Air sealing and the point of diminishing returns

I’m curious at what point does it no longer make sense to spend more time/money on tightening up a house. We had our house blower door tested unfortunately after construction was completed. The house is closed cell spray foam walls and ceiling.
I was shocked that the first test was 3.2 ACH50. The test along with thermal imaging allowed us to locate some major problem areas that we addressed, most of which were behind timbers in corners that did not get sealed well. (House is a timberframe hybrid).
After additional sealing in those areas we tested at 1.9ACH50. Our final report showed that wasted energy from air leakage at 1.9ACH50 was minimal and financially didn’t make sense to spend any more time or money.
I’m not sure how accurate that is and was wondering what your opinions are? Are there any additional savings of significance by tightening up any more than where we are at now? If we do tighten up the house more, my concern is that any savings would be offset by having to install a HRV. With an active house and 3 kids an HRV has not been necessary although we did plan for the addition of one if needed at a later time.
Jeremy
GBA Detail Library
A collection of one thousand construction details organized by climate and house part
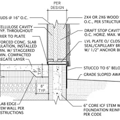
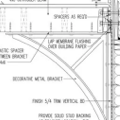
Replies
Jeremy,
I think you need to look at your numbers more (it's simple math), or wait for someone here maybe to do it, concerning your ventilation needs. At 3.2 ach50, it was probably already time to add mechanical ventilation (ERV, etc.), especially with all those CO2 generators in the house.
I achieved 4 ach50 with a not too aggressive retrofit, but according to the latest ASHRAE ventilation standard, I need mechanical ventilation. I have been living 2-3 years at that number and no added ventilation without any concerns, but if I was at 3.2 or less with kids, I really think I would need to add ventilation.
Thanks Rick. I'm interested to hear what others may say. My CO2 generators mean doors are constantly opened and closed, bath fans are always on, and the electric dryers moves air out of the home for hours a day or so it seems anyway.
All that ancillary ventilation just may be keeping you all healthy, at 1.9. All I am saying is that I think
you are under ASHRAE recommended ventilation, and probably below your local code, also.
Rick this was my thought as well and is why we chose not to install an HRV but planned for one in the future when its just my wife and myself living here. Right now we have a very active home and no signs of needing additional ventilation.
Jeremy,
Good for you for caring about air sealing, and good for you for setting a high bar.
As you have discovered, it's a little late to pay attention to air sealing after the construction work is complete. It's probably true that you've done the best you can at this late stage of the game. As weatherization workers know well, there is a point reached where the crew members all say, "We've done all that we can. Tracing down the last few leaks will take more hours that it's worth."
I urge you to come up with a plan to install a mechanical ventilation system. For more on this topic, see the article scheduled for publication this morning: All About Indoor Air Quality.
Hi Martin,
I did all of the weatherization after the fact myself so there is no additional cost to working on it some more other than time. I know where some of the additional leaks are coming from. It's not easy to seal but can be done and none of them are high in the envelope. So back to my original question, would there be any significant savings to take our house from 1.9ACH50 to say 1.0ACH50? Based on my utility bills and how little it takes to heat our home I'm assuming probably not?
Jeremy,
I think that it makes sense to aim for 1 ach50, if you can get there without too much pain. There are many benefits to air sealing. Not only does air sealing lower your energy bills; it also reduces temperature stratification in your home, reduces room-to-room temperature imbalances, improves occupant comfort, and makes the house more resilient (because the house won't see as much of a temperature drop during power outages as a leakier house).
So, if you are willing to continue your efforts -- by all means, continue.
If you are an air sealing nerd, you should go out and buy a theatrical fog machine: Pinpointing Leaks With a Fog Machine.
Martin I'm in the pyrotechnics business so I actually have a few machines sitting in my shop at work. I've just been waiting for warmer weather before putting them to work. Thanks for the link to the article. I'm not a prime member so I couldn't read it but have read many others on this and other sites which is why we had our HVAC system designed so that we could add ventilation if needed at a later time.
