Advice on plan for exterior insulation (zone 6)

I hope GBA experts could weigh in on this plan for my home in St. Paul, MN (zone 6).
The top-down cross-section below is the current plan for adding exterior insulation to a 1976 home with existing fiberboard sheathing. I also plan to install Alpen high-efficiency windows as “innies” flashing to the WRB with the sill pan extended beyond the insulation into the rainscreen.
Some questions I have:
– Is it best to have the WRB on the Bildrite? (I believe it will be simpler and better for air sealing from the foundation to the top of the wall and considering the windows being innies and flashed to the WRB)
– Is it important that the WRB be high-perm (16 perms in this case) and NOT a vapor barrier?
– If I have a WRB such as Hydro-gap Self Adhering, which has a 1mm gap (hydrostatic pressure relief and increased drainage potential), Is it too risky to install vapor-impermeable insulation such as foil-faced poly-iso OR XPS? And if so, is EPS or Rockwool comfort board the better option? (I am concerned about the increased cost and reduced R-value of the comfort board)
– Should the seams be taped if EPS, XPS, or Polyiso is the solution?
Thank you in advance for any feedback, input, or guidance you can provide.
EDIT: I fixed the image, and I am now considering Poly-iso for the insulation layer.
Mike
GBA Detail Library
A collection of one thousand construction details organized by climate and house part
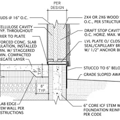
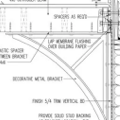
Replies
Mike,
I am not able to find the attachment you uploaded.
I can’t see any reason to avoid the no-perm insulation like polyiso. Your assembly can still dry on the outside of the WRB with the air gap you are creating. And it can dry on the outside of the polyiso (I’m assuming you’ll have furring strips or some equivalent on the outside of the rigid insulation?). The polyiso won’t care if it gets wet occasionally. You’ll lose some R-value when that happens but your cladding should prevent the majority of the water getting through.
It wouldn’t hurt to tape the seams of the polyiso to get a secondary water barrier. And taping the edges would discourage bugs from chewing through it.
Long story short, as long as your assembly can dry on both sides of the polyiso it should not be a big deal. Polyiso has a lower embodied carbon than mineral wool, for what it’s worth.
FYI they do make vapor-open polyiso. This product linked here is a fiberglass-faced board instead of foil-faced with 1.2 perms at 1 inch:
https://wall.atlasrwi.com/products/commercial/energyshield-cgf-pro/#tap-properties
You lose the radiant barrier but for your climate that is not needed.
I have seen a considerable amount of historical information that polyiso decreases in R-value at low temperatures. If so, is it still worth considering Polyiso? Is there a brand out there that solves this?
Secondly, EPS and XPS increase in R-value as it gets colder, with XPS having a higher R-value. Historically XPS blowing agents have had a higher global warming potential, but I believe that's substantially reduced with the latest versions of products like Fomular.
At this point, I might be leaning towards XPS, but there's no clear winner.
Even when "derated for cold", polyiso is typically still considered to be about R 5 per inch. That's about the same as XPS (which degrades a bit with age), and better than EPS (which is the most stable over time in terms of R value).
There is a lot of concern over the "reduced R value in the cold" issue with polyiso, but it's typically overstated, and only occurs at very low MEAN temperatures, which aren't situations you're likely to encounter in most normal applications. In a typical house, polyiso will perform at least as well as the other materials, and under most conditions, polyiso will perform better.
BTW, is there any reason for that interior side vapor BARRIER? Is it already present in an existing structure, for example? You could increase the robustness of that assembly by using a smart vapor RETARDER instead of a vapor BARRIER (which is usually polyethylene sheet).
Bill
Hi Bill,
The interior side vapor barrier is already there. Unless I see obvious issues with the Biltrite, I do not want to de-construct the wall for cost reasons.
Is there a compelling reason to source non-foil-faced or foil-faced?
As for a WRB with a small air gap at the sheathing, I have Hydro-gap specified, but could I do a smooth WRB without a gap instead? Or is there another more cost-effective way to create that small gap?
The usual reasons to go with non-foil faced polyiso is either to save money, or because you want the material to be a little more vapor open (the foil facer is what makes foil faced polyiso a vapor barrier, the polyiso insulating material itself is not a vapor barrier).
