Air sealing strategy for north Idaho ranch

I’m working with a builder who is not a “green builder”. My perception is he does practice good technique in terms of installing and sealing windows and doors but has not been tasked with achieving a low air infiltration in the past.
In order to get to my goal (3.0 ACH50), I put together this strategy, see attached. My thought is to identify the actions he will execute to get to my goal.
Does this list look like it is enough? Am I missing any big bang for the buck items?
Thanks.
GBA Detail Library
A collection of one thousand construction details organized by climate and house part
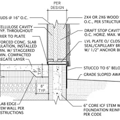
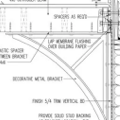
Replies
Air leakage of 3ACH/50 isn't really optional- it's the IRC 2015 code maximum, and it's really a stripe on the floor, not a hurdle to hit, with even cursory attention paid to air sealing. Set some tighter goals, say 1ACH/50, or 1.5ACH/50 (half code-max.)
You need to seal the bottom plates of studwalls to the subfloor or foundation, and between any doubled-up top plates, as well as caulking the framing to the sheathing inside every stud bay. Polyurethane caulk is a good material for that application, and it goes surprisingly quickly using powered caulk guns.
Foamy sill gaskets between bottom plates & foundation are notoriously poor at air sealing, but EPDM sill gaskets can work well without additional goop. If the top of the foundation is uneven or rough it's sometimes necessary to use a bead of expanding can-foam under the plate as the framing goes up.
Electrical & plumbing penetrations need to be foam-sealed at every framing penetration too, not just at sheathing or top/bottom plate penetrations.
Ideally all ducts will be fully inside the pressure boundary of the house.
Make sure there is taped wallboard everywhere even where it won't be painted or won't show, including behind tub-surrounds and cabinet work. Tract home builders on tight margins will sometimes slap up a crummy sheet of polyethylene or nothing at all behind tubs & showers to save the cost of a few sheets of wallboard, and it's a total PITA to fix those leakage paths after the fact.
Thanks Dana. Some good tips.
I should have added more detail on construction. The house will be slab on grade, I will be sure to spec EPDM gasket. The heat will be hydronic floor heat. The only ducts at this point are for kitchen hood and bathroom vent fans. I'll save the ventilation questions for another post. I'll be using blown in fiberglass for wall insulation. I have a tile shower on the outside wall, no surrounds.
Evidently "code" is a local thing. In Idaho, I believe they are operating with IRC 2012 as current code, but I am still researching that. My builder has never done a blower door test.
Steve,
Lists like yours are good, as far as they go. But a successful job depends on good execution, which is hard to describe in words.
You need a builder who cares; who understands the basic principles of air sealing; who pays attention to air sealing at every stage of the project; and (ideally) who has already built several buildings tested by a blower door.
If this is the first job your builder has ever done that included a blower door test, cross your fingers. You probably want to schedule two blower door tests: One right before drywall goes up -- that's the one where you are on hand with caulk, tape, and spray foam, because this test is basically an opportunity for blower-door-directed air sealing -- and another test after the house is complete.
-- Martin Holladay
Thanks Martin. I believe I do have a builder that cares about doing what I ask. And I have the luxury of being able to be present every day during the build. Successful projects happen because you have clearly identified what you will do and then execute, I get that. Thus my desire to have a list that identifies specific items worth doing. I see the interim blower test on a house with vented eaves and ridge as difficult to execute and unnecessary. If the list correctly identifies major points of infiltration and we execute, we should hit the goal. The blower test at the end will confirm it and then we'll break out the beer.
I've modified my goal based on Dana's input to be less than 2.0 ACH50, same as Pretty Good House.
Are the items on my list now sufficient (assume good execution) in your opinion to achieve 2.0 ACH50?
Here is the updated list.
If you take Martin's suggestion to chase and fix all the air leaks you can find with a blower door before the wallboard goes up you have an excellent shot at beating 2ACH/50 by the end (or even 1ACH/50.)
The first blower door test must be BEFORE the insulation is installed, so that you can see all the framing and easily find and repair the leaks. After insulation is complete the leaks are much harder to find. If you wait until after the drywall, you have very little opportunity to do anything about it. We've had two situations where the pre-insulation showed 10 ACH on one house and 3 ACH at another. We found and repaired the leaks and tested around 1 ACH50. After insulation and finish, they were both well under 1 ACH.
Just completed my blower door test. ACH 50 is 1.7. I'm happy with that. I attached an updated strategy I used to get this level of air tightness. I added notes for products used.
I appreciated the advice on this thread and others to get to this level. I will admit I ignored the advice to get a blower door test before wallboard.
Things I could have done better:
Better windows. I used Jeld Wen triple pane single hung. A lot lower cost than imported casement windows.
Better door seals. During the blower test, it was obvious those were a weakness, but something I can address over time. I have 5 doors to exterior.
Sealing of windows and doors after installation. Unfortunately because of my schedule I had to rely on the insulation contractors to do this. From what I saw, they did OK but I would have liked to have done that myself.
Here is the air sealing strategy document referred to in previous post
Steve,
Thanks for sharing your document and reporting back on your results.
1.7ACH/50 means you beat the Canadian R2000 house air tightness standard (
That's pretty good for "...working with a builder who is not a "green builder"...", and not being able to fully inspect (or perform) all those air sealing details yourself.
The annual energy use difference between your 1ACH/50 house and the same house at PassiveHouse type tightness is pretty small. Ya done good!
Thanks Dana. It's quite satisfying to get this first piece of data on the results of my efforts. Can't wait to get some energy use data.