Adding a Cellulose-Filled Wall to the Interior of Existing Wall

The problem:
In the early 90’s, before I knew anything, I remodeled my 1960’s house in Durango Colorado (6B). The main open living area is 24’x25′. The walls, from in to out, are 5/8″ sheetrock, stapled plastic vapor barrier, 2″x4″x8′ studs 16″OC, blown fiberglass, OSB, 15lb felt, composite wood siding. The roof is 4/12 trusses 24″ OC
In addition to that nightmare, there are two rows of horizontal blocking and many windows with solid headers. There is very little insulated area and what there is, of course, is only 3 ½” thick. In hindsight, the walls are more like a solid wood cabin built out of 4” logs.
The solution I’d like:
Please let me know if this is a doomed idea. I would like to put up an inner 2”x4” wall on the 3 exterior sides, spaced out from the old ones and fill the void with dense packed Cellulose. Effectively a retrofitted double stud wall. It would allow me to break all the thermal bridging from the wood, bring the R value to something modern, increase the skinny depth of insulation over the top of the walls from the 2”x4” bottom truss chord, and shrink the area inside to be warmed as well. Making window buck/jamb extensions and re-trimming them seems much easier, lower carbon, and less expensive than cantilevering some huge amount of foam, furring, and rain screen on the outside. My main concern is the poly sheeting. It would be a much larger job if I had to take it and the old rock out. If I am fanatical about air sealing and use a fancy one way vapor retarder, is there a way to do it? Could it be worse than what I have?”
All ideas welcome!
GBA Detail Library
A collection of one thousand construction details organized by climate and house part
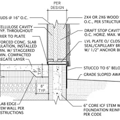
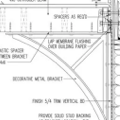
Replies
Hi David,
I’ll give your post a bump and will be interested to see what the experts suggest.
David,
Adding insulation to an assembly decreases drying potential and increases risk, so yes, this retrofit could make things worse. Leaving the OSB and polyethylene intact is concerning given your goal. OSB is very moisture sensitive and has low drying potential (low permeability) and poly is effectively zero perm. If you have decent overhangs, that minimizes some risk, but know that a well-insulated wall can't tolerate even small leaks especially in absence of a rainscreen for drainage.
The poly and drywall are currently your air barrier and vapor control. You wouldn't want to add more than about R10 to the interior or else the poly will get too cold and condensation will form in the walls. I don't think an additional vapor control membrane would help-- you want as much inward drying from the poly as possible.
Better and safer approach is to create a better air barrier at the OSB, insulate on the exterior and install a rainscreen, but it's a pain I get it.
David,
I lived in Durango for about 5 years way back in the early 70's - congrats it's one of the world's really beautiful spots, it's also a pretty dry climate - so don't let them scare you with moisture build up in the walls talk! Here is the way - If and only if, you can stand the cost and the loss of space due to the increased wall thickness. Install 2 inches (or more) of foil faced polyiso directly on top of the existing drywall - tape all seams and tape and or calk to floor and ceiling - then build the new 2x4 stud wall against the polyiso and fill it with your choice of insulation. This will produce a total wall R value of 26 or higher but more important, it will place the condensing surface approx. 1/3 of the way in (1/3 0f the total thermal resistance of the wall - not 1/3 of the thickness!) from the warm side of the wall. This means that even at an outside temp. of say -10 (it almost never gets that cold in Durango) and holding the interior at 70 with 40% humidity, the interior surface of the foam will remain well above the dew point - you won't get any moisture build up in the walls ( they can dry to both sides).
Good Luck!
Perhaps you drill holes in the drywall & poly sheeting to allow vapor to move thru it?
Thanks for the replies! Durango is very forging in terms of drying. Unfortunately, more so every year. The weather and forest is very different than it was 30 years ago. Hence my motivation to lower my carbon footprint. I have overhangs that keep water off the exterior.
Jason, you articulated my own concern exactly. Do you feel Forest's idea is viable?
Forest, shhhhhh about Durango! I like your solution. But wonder if the The sheet rock trapped between the poly and foil could be a calamity in the making. I also wory about the impact of carbon and general nastyness involved in foam production.
Since I'm re- rocking anyway I could suck it up and tear out the old rock and poly but anyone who's done much of that knows how much fun that is, to say nothing of having to dispose of it. I know there is no perfect answer I'm just trying t steer a workable course for my budget and a net positive impact on the climate soon, not in the distant future.
Yes, Forrest's solution can work. You would effectively make the taped foam your new air barrier and it should be detailed accordingly at corners and penetrations. It's unlikely that moisture would get trapped between the existing poly and the foil facing of the foam in this application.
The overhangs and dry climate should limit the reduced drying risk of the OSB, unless other defects are present like finish grade too high relative to siding/sheathing or missing flashings or capillary break at the foundation wall.
If the poly remains, +1 on following the Canadians and keeping it no more that 1/3 of the way to the exterior (on an R value basis). So adding R6 of interior side foam or mineral wool board should work. There will be some condensation/sorption at the studs, but evidently experience says this works.
Others would look at rules for exterior foam protecting sheathing and go as far as 64% of the way through the wall in Z6. I disagree (your exterior insulation isn't continuous), but maybe if the amount of moisture entering the wall is limited.