“Accidental dehumidification” in a renovated building raised on two courses of block

Hello to all; this is my first post here. I am in the process of renovating an old agricultural outbuilding in climate zone 6 (Northern Michigan) to be used as a heated artist’s studio/ workshop. The slab is on grade. The building has been raised onto two courses of 6” thick cement filled blocks that are above grade. The interior face of the cement blocks is becoming wet due to thermal bridging. At the corners, where the cold from outside is most concentrated inside, the blocks are the wettest (though they get wet to the touch overall).
I would like to cover the blocks with rigid foam inside the building (rather than spray foam for fear of allergies) and conceal that with baseboard or wainscoting. Would 2” XPS be thick enough to solve “accidental dehumidification” on the blocks? If not, how thick should the foam be to rectify this problem? For aesthetic reasons, I would prefer to insulate the blocks on the interior of the building as opposed to the exterior, though I would not absolutely rule that out, if it came to it.
Briefly, the building (measuring 19’ x 35’ inside) is presently comprised of the following:
1) At least 3 ½” slab on grade that was already in place
2) 2 coats of drylok masonry waterproofing
3) ¾” blue board XPS ridgid foam sections between 2 ½” pine sleepers (painted on the bottom) 16” on center
4) ¾” plywood subfloor (3/4” solid oak flooring to cover this)
5) Two 6” thick rows of 8” tall block with cement filled cores
6) Sill seal
7) 2×6 framed wall filled with Roxul Comfort Batt insulation covered on the interior wall side with a 6 mil plastic vapor barrier. There is no extra exterior sheathing on the walls because the siding was left intact.
8) 2×8 rafters filled with Roxul Comfort Batt
9) ½” Johns Manville AP Foil-Faced Foam Sheathing board (polyisocyanurate foam) with foil facing the interior of building and metal-taped joints
10) 1” thick pine shiplap covers the ceiling
11) Cold roof design including:
a. 5/8” plywood over existing ¾” roof boards
b. ¾” block + ¾” furring nailer strips for 24 gauge corrugated galvanized steel roofing with COR-A-VENT S-400 Strip Vent Continuous strip soffit vent concealed at eaves and COR-A-VENT V-600 Ridge vent
12) The building’s heating/cooling is to be a ductless mini-split with an electric heater for back-up (right now the back-up is what I have for heating)
Thanks in advance for any advice and insight that you might choose to share regarding this build out.
GBA Detail Library
A collection of one thousand construction details organized by climate and house part
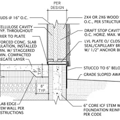
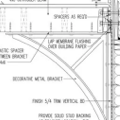
Replies
Kevin,
You have several problems here.
Ideally, your above-grade walls would be insulated to at least R-20. That means 4 or 5 inches of rigid foam on the interior or exterior side of your concrete blocks. This detail should have been implemented before you installed drywall on your interior walls; now this bump-out might be a problem (unless you design some type of bench around your perimeter walls, to make the detail look planned).
Your roof assembly is also problematic. It doesn't sound as if you remembered to include a ventilation channel between the top of the mineral wool insulation and the underside of the roof sheathing.