Robust Insulation/Ventilation for an Unconditioned Detached Garage

I’ve built a 32×24 detached garage with huge storage space upstairs. I’ll be spraying roughly 2-3 inches of closed cell spray foam in walls and roof rafters so the building will have a nice sealed envelope. (soffits and roof ridge are NOT vented.)
My question is this: If the space is sealed/insulated, do I need to have some type of ventilation? Or maybe just a dehumidifier?
I don’t need heating or cooling because we really won’t be in the building very much.
Thanks for any advice!
btw- I’m in middle Tennessee
GBA Detail Library
A collection of one thousand construction details organized by climate and house part
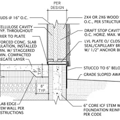
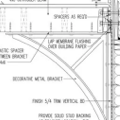
Replies
David,
if you aren't heating or cooling the building, what's the intention behind insulating it?
The insulation is really just in case we wanted to use the building as conditioned/living space at some time in the future. And the wife wants it drywalled, so now is the time to insulate.
What climate are you in?
What type of closed cell spray foam? You can dramatically reduce the high climate impact of spray foam by specifying "HFO" spray foam instead of the regular "HFC". It's better performance too.
Are you planning drywall over the spray foam? Why spray foam rather than simply fiberglass?
We're in middle tennessee. My wife wants it drywalled so I figured now would be the best time to insulate. I also wanted the spray foam to help make the building more structurally rigid.
What are you using this space for? It's a nice looking garage and spacious but you said you don't need heating or cooling so why insulate it? I have a detached garage that is uninsulated and I only considered insulating it to turn into a man cave. I plan to do it this summer but I also plan to spend time it in and heat it in winter. If you aren't heating or cooling insulation is a waste of money imho
Just in case we want to heat/cool it later on. And it's going to be drywalled so I might as well do it now.
Upstairs will just be storage space for all of our crap. Downstairs will have my workshop/tools and mower/tractor.
Controlling the interior moisture level is important. If still possible, address any bulk water issues first, such as ice, snow or rain water that melts off vehicles. I always install a floor drain in a garage to get rid of that moisture load first. You'd have to check will local codes about garage floor drains. Next, control the moisture in vapor form. A dehumidifier will work, but will add up to $60 a month to your electric bill depending on run time. I've put in a few exhaust only fans that are designed for garages. The manufacturer is out of Canada, called Humidex GVS-SD. I think they are available through Wayfair. They monitor both indoor humidity and CO and turn on if either are high. Best is a dedicated HRV/ERV, but I only see them in attached garages. Most insulated garages in my climate, climate zone 7, Northern Minnesota will stay above freezing during all but the coldest days, we are talking -20°F. Controlling moisture is very important to the durability of the structure.
Seems like a dehumidifier would be beneficial. (I put a nice one in my home's crawl space last year.) And then maybe some type of ventilation fan than operates based on preset temps?
Or would it be too wasteful or costly(monthly) to install a really efficient mini-spilt that would prevent the interior's temperature from getting to extreme?
Ventilation is a good idea for such a tightly sealed garage where I suspect you'll probably store gasoline/chemicals/solvents. I've lived in Nashville - middle TN gets really muggy from May through September. A dehumidifier to control humidity (which WILL get too high otherwise) along with an ERV for some fresh air exchange makes sense. Most garages are uninsulated and leaky and wouldn't require these things, but your CCSPF changes that. A mini-split is not a bad idea either, and if you might live in it in the future, you'll be glad you went ahead and did it ahead of time. If you do, the dehumidifier could probably be downgraded to a consumer model that would mainly come in handy during the shoulder seasons when the AC doesn't get called for very often.
In my opinion you are taking on a lot of risk and cost for almost no reward.
First let me say it I hate spray foam insulation. All the DIY TV shows have sold it as the best solution to every insulation need. Absolute nothing could be farther from the truth. Spray foam is the most expensive insulation sold. I say spray foam is the least green building product on earth and smart people should only use it when no other produce will work. The way I see it with a small amount of planning in new construction spray foam can all but be eliminated. I see spray foam on a set of plans as a big red flag look here ,this is poor planning done by someone all to quick throw your money at a problem without a thought.
I am afraid if you fill the joists with closed cell foam you will trap moisture up against the roof sheeting the moisture will condense on the nails the wood around the nails will get wet and pull away from the nail allowing the wind to blow the shingles off the roof. Fairly common problem that often goes diagnosed. People blame the roofer or the plywood and just expect to replace a few from time to time.
If you choose open cell foam you end up with almost the same R value as the cheap fluffy insulation at 4x the price.
The way I see it an unvented roof need a conditioned space to prevent moisture from accumulating.
If you do happen to finish the space some day it seems likely you will pull down lots of the drywall and insulation to secure the wall and get outlets and light switches in place.
I say make the wife happy give her the drywall and one coat of mud and nothing more.
Are you ready to live with rusty tools? Tool in unconditioned shops will rust unless coated in oil. The problem is at its worst this time of year it is cold for a few days the large heavy saw/mill gets cold the wind shifts from the south and blows warm moist air into the shop the heavy tables of your machines are now much colder than the dew point of the air in the shop and are as wet as a can of soda on a hot day. It could take days for the iron top to warm above the dew point. This will happen many days a year just not so dramatically and go unnoticed until you see the rust.
Walt