In regards to ventilation I have read many articles about the need and benefit and I'm not dismissing the importance. I just don't see the need for it in our current circumstances. If it were just two of us living here I would agree however we have 3 kids ages 7-12 and a very active house. Here are some of our home details. First, we do not have a humidity problem in the house at any time, even in the warm summer months. I have zoned wifi t-stats and can monitor humidity so I know the actual readings including the conditioned attic space. The air does not have a stale or musky smell to it when we arrive home at any time, it always smells/feels fresh. (very unscientific I know) Other than a gas range top (oven is electric) the whole home is electric with geothermal heat/air. There is no carpet in the house, its all hardwood floors, no smokers, no candles, no plug in air fresheners, etc, etc. We do have a wood burning fireplace insert with glass doors however I had it designed as a see thru indoor/outdoor unit. It uses outside combustion air and all loading and cleaning is done from outside of the home. No indoor pets in the home.
In regards to exhaust our home is 3500 sq/ft. Assuming 80 cfm needed (correct me if I'm way off) thats 115,200 per day needed. All of my bath fans are 90 cfm units connected to the lights so if the lights are on the fans are exhausting. We do a minimum of two loads of laundry a day @ 240 cfm. Over the range kitchen hood is 600 cfm.
- Showers/bathroom use 90*5 persons* 45 minutes per day = 20,250 (in reality the kids never turn them off when their done. I'm turning into my parents with my ocd on lights)
- Dryer 240 cfm * 120 minutes = 28,880
- Range Hood 600 cfm * 30 minutes = 18,000
Total = 67,130
Now add in all of the daily activity in and out of the house with doors opening and closing all day long and I just don't see how we are not meeting our daily needs for ventilation. I know I'm going to get replies that say I am absolutely wrong but that's ok. That's why I've chosen to discuss this in more detail so I can learn what others have to say and why.
Jeremy
I'd check CO2 levels as a proxy for IAQ. Too much CO2 makes us mentally sluggish.
Stephen do you have any recommendations for a quality meter that won't break the bank?
>>would there be any significant savings to take our house from 1.9ACH50 to say 1.0ACH50? Based on my utility bills and how little it takes to heat our home I'm assuming probably not?
You could approximate the answer using some basic math. Take a leap of faith and turn the two ACH50 numbers into ACHn numbers, and calculate the cost of heating the air lost via natural exfiltration using your assumed fuel and heating efficiency costs. Then, calculate the needed ventilation and factor in the cost of heating the ventilation air.
My guess is that it's worth very little in your case to do much additional air sealing. Your ACH50 number is already quite low and if you have a correctly functioning geo system you probably have a very low heating cost. If you had high heating costs and already had a HRV, the math would be different and would probably favor more air sealing.
Jeremy wrote:
"Martin I'm in the pyrotechnics business so I actually have a few machines sitting in my shop at work."
Perhaps the best reply I can remember on GBA.
Stephen wrote
"I'd check CO2 levels as a proxy for IAQ. Too much CO2 makes us mentally sluggish"
My wife accuses me from time to time of being mentally sluggish, only she does not phrase it in such nice words. I've order a CO2 monitor and will know shortly if I have an excuse. I'll be quick to admit if I'm wrong about our air exchanges and will post results when I have them.
I recently ran across a comprehensive collection of notes on indoor air quality monitors, mostly consumer units priced around $200:
http://www.energycircle.com/guide/guide-indoor-air-quality-monitoring-devices-healthy-home
and
https://docs.google.com/spreadsheets/d/1hDEeuR8-v7HLb90Fmq0gNfH0vRPXaCywMFPHekscFOw/edit#gid=0
Basded on that and browsing some Amazon reviews, I'm thinking of trying an Air Mentor Pro.
Charlie thank you for the taking the time to post your list. I appreciate it. David I ran the numbers and you are correct that additional air sealing would not gain us any significant savings and is a net negative when factoring in an HRV. Now just need to wait for some air monitoring to find out if we do or do not need to make this investment as others have suggested.
