2nd floor is colder than the 1st floor in an ICF home
Hi All,
New home, with the ‘guts’ built by a (rather poor) contractor.
Walls are 6-8″ foxblock ICF with energy sticks. Attic insulation is R50. So should be very tight.
Single stage gas furnace. Installed by amateurs, Builder refuses to adknowledge problem and his trades’ incompetence since day 1. Not having a lot of luck bringing them back, and we are speaking through lawyers at this point…let’s just say that during the walkthrough we discovered the HRV inlet/outlet lines were reversed, so little/no fresh air was being drawn into the house.
Anyways, we got that fixed, but now its 74F on the main floor, and only 64F on the 2nd floor. The home has cold air returns in all rooms. At floor level in bedrooms, but near the ceiling in bathrooms (where they connect to the HRV).
When the heat ducting leaves the furnace, it splits into 3 – basement, 2nd floor, 3rd floor. The furnace is in the basement. The HVAC trade put dampers on the 2 round ducts that head upstairs, but nothing on the basement duct.
Hubby has been adjusting the two dampers to the upstairs, and closing the heat registers on the main floor, but its only increased the temperature by <2degrees. It’s awful. We wanted the 2nd floor to be warmer since we are always cold when we sleep. Suggestions for improvement? We are contemplating adding a damper to the square duct, since that’s the shortest run and closest to the basement.
GBA Detail Library
A collection of one thousand construction details organized by climate and house part
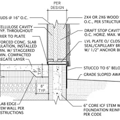
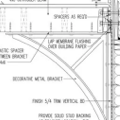
Replies
I'll add that this house doesn't have a huge amount of windows, and is designed old school 'closed concept'.
Is this a 3 story structure being operated as a single zone? This is sometimes hard to get the temperature balance perfect even with a Manual-D duct design, but 10F is quite a bit off the reservation.
Installing a balancing vane in the as-yet undampered zone to reduce those flows only works up to a point, since there are minimum flow requirements that need to be met for the heat exchangers in the furnace. If the supply ducts are undersized start with a (gingerly applied, don't throttle it way back) balancing vane to the square duct, and improving the flow to the cold zone where you can.
Start by sealing (to the extent possible the duct runs and register boot to the top floor at every joint & seam with duct mastic, and caulk the boots to the wall/floor where they they enter. If there is any flex duct on that run, replace it with hard-piping. If there are any sharp-throated ells with a hard 90 degree angle inside of the turn, replace them with radiused ells, which have a much shorter "effective length".
If those measures fail, a duct booster fan to the cold floor supply duct could be added to improve flow as a last resort.
Roberta,
Dana gave you good advice. We don't know whether (a) Your heating system was well designed, or (b) Your heating system was well installed.
At the design stage, the HVAC system designer might have failed to perform an accurate Manual J load calculation, or might have undersized some of your ducts.
At the installation stage, the HVAC system installer might have failed to seal leaks in the ductwork, or failed to follow the duct design.
It's really hard to diagnose this type of problem over the internet.
Hi Dana and Martin,
Thank you for the quick reply.
To answer your questions
- Yes, 3 stories on a single zone system
- we are in Canada, so 'Manual' Calculations were not used. They claim they used ASHRAE...on a piece of unsigned paper from a distributor...after we pointed our contract required detailed calculations for HVAC design. Our Builder refuses to say anything to us other than "Its done right!"
- We were there when they installed the ducting - it is all rigid, and heat runs were taped/liquid-sealed, though we had to redo a bunch of them RIGHT before drywalling due to them not even pressing the tape down so it stuck!
- Unfortunately the HVAC company sub'ed out the tinbashing, and that company told us 'we were just given a box of parts of make work', so it may well be suboptimal. We have massive round ducts (10-12" possibly?!) going to the main and 2nd floor, as they were trying to reduce losses.
The fact that it's all hard-piped is encouraging, as long as it's all hooked-up, with no broken joints blasting away into a stud bay or chase.
Seal up what you can, including pulling the registers to verify that the register boots are caulked/sealed to the wall or floor, and give the balancing vane on the un-dampered floor a shot before resigning yourself to a duct booster fan.
My guess is the upstairs is cold because that is where the heat loss is. If it were well sealed and insulated the warm air from down stairs would find its way there and the second floor would be warmer than the first.
I think money spent on an energy audit with a blower door test and inferred camera will pay off big.
Walt
PS if your builder really was trying cheap out on your HVAC you would not find any metal duct work, dampers , cold air returns or an HRV.
Walter -
We did tape every darn joint we could find during the wee hours the morning before the drywallers showed up, because complaining to the builder did little.
I'm uncertain why you think an energy audit will show anything? This is a full 3 story ICF home, so other than the roof, there really is little way for heat to escape. (I checked and re-foamed doors and windows myself prior to drywall, if I felt the builder didn't put enough in. We have horizontal access via an insulated door to the attic, and blow-in insulation to R50 level in the attic (yes, I've been up there lots...we had a roof leak...). Some air will leak out the kitchen vent/damper, since the wind likes to catch the flapper, but the doors are insulated fibreglass with proper weatherseals, corner seal pads, etc.
We paid the builder well over double what a 'typical' house in the area costs, with emphasis on energy-efficiency, and removing as much thermal bridging as possible. The HVAC cost us over $25k for the house. The HRV is a code-requirement in the frigid north where we are.
Dana - the heat duct boots aren't sealed to the floor, so I will tape those tonight to see if it helps. Would the cold air returns need this done as well?
Thanks!
Roberta / Little Birdie,
Walter makes a good point. During the winter, the indoor air temperature in most two-story and three-story homes is higher on the upper floors and lower on the lower floors, even if almost all of the heat is delivered to the first floor. Something may be wrong with your thermal envelope or ventilation system.
You need a lot more measuring. Ie, measure register & duct flows, duct pressures, room to room pressures, indoor to outdoor pressure and HRV balance (with and without the furnace fan on).
As a general energy efficiency benefit, I'd get a blower door test done. I expect that most people who have believed "there can't be any air leaks" have been proven wrong.
Jon - I hear ya, and am not disagreeing - I'll have to look at how much itll cost a third party company to do that. The builder insisted the hrv rates were correct and refused to show us the measurement data until the building inspector agreed w my husband and forced him to provide it...
I'd get the energy audit as well. I replaced a crawl space under my home with a full height ICF basement. If they did a poor job and thorough inspection was not done by the GC, there could be voids that penetrate the envelope. I had a devil of a time getting complete concrete flow under window bucks. Was successful with one exception, but I did it myself on my own home so was extra diligent. If your contractor was incompetent it would be easy to miss. What is the ICF foam thickness, and was it air sealed?
David, the ICF is 8" in the basement and 6" above, with foxblock 'energy sticks' for extra energy efficiency and to shift the thermal mass to the inside of the wall.
The more I think about this, the more I think that poor duct flow to the second floor is unlikely to be the root cause of the problem. This is based on my own experience with a variety of homes in a moderately cold climate (Upstate NY, zones 5-6) and on research done by Ian Shapiro, which indicates that supplying 80+% of the heat to the first floor is an appropriate design strategy. See his blog series:
https://buildingevidence.wordpress.com/2016/12/21/heating-downstairs-versus-upstairs/
In addition to the energy audit (and I’d recommended seeking out an auditor with HVAC troubleshooting and commissioning experience), I’d look closely at the control setup. Is the thermostat located too close to a supply register or other heat source? Is the house being over-ventilated (i.e. can the HRV speed or run time be reduced while still meeting fresh air targets)? The contractor's shiftiness around the ventilation measurements is a bit of a red flag for me.