Advice on Insulating (partially or not?) Basement Walls in 1982 Home. Please help?

RastaCook
| Posted in General Questions on
I’m renovating the basement of my 1982 house in Quebec (canada), which I believe is zone 6a. We had a flood (sewer backup) and had to remove flooring and cut bottom of the walls.
The foundation walls are poured concrete and there is nothing on the exterior (no membrane or insulation).
Due to the layout of my basement and stairs position, in many cases I will only have 2 inches of space behind my gypsum drywall. I cannot change this, the wall framing is already built (using metal studs) and even if we wanted to redo the framing there would still be problematic areas where we would have to limit ourselves to this 2in space unless we start doing some really major/expensive adjustments like relocating the stairs etc.
The current wall assembly is as follow :
Concrete Wall > 2in White Styrofoam > Clear Poly plastic vapor/air barrier > Gypsum drywall panels.
Note that the white Styrofoam is only installed in the TOP 3-4 feet of the concrete wall, there is nothing bellow (but the clear plastic poly does cover the whole height of wall)
The wall framing is built with metal studs and they are installed with the “4in” side facing the concrete, there is not a lot of space behind the studs, maybe 0.25-0.5in more or less I think.
I am not sure what should be done.
Different contractors have suggested different things but they seems to generally just recommend what they usually do, which may or may not necessarily be whats best for my situation.
Many contractor suggested spray foam, 2in spray foam could be as much as R14, its easy and fast to apply, etc… I did some research and there seem to be 3 issues with this, first it would seal the concrete from the inside, which would drive the moisture up the concrete wall into the floor sill plate creating rot / mold overtime (in most cases around my foundation, the sill doesnt have a lot of clearance or exposure to sun). Second, apparently its relatively common for the chemicals to not always mix properly and there is a risk that they would off-gaz for many months (years?) and this could be a hazard, especially since we spend a lot of time in the basement. Third, the expanding foam could bend the metal studs.
Another contractor says its not worth to change what I have and that I should keep the bottom 2 to 4 feet empty behind the gypsum walls, just like it is now, this gives some airspace and reduce risk of moisture being trapped in tight space, he says if we put foam boards all the way down against the concrete and cover with plastic membrane and gypsum, it will trap moisture. He says if I want slightly better insulation, we could replace the white styrofoam at the top with 2in xps and instead of just the top 3-4 feet we could go down to 5.5 feet to fill the wall a bit more but he strongly recommend NOT going all the way down. Even if we do this, he says its not going to make a huge difference in comfort / heating, so its not really worth it.
What should I do? Whats the best option when you only have 2in behind drywall? Although we do spend a lot of time in the basement (home office + kids play room), I dont mind cranking up the heat if/when necessary, my priority is simply not to do anything that would cause condensation / mold / rotting issues…
Really appreciate any input,
Thanks
GBA Detail Library
A collection of one thousand construction details organized by climate and house part
Search and download construction details
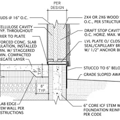
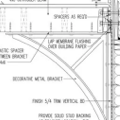
Replies
Do you have any moisture problems with that wall now? The simple way to test for this is to tape a piece of poly over the concrete somewhere and watch for moisture to appear over time behind the poly.
You might have a capillary break at the top of the wall, which will greatly reduce the potential for moisture/rot issues for the wood framing if you do. I would check for this. Sometimes you'll have a "sill seal" gasket (often pink foam-like plastic that feels almost like packaging material), which will serve just fine as a capillary break. If you have something in place there that will work, you have less to worry about in terms of what you do to the rest of the wall.
EPS ("white styrofoam"), IF UNFACED, is more vapor open than XPS. If you were to add more rigid foam, I would stick with EPS and not use XPS. If you have to use XPS for some reason, I'd use that in the lower part of the wall and leave the EPS in the upper part of the wall to keep a small amount of drying ability up there to help with moisture wicking if that's a concern. I don't think it will make a whole lot of difference either way though -- you really want a capillary break regardless. I don't see a problem going all the way down with either type of insulation.
Spray foam would work, but the stud bowing concern might be an issue. I think the spray foam would probably expand around the studs and not push them out much, if at all, but I can't say for sure without seeing the wall assembly, and it's difficult to predict with certainty anyway. The "chemicals don't mix right" issue is overblown. What you have is the potential for a very bad problem to occur, and people that have that problem talk about it. The vast majority of projects go fine, and no one complains. The result is that you see more people complaining than not, which skews peoples perspective in regards to the liklihood of the problem occuring. All that said though, my preference would be to use rigid foam panels here and not spray foam.