I looked at the Energy Circle article on low-priced IAQ monitors and it doesn't address whether any of them can be recalibrated. As such, they are probably disposable after a certain point... a couple of years?
I brought one of our fog machine home today along with a 3600 cfm fan and learned a few things.
1. No residue left behind. The house is full of exposed beams and finished woodwork. I was a little nervous but there was absolutely nothing left behind on any surfaces.
2. Glad press & seal works great for sealing up smoke detectors and will stick to both finished wood surfaces and sheetrock.
3. Average leaks are easy to find. Very small leaks not so much. I found I was losing a lot of air through the electrical service penetration into the house. I also decided to fog the garage and pressurize to check some of the solid duct work running through a portion of the attached garage. I found at low pressure we did not have any leaks however at max pressure (3600 cfm) some of the fog found its was into the adjacent mechanical room with our geo unit as well as into the supply ductwork leading into our living room. Not good. Time for some duct sealing and a door with a better seal to our mechanical room.
Jeremy,
It sounds like my suggestion (in Comment #7) to use a fog machine is bearing fruit. That's great! (Excellent photos, by the way.) I had no idea that you were in a profession that required fog machines, and that you had a few of these devices sitting in your office.
I'm really glad to hear of another successful application of this useful technique.
Congratulations on your air sealing results.
I encourage you to take CO2 measurements over a period of time, under different conditions. Hopefully your monitor can save peak readings. The results in my house were surprising to me, especially how quickly CO2 builds when interior doors are closed and there is no active air distribution in the room. If you find anything interesting after a couple of weeks, please post.
How did you pressurize the house? I assume you installed your fan in a door or window somewhere.
If you can get ahold of a thermal imager, depressurize the house on a cold day with the range hood, bath fans, and clothes dryer, and then look for cold air infiltration.
Hi Andrew. The unit I've got ordered does track and log peak readings so if we have a spike I'll be able to detect it. I'll be sure to post results when available. I'll either be correct in my assumptions of enough air exchange or will be a good poster child for some of you to point to as an example of why an HRV is important.
David I used some rigid foam in a window with a cutout for a 3600 cfm fan that I used to pressurize the house. In the previous blower door tests we did those in the winter and did use a thermal scanner to find cold spots as you pointed out. It we very helpful to see the problem areas.
Jeremy
The short answer is that it probably does not make economic sense (you have to put some value on your time) but so what? As Martin points out, there are many other benefits to improving the air tightness and I'll add another. I know from experience how difficult it is to tighten up a house after the fact. Achieving 1.0 ach@50 is quite doable -- if you are starting from a clean sheet of paper or doing a deep energy retrofit -- but is pretty challenging other wise. I'd say 1.9 is impressive and you should feel a great deal of personal satisfaction if you actually could get to 1.
Question: When you blew the 1.9, which vent openings were sealed? I am especially curious about your glass door fireplace? Every "airtight" glass door fireplace I've seen is no where close to airtight but you could seal the exhaust flue opening and the make up air intake. I believe it is customary to seal HRV/ERV openings which makes sense to me. Not so sure about direct vent exhaust openings, let alone fireplaces. If they are shut off, does that not compromise the validity of the test?
As for ventilation, your bath fans and kitchen fan are certainly potentially adequate to provide sufficient ventilation. But that doesn't mean that an HRV/ERV wouldn't be a good idea since they combine ventilation with energy recovery and also reduce the reliance on occupant participation. One suggestion, wire the bath fan and bath fan light separately and put the fan on a timer and encourage users to set the fan to continue to run (if appropriate) after the light is switched off.
Beautiful house, by the way.
Hi Buzz. None of our vents including the fireplace were sealed for the test. The flue damper was closed only, not sealed. As far as the glass doors they are not airtight but do seal pretty well. When I fogged the house I did check the fireplace. There was a very small amount of fog inside at the end of the test. I was quite happy with how well it did. After seeing the fog movement from the garage space into the living areas my guess is that a decent amount of air loss during testing is through leakage from our ducts and HVAC unit located in unconditioned (untested) space. I started efforts yesterday at additional sealing of ducts in this area as well as our mechanical room. If I am correct, the actual leakage would be minimal since this area would not be under pressure unless the garage doors were opened. It does however present a potential health issue which is why I'm addressing it.
