Air seal existing house

I recently bought a house in Northern Virginia (Zone 4). The house was built in 1982 and is all electric with heatpump.
Since moving in I have had the roof fixed/replaced (no ventilation originally and exhaust fans terminating in the attic = lots of moisture damage), replaced the bathroom fans with Broan fans that have programmable Z-wave controllers to provide continuous exhaust ventilation (and terminates outside the house with 6″ ducts), air sealed the attic, and added cellulose insulation to the attic.
Net result – roof does not leak into the house anymore, bathroom moisture (and a lot of heat in the summer) exhausts outside the house, and the draftiness in the bedrooms (2nd floor) is gone.
But I am still concernd about a couple of things relating to airsealing the siding of the house;
I pulled up some of the siding and noticed the house is wrapped in 3/8 polysio. But the very first piece of siding I moved out of the way revealed a hole in the polysio big enough to put my hand through, and secondly, that the polysio does not cover the floor joists. It basically forms the sheathing inbetween the floors. The polysio sheets are also not sealed to cover the gap inbetween sheets.
The basement is fully finished with sheetrock. With some poking in outlets and other holes I know the fiberglass bats dont fit tight and the sill is not sealed.
And then the shocker was when a couple of weeks ago I ripped out the baseboard in a bedroom to remodel and discovered a nest of stink bugs (around 50) living in the cavity behind the baseboard.
So obviously lots of holes in the building structure but I just dont know how I go about fixing it economically
As a side not I suspect the necessary strapping at the corners when polysio is used as sheathing is not present either but cannot confirm without pulling the siding.
What are my options?
GBA Detail Library
A collection of one thousand construction details organized by climate and house part
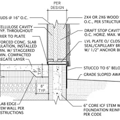
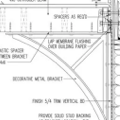
Replies
It's not clear whether the un-taped iso was a necessary part of the air barrier in the first place. If the house is sheathed in plywood with 15# felt under the iso and the didn't leave any big holes the fact that the iso wasn't detailed as an air barrier may be of little consequence.
A blower door test with infra-red imaging would tell you if you have a lot of wall leakage, but the most important air leaks to deal with are typically the band-joist/foundation sill area, and the upper floor ceiling, and any flue chases etc that might leak air from the basement directly to the attic, bypassing the conditioned space air. Stack-effect is the major infiltration driver in most homes- if you seal the top of the stack as well as the bottom you can kill more than half the infiltration losses even if there's still wall-leakage on the intervening floors. The taller the house, the bigger the stack effect.
Fiberglass batts up against a foundation wall is a bad idea from the get-go, and if they didn't air-seal the band joist & foundation sill it could sill be leaking a lot of air. In summer that air leakage could add a substantial amount of moisture to the studwall cavities. You may have to do quite a bit of the basement wall over to achieve a satisfactory result, but you'd want to put at least a half-inch (an inch is better) of XPS or EPS between the stud framing and concrete as a thermal break and minimal vapor retarder/capillary break, and put unfaced-batts in the cavities (make them fit nice too.) If the existing batts aren't moldy or full of mouse nests they can be re-used if you're on a budget and doing it DIY.. If it's moldy and/or full of bug-poop and rodent nests, chuck it.
Putting a half inch or more of XPS or EPS foam between the bottom plate of the studwall and the slab helps too- the stud stays warmer/drier, and the foam provides a bit of capillary break. With even a small amount of foam between the stud plate and any ground moisture present in the slab.
If you're keeping the ducted heat pump system, verify/rectify that they're well sealed. Use duct-mastic rather than tapes, and hit every seam & joint on metal ducts. Sealing the air-handler seams with FSK tape is a good idea too. Also seal between any register-boots and wall-board/flooring, etc with caulk or 10-part foam. "Typical" duct installations from the 1980s leak something like 25% of the total volume of air to somewhere other than intended, some more than 40%, and sealing the ducts can have a huge impact on system efficiency. (It makes them quieter too, with far less whistle & hiss.) Seal the return ducts too, no just the supplies.
Keep any eye out for any balancing issues: Doored off areas need jump-ducts or grilles etc for a return path if they don't have a dedicated return. (Deep door cuts can supply the cross section required in some instances.)
If the ducts are in the attic, above the insulation, it's something of an efficiency disaster on a couple of accounts, but I won't get into it unless you say that's the case. With any luck they're in the basement, fully within the pressure & thermal boundary of the house.