2" EPS is going to get you around R8.4-R10 or so, depending on the density of the material. You can bump that up a bit using GPS (EPS with graphite mixed in, which has a gray-ish appearance), but that stuff is more expensive and much less readily available. I'd probably just stay with 2" EPS against the entirety of the wall, unless there is enough of a moisture issue to really be a problem, which I doubt is the case here.
Bill
Thanks for the input.
I dont have any access anywhere to see if there is a capillary break, not sure if its possible to see this from the outside somehow but the ceilings in my basement are all closed so cant see from the inside... I assume that I dont since its an older house. It would be really nice if I do as I think in theory spray foam would really be the best option, but the potential downside were a bit worrying (off-gas + rotting, less the stud bending as I guess they could be braced or if done by someone experienced they can do it carefully)...
My neighbour said that their contractor put a Delta-MS dimpled membrane all around the interior foundation walls and then spray foamed, they say this leaves an air gap between the foam and foundation... Not sure if this is a good idea and if could work to prevent rotting of the sill framing... I think the thickness of the membrane is about 5/16" so in the raised area it would reduce the maximum thickness of the spray foam but overall there would still be at least 1.5in thick.
Aside from that, I dont know how much of a moisture problem I have if any... Some observations:
1. Not sure how relevant this is regarding the walls, but I know there is some water under the slab floor. I can see this because there is a square hole in the concrete where there is the acces to the main drain cleanout and the hole goes through the whole thickness of the slab, there are drainage rocks at the bottom of the hole and I can see some water there. Contractors have told me this isnt ideal, but, its very common, it could indicate that the french drain isnt performing well. Redoing the french drain is not an option, but we may we want to add a sump pump that would capture ground water and expel it outside. I did lay down a clear 18x18in plastic on the concrete floor for a few weeks now and it has never been humid behind the plastic even though I know there is some water under the slab at least in 1 area where the main drain access is...
2. If I look at the BOTTOM of the concrete walls, In some areas I do see a little bit of efflorescence... I dont know if this is from a while back or what, the walls have only been open for the last 3 months... when I moved into this house 5 years ago, I installed pavers in the backyard which almost go up against the backyard foundation wall, these pavers are slightly graded away from the house, I also extended the gutters so they drain on the sloped driveway away from the house... Previously the backyard had negative slope towards the house and the gutters were dumping water directly at the corner/side of the house foundations.
3. When I moved in, I think the basement was a bit humid, not necessarily because it felt or smelled very humid but because I noticed bugs regularly (pill bugs and centipedes)... I setup a dehumidifier and this helped greatly, I also properly sealed the windows (there are 3 windows in the basement that are all original 1982 aluminum windows with wooden frame, they were not really maintained, part of their wood framing had rotten and they were just not airtight at all, I added caulking and filled the frame, the windows were in window wells but the top of the window well was open and the gravel at the bottom was reaching the bottom of the window, so rain would it the wood frame and it would also get rain splash from hitting the bottom gravel. I replaced the window wells for bigger ones, dug down deeper in the window well to leave at least 2in between bottom of window and gravel, and I also put a window well cover). I think all these things reduced humidity greatly, I never see any pill bugs anymore since a long time and centipedes I do see but its been gradually declining and its pretty very rare now (once every 3 to 6 months).
Dimple mat is usually used when you have bulk water problems (water seeping through the walls during storms typically). This works best when you have an internal perimeter drain at the bottom of the wall where the dimple mat can drain to. My gut feel is that the dimple mat does help to limit moisture wicking up to the sill plate, but I've never done any formal testing on that and I haven't read anything from anyone who has, either. I can't say for certain if dimple mat will help with your moisture concern, but it won't hurt. you would have an issue though with the spray foam pulling away from the wall if you use dimple mat, and that includes between studs where the weight of the spray foam before it cures will pull the dimple mat away from the wall resulting in a thinner than expected layer of spray foam. You'd need to secure the dimple mat somehow which I think would be difficult to do well.
My guess based on what you've said is that any bulk water issues you've had were solved when you regraded the exterior to drain way from the house. That probably means you won't have any significant water issues to deal with. I think you're safe to insulate the entirety of the wall. I would NOT be concerned with moisture in regards to insulating the entirety of the wall, I would ONLY be concerned about bulk water issues, which don't seem to apply in your case. The sill plate is a bit of a concern, but if your "poly on the concrete" tests haven't shown moisture, you're probably OK here too.
