A cautionary tale on HVAC contractors

I wanted to share a story about a HVAC gone wrong in the hope that it may help other users avoid a similar situation in the future.
Last year I purchased a home in central pennsylvania which was built in 1978. The home had a massively oversized Weil-McLain oil fired boiler w/ baseboard convectors and no air conditioning. When I purchased the house I knew that I would eventually add air conditioning and update the heating system to something more efficient. Over the winter I ended up spending $3500+ on fuel oil, despite having the thermostats set very conservatively (~62ºF) the majority of the time.
After agonizing about many possible approaches and talking to at least 8 different contractors, I finally settled on a partially ducted four zone hyper heat Mitsubishi system which would cover all heating and cooling needs of the living areas of the home. The air handler for the ducted portion of the system would be located behind the knee wall in what is currently unfinished attic space, but the air handler and all ducting will eventually be brought inside the thermal envelope when that space is finished. I made this decision for a multitude of reasons, including some fundamental design issues in the existing hydronic system and a decaying chimney flue which would require a liner to be installed in the near future.
I was very careful to select a contractor which did a detailed heat loss calculation by default without me asking for it. I was also careful to select a contractor who specified high/low returns in each room, rather than central returns. I also selected one of the few Mitsubishi Diamond Elite dealers which serve the local area expecting that this would ensure me not only a longer warranty, but a certain level of quality in the installation.
Unfortunately things have not gone as I planned since the install started. Workmanship has been extremely poor, particular concerning the ducted portion of the system which is located in a currently unfinished attic space.
Photo Album: https://photos.app.goo.gl/1QexDSyxR571uxJw5
1. The placement of the outdoor unit does not meet the minimum clearance specifications provided by Mitsubishi. As installed it has only 19″ of clearance overhead and 9″ behind. I raised this as an issue after the first day of the installation to the installer on site as well as the sales rep I was working with, but my concerns were dismissed.
2. The workmanship on the metal ducting which has been installed in the attic so far is not acceptable:
3. There are also several issues with flex ducting in the attic:
4. Return issues:
5. The workmanship and layout of the linesets and electrical which have been run under the deck are completely unprofessional. (see photos)
6. The floor unit (MFZ-KJ09NA) installed in the upstairs office has been completely unable to maintain the desired setpoint. Today the office reached 75°F when the outdoor temperature was 85°F and the thermostat was set to 65°F.
8.There has been drywall damage in several rooms which was not mentioned to me by the crew. Additionally, debris from cutting drywall has not been cleaned up in several instances and room contents were not sufficiently protected from drywall debris. In particular several items in one room have been damaged as a result of being covered in drywall dust.
9.Lineset insulation throughout the system has been shredded when it was pulled and not repaired/replaced. I’ll note that I raised a concern about this after the first day of installation and was assured it would be addressed (it has not been).
—
GBA Detail Library
A collection of one thousand construction details organized by climate and house part
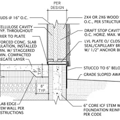
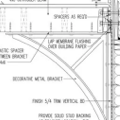
Replies
Fixing the funky hardware they used to level the outdoor unit should be easy. I'd normally just use stacks of washers for something like this. What looks really odd to me is what appears to be a tapcon in a lag shield anchor. Tapcons are supposed to go right into the concrete. If they used just the top part of a lagshield as a spacer, it will probably come off at some point -- the "clips" that hold the two halves together are very loose and won't stay secure. The other odd one is what appears to be a carriage bolt used like a foot setting on the concrete. That probably isn't actually attached to the concrete in any way.
I would have used red head style anchors for this, possibly with some unistrut depending on how it had to be done. I don't trust lag shields with any kind of load on them, especially with something that vibrates like a compressor assembly.
The line set insulation can probably just be taped as long as there aren't pieces missing. A little squish or gouge here or there won't make much difference if you tape over the damage. It won't look great, but it will be OK functionally.
I'm not a fan of flex duct anywhere, but the one thing you just CAN NOT do with flex duct is smash it into a sharp 90 degree bend. You would really need a turning vane for that, which isn't possible with flex duct.
The drywall damage is totally unacceptable. If they didn't even point it out (a "we're really sorry, but we'll fix it" kind of thing), then they probably hoped you wouldn't notice. I'd normally think they just didn't notice they damaged the drywall, but if they just installed those vents next to the damage...
I'd lean on this contractor heavily until they fix these issues. This isn't installed in a professional manner. The code actually DOES require things to be installed in a "workmanship like manner".
Bill
Bill,
The hardware for the wall bracket is an easy fix, but it just demonstrates the complete lack of attention to detail across the entire job. I'm not sure of the specifics of how the bracket was anchored to the wall, but I know some sort of epoxy was also used.
The good news at this point is that I've finally gotten some traction with getting my complete list of issues addressed. I ended up emailing the founder / CEO of the company last night and that seems to have almost immediately resulted in action being taken. The general manager and installation manager were on site today for several hours going over the entire system and working with me to come up with a specific list of defects and how they will be addressed. This includes relocating the outdoor unit to another location that meets Mitsubishi specifications and moving the branch box into a basement utility room.
It's entirely possible the guys in the field cut some corners and the higher ups in the company didn't know and don't want that kind of work done in their name. Glad to hear you're making some progress on getting things fixed though.
I like to say the different between "good" contractors and "bad" contractors is how they handle issues when they arise. Everyone has issues sometimes. Good contractors are quick to fix your issue, and don't give you a hard time. Bad contractors magically disappear and don't return your phone calls. Sounds like you have a good contractor.
Bill