Air-Sealing Plank Sheathing

I’m getting ready to replace the siding on my 100-year-old house and want to make energy/comfort improvements while I have the walls exposed. The current walls are (from the inside out) ½” drywall, kraft-faced fiberglass batts, ¾” horizontal shiplap sheathing, and vinyl siding. I’m going to remove the vinyl siding and add a WRB, replace all windows (the current ones are aluminum and in terrible shape), add Comfortboard continuous insulation, rainscreen, and Hardie plank siding. My concern is with the current sheathing as the shiplap presents a problem with air sealing and, here in seismically active Seattle, it’s also a problem with regard to shear strength. We’re going to have a seismic retrofit done first so the pony wall will be sheathed to current code, and current seismic retrofit recommendations (and code) don’t include resheathing all walls. Still, I’d feel more comfortable with some additional shear strength, and I expect that sheet sheathing would allow me to get the house much tighter. Note that we’re not going to be opening up the interior side of the walls anytime soon, so sealing from the inside isn’t an option. The question is if I should do something about the sheathing, and, if so, what; or, alternatively, if I leave the sheathing as is, what I should do to properly air seal shiplap. The options that I’m currently considering are:
1) Leave things alone, don’t worry about the shear strength problem and air seal with a peel and stick WRB
2) Strategically replace sections of sheathing with plywood/OSB to act as shear walls, and air seal with a peel and stick WRB
3) Leave the current sheathing in place, but add a layer of Zip sheathing over the current sheathing and use that as my air/water barrier (note that given current prices I can get zip for about the same price as regular OSB + Tyvek)
4) Fully resheathe the house with Zip sheathing
The price difference between the options isn’t large enough to be terribly influential in the decision. The bigger issue is the amount of time/work each will take since we have a fairly short dry season here in which to do all of this work. What are the opinions here on these options or do others see any better choices? Thanks!
-Jeff
GBA Detail Library
A collection of one thousand construction details organized by climate and house part
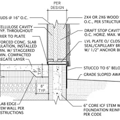
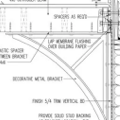
Replies
There's no doubt that adding sheathing to the whole house will improve its seismic strength/stiffness. That could be enough reason to do it by itself. With the general cost of your work, the cost of the various sheathing options won't move the needle all that much in either direction. I think I'd go with adding a full layer of sheathing and WRB over the existing board sheathing. Taking the boards off adds time & expense as well as more landfill space. Plus, the board sheathing adds a little bit of R-value. If ZIP is about the same price as OSB+Tyvek, I'd probably go with the ZIP. That's going to be easier to treat as air/water layer.
Thanks Peter. That's the direction I've been leaning for exactly the reasons you stated. I wanted to make sure that 1) sheathing over sheathing isn't a great sin that I'm unaware of, 2) that I'm not being neurotic and taking on pointless work, and 3) that there isn't some better solution that I'm missing. I appreciate your thoughts.
Jeffrey,
If you do decide to add sheathing, I'd go the extra step and tie your newly seismically upgraded pony walls into the ones above. There are a few details for that. Two common ones use Simpson HTT4 hold-downs, or ST22 straps.
Thanks Malcom. I’ll definitely look into code/recommendations for strapping between floors.
There is an in-between option as well.
You can brace the corners of the structure with new sheathing and leave the rest as is. It will significantly improve the strength of the structure without having the re-sheath the whole place.
You can strip off the shiplap in the corners for space which would keep everything co-planar or go over the shiplap and use exterior rigid 1/2" thinner in those areas.
That’s an interesting idea. Similar to option 2 but saves the work and waste of removing sections of sheathing. I’m a little nervous about foam since I’m under the impression that it’s usually safest to maintain some vapor permeability in old houses (hence the plan to use comfort board). Is that something that I shouldn’t really worry about?
As long as you have the right amount of rigid for your climate for condensation control any type of foam is fine. See here for ratios:
https://www.buildingscience.com/documents/building-science-insights-newsletters/bsi-100-hybrid-assemblies
If the amount of rigid is less, it can still work provide the foam is permeable and there is a some vapor barrier coating on the inside. Usually 100 year old walls have multiple layers of oil paint which are pretty much vapor barriers. Permeable foam is unfaced EPS/GPS/XPS or breathable polyiso (ie Ener-air).
Mineral wool is great option but it is pretty spendy plus a bit annoying to work with as it is still somewhat squishy and it takes a lot of adjusting to get strapping flat.
I have a very similar situation with a 150 year old home, minus the earthquake issue. I was planning on using Blueskin over my T&G sheathing, 2 inch PolyIso, rain screen and then Hardie Board.
I'm also opening up the interior walls and redoing them as well, perhaps with closed cell or Rockwool.