Adding XPS insulation

Question about adding rigid XPS foam to my house. I am in zone 5, and my home was built in 1988. The wall system consists of 2×4 framed walls with 1/2 inch XPS foam as the exterior sheathing. The builder insulated the 2×4 bays with an R13 paper faced fiberglass batt insulation, with the facing on the inside of the wall system.
I have done a number of renovations and never noticed any issues with moisture, but I wanted to ask if I may introduce moisture issues if I add an additional 1.5 inch layer of XPS insulation on the exterior when replacing a section of siding?
GBA Detail Library
A collection of one thousand construction details organized by climate and house part
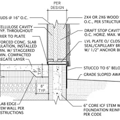
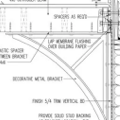
Replies
Hi John.
If there are no water intrusion issues, or you fix them, and if you do an excellent job air sealing (this can be verified with blower door testing), you should not have a problem. Well, you probably wouldn't have a problem anyway, but those details are important.
Most kraft-faced batts are variable-perm materials, which means that in wet conditions they will allow inward drying.
Keep in mind however, that XPS is one of the less-environmentally-friendly insulation types and you could use EPS or reclaimed polyiso instead.
It is a good idea for you to have R-5 or greater of continuous exterior insulation for condensation control in your situation.
Brian has it right.
In Zone 5 if the siding is back-ventilated (like vinyl siding) the ~2-3 perm vapor permeance of half-inch XPS offers sufficient drying capacity to protect the sheathing from interior moisture drives. Without back ventilated siding it's slightly riskier, but not very risky if the interior side is air-tight. The kraft facers on the insulation are "smart" vapor retarders, less than 1 perm when the entrained air in the cavity is low humidity( which is is when the sheathing is cold), but becomes more vapor open than interior latex paint when the humidity levels are high enough to support mold.
Mind you, the labeled R2.5 of half-inch XPS is really closer to R2.1 on a lifecycle basis, given that most of the climate damaging HFC-soup blowing agent giving it a performance boost is gone after 20 years.
A greener solution would be to use 1" foil faced polyiso under back ventilated siding (rainscreened, or vinyl.) The foil facer next to an air gap delivers another ~R1 in seasonal performance, polyiso is a more benign polymer per R than polystyrene, and it's blown with very low impact hydrocarbon blowing agents, not an HFC soup of ultra-high GWP refrigerants.
Foil facers are extremely low permeance (<0.1 perms) but with sufficiently R value it doesn't really matter- the sheathing stays warm enough to never accumulate excessive amounts of moisture, and can dry readily toward the interior.
If adding a layer of foam over pre-existing half inch XPS, from a dew point control analysis perspective credit the old foam for R2.1, the fully depleted performance. Credit any NEW XPS at no more than R4.5/inch, which is the 20 year warranteed performance. Derate any brand-x foil faced polyiso to R5/inch for wintertime performance, since most will underperform it's labeled performance slightly when on the cold side of the assembly. But it's legit to add the R1 if the foil facer is adjacent to an air layer 1/4" or deeper. So adding a layer 3/4" polyiso over old half-inch XPS would deliver about R6.5 total, R7.5 if there's a rainscreen gap, which is plenty of dew point control on R13 cavity fill in your climate.
If you already have the stack of 1.5" XPS that can't be returned, assume the warranteed R6.75, added to the fully depleted R2.1 for the pre-existing half-inch foam and you're at R8.9, also plenty good. Adding 1.5" of polyiso would be both higher performance and a lot greener.
The density of foil faced polyiso is usually 1lbs per cubic foot, half the density of closed cell spray polyurethane (a closely related polymer of similar chemistry.) That gives polyiso about half the CO2e footprint of HFO blown closed cell foam in this chart, roughly on par with fiberglass batts:
https://materialspalette.org/wp-content/uploads/2018/08/CSMP-Insulation_090919-01.png
Thank you both - this is very helpful. I will be using a wood shiplap board to finish over the foam as this area is on the inside of a screened porch. I’ll add an air gap behind the board to aid in drying should it ever be needed.
A 1/4" air gap between the siding and foam is sufficient in most areas. (In foggy-dew western British Columbia code requires a 10mm or ~ 3/8" gap.)
With ship lap siding it's best to primer-paint the backside to moderate the drying/wetting rates to something similar to the exterior side, reducing warping/cracking potential and improving paint longevity.