold climates. ADA standing alone needs great attention to detail.
This is an owner build (me), so I am not concerned with attention to detail - If it's done wrong, I can just fire the guy ;). But I am looking for the for maximum return on my time, of course. That's why I am questioning if ADA is necessary for my wall assembly in Zone 4A/3A. I would like to avoid if the benefits are marginal. Although, I am the type who wakes up from stress dreams about moisture in my walls, so I might just do it so I can sleep better.
It is not just moisture but airtightness and building performance you should be considering. A leaky house is tough to heat and cool and in this day and age it is inexcusable to build a new , leaky, drafty house. If you put a value on your time you will air seal to the highest degree. You can brag about your efforts and ask others, what is your ACH50?
It is much easier to seal things properly as you build the house than it is to go back and try to retrofit airsealing afterwards. Do it correctly now, you’ll thank yourself later.
Bill