Overall the performance of our envelope has been very good. The house is very open so I have no issues with warmer or colder areas from 1st to 2nd floor. All t-stats maintain a very even temperature. The house holds heat surprising well given the number of windows and exterior doors ( 32 windows 6 exterior doors). Heat has been off for several days. Last night our house temp was 70 degrees with an outside temp of 61. Temps dropped overnight to 36 degrees, yet our home was still 68 degrees at 9am this morning. As I'm typing this afternoon it is sunny and 65 and our inside temps are back to 70.
Thanks for the suggestion about fan timers. I should have my monitor on Saturday and will be able to start taking readings. I'll post what I find. Also thank you for the comments on the home. I was the designer, general contractor, and did all of the finish work on the home so we are proud of the end result. Here's a link to additional pics if interested. https://www.flickr.com/gp/jeremykovac/21Z902
Edit: Much credit is due to Clydesdale Frames Co as well who took our plans and ideas and contributed to the final design. They did the finished construction drawings/plans for us and helped bring everything together to a single master plan including cutting and standing the frame. Outstanding work on their part.
I received my Co2 monitor yesterday. So far I have only monitored the main living area. In future days I'll setup in the kids bedrooms and measure for spikes in those rooms that are a little more isolated. The house has been sealed up for the last several days. Current Co2 level is measuring at 647 ppm.
Jeremy
Co2 levels spiked a bit this evening with lots of company over. Will see if it levels off on its own. Looks like I may need a bit longer to develop a trend and see how the house is performing.
At what level of sustained ppm levels should I start to take notice? Now that I've got my monitor I need to know what we should be aiming for for a base level or what would be considered high?
Bump. Anyone? Still wondering at what CO2 level would anyone with knowledge consider it likely that a home poor air exchange? After checking our logger for a few days now we are averaging between 750ppm to 900ppm. Largest spike was 1155ppm while cooking with company over. 2-1/2 hours later it was back below 1000. This is the only time in the last 4 days it has been above 1000. Thoughts?
Jeremy,
You might want to read this article: Stuffy Offices Lower Cognitive Function.
The article quoted a researcher who said, "We found statistically significant declines in cognitive function scores when CO2 concentrations were increased to levels that are common in indoor spaces (approximately 950 ppm)."
Thanks Martin. So for those of you with an ERV/HRV that have monitored CO2 levels what do your numbers look like? We are averaging about 830-850 most of the time. I'm finding it hard to justify investing a few thousand dollars when we are already under ASHRAE standards as I suspected.
Jeremy,
More information on CO2 and ventilation comes from the manufacturer of the CERV. The manufacturer advises owners of this device -- the operation of which is controlled by a CO2 monitor -- to set the controls so that ventilation begins when CO2 levels reach 1,000 ppm.
For more information, see A Balanced Ventilation System With a Built-In Heat Pump.
Our house runs in the 800-1000ppm CO2 range with exhaust-only ventilation. For whatever reason, it won't really go below about 600ppm even if I leave the windows and doors open. I've noticed this same thing in other houses. It's a hair under 400ppm outdoors, but never near that indoors.
Thanks David as well as everyone else that has replied so far.
Our meter shows 400ppm outdoors. I may look into Buzz suggestion of bath timers to add a bit longer exhaust run times for now and will continue to monitor for any changes. I've finished duct sealing in the garage and mechanical room. May try to fog test this area again tomorrow to see if leakage into living areas has improved.