In your assembly, I would usually think the non-foil faced polyiso would be a little safer, because it would allow a little drying potential, but with the drainable house wrap that is probably moot. My guess here is that going with permeable faced (kraft or fiberglass mat) faced polyiso would offer similar drying ability to that drainable housewrap, so you could probably use the more permeable polyiso without the hydrogap layer.
Note that if you go with non-foil faced polyiso, I would advise some type of WRB be used over the polyiso.
Bill
Arguably, the drainage gap behind the polyiso is not necessary at all. It’s a good idea, to be sure, but even Matt Risinger doesn’t have an air gap on the back of his polyiso on his own personal house. He attached the polyiso directly to his Zip WRB. See below video. There is another video where he pours a water bottle of red dyed water behind the insulation against the Zip WRB and says something to the extent of “it has good enough drainage”, but I couldn’t find that exact video.
https://m.youtube.com/watch?v=IDFSnjuNl5U&pp=ygUvTWF0dCByaXNvbmdlciBkcnlpbmcgYmVoaW5kIGV4dGVyaW9yIGluc3VsYXRpb24%3D
Matt Risinger's wall can dry to the inside, and Austin is a warm climate, so that will be the vapor drive direction most of the time (outside to inside). And with Matt Risinger's wall, one could argue he has increased the risk of the wall by adding an impermeable layer. However, he did everything else correctly, has a rain screen, and will probably never have a problem. His argument of pouring water down the wall on his WRB shows bulk water shedding, but not necessarily something inside the wall wetting the framing and then trying to dry in a vapor process. In my case, already having an interior vapor barrier means I have to mostly dry outwards, and if I put another impermeable layer, I am potentially creating an impermeable sandwich. Thus, if my reasoning is correct, I want an un-faced poly-iso, followed by another WRB at the rainscreen to prevent absorption of water that may enter the rainscreen (rare). It's more materials and labor to add another WRB, and I wish I didn't need the additional WRB.
Also, I am considering not doing Hydrogap SA but Grace enV-s SA since I can source it for 1/2 the price.
so...
Looking at the Atlas EnergySield CGF poly-iso spec sheet, I am not convinced I need another WRB at the rainscreen.
"Atlas EnergyShield CGF combines high R-value, enhanced durability from two coated glass-mat facers, and water resistive attributes in a high performance rigid Wall insulation. "
https://wall.atlasrwi.com/products/residentiallight-commercial/energyshield-cgf/#tab-thermal-value
In fact, Atlas CGF provides a link showing no WRB with taped seams:
https://www.atlasrwi.com/resource-folder/wall/Illustration%20Details/Wood_Frame_ES_CGF_Insulated_Sheathing_&_WRB_Furring_Siding-IllustrationDetails.pdf
Matthew25,
Hydor-gap is fairly permeable, but is really marketed as providing a drainage plane to remove bulk water intrusions from the outside. Being only 1 mm deep, I wonder how much drying to the exterior you would get with impermeable foam? Put another way: what's the mechanism that moves any interior moisture through the sheathing and WRB, and out of the cavity?
Deleted
Mike,
I would encourage you to avoid XPS. Not only is it the worse option for exterior rigid foam in terms of lifecycle carbon costs, it also has a mediocre R-value. The initial value is around R-4.7/inch but it drops to R-4.3/inch relatively soon (see below references). Polyiso has a manufacturer-stated long-term R-value of about R-6.0/inch at standard conditions but it is dependent on the average temperature across the insulation. The NRCA has deemed the LTTR of polyiso to be closer to R-5.5/inch, but that is still better than XPS.
Some quick googling tells me the yearly average temperature in St. Paul is about 46 degF, and assuming an indoor setpoint temperature of 75 degF the apparent R-value for the polyiso will be about R-5.5/inch. Even the R-value in the coldest months (average temperature of 10 degF) will be about R-5.3/inch. In pretty much any weather scenario, the polyiso will have a higher effective R-value than the long-term thermal resistance of XPS. See Figure 3 on page 4 of the BSC article for the plots of 2" polyiso samples I am referencing.
XPS LTTR Reference: https://www.greenbuildingadvisor.com/article/thermal-drift-of-polyiso-and-xps
Polyiso LTTR Reference: https://buildingscience.com/sites/default/files/migrate/pdf/BSCInfo_502r_Temperature_Dependence_R-Values.pdf
St. Paul, MN Temperature reference: https://weatherspark.com/y/10422/Average-Weather-in-Saint-Paul-Minnesota-United-States-Year-Round
Thanks for the great information.
