Adding rigid foam to basement floor after partition walls

Hello,
I’m looking to add rigid foam to my existing concrete basement floor. The basement already has partition walls installed including drywall. How should I detail the foam to wood stud wall connection? I suspect that I should remove a strip of drywall off the bottom of the wall?
I would also include a layer of poly between the slab and the foam. Unfortunately when the walls were built (in the 80’s) there was no barrier installed between the bottom plate and the slab.
The home is located in climate zone 7 in Ontario.
I browsed some articles about insulating floors but didn’t come across this issue. If there’s an article I missed please let me know.
thank you.
James
GBA Detail Library
A collection of one thousand construction details organized by climate and house part
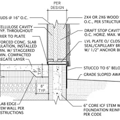
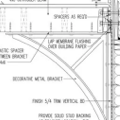
Replies
I'd be cutting off the bottom of the walls first raising the bottom plate and resting them atop the new flooring. Heat flow along with moisture will find that bottom plate and lead to rot.
I would definitely avoid burying any drywall in/below the foam.
If the bottom plates are pressure treated lumber, then I think it'd be fine, and much easier, to just leave the framing alone. If the bottom plates are regular lumber, then I would remove them and adjust the framing as Paul describes.
Thank you for the replies. I'll look into your recommendations.
Hi James -
Even in your climate, when you get to the basement floor (assuming it's not a walkout basement), the delta-T is small enough that the rigid insulation is more about managing moisture and thermal comfort than it is energy efficiency.
A capillary break between any wood or gypsum wall board and concrete is important, but not easy to accomplish after the fact. If your framed wall bottom plates don't have a cap break, inspect and even measure their moisture content, to get a sense of what moisture exposure they may be "seeing." If your bottom plates are pressure-treated you don't likely need to worry about their moisture exposure, but then without a cap break they can wick moisture up to the bottom of your wall studs. You can't use a moisture meter to test the moisture content of pressure-treated wood (the salts in the PT wood render the measurements inaccurate), by the way.
Peter