AAC or conventional “green” — which way to go?

My wife and I want to build a healthy house. We both have chemical sensitives that make “usual” building practices undesirable. Before the market bottomed, we were planning to build a healthy house following BauBiology practices (as much as practical) and using autoclaved aerated concrete for the structure.
We had to delay building until the market improved. While waiting, we learned that AAC talent in our area (Atlanta metro) had pretty much evaporated. As a consequence, we set about designing a house that would use conventional framing and as many no or low VOC materials as possible. We are also planning on a carefully designed HVAC system and energy recovery unit.
We heard that AAC construction was usually about 15% more than standard building. That kind of made frame construction look more appealing–even though it’s still not our preference. Now, my building contacts say material costs for “regular” materials are going through the roof. (So to speak.) As the story goes, building has picked up and the manufacturing capacity is not there to supply the demand.
My question is: Are you professional builders seeing big price spikes? Are they broad and large enough that I should take another look at AAC?
I ask because I have since Identified one and maybe two AAC resources I could use on my project. Thanks in advance for your input.
GBA Detail Library
A collection of one thousand construction details organized by climate and house part
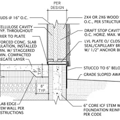
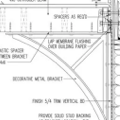
Replies
Steven,
It's hard to imagine that you could ever build an AAC wall for the same price as a wood-framed wall.
Moreover, AAC walls have a very low R-value -- most are in the range of R-8 to R-11 -- and often require poured concrete bond beams that result in horrendous thermal bridging.
Hi Martin:
I appreciate the feedback. The "effective" R-value of an 8-inch block is around 21. I know that's not stellar, but you can create a very airtight structure with AAC. And most builders use U blocks and grout to form the bond beam. Concrete will create thermal bridging, as you suggested.
Perhaps my best course it to invite the AAC builder to bid on the project and see how it compares.
Steven,
"Effective R-value" has no legal definition and is an example of deceptive marketing hype.
The Dynamic Benefit for Massive Systems (DBMS) "effective-R" most cited by AAC vendors is based on a particularly house design used by the Oak Ridge National Labs and a DOE2.1 energy use modeling used for comparison purposes, but unless you build exactly that house, the DBMS numbers aren't necessarily going to reflect the real performance. Whatever DBMS model you use to assign an "effective R", it's true performance will vary substantially with the climate/weather/season, the actual house design, and site conditions.
And the DBMS-R only affects the sensible loads. AAC has a very high vapor permeance and moisture absorption- a moisture reservoir that passes both water vapor and liquid water more readily than most building materials, making it a far-less-than-perfect choice for Atlanta's high latent-load summertime issues. You'd probably be able to build a true/stable R20 (or even R30) wall by other methods (and more appropriate moisture control) for the money, and have lower overall cooling/heating loads.
Attempts to control vapor diffusion or capillary moisture transfer in AAC with low-perm coatings/paints/sealers are doomed to failure- they blister/peel/flake (whether on the interior or exterior) and only semi-permeable paints can be used. In the cooler drier air of northern Europe it does OK from a moisture performance point of view, but it's so low-R that it doesn't meet current thermal requirements without adding exterior insulation.
AAC is fine as a substitute for old-school CMU, but as a standalone insulation it just barely cuts it for a SE US zone-3A location, even in locations where R13 2x4 (R10 whole-wall) is the tract-house standard. In drier US zones 1B-3B locations with high diurnal temperature swings it may be worth considering for code-min with a bit of a dynamic-mass edge, but not in the muggy-sticky SE.
A standard CMU wall with an 1.5" of continuous exterior iso will beat a minimalist AAC wall on both thermal and moisture performance- as it would be more thermal mass, fully inside the thermal envelope. R5 continuous insulation on a CMU wall would meet code min in Atlanta, as would an 8" AAC. But for the cost of AAC there's usually more performance to be had elsewhere. It's real advantage is in larger buildings where fire-resistance is at a premium, in climates where higher-R values don't buy you much. (I saw a fair amount of AAC construction with brick facade going on in larger apartment-block buildings in the Netherlands a couple of decades ago- not sure if it still meets current code there without more insulation though.)
Thank you, Dana.
That's the clearest explanation of the pros and cons of AAC I've ever read. After several false starts, I'd really like to get going on this house. It sounds like conventional is my best option. To make it healthy, we will build as much as possible with low VOC and no VOC materials and specify as many air and moisture sealing steps and HVAC calculations as are practical for our budget.
It's really a shame that AAC won't perform in this climate. There's something about mass that appeals to me.
It's difficult for you to get the AAC wall for the same price as a wood-framed wall and as mentioned bysomebody they have a very low R-value. Check with AAC contractor and find out the best way to do it and more information on the project.
ICF walls can be reasonably cost/performance-wise in the ~R18-22 range, if you are willing to pay a small premium for what you're getting in structural integrity and hurricane resistance as compared to timber-framed R20 (whole-wall) assemblies. At truly high-R it's a bit harder to make the case for ICF, since EPS is pretty steep- R, when it comes in the form of an ICF. Reinforced poured concrete is a heluva lot stouter than any AAC or CMU wall in the face of hurricane force winds- but you still have to pay attention to roof design/anchoring to get the full hurricane-resistance benefit for the house. (Unvented attics fare better than vented, since there's no uplift force from soffit leakage- so as long as your windows & door integrity hold it won't peel the sheathing off the roof or lift the whole roof off in one piece.)