Regarding XPS, I see this Foamular product is advertised as R 5.0 LTTR @75F and R5.6 at 25F.
https://dcpd6wotaa0mb.cloudfront.net/mdms/dms/EIS/43522/43522-FOAMULAR-250-XPS-Insulation-Product-Data-Sheet.pdf?v=1664703006000
I wonder if this XPS product is doing something unique? Is there a particular Polyiso brand recommended for low temp?
Unfortunately the BSC article does not list the manufacturers they tested, or at least I can't seem to find it if they do.
XPS does tend to increase R-value with decreasing temperatures, which is an advantage. But I wouldn't use their 25 degF mean temperature as your baseline, because that would not be the mean temperature for the vast majority of the year. If 46 degF is the average outdoor temperature and 75 degF is your indoor setpoint, you are looking at a yearly average mean temperature across the insulation of 61 degF. I think your effective R-value with XPS will be somewhere between 5 and 5.4 per inch. Polyiso will be R-5.3/inch even at your lowest historical monthly averages. And slightly better than that for most of the year.
I would like to point out that the environmental product declaration page for the NGX product (see link below, page 17, table 9) still shows a GWP of 9.59 kg CO2e for the standard measured size of 1m^2 @ RSI-1. This number includes categories A1-A3, A5 and B1 which basically encompasses the manufacturing of the product, the installation of the product, and the "use", or off-gassing over time. Compare that to the Efficiency Vermont article linked below and you will see on the table in page 8 that the average of the polyiso samples they reviewed have a GWP for the same categories of only 2.32 kg CO2e. So even the newest generation of XPS is approximately 4 times worse than polyiso in terms of embodied carbon.
Unless there is a significant cost savings in your area, I don't understand the desire to switch to XPS. You will have drainage on both sides of this insulation already so vapor permeance shouldn't be a concern. And the Atlas GCF product I mentioned earlier has about the same perm rating as NGX (1.2 vs 1.5 perms at 1 inch) if that's what you're worried about.
NGX EPD: https://dcpd6wotaa0mb.cloudfront.net/mdms/dms/Shared/10024576/FOAMULAR-NGX-XPS-Insulation-EPD_UL_corrected.pdf?v=1646664386000
Efficiency Vermont GHG Article: https://www.efficiencyvermont.com/Media/Default/docs/white-papers/20210122-GHG-RNC-final-report.pdf
Polyiso will never have an r value lower than XPS, at any real temperature. Otherwise it will always be higher.
Deleted
Based on this information, it looks like Polyiso is better. The costs between Polyiso and XPS in my area are almost equivalent. Given the decreased global warming potential of Polyiso vs. XPS (which I care strongly about) and the slight R-value improvement over XPS, Polyiso is now the front-runner.
Is there a compelling reason to source non-foil-faced or foil-faced? I see that some foil-faced Polyiso panels are structurally rated, which I am intrigued by, to add some shear strength to my home, given my home currently has fiberboard sheathing. However, non-foil-faced poly-iso has some drying potential but still low perms.
Before this is more than a plan on paper do a budget and an energy model. It seems impossible to me that you could live long enough for this project to make economic sense given its high costs and low saving.
Walta
It is a great point to consider. Why do this? For me, it is about maximizing the comfort and health of the home. Cost is a factor, but ROI from energy bills is not the #1 priority. With this exterior remodel, there are aspects that I will do no matter what, including new windows, siding, and adding a WRB. The existing 1970s windows and 2x4 framing makes for an uncomfortable home. So the incremental cost to add more insulation, air sealing, and comfort to a 1970s home is a small percentage of the overall project. So far, I am looking at a ~15% increase in the overall project to add a high-performance WRB and continuous insulation. I expect this will add 100 years to the life of the structure and comfort and energy savings during that duration.
Some rough numbers from manual J HVAC calculations I have done. I am reducing my 44kbtu heating load down to 22-24kbtu. With a heat pump, that equates to about a 30-40% reduction in total home electricity costs associated with my heat pump and the ability to downsize the equipment size in the future for additional savings on equipment when it needs to be replaced. Roughly converting that to energy savings is about $850-1000/yr. So for the insulation upgrades, the ROI is about 10-15 years with current energy rates. As a side note, less solar is needed on my roof for the future offset of my usage. So savings from an energy ROI standpoint are not as significant. Still, the comfort factor will be large in Minnesota, and the overall wall R-value will align with current local codes. No more cold air drafts in the winter, windows iced up, cold drafts, and uncontrollable humidity issues.