Jeremy
Jeremy, thanks for the pics, great job! Back to your diminishing returns and air quality issues; In your initial question you stated that "Our final report showed that wasted energy from air leakage at 1.9ACH50 was minimal and financially didn't make sense to spend any more time or money." One responder said that the energy savings should be a straightforward calculation. But is it? The test is performed at 50 pascals, a pressure differential that's way more than typical. That doesn't make the test invalid, but the test results do not provide enough data to accurately calculate the energy cost from air infiltration. To do that you would need to know actual pressure differential and presumably the final report took that into consideration and calculated energy savings using an estimated pressure differential leading to the conclusion that additional air tightening would not be cost effective. But the pressure differential is constantly changing with atmospheric conditions and the operation of fans and combustion appliances and who knows if air infiltration varies lineally with pressure differential or not, making it even more difficult to calculate with much precision. It's easy to get hung up on numbers, I know I am often guilty of that, but the bottom line is total house performance and your house seems to be performing quite well. Which leads me to some questions for you. Do you mind telling me the manufacturer and model of your fireplace insert? I am also curious about your comment that your hvac system is located in an unconditioned and untested space. A space can be unconditioned but still inside the thermal envelope but when you say that it is also untested I assume that means it is outside the envelope. What type of system is it and what led to your decision to place it outside of the thermal envelope? And finally, loved the pictures and the timber frame interior is spectacular. It appears as if most or all of the wall insulation is outside of the timber frame and isn't particularly thick yet you're getting good performance. SIP's?
>>One responder said that the energy savings should be a straightforward calculation. But is it?
What I said is that the math is straightforward, but you have to accept there can only be estimates of air leakage under natural conditions. The Energy Conservatory's blower door software provides fairly detailed output, including estimates of natural air leakage and the dollar cost of air infiltration based on your stated heating fuel cost and system efficiency. I have not drilled down on exactly how these estimates are made, or how accurate they are thought to be, but if you have nothing else to go on (and you don't...) they are a start.
Not a problem Buzz. Glad to share. Please see answers below.
Buzz asked: Do you mind telling me the manufacturer and model of your fireplace insert?
Answer: Acucraft Hearth Room 44. See through model with outside combustion air.
Buzz asked:I am also curious about your comment that your hvac system is located in an unconditioned and untested space.
Answer: We have two geothermal heat pumps. One on the north end of the basement in conditioned space. The second which I was referring to is in a mechanical room built into the corner of the garage on the south end of the basement. We could get by easily with one unit but that's for another thread. Our HVAC contractor was apparently not up to speed on closed cell foam performance. Hardly anyone in our area spends extra money for stuff they can't see when they build.
Buzz asked: A space can be unconditioned but still inside the thermal envelope but when you say that it is also untested I assume that means it is outside the envelope. What type of system is it and what led to your decision to place it outside of the thermal envelope?
Answer: The garage is a walkout basement garage. So technically because it is insulated I guess it would be as you described. Unconditioned but within the thermal envelope. After some work this last week I have found that I have the mechanical room which houses this geothermal unit very well sealed from the garage. I still do however have some leakage through the ceiling under pressure as well as through the return air duct that runs through the garage. Work still needs to be done there. The HVAC contractors decision to use two geothermal units was based on the size of home and layout. By splitting the units it shortened duct runs. The very open floor plan with timber construction left us with limited areas to hide mechanicals including HVAC ductwork.
Buzz asked: And finally, loved the pictures and the timber frame interior is spectacular. It appears as if most or all of the wall insulation is outside of the timber frame and isn't particularly thick yet you're getting good performance. SIP's?
Answer: Thanks for the comments. We are in NW Missouri zone 5. The timberframe is almost completely wrapped with only 3 timbers that penetrate the building envelope. We chose to stick frame in place of using sip panels. Exterior walls are filled with 3-1/2" closed cell foam on exterior walls. Certainteed insulated vinyl siding on outside of exterior walls. Cathedral ceiling is 5-1/2" closed cell spray foam. Remainder of ceilings are 6-1/2" of closed cell so that rafters are not exposed to help with thermal bridging. Basement walls 2" closed cell spray foam on all walls. 2" closed cell spray foam in basement garage ceiling. Batt insulation in finished basement ceiling. No insulation under slab. We chose not to insulate under our basement slab due to how we use our basement finished space. With 3 kids the basement is used all summer long, much more than during our winter months. With the closed cell on walls and insulated ceiling our basement maintains a very nice 67 degrees in the summer and 65 degrees in the winter without the HVAC running. We have the basement zoned for HVAC but rarely use it. Our heating bill this winter was roughly around $500 for the season. 0.13 Kwh electric rate.