Francois,
I would investigate the area where you found the stink bugs to see if there are any signs of moisture damage. If there are, then figure out where the moisture came from; it may have come from bad window flashing above the baseboard. If there are no signs of moisture problems in that area, that's good. Get rid of the bugs and keep your fingers crossed.
Dana is correct: once you have performed air sealing in your attic, the next place to perform air sealing is at the rim joist area in the basement. Expose the rim joist and get to work.
Beyond that, it's always a good idea to get a blower-door test to find out where the big holes in your air barrier are.
Thanks for the responses!
First, the polyiso is the sheathing, there is no plywood and as far as I can tell no vapor barrier.
I guess my un-clear question from the first post is: Can I seal up the rim joists from the outside or do I need to cup open the drywall in the basement? Dana's response is very detailed and good advice about insulation and I wouldn't mind re-doing the insulation, but I would hate to cut open all the basement walls if the improvement is marginal.
The stink bugs came in at a corner of the house, so I assume there is a gap where the corner is constructed (again probably bad join between polyiso sheets). No moisture damage.
I agree on the blower door test, but my thinking was I want to seal up as many of the big/obvious holes as possible first prior to the blower test so that it can point out the less obvious "next round" of holes to fix.
Thanks again for all the helpful information!
Francois,
In theory, you can perform air sealing work from either the interior or the exterior. Only you can decide which approach is easier.
The usual way to seal a rim joist area is from the interior, using a 2-component Froth-Pak kit (a spray foam kit). However, you could do the air sealing with caulk or a high-quality European air-sealing tape from the exterior if you want -- you just wouldn't get the bonus R-value that comes with the use of spray foam.
More information on air-sealing the rim joist area: Basement Insulation — Part 2.
How about making holes in the ceiling inbetween the joists close to the outside wall and blasting the cavity with foam? I could use a snake camera to make sure the job was done right. Patching a hole would be easier than replacing big holes in the wall and ceiling.
That could end up taking a lot of foam and a lot of money. The FrothPak kits sold at box stores produce only ~1-cubic foot of 1.5lb density foam. Going more than 2" per lift with closed cell foam (evenTiger-Foam/Fomo-foam /Froth-Pak) is a fire hazard and ends up with shrinkage/adhesion issues.
If the stud bays are empty and not riddled with nail-points sticking in there are a few Michelangelos & Rafaels of the spray foam trades capable of shooting open cell foam into wall cavities from a hole large enough to get the gun into, but I wouldn't necessarily recommend that approach. (And it's certainly not a DIY job.) A safer but more expensive approach is to use non-expanding injection foam over the batts to fill in voids and seal large holes. It doesn't seal quite as well as open cell polyurethane but it'll fix most of the mid-sized holes. That's also not a DIY project.
It's not clear that a house in N.VA need a vapor barrier- it really depends on the stackup. Foil faced polyiso is highly vapor retardent on it's own, but it's at 3/8" it's pretty marginal in R-value from a dew-point protection point of view in your climate- you'll get at least some wintertime condensation on the interior face of the iso during cold snaps, but maybe not enough to end up with a springtime mold issue.
It does need something to keep the walls from racking though- if not sheathing I hope it has some cut-in diagonal bracing?
A common big hole to watch out for in 1980s construction is the missing gypsum behind bath tubs etc on exterior walls. I've seen a cellulose installer pump in 5-6x the volume that would normally go into a wall cavity when retrofitting, and ended up insulating the tub-surround and some of the floor joist space as a result. It tightened up the space, but it was hard to tell exactly where all of that insulation was ending up until it started coming out next to plumbing penetrations in the floor under the sink. (I'll bet the tub stays warm longer now! :-) )
Thx for the bad news :)
I am really worried about the bracing of the walls. I only recently realized the sheathing is polyiso. Some of the interior doors have creases in the drywall above them running upwards at a 45 degree angle. This does not necessarily mean there is an issue, but I'm still worried. How can I check?
No worries about bathtubs. None against the outside!
Dana,
My recommendation for using a two-component spray foam kit was for the rim joist area, not the whole house. I don't understand why you think this isn't a good approach. Builders do it all the time; the link I provided shows photos of Marc Rosenbaum's do-it-yourself job at his house in Massachusetts.
It's pretty routine.