Advice on double stud wall retrofit

I am planning to retrofit double stud walls in about 40% of my house.
I have detailed what I plan to do here (in great detail):
http://netzeroenergy.org/walls.php
That’s my site, my plan is to document in detail my energy upgrades to help others and thus get a multiplying effect. If you have improvements for that page I can be reached at mark at netzeroenergy.org . I’ve already got to net-negative, but I’m not changing the domain name!
On the upper floor I will remove the existing ugly thin-as-paper wooden panel board. On the lower floor I have existing sheetrock walls, and prefer not to remove the existing sheetrock.
——
So here are my questions:
Q1: Where I have existing sheet rock walls, what’s my best strategy … make 2″ holes in the sheet rock so I can damage the kraft paper to avoid having two vapor retarders, or remove the sheetrock?
Removing the sheetrock is more mess and waste and loss of thermal mass. If removed it maybe I could use it as a backing for the new sheetrock (i.e. double thickness), that’s if I can remove it in large pieces.
Another reason to remove the sheetrock and dispose of it, is that it likely has latex paint on it that will be a slight vapor retarder. What are your thoughts?
Q2:
My preferences for the inner rigid foam board are:
2″ fiber faced or unfaced polyisocyanurate (if I can get it), or 2″ XPS or 2″ foil faced polyiso.
If I cannot get the fiber faced polyiso locally, which do you think is best, 2″ XPS or 2″ foil faced polyiso? (The former being a vapor retarder but R10, the later being a vapor barrier but R13)
Q3:
I might be able to get fiber faced polyiso that is intended for roof construction. Is there any reason you know of not to use it in a wall?
Q4:
What do you think to my idea of cutting the floor boards to air seal and insulate the void below the new inner wall? (See web link last section. The current floor surface will be replaced with cork planks).
Q5:
I have old base boards around the existing wall. So I’m going to rip them out. I’ve upgraded to geothermal forced air heating. I could cap the copper pipes and even insulate them, for possible future use, but am I wasting my time capping and/or insulating since I have no plans for them? Alternatively I could cut the copper pipe out and recycle the copper? (See last picture in web page for suspected location of pipes)
Q6:
Any suggestions for that web page email mark at netzeroenergy.org
Answers to any of these questions will be appreciated.
– Mark
GBA Detail Library
A collection of one thousand construction details organized by climate and house part
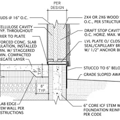
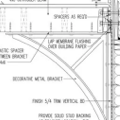
Replies
I received this from Robert Riversong (along with web page suggestions):
There are statements reflecting significant misunderstandings about vapor permeance and condensation plain as well as vapor diffusion driving forces.
So is there something I am missing here?
1) Remove the existing DW in order to remove the existing vapor retarder. Thermal mass interior to the thermal envelope will offer almost no advantage. Latex paint (unless it's labeled a vapor retarder) is vapor semi-permeable (perm 3.5-6).
2) I would not place a vapor barrier in the middle of a retrofit wall, particularly since AirKrete does not list a perm rating. I would want to maximize drying potential in both directions. Use XPS if you must use foam. Better yet, fill both interior stud and thermal break cavities with dense-pack cellulose.
4) Good idea, but you'll also have to insulate and seal the gable ends of the floor (parallel to joists) and add support for the interior wall with blocking.
5) You mean baseboard radiators, not baseboards. Yes, remove piping (it will conduct heat) and recycle the copper.
Also, to determine condensation potential in your double-stud wall, you need to independently analyze the cross-sections that include framing, particularly where two studs line up (such as at window openings).
I would suggest keeping your vapor retarder (1 perm is good - no poly or foil) and air barrier at the inside plane of the wall system (airtight drywall).
My comment (which you quoted above) was in reference to your website statement that "The condensation plain (if I understand it correctly) will be the first surface (moving warm to cold) at which air movement is retarded and the temperature is below the air dew point." A condensation plane is a relatively vapor-impermeable surface that is below the dew point. Air movement is a different problem.
And your statement that: "excess water will leave via the path of least resistance" ignores the fact that moisture will move only if there is a driving force - such as temperature gradient, concentration gradient, pressure gradient, gravity gradient, momentum gradient or surface tension gradient. Otherwise, what's wet remains wet. Hence maximizing drying potential is at least as important as minimizing moisture intrusion, and moisture storage (buffering) capacity allows a time lag between wetting and drying without doing damage.
Robert, thanks for the detailed answers.
I will reconsider using dense pack cellulose for the interior including thermal break. The disadvantages to me of using cellulose are, loss of about R3 compared with 2" XPS, needing to install a separate vapor retarder. Also I would prefer to complete one room at a time, which means renting the cellulose machine multiple times, and any mess cleanup multiple times, but I may be able to deal with this.
