2,700 sq/ft house climate zone 6 R20-R27-R40-R70 7,300 HDD -1 Design temp…minisplit sizing and zones?

First of all thank you all of have contributed to this website. I’ve researched a lot and it’s provided valuable insight. I’m designing my house right now. 2×6 framing with zip sheathing as the primary air barrier and 4″ exterior polyiso R42. Basement walls will be 2″ polyiso with 3.5″ roxul R27 (should I increase this?. Slab 4″ XPS R20, and attic R70-blown in with poly as the air barrier. The plans show sliding windows and sliding doors but everything will be single doors and awning/casement/fixed. The bonus area over the garage will use Zip as the floor air barrier with blown-in insulation to R50’ish. Is that high enough to not worry about the thermal bridge in the floor?
Anyways, I really want to heat the home with a minisplit. I like the Fujitsu models with extra low temp heating. My question is can I get by on a single mini split for the whole house? Or two zones, or 3? The SEER is the highest for the single head models. Where should I place the head/heads? The main-upper staircase will be open tread design. Haven’t decided on an HRV but I like the Aldes model with the booster fans to centralize the exhaust and HRV. So the air will move.
If you need further specifics let me know.
Thanks,
GBA Detail Library
A collection of one thousand construction details organized by climate and house part
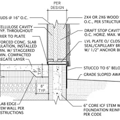
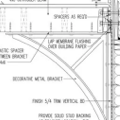
Replies
A room-by-room heating load calculation at the outside design temperature would be a good place to start.
With a wall U-factor in the ~U0.25 range window losses and air infiltration assumptions are likely to dominate the heat load.
Without it there's no way to really answer the questions with any confidence.
In the basement with 2" of polyiso between the R15 rock wool and foundation you have adequate dew point control for the above grade section, and the total performance beats code-minimum. If you increase the fiber-R by going with 2x6 /R23 you'd have to add another half-inch of polyiso to maintain a similar dew point margin. Whether it's "worth it" depends a bit on how much above-grade exposure it has, and what your performance goals are.
Since it's in the design phase it's not too late to swap out the sub-slab XPS for 4-5" of Type-II EPS, which is both cheaper and greener. Over a few decades the performance of XPS will fall to that of EPS of similar thickness & density, as it's climate damaging HFCs leak out. EPS is blown with a much lower impact blowing agent, most of which is recovered at the factory, and it's performance is stable over time.
As far as zoning goes, you'll be better off with a minimum of three zones, one for each fully conditioned level. Whether or not you need more than one ductless HEAD per story depends on the room-by -room load numbers, particularly the loads of rooms doored-off from other rooms on that level. Basements (even walk -out basements) have very different loss characteristics than fully above-grade floors, and the floor-to-floor temperature balance changes with the weather. Convective stratification makes the top floors not balance very well when zoned together with the lower floors too, though that's less problematic during the heating season than basements. But top floor cooling loads are usually higher than lower floors, which makes cooling season temperature balances off if zoned together with lower floors.
In a zone 6 climate you should be ignoring the SEER efficiency- the HSPF numbers are far more important. But sizing the compressor capacity at the 99% outside design temp to the actual heating loads it's supporting is usually more important than the nameplate HSPF. Oversizing the compressor by too much is going to destroy it's "as used" shoulder season efficiency (and overall seasonal average efficiency) by forcing into a cycling rather than modulating mode. For example:
A single head Fujitsu can only throttle back to 3100 BTU/hr out @ +47F, but if there are three of them there's a minimum output of 9300 BTU/hr @ +47F. But a 3-zone Fujitsu XTLH multi-split can throttle down to 6100 BTU/hr @ +47F. So if the load at +47 is much less than 9300 BTU/hr (probably is, but run an aggressive Manual-J to prove it) and the separate mini-splits would likely be cycling on/off a lot even when it's below freezing, in which case it's likely that the multi-split will deliver higher as-used heating efficiency than three separate mini-splits despite testing at a lousier HSPF number. (For very low heat loads there can be advantages to going with Mitsubishi's half-ton and 3/4 ton cold climate mini-splits, since they can dial back to 1600 BTU/hr @ +47F and will modulate more, cycle less.)