I would probably just put EPS against the entire wall and not worry about it.
Bill
thanks again for the input.
Would you put plastic over the eps foam before putting the drywall board back?
The test i did was on the floor and I must say also there hasn't been particularly a ton rain ever since AND the whole concrete floor is open (no flooring installed yet), AND I do have a dehumidifier running (as always) in the basement so, I suspect that this is a test in best case scenario which wouldn't necessarily tell me much aside that in best case scenario there is no moisture problem... perhaps I can try to cover a much larger area and also turn off the dehumidifier to see, but we are now getting in a much colder period late october so, not sure if that could also be a factor (less humidity in colder months?).
I don't think the poly is really necassary, but it shouldn't hurt if used this way. The general thinking is that if you get mold growing on a moist foundation wall behind the insulation, if the insulation is rigid foam, the mold is effectively encapsulated, so the mold can't really hurt you. The EPS won't pass enough moisture (assuming 2" thickness here) to be an issue for the rest of the assembly. You do need to be careful about airsealing that insulation though, and the poly might help with that.
If the metal studs go all the way back to the masonry (as DC was thinking), that's a problem -- they are thermally conductive, which negates some of your insulation, and they're probably going to rot out from moisture at some point too. I had thought the metal studs were just on top of the insulation, with the EPS as a continuous, unbroken, layer of foam against the wall. You want that continuous insulation without any studs poking through it.
Bill
For some reason, I cant reply to your latest comment bellow, so am answering here again.
Basically yes the metal studs are not behind the current eps foam but rather in between (looks like maybe they embedded the studs inside the foam, like pressing it against the foam or maybe they cut around the foam, hard to tell with what I can see), the studs are not touching the foundation though, there is maybe 0.5in to 1in gap between the studs and the foundation.
I do notice a FEW of the metal stud have a little bit of rust near the bottom but it seems minimal and its not affecting all studs.
I assume that getting a really good seal with the EPS foam will be tricky and it would probably be easier to do a good job using spray foam as it can get behind the studs, but I am not sure about the risks related to spray foam (rotting of sill, off gassing and potential bending of metal studs).
I've also found out about smart barriers, they allow moisture to go through depending on humidity level or temperature, so it doesnt trap moisture and would allow better drying, but not sure if this would be helpful in my situation and if it should be against the foundation or rather just behind the drywall (i think that would be easier to install and maybe more uselful, so that concrete moisture when it is low remains behind the wall without risk of molding, but if it gets too high would pass through and be allowed to dry through the wall, but not sure if its a risk to the drywall paper backing to start molding...)
Gosh, I never thought renovating the basement would turn out to be so complex.
I don't think smart vapor retarders are an option for you here. Those are used in regular above-grade walls, where they can help to control moisture within the walls. Regular walls don't have constant SOURCES of moisture though, and your foundation wall is basically a constant source. I'd stick with regular poly here.
It's easy to seal EPS. With the denser grades, you can use tape, similar to that used for crawslspace encapsulation (i.e. wide and good adhesion to this sort of material). I've usually just used canned foam myself -- I leave a 1/4" or so gap between insulation panels, then I inject canned foam into the gap as a last step. The cannedfoam fills the gap and adheres to the EPS, giving you a nice air seal -- even with an irregular surface like some dings and dents in the edge of the sheet.
It would be better if your studs were further off of the wall. Steel studs are much worse than wood in terms of thermal bridging. The "little bit of rust" probably isn't a big deal as long as it's not eating into the stud too much. You could always put a coat of Rust Oleum's "Rusty Metal Primer" (the brown stuff) on the studs as a protectant in any problem areas.
Bill
thanks again... I'm really not sure about the plastic... It seems the traditionnal common thing people recommend is to use plastic vapor barrier, but then I can also find "experts?" that are completely against it, so, not sure which way to go.
For example :
https://youtu.be/QnFoiUXr4h4?si=I7VGS1F2sxRELyAK
https://www.youtube.com/watch?v=ERwWTC4pnQo&t=84s&ab_channel=CrewcutTV
these are just 2 examples and overall i do see there are way more people recommending there should be plastic behind the drywall, but, both option seem to make sense so, im not sure...?