Jeremy
Buzz I dug into some numbers for this last year Jan 15 to Dec 15. Here's some exact usage numbers for whole home energy use with 5 occupants as well as just heat. I did not monitor for air conditioning last summer. House is total electric with the exception of a gas range top, oven is electric. Fireplace use was very limited this season. We get a lot of solar gain from all of the large windows. The large roof overhangs help shade the windows in the summer months.
1st & 2nd Floor Sq/Footage - 3750
finished basement Sq/Footage - 900
Total home Kwh usage including heat/air - 28,261
Heat (Oct 2015 through yesterday) - 3,782
Thanks, Jeremy. I'm sure many of the readers of this site have similar stories of HVAC contractors grossly over estimating the heating/cooling requirements of well insulated homes. Our 3300 sf house was built in the early seventies to the typical standards of the day and was heated by a 100,000 BTU oil burner and cooled with 4 1/2 tons of ac. A few years ago we replaced all that with a geothermal system. I explained to the HVAC contractor how I had significantly upgraded the insulation and air tightness over the years but he insisted that we needed a 5 geothermal unit. We compromised at 4 tons. Fortunately, it's a 2 speed 4 ton and it's possible to lock out the higher speed (it operates more efficiently at the lower speed). I have locked out the high speed setting so it is effectively a 2.6 ton system. And it has never failed to maintain the desired temperature running at half the recommended capacity which is also less than a third of the capacity of the original oil burner.
I ended up doing something similar with our units. They move from stage 1 to stage 2 depending on the percentage of zone called. I basically added an additional zone that did not exist so that even when all present zones called, it kept our percentage low enough to prevent stage 2. Effectively turning our two 4 ton units into 2-1/2 ton units. I also modified zone dampers to not close completely to allow for bleed into non-called zones. This lowered the airflow in calling zones and helped out the zones that were not calling so that they held temp longer before calling again. This greatly helped the short cycling problem we were having and everything seems to be working well and efficiently now.
Just a quick update. After three weeks of monitoring Co2 levels my numbers seem to range from 640 to about 820. Most of the time it is in the 720-740 range. The total volume of the house may be working in our favor as well. We have about 52,000 cubic ft of conditioned space. I did add timers to the bathroom fans.
I was also able to seal off the ductwork and mechanical room in the garage portion of the house completely. In my initial fog test I had fog coming through all return and supply vents in the conditioned space under pressure as well as through the floor next to the bedroom wall in one area. Now there is no visible sign of leakage when fog testing, even after a sustained period of time. If anything has come of this thread, we should no longer have to worry about air leakage from the garage into the living quarters.
Jeremy,
Congratulations on your air sealing work. It's always encouraging to hear a success story.
Jeremy - your house is huge compared to mine (12K cuFt total volume includes basement) and my last blower door numbers yielded 4ACH50 (starting value before air sealing: 6.75ACH50).
That number includes the basement, however we have sealed off the basement door pretty well after observing a ton of air coming to the main floor via the door to the basement. I bet if we did a blower door test with the basement door closed, we'd be less than 4ACH50.
We have a 70cfm bathroom fan, which sits in our (single) 5x7ft bathroom as well as the stove fan which claims 150cfm. We do not run either of these constantly - we use them when cooking & or using the bathroom.
I also monitor CO2. What I've found is that it's really hard to get a good average value because it's always moving if we're home. When we leave for work in the morning, the levels steadily drop. When we're home in the evening, they steadily rise. When we sleep, they shoot up. When the furnace comes on in the morning, the levels fall again (possibly because of dilution with basement or outside air from leaky ductwork).
