Cost-Effective Better-than-Code-Minimum Roof and Wall Assemblies

Hi,
Renovating/expanding a colonial in CT. Trying to get a much better than Code house for reasonable cost. Proposed wall assembly: sheetrock, 2×6 studs with R23 Rockwool, 1/2″ plywood, Henry Blueskin VP100, 2″ polyiso, 2″ eps, tyvek, vinyl siding. 1) Would easiest framing be a 2×8 pt sill plate with 2″ foam overhang? 2.) Is HBVP100 overkill/unnecessary on the sheathing? 3) Would building the house without eaves and rakes to attain a better air seal (added back after seal and before 2nd layer of foam) be more costly that traditional overhangs?
Roof: sheetrock, R38 Rockwool, 5/8 plywood, HBVP100, 4″ poly iso, 2″ eps, 1/2 plywood, underlayment, asphalt shingles. Is there a more cost effective way to get continuous insulation on the roof in my zone?
Welcome recommendations for contractors familiar with exterior insulation in my area: 06878
Thanks very much.
Andy
GBA Detail Library
A collection of one thousand construction details organized by climate and house part
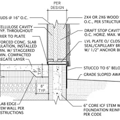
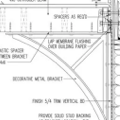
Replies
Andy,
I would vote to skip the VP100 on the plywood and use tyvek here as well, taping the seams of the plywood with something like zip tape or the 3m 8067.. The VP100 and tyvek have similar perm ratings, but the VP100 costs about 5x more, and really isn't easier to install. It's also recommended to use their aquatec primer first, which is another step in the installation that i think a lot of people skim over, that's extra time and money too. The polyiso will be vapor impermeable as it is, so the permeability of the WRB is somewhat of a moot. A good install will have it being a good air barrier alongside whichever wrb you choose.
One thing you might consider on the insulation - instead of buying EPS and polyiso separate, you might choose to just go polyiso and try to get a bulk discount. A house worth would probably get you closer with just one, as opposed to two smaller quantities.
Maybe you left it out, but what's your plan on attaching the vinyl siding to the structure? It's common to direct attach up to an inch, but I certainly wouldn't sleep well attaching it to the sheathing through four inches of foam. Rainscreen? Built in furring strips with insulation inbetween? etc.
I'm going to vote no on the 'monoply' style of build, just out of the amount of work it takes. It might be better, but I suspect the offset in construction costs and effort isn't worth it. If you have insulation on the roof deck, there will be little incident radiation on the rafter tails, and at most they'll be at ambient temp. Sure it's a thermal bridge, but not one I'd be willing to die on. As far as underlayment goes, I'd again skip the expensive stuff if you're throwing down an impermeable insulation on it anyways, unless there's going to be a significant delay between the application of the underlayment and the rest of the roof. I'd tape the seams, and then #30 will work just fine under the polyiso. The synthetic stuff will work fine too, and the VP100 isn't rated for roofs as it is, even though I know it's not what would really be considered the roof.
If you're using the EPS to keep the polyiso warm, I'd also look into throwing a vapor diffusion port on top, and possibly even adding a ventilation channel for your climate zone. I'd just go with a double layer of the polyiso again, for the cost savings if you can find it.
Hi Kyle,
Thanks for the response. The builders in my area are not familiar with ci and I might just give up on the 4” of exterior and go with 2x6 with 4” closed cell in the studs, plywood sheathing , air/wrb and 1” gps with insulated vinyl siding (it has an integrated rain screen) as cladding. Maybe a 12” rafter with flash and batt.
Andy
If you are not in an area where CI is mandated, you'll have a very hard time finding somebody to build with it. Switching to SPF increases the center of cavity R value but because of the thermal bridging of the studs it doesn't budge the assembly R value all that much. Lot of cost for not much performance improvement.
With lumber prices back to normal, the better option is 2x8 24" OC walls with high density (either fiberglass or mineral wool batts). This has about the the same assembly R value as 2x6 wall with 1.5" of rigid but without any of the issue of dealing with exterior rigid. For best performance, build the walls with plywood instead of OSB and install your siding over strapping.
For roof insulation, your lowest cost high R value assembly is a vented roof with a flat (or low slope scissor truss) with loose fill insulation. SPF in overkill and expensive in new construction unless you are looking for a compact ceiling.
Overall your best return on your dollar is getting the place air tight. This means taped sheathing and solid air barrier transitions from your foundation to your walls and from the walls to your ceiling. Except for a bit of care and a couple of rolls of quality tape, getting this right cost very little.
The other big item is keeping your hvac and ducting within conditioned space.
> 2x8 24" OC walls...plywood ... strapping.
