About to build a house. Questions abound on choices.

Long time lurker here, came through the NY Times article on the Park Passivehaus built in Seattle.
We’re about to build a house here in Seattle as well, a prefab home through Greenfab. We’ve settled on a layout, about 1700 ft^2 for 3 of us, with an extra basement BR for my wife’s work space (200 ft^2) and a MIL apartment (1BR, 600 ft^2). We’re modifying a variant of their 1700 series home.
The PGH ‘standard’ according to the builder would put the project above our target budget. They are building to the 2012 IECC code – R21 walls (fiberglass), R39 roof, 3ach verifiable via blower testing..
The 1FL and 2FL systems will be ductless minisplits.
The basement rooms will be concrete floor, radiant wall panels. No underslab insulation was specified – I guess IECC says, R10 if using slab radiant heat. We aren’t using radiant…
We started talking to the Conservation Services Group who advises on these issues locally, and they told me a few things:
1. Dont spend money at our perf envelope on triple pane. that’s the last thing.
2. Perhaps upgrade wall insulation to something not fiberglass.
3. Consider solar, as the payback with Seattle incentives is under 7 years
4. Get LEED or Built Green certification, it improves resale value and the builder should know paperwork since they built the first LEED plat cert home in Seattle.
I’ve tried to provide as much detail as I know. Given our budget constraints – where would we spend money gainfully? I think that fiberglsas -> cellulose in walls might be more costly than the $7k we might save on triple->double pane.
Given the fact that the basement will be full time occupied, it seems underslab insulation is really going to help but, how much? EPS?
Resale value is important to us, as we may have to move at some point. I’m not building as an investment property, I’d love to stay, but I said that about our East coast apartment…. and here we are.
Flood/water control in basement is important given Seattle mold issues. Lot is flat, a tear down of a pre war home. The current basement is musty but no indication of mold.
This site’s been fantastic for a tech geek like me, but like our software projects, we need to prioritize feature and budget. Where can I get best bang for my buck now? I wish I could do the PGH standard but we can’t.
Your wisdom is appreciated.
GBA Detail Library
A collection of one thousand construction details organized by climate and house part
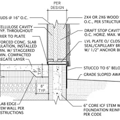
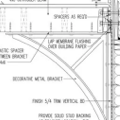
Replies
Bernard,
The usual method of comparing the types of tradeoffs you are describing is with energy modeling software. Ideally, your designer has such software and knows how to use it. If your designer doesn't, that's a bad sign; but it can be remedied if you are willing to hire an energy consultant to help with the specs.
For more information on energy modeling software, see my Fine Homebuilding article on the topic.
A layer of horizontal rigid foam under a basement slab serves several functions. It doesn't just save energy; it also raises the temperature of your slab enough to prevent condensation during the summer. This is more comfortable for occupants, and limits the growth of mold that often creates funny odors in basements. So I think that you should include a horizontal layer of rigid foam under your basement slab.
In your climate, it's hard to justify the cost of triple-glazed windows.
I don't recommend the use of fiberglass batts.
Thanks, Martin. I'll ask them about energy modeling software.
Bernard,
The Energy Modeling Software article is also available on GBA. Here is the link:
Energy Modeling Software.
Our plans, FYI.
So we did our energy audit and our architects recommended that we choose triple pane windows and a more efficient heating system over upgrades to the r21 batts or external wall insulation or the underslab insulation. I'm surprised; i thought that the underslab insulation would be a clear win. Any other ways to look at the data?
Bernard,
Congratulations to you and your team for having conducted this analysis. That's exactly the type of analysis that you should be doing -- and it's something that isn't done for 99% of new homes.
You now have the information you need to go forward (assuming, of course, that the modeling software is accurate, and the inputs were done properly).
I would just repeat my earlier comment: "A layer of horizontal rigid foam under a basement slab serves several functions. It doesn't just save energy; it also raises the temperature of your slab enough to prevent condensation during the summer. This is more comfortable for occupants, and limits the growth of mold that often creates funny odors in basements."
I'm not sure I see the logic behind your architect's recommendations. I am looking at the monthly energy cost projection and not the HERS rating. Base energy cost is stated to be $66/month. For an investment of $1000-1500 (extra air sealing) you can reduce that to $64/month, but instead they are recommending an investment of $1500-2000 (upgrade Fujitsu) for the same $2/month savings. And, you can invest $4000-5000 (triple pane) and save $3/month (payback period would appear to be >100 years) but that is their #2 priority.
I would be asking some hard questions right now. You stated that this is a pre-fab home. Maybe they don't want to alter their usual methods and do the air-sealing differently in the factory, or deal with adding a layer of rigid over the shell, because that just slows them down and asks their workers to do something new. I know that on my crew we have had a learning curve with the air-sealing and exterior insulation techniques, one that I have be happy to meet, but it has not been free.
Another sinister suspicion: maybe they make more by selling more expensive products (windows and mechanicals) more easily, and want to steer you in that direction.
OR... maybe they are actually making an informed analysis that you will be happier with triple-pane windows, and that you should do it even if it doesn't pencil out on the energy analysis.
Not sure, but I would be asking some hard questions by now. It is nuts in my opinion not to put at least R-10 rigid under your slab, so I hope the base at includes that and they are not trying to sell it as an upgrade.
Can you find other Greenfab clients in your area? Might not be a bad idea to quiz them on real world performance.