Unlike some other foams, EPS loses the vast majority of it's blowing agent (usually pentane, post- Montreal Protocol) prior to installation, and behind a gypsum finish wall styrene aerosols won't make it into the conditioned space air. If you heat it up to near boiling you can get measurable releases of ethylbenzene, styrene monomer, and acetophenone, but at room temperature it's pretty inert outgassing extremely slowly, except when freshly blown. You're far more likely to get measurable VOC outgassing from EPS packing materials or coffee cups than EPS concrete forms aging in your walls behind wallboard at reasonable temperatures.
I appreciate the ongoing feedback and suggestions.
Dana, I did look into ICF for few months ago and the builder said the costs were not encouraging. Apparently, ICF units and cement are both much more expensive more expensive than conventional construction. And that was before the market began to turn and all the suppliers started raising prices (as I have been told).
Hey Steven, maybe Iam mistaken but it seems like your main strategy to achieve better indoor air quality is focusing on the building materials. Just want to make sure that you are aware of the importance of outdoor air introduction with mechanical ventilation. This should probably be your main strategy. Coincidentally just wrote a couple blogs about that if the moderators allow..
http://www.springtimehomes.com/asheville-builders-blog/?p=283
Thanks, Brian.
Yes, we are very focused on limiting or eliminating VOCs in the structure. We are also insisting on an accurately sized HVAC (no best guesses) and an energy recovery unit for air exchanges. The house will be total electric and have no combustion sources (not even a fireplace).
Thanks for the link. I will check it out.
Hey Steven,
I was a builder in Atlanta a few years ago and am returning soon. i was also interested in AAC and have been for many years now. I am neither pro nor con on AAC. I think it is a good choice for the ATL area but i know what you mean about the talent drying up. That said, AAC is incredibly easy to build with if you plan it out right. The blocks can be laid up easily by normal block masons and it is not true that you will have massive thermal bridges. I just found out about this site last week and am not sure if i can send you my contact details or not. I would be glad to help any way I can.
Hi Mark:
I appreciate the input, but I'm taken AAC off the table. I'm at the stage where I need to stick with a plan, or I'll never get this house going.
I hear ya. What is the new plan, stick-built? I am leaning towards poured in place concrete for my next home or good old CMU double wythe. I think i am going to start using more commercial approaches since i will be building only modern house styles from now on.
Hi Mark:
Yes, it will be stick built with Earth Craft Platinum as the goal. We will minimize spray foam and attempt to use mainly rigid and cellulose. Good luck on using the more commercial strategies. I am finding "regular" construction to be quite expensive.
are you using OVE? be careful also, the lumber companies put a higher factor of safety on framing designs than neccesary, this boost the material cost up quite a bit since they ALWAYS want you to buy LVLs since they make a lot more margin with them. I found OVE with screw and glue floor decking at 24" (with open webs) to be they strongest cheapest easiest to insulate.
Not sure what OVE is. Can you define?
We are using advanced framing, which certainly helps on lumber costs. And I specified web trusses since wood I-beams make me a little nervous. Most of the builders I've talked to use 5/8 sheathing, but I hate spongy floors and have been considering 3/4.
My specs call for glue (low or no VOC) and screw and a complete soundproofing package. The last one I may end up doing myself if the time and schedule allow. We are renting a townhouse in the community where our lot is located. It is build to standard Earthcraft specs, and the noise transmission between floors is pretty awful.
Overall, I'm trying to adhere to the Pretty Good House approach that's been written about here and on Allison Bailes blog.
Steven,
"OVE" framing stands for "optimal value engineered" framing. More information here: The Pros and Cons of Advanced Framing.
Steven, Wood I beams are fine, so is dimensional lumber. I personally prefer open web joists for the floor of the second story and build a chase for the utilities so as to negate any need for HVAC in the attic (all to common in ATL) if you are chasing Earth Craft Platinum then you are probably going to build a great house. The one piece of advice i can give after building there for several years is Manual J and D your HVAC and go with the next lowest tonnage (as i believe J and D still have 15% overage built-in to sizing). i also found zoning (open web trusses make this possible) to be a real energy saver and $$$ saver. When do you break ground?
Hi Mark.
I will have Manual J, D, and S run before we ever break ground. We're planning to use split minis with short runs of duct to facilitate air distribution. Plan is to break ground within 60 days.
steve, great to hear! i would also "round down" on the size if you come up with 2.25 tons cooling on manual D rounding down with a variable speed air handler is as about as efficient as you can get. Also all of the "name " brands, carrier, etc. have generic alternative that are practically the same thin for sometimes many thousands less. Payne is the carrier generic. So heat pump?
Also HVAC guys love to tell you how manual D design (and J for that matter) doesn't make sense that you should have a "central return point" to facilitate "air mixing" this saves them running returns to the places where you actually need them. Even breaking them out of "rule of thumb" upsets a lot of them as they are used to the HVAC Jedi Mind Trick. I use my J and D as bid documents and always spec the generic, Goodman, or Payne.
Hi 🙋♀️Did you use AAC BLOCK for your chemical sensitivities? Thanks
Dayna,
This old thread is a reminder to me of how little I knew about building science in 2013. On this project, I ended up using conventional materials (2x6 framing) and practices to build a energy efficient home. I paid a lot of attention to specifying zero or low-VOC materials and also worked with a few professionals to ensure that we had a sound HVAC and ventilation strategy.
If you have health issues, I'd advise focusing on indoor air quality over trying to source a niche product like AAC. What you really want here is to build what GBA refers to as a "pretty good house." A PGH will be affordable to build and operate, comfortable to live in, and less likely to aggravate underlying health issues.
GBA has lots of content on the PGH concept. For example, here: https://www.greenbuildingadvisor.com/article/pretty-good-house-2-0.