Air drying Ponderosa pine

I live in SW Colorado near a sawmill that has a lot of reject 6×6 and bigger ponderosa pine posts and beams that are too warped or twisted too much to be used. Normally these are cut up for firewood but I want to slice them into 3/4″ thick end grain tiles, air dry and dimension them and use them for residential flooring. I’ll use a moisture meter of course but would like to have a rough idea of time needed for air drying before I start.
The tables and formulas for air drying pertain to flat cut lumber but being end cut I’d think the time will be a lot less. For drying they will be stacked on edge with spacing between each with stickers separating the layers. It’ll all be outside but under a metal roof to avoid direct sunlight.
GBA Detail Library
A collection of one thousand construction details organized by climate and house part
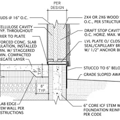
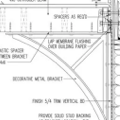
Replies
Jack,
I would imagine that these 3/4" thick slices of pine will check and split like crazy. It's hard to imagine how you can control the splitting with slices that thin.
You can always experiment. I would certainly paint the end grain on both sides (immediately after sawing) to slow down the drying process as much as possible.
Jack - This is almost certainly an experiment waiting to fail. I looked up the shrinkage of Ponderosa pine and it is nearly double that of Eastern White Pine, a fairly stable wood species that I'm familiar with and would never consider using in this application. Cutting some as an experiment and leaving them to dry over the rest of the winter will give you an idea of what they'll look like. Douglas fir, redwood, and western red cedar are considered some of the most stable, but even these would probably not do well. There is a very good reason why you don't see end grain wood tiles very often - they move too much even if very well sealed. Read up on wood shrinkage, tangential versus radial shrinkage, and the different characteristics of different species before you attempt this. The Samoset resort in Rockport. Maine has end grain wood tiles in their lobby, that I believe are Douglas fir. I imagine they were very well dried and then somehow super sealed before use. Good luck, but proceed with caution.
Jack,
I tend to agree with Martin in that it will not be easy to control the splitting. Wood that is free of heart will stand a better chance of not splitting compared to a piece that is heart centered so if the tree is big enough there is hope. You could also look at materials used to control shrinkage such as polyethylene glycol (PEG for short - just google "use of PEG for drying wood")
I wouldn't give up, but I'd cut some tiles and dry them for a few months to see what happens. I love end grain tile floors. They apparently used to be a popular floor for then of the century factories and machine shops, but Douglas Fir was the commonly used species. There are some things you will find with a Google search. Generally a wood paste is made to "grout" between tiles and fill cracked, followed by several coats of poly.
Jack - I came across this website today by chance that specializes in end grain floor tiles. It made me think that maybe your idea was not as impractical as I originally thought. http://www.kaswell.com Good luck.