You'll find people out there saying the wall "needs to dry to the interior". That's a carryover from above ground walls -- regular studwalls -- that DO generally need to dry in one direction or the other (or both). The difference is that wood rots, so moisture is a problem for the studwall, but concrete doesn't care if it's wet, so moisture with a typical concrete foundation wall doesn't matter. Remember that they build hydroelectric dams out of concrete, and the concrete obviously doesn't have any problem being wet all the time there!
Poly against the wall isn't going to hurt anything in terms of moisture. What you CAN sometimes find is that mold will grow between the poly and the concrete. That mold is encapsulated by the poly though, so it can't release spores into the living space, making it much less of an issue. With a fully adhered layer like spray foam, there isn't even anywhere for mold to grow.
The other reason to use polyethylene sheet is to keep moisture from the foundation wall out of the studwall. That means you need a VAPOR BARRIER, but it doesn't have to be POLYETHYLENE SHEET. 2" EPS here has a low enough moisture permeability to act as a vapor barrier, so it can do double duty. Adding the poly won't hurt anything, but isn't required either.
I think you're starting to overthink this a little with information overload. The common way to insulate basement walls is with rigid foam, and it's proven to work reliably. I would just keep using EPS and not worry about it, you should be fine.
Bill
What you really don't want to do is have the plastic -- or any vapor barrier -- right behind the drywall. You need to have a vapor barrier against the concrete, but you want any moisture that gets into the wall to be able to escape, and the only way it can escape is to the interior. This is particularly true if the wall includes permeable insulation like fiberglass batts.
With polyethylene plastic over the entire wall, you currently have no inward drying anyway, so adding more foam won't make any difference. It may be worthwhile to pull off a piece of siding or cut a hole in the ceiling to check the moisture content of the sill and rim board.
Indeed, it doesn't go through the plastic, but there is a lot of air space so perhaps this helps, at least that's what some contractors have said and it's why some said to leave the bottom empty...
Even if I could see the sill and it would look dry, I don't know if this will remain the case after putting spray foam for example... Right now from the inside there is a trap on the ceiling to access a shut off valve for the outdoor hose bib, if I look in there, I can see the sill board (iat the end of 2 parallel joists) and it looks ok, but I can't see if there is anything between the board and the concrete, the view is obstructed for the bottom...
A small volume of air can only hold a very minuscule amount of water. And once that small volume of air is saturated, there is no more drying. You only get drying when the saturated air at the wall surface is being continuously replaced by dry air.
I'm going to be a bit of a Contrarian here and say the only way you want that concrete drying is to the outside on the small bit that's above ground. The poly sheeting that's there now is good, you want to prevent any moisture in the soil from entering your living space. Moisture doesn't harm concrete. Moisture might harm your sill plates, if they're not treated and there's no capillary break. But if you've gone 40 years that may not be an issue. Certainly insulating the basement is not going to make it worse.
I'm a little puzzled at the advice not to insulate the bottom of the wall. Any indication as to what they're afraid of?
I fear that the existing insulation is not too effective. Steel is highly conductive, the steel studs give a parallel heat path that largely negates the insulation.
Thanks for your input.
They are afraid that if the insulation goes all the way to the bottom, it will create moisture issues, that's why they strongly recommend I leave 2 feet with nothing... Either that or they say I have to redo the whole basement wall framing so there is more space to properly insulate then they can go all the way to the bottom, but in some area we would still be stuck with 2in space.
I think maybe the previous owner used steel stud because it's a basement and he wanted to minimize any organic material, especially since he put them so close to the concrete wall... Maybe he had moisture issue at some point and redid the place with steel stud idk...
Anyways, so in your opinion I should do what? Keep the rigid foam panels I have at the top and just cover the rest of walls all the way down with rigid foam? The space behind the studs I don't think is big enough to slide foam panels, we could maybe use cans of spray foam maybe to shoot behind or leave empty (not sure if spray foam behind the stud would bend the studs).... Or instead of foam panels just remove the current top panels and spray foam from top to bottom 2in thick but I assume this wouldn't completely fill behind studs...
I'm thinking take the wall drywall off and put a 2" layer of foam over the studs, then put the drywall back with 2-1/2" screws. Any outlets in the wall have to be moved out 2".
In a 1982 house I would worry about how the joist bays were treated. They can be a major source of air leakage and if not done properly can contribute a lot of condensation. You'd probably have to peel the ceiling back at least a foot but if you're redoing all the walls a little more drywall isn't a big deal. Drywall is cheap.