Preventing Condensation in Unvented Roof with Open-Cell Spray Foam

I live in Central Alabama CZ3A new construction. I plan to open cell foam the entire house roof for an unvented attic. Our master bedroom has a cathedral ceiling with 2×8 ceiling joints/roof rafters. Shingle roof is installed over the OSB decking. Foam installer is going to fill all the 2×6 roof rafters (so 5.5″ of foam, ~R20) and I assume only fill the 2×8 bedroom ceiling rafters with 5.5″ as well according to the contract. I plan to install T&G pine as the ceiling covering.
(I understand that the R20 is not the best but building during a pandemic has wreaked my budget.)
My question is would the ~2″ of space between the foam and the T&G ceiling condensate and cause eventual rot of roof sheathing? Would an air barrier prevent this? Would properly sealed tyvek work (cheaper and easier to install than drywall)?
I am sure I could trade off filling the 2×8 cavity completely by potentially swapping to fiberglass batts in the garage walls if run out of foam because of this change order. (contracted price based on 4 sets of foam).
Thank you.
GBA Detail Library
A collection of one thousand construction details organized by climate and house part
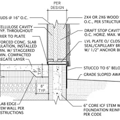
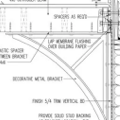
Replies
An interior side air gap isn't a problem. But do consider adding 2" more insulation (any kind) where it is easy to do so.
Open cell spray foam + sealing + ideally testing can be your air barrier. But if still possible, fully adhered underlayment is better. In zone 3A, code doesn't require a vapor retarder with open cell foam - the foam itself is a Class III.
This assembly is under insulated (well below IRC code) and the roof deck is not well protected from wintertime moisture accumulation. The 2" gap is not a problem but the high vapor permeance of open cell foam is.
This assembly won't meet code (on R-value or vapor permeance for unvented roofs), but resilience could be improved with an air barrier/vapor-retarder layer such as Intello Plus or Certainteed MemBrain between the t & g and the rest.
For(probably) less money than the 5.5" of o.c. foam one could go with interior-side Intello or MemBrain but instead of R20 foam install R30 rock wool batts, which are designed to fit in 2x8 framing. That is still R8 shy of the IRC's prescriptive R38, but a heluva lot better than R20. Detailing an OSB roof deck as an air barrier from the interior side is pretty straightforward using a bead polyurethane caulk on the seams between the rafters & OSB the full perimeter of every rafter bay, and the appropriate air sealing tapes (or mesh tape + 1/8" to 3/16" of duct mastic) on every seam between sheets of OSB.
Air leakage (more than vapor diffusion) from the interior side is the most critical risk factor, so whether foam or rock wool be meticulous about detailing the membrane-type vapor retarders as an air barrier. If the budget allows, half inch gypsum board detailed as an air barrier under the t & g would be more robust. With gypsum board as the air barrier painting it with "vapor barrier latex" would be almost as good as the membrane type vapor retarders.
Probably more expensive than R20 foam or R30 rock wool, 7.25" of dense packed cellulose (2.8lbs per cubic foot minimum. 3lbs+ is better) would deliver ~R27, and would share the wintertime moisture burden with the structural roof deck, safely storing and redistributing that moisture without loss of function. The up side to a cellulose solution is the much lower thermal diffusivity compared to foam or rock wool, which delays and lowers the peak ceiling temp during the cooling season. At lower than code R-values it's enough of a factor to make a comfort difference. The down side to an unvented cellulose ceiling is that in the event of a minor roof leak it can potentially saturate the entire rafter bay before the leak is discovered. (Self healing roofing membranes such as Grace Ice & Water Shield can mitigate against that leak risk, but you probably used something else under the shingles.)
thank you dana i had to do some research to find out why my 2 different insulation contractors quoted only R19. Turns out that this is GA code. (I live in adjacent county to GA). I looked up the GA code and R19 is allowed 'with trade off's' However I cannot seem to find what these 'trade off's' are. But I assume I meet these criteria because of these quotes I have received. (no code requirement in county I live in). However I am still kind of on the fence about this because technically I would meet the GA code. But your comment about 'a noticeable difference' obviously has me concerned because this is in our bedroom where we will spend a lot of time. Also need to consider that sun sets on opposite side from this bed room. So taking some of your advice, I will get my installation contractor to fill 7.5" joist bay and that will be R27. Before I T&G, I might add 2" rigid foam board to ceiling joists to bring up R value to R37.
Any additional comments?
Thank you for your suggestions.
As subpar as codes are in Georgia, I don't think there is any county where R-19 in the ceiling is good enough. I think you must have read the provision for insulation under the attic-located HVAC platform.
"For attic HVAC platforms, R-19 is acceptable to meet the requirements of R-30/R38 in the ceiling for up to 32 sq. ft. of attic decking per HVAC system. R-19 is also acceptable underneath a maximum 32-inch wide passage to the HVAC system. "
It looks like R-5 (impermeable) plus R-20 (air permeable) is okay if you are climate zone 3. Whatever you do, pay attention to air sealing. If you have recessed lights, consider removing them or installing low-profile LEDs.
The comfort difference is negligible, < 1/2 degree in the ceiling temperature when it's 40F or 100F outside. Turn up/down the thermostat by 1/4 degree and you will be equally comfortable.
jon, thanks is that with the 7.5 or the 5.5?
I used R37 vs R19. Comparing to R27 is about 1/4 of a degree. Base your decision on energy savings.
Thanks STeve and Jon for your advise. Steve just for your database, I did talk with the building inspector for the adjacent GA county just to get clarification on the R19/R38. R19 is acceptable for an unvented foamed attic as long as entire house envelope is also foamed. I guess this was the 'trade off' that was mentioned in the code.