Air Sealing Target & Technique

Context first, then two questions for the community below.
I am building a 3,900 square foot, 3-story, 6 unit apartment building in climate zone 6A with the following wall assembly:
– Hardie Siding
– Rain Screen
– Tyvec House Wrap
– Type X DenseGlass (for fire rating)
– Plywood
-2×6 framing @ 24OC w/dense packed cellulose
– ProClima DB+ smart air barrier
– Type X Gyp
It’s my understanding that properly detailed, the ProClima DB+ will serve as my primary air barrier, with the stapled Tyvec as a secondary (albeit poor) backup.
I would like to set a contractual air tightness target of 0.8 ACH50 for the builder but they are hesitant.
My questions are:
1) Is 0.8 ACH50 a reasonable (no heroism involved) target for this assembly if details are appropriately implemented? If not, what is reasonable?
2) Is the air sealing proposed sufficient, or should I also be taping the seams of the plywood?
GBA Detail Library
A collection of one thousand construction details organized by climate and house part
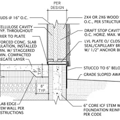
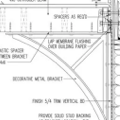
Replies
If you look at it from the contractors point of view taking on risk without a bigger reward is a bad business decision.
If they take on risk of some penalty by putting in writing .08 ACH what is the reward to the contractor?
Now if you are offering a bonus for making the goal and no penalty for failure that is a very different proposition, assuming the bonus is too large to be ignored.
Walta
cmfischer,
You will have much better chance of achieving the air-sealing target if all the details are incorporated into the construction drawings. Then the contractor just has to follow them, rather than invent them onsite. Of particular usefulness will be air-sealing of things like party-walls, common areas, mechanical penetrations, etc. that are unique to multi-unit buildings.
A three story building with multiple units will have a large stack effect. You may want to consider completely sheathing the underside of the trusses before interior framing and drywall.
CMFischer,
If you want a really tight building, you also will need mechanical ventilation. What do you have in mind?
Also... Have you considered using an integrated multi-family system such as Build Smart (https://buildsmartna.com/products/)? It might be worth the cost to avoid remaking the wheel.
Some sources list perm values of 8 for plywood (wet perms), 17 for DensGlass and 56 for Tyvek.
1/(1/8 + 1/17 + 1/56) = 4.96. So you don't quite make the 5+ exterior perms recommended to avoid wall moisture problems. While cellulose and variable perms on the interior help, 3rd floor stack effect and the less conscientious humidity control of renters suggest being more conservative. So consider 1.5" unfaced EPS outside the plywood (see here).
.8 ACH50 is going to be difficult for a builder not well versed in highly efficient construction. A more realistic target would be 1.5 ACH50 with incentives to improve it. You will still get high performance with 1.5 ACH50, remember this is the leakage rate under depressurization and not typical year long. As others have said, the details for this building need to be clearly spelled out, have a good plan.