It's a good option - I'd also follow the recommendations here, specifically for the interior vs exterior side perms (table 2A) and for air barriers on both sides (4.2.3). Smart retarders are another "better than code" option.
https://www.appliedbuildingtech.com/system/files/abtg_rr_1701-01_moisture_control_guidelines.pdf
You could also price out zip r
Kyle, Jon and Akos,
Great advice. The building industry around here generally doesnt think beyond spray foam, zip and hardie or boral. No strapping, no rain screens, no 2x8 walls, no exterior insulation, no 24” framing, no idea what a smart vapor barrier is. Architects as well. It is very difficult to make building science advances. I have seen some Zip R… an assembly with Zip R and mineral wool might be something I could make happen. For roof.. the attic square footage is critical in this area so an unvented flash and batt might be easiest. I was thinking of 16” tji with 6” ccsf and 10” mineral wool and smart vapor barrier as belt & suspender. Are tji rafters more or less costly than dimensional lumber (material and/or labor)? I believe thermal bridging through them is a lot less than through lumber.
Thanks
A
Engineered rafters in general are lighter, straighter, and provide a higher strength per unit weight. Their ease depends on the details used, but I would rate then as harder to work with, than regular old 2X dimensional lumber, due to the web stiffeners and other hardware usually required.
Anybody that can build a 2x6 framed house can build a 2x8 24" OC one. There is zero learning curve required, definitely less than ZipR. Attitudes are always hard to change, sometimes you have to accept local limitations.
As for the roof, I-joists make a lot of sense if you have longer spans and can sometimes be even cheaper than dimensional lumber as you can increase the spacing. There is a bit more work to build with them as they can't be notched. You can also look at parallel cord or scissor trusses for the roof.
With SPF in the roof, there is no ROI (or CO2 savings) by going overboard on insulation. Stick to code minimum and with a low thermal bridging assembly (I-joist or trusses) you can look at complying based on assembly U factor. In Zone 5, this can means you can go with 9.5" I-joists 24" OC with 4" of CC SPF plus 5.5" batts.
Akos, my interest is piqued on 2x8 and 24" OC as an an option to 2x6 and 24" OC with external insulation. Can you point to any discussion on this?
Mark,
I don't think there is too much information out there as it is very close to standard construction. I have not built it but would have no problem with it. About the only extra cost would be that 2x8 don't come pre-cut to 92" 5/8 and 104" 5/8, so have to do a bit of extra cutting. Not a huge time add.
This wall can be treated the same as a thinner double stud wall in terms of moisture performance. This means you should have a solid air barrier, the sheathing should be permeable (CDX or gypsum) and the siding needs to be installed over a rain screen.
Thanks, Akos! I'm just trying to understand all the trade-offs (everything is a compromise!). Giving lots of thoughts to labor and difficulty as I'll be doing most/nearly all work. So, material cost, effectiveness and labor are all in competition!
I'm not sure that the extra EPS is needed, but otherwise I love your wall section. Exterior insulation stops thermal bridging which is responsible for up to 1/3 of your heat loss. Neither spray foam nor any other insulation in the stud cavities will make up for lack of exterior insulation.
A couple of other points - the air tightness of the house is critical to a well performing home. With your Henry Blueskin in the assembly, 1 ACH50 should be within easy reach.
I've installed 4" of exterior foam on several projects, strapped over it with long screws and have had no issues with installing siding.
And lastly - condition your basement!!! manage the moisture, and insulate your walls and the basement floor. Whether it's a new home or an antique, conditioning the basement is critical to the performance. Ignoring it is like going out in January with bare feet; hard to heat up the rest of you if your feet are cold.
If cost affectedness is important to you the only real way to answer your question is to build a computer model of your home with the cost per square foot to build each option and run the numbers.
The US government provides the computer program to use free of charge. To watch the training videos on YouTube, learn the program and enter the data is a 20 hour commitment.
https://www.nrel.gov/buildings/beopt.html
In general the latest model codes requirements are high enough that exceeding them given today’s low fuel costs would likely require you to stay in the home more than 20 years to recover the costs.
Walta
> better than Code house
It's important to define "better". More cost effective based on cost to build and energy costs, lower carbon, less likely to suffer moisture problems, easier to build, etc. Some would even add comfort, but IMO, there will be no detectable difference between the options you are discussing.
Look at "whole assembly R value" and otherwise ignore thermal bridging.
Regarding evaluating "whole assembly R value," what building profession that one would hire would be THE one to assess this? I know that there are tables/equations for all this, and while I'll probably use such to help focus on what I believe will be acceptable to me, I'd nonetheless want a good set of eyes to approve/stamp any selection.