I thought that it was generally considered a good idea to have more thermal mass on the inside of the thermal envelope to behave as a thermal buffer. I've seen on popular TV (Renovation Nation) an architect boasting about the total weight of 5/8 sheet rock installed. But you say it will offer almost no advantage. Am I confusing this with passive house design?
Do you think that making the 2" holes in the existing sheet rock is an inadequate solution to wreck the existing vapor retarder?
(In this case the thermal mass would be left in the center of the wall)
You can always make up in thickness of cellulose what you'd lose in R-value by eliminating the rigid foam - just add an inch to the wall system. You don't need, nor want, any separate vapor barrier membrane when using cellulose. To comply with the code, use latex vapor retarder primer (approx 1 perm).
In regard to themal mass, I was refering to the alleged advantage of leaving the DW in the middle of the thermal envelope. To be effective, themal mass should be contiguous with the conditioned space.
The 2" holes might be adequate if the AirKrete is vapor permeable, but since they don't disclose the perm rating it would be better not to leave even a holy semi-impermeable layer in the center of the wall. If the AirKrete is well-installed, it will help in air-sealing the wall system, but I would still use an interior air barrier and seal all penetrations.
Which reminds me: on your website you spoke of sealing with foam around electrical box "extensions". You wont' be able to extend electrical boxes 6" - they'll have to be moved (if you can dislodge the wiring from the AirKrete), and sealing the box edges does little if the many holes typical in metal or plastic wall boxes are not sealed. I use Lessco polypans behind all outlet boxes in insulated walls and ceilings and Tremco acoustical caulk to seal the DW to the flanges.
I called the Air Krete manufacturer they haven't had a vapor perm test done. However, they thought it should be significantly more permeable than stuco which has a perm of about 4. It is effectively an ultra light weight aerated cement, so light it crumbles to the touch. Given that the Air Krete is mixed in with thin fiberglass I think that's a total perm of about 0.5 for the existing wall minus sheetrock but including sheathing (1" tongue and groove). So I probably can use the 2" hole idea.
However, given the amount of mess there will be anyway, removing the sheet rock sounds better than my 2" hole idea, and it will make removing electrical boxes much easier.
Bummer about not being able to extend the electrical boxes, thanks a lot for pointing that out!
Another advantage to dense pack is being able to fish wires along the thermal break if ever needed in future. Although using 2x3 lumber for the inner wall would also make that possible with rigid foam and bats.
QUESTION:
Since you mentioned code conformance. Does my idea with the foam board (assuming XPS or fiber faced polyiso) in the thermal break comply with code to your knowledge?
There should be no code issue with an internal foam thermal break (though the best person to ask is always your local code official).
I wouldn't trust a guess on AirKrete's permeability, but how do you figure 0.5 perm for as-is wall assembly? And are you telling me that the AirKrete will crumble if you try to remove existing wiring and boxes from it (I've heard that if it's improperly mixed during application, it can crumble to dust on its own)?
The difficulty in doing such renovations is one of many reasons that I avoid foamed-in-place insulations of any type.
The nature of Air Krete is that once set if you poke your finger in it, there will be a finger sized hole and some dust, it will not expand or flex to fill the hole. So where I remove a wire there will be a wire sized hole, which I can maybe fill with spray foam but I would have to test first. Fishing new wires through Air Krete would severely damage it.
I actually have a number of blocks or Air Krete in my garage, and a sort of sale's man's 3'x3' section of a stud wall with Air Krete, and a stud bay in my garage with fiberglass and Air Krete behind some plexiglass (just like my walls have). So I have plenty of test samples. The Air Krete behind the plexiglass has not settled (not that I would expect it to), and looks to have air sealed the bay well. But would risk getting damaged if I removed the plexiglass.
That was actually another reason why I originally wanted to leave the sheetrock in place, because I didn't want to damage the Air Krete while removing the sheetrock. If it looks like I'm going to damage the Air Krete, I'll fall back to my idea of making 2" holes in the sheetrock.
I guessed a perm of about 0.5 for the existing wall (minus sheetrock) i.e. 3" of Air Krete and 1" of tongue and grove. As I understand it there is roughly a reciprocal relationship so 3" of perm 1 gives roughly 0.33. So 3" of perm 4 gives perm 1 for cavity, plus another perm 1 for wood gives perm 0.5. I used perm 4 because that's what stuco is, and Air Krete is also cement based, but it is a guess. When you have touched and felt Air Krete is it hard to imagine it blocking water vapor, there are a lot of tiny air spaces in it.