A typical day for us(a family of 2) is a peak at 1600ppm overnight, furnace comes on, drops it to about 1200ppm by the time we wake, morning showers with the bathroom fan drop it down to around 1000ppm. Leave, come back in the evening, it'll be around 6-700ppm. By the time we sleep, back up to 11-1200ppm.
It's eye opener to me that a family of 5 with a 1.9ACH50 number needs no mechanical ventilation, but a family of 2 with a 4ACH50 number probably could benefit from mechanical ventilation. Maybe the fact that your house is almost 5 times as large really changes the 'actual required ventilation' look of things.
Jeff one thing to keep in mind is that with the volume of our home, the actual leakage at 1.9ach50 is much greater than a home with a smaller volume as yours. Thus we are leaking a much higher cfm than a house with a quarter of the volume at the same Ach50. If I remember correctly my cfm50 was about 1650 for a 1.9Ach50. At your volume if my math is correct you have about half of the actual leakage that we do at 50 pascals. When I left this morning our Co2 monitor was reading 810.
Jeremy,
I congratulate you on the work you have been doing on your house. You are correct that 1.9ACH50 for a house of your size is much greater leakage than the same number on a house half the size of yours. This is one the reasons PHIUS broke away from the PHI standards and went to a CFM measure which in now .05 CFM50/SF of conditioned space. At 52k CF, I would guess your conditioned SF is around 5k. The PHIUS standard for your house would be closer to 250 CFM.
As for the CO2 levels, I believe the bedroom levels with stay under 1000ppm with an ERV/HRV.
Btw, I love the fireplace. I have a similar setup in my current house with a Quadrafire 7100 fireplace. We are moving next year to a PH that I am designing and building and the thing I will miss the most is my Quadrafire.
You are pretty close on size Jonathan. We have about 4,650 sq/ft of living space including the finished basement. Since its a timberframe home there is no unconditioned attic space which accounts for some of the extra volume.
I would miss our fireplace as well if we didn't have it. Being able to load and clean from the outside is really nice.
Wow! that sound really good for a timberframe houses, We did not have any thermal imaging equipment, I am sure it would have been helpful, but we just did what we thought was the right thing to do, and we get a HERS Score of 49 and a ACH50 of 1.73. All of our homes are stick framed with 2x6 10' ceiling.
Thanks
This website is really helpful....
To go along with what Buzz said in #32, a blower door test is done with enough depressurization that leakage is so much more than "natural" so as to get a sense of the leakiness of the structure independently of atmospheric conditions at the time. "Natural" ACH estimated as ACH50 divided by some number between 15 and 20 is at best a crude guess of what leakage there could be under the worst atmospheric conditions, windy and bitter cold outside. When the weather is mild and nearly windless, the house won't leak much at all on its own. In such conditions, indoor air quality becomes strongly dependent on what the occupants are doing, how much they use the various exhausting devices (bath vents, dryer, range hood, etc.) and open doors and windows, and how much interior volume there is to damp out the swings in things like ppm CO2 between doing anything that ventilates the house. Clearly, the philosophy still expressed by some that "the house should be tight, but not too tight - it has to "breathe" - is a poor strategy for new construction.
I agree with the original suspicion in this thread that spending a lot post-construction to reduce air leakage below what already is a fairly decent result probably would not make economic sense. But using that as justification for avoiding the cost of an HRV or ERV, figuring that the present leakiness avoids air quality problems, is reasonable only if the living practices of the occupants do actually result in regular and sufficient ventilation. Without that, the only strategy that does make sense is that saying "build tight - ventilate right."
Dick: What- you mean to tell us that random air leakage doesn't auto-magically introduce outdoor air and vent indoor air exactly where it's needed the most, and in the right proportions? ;-)
This is an old thread, but somewhere near the bottom line: Even LEAKY houses need ventilation, and ACH/natural derived from an ACH/50 number is barely more than WAG, with huge error bars.
Yes, we understand that when a home is built to extreme tightness that we need to have away to bring in fresh air, and we do by injecting it though our A/C unit.