FYI the plans are attached in the first post. The king has spoken. I've read over a hundred of your posts thank you for chiming in. It is not too late to swap for type II eps thank you for the suggestion. I attached the floor plans in the original post. The basement is 25% garden level 25% forced walkout and 50% full basement. I'm fine with R27 down there so I don't further encroach the square footage.
Do you have a resource you can refer me to run the manual J? The windows will be the weak link for sure. Zip sheathing is common here but not the additional steps to ensure the air tightness we don't know what to expect but I think under 1 ACH is reasonable. We're taping the two 2" layers of polyiso over the Zip.
The upper level is just under 1200 sq/ft. The plans may deviate but he's going off of the exterior foam dimensions. We were originally going to use 2x4 framing with 6" exterior polyiso but my "wholesaler" cannot reliably source it at the cost needed to make the numbers work. I'm gathering that a 3-zone Fujitsu may be a good fit.
Thanks again!
For non-standard assemblies like this it's better to hire a certified professional engineer to first calculate the U-factors necessary to run the load numbers. There may be some sharp RESNET raters capable of getting there too, but most Manual-J software tools are ill-prepared for getting realistic numbers on high-R houses, and the default settings for air-leakage etc are abyssmal.
The air leaks may still be where the foundation sill meets the foundation ( EPDM sill gaskets under the bottom plates recommended), but there are 1001 other details to get right to duck under 1ACH/50. Electrical & plumbing penetrations of the walls and upper floor ceiling abound, and sloppy window & door detailing can still leak copious amounts if given short-shrift.
A 3 zone Fujitsu may or may not be a good fit, depending on where the load numbers come out. At the moment optimizing the window glazing size & type for wintertime solar gains while rejecting summertime heat is a worthwhile exercise.
In a zone 6 climate even with a 99% design temp of -1F you may still find that double low-E double panes are the price/performance sweet spot with low-E coatings on surfaces #2 and #4, which generally work out in the ~U0.25 range, which are much cheaper than triple-panes in the U0.20 and lower range. But the combination coatings on west facing windows (and maybe the east) should have a lower SGHC than on south and north facing windows. The low-E coating on surface #4 increases wintertime condensation/frost issues on the windows when it's -10F out, but if your 99th percentile temperature bin is -1F it shouldn't be a big issue.
User-6925805,
First, it would be nice if you could tell us your name.
Second: Dana Dorsett has given you good advice. For more information on hiring someone to perform your Manual J calculations, see this article: Who Can Perform My Load Calculations?
One of your questions -- "can I get by on a single minisplit for the whole house?" -- is easy to answer: No. A two-story house needs a minimum of two minisplits: one downstairs, and one upstairs. The downstairs unit is often sufficient to provide all of the home's heating needs, while the upstairs unit is often sufficient to provide all of the home's cooling needs. But you still need at least two units.
Hi Martin,
My name is Brandon and I live in SE WY. Unfortunately I cannot get the link to work but perhaps it's because I'm under the free trial.
The home is 2-story on a full basement. Are you recommending one in the basement and one upstairs?
Brandon,
If you have signed up for our free trial, the link should work. I recommend that you contact our customer service department for help with the link problem.
Taunton Customer Service
E-mail: [email protected]
Phone number: 800-943-0253
Since your basement is finished, and it includes a family room, bedroom, and bathroom, you really have a three-story house. There are many ways to proceed; for example, you could install a ducted minisplit unit to serve the basement and the first floor, and then you could install a ductless minisplit (perhaps -- depending on your family's expectations concerning room-to-room temperature variations) to serve the second floor.
But, as I wrote, you can't heat and cool the entire house with one minisplit.
And, as Dana told you, the first step is an accurate load calculation.
It really needs to be at least three zones, if the basement is being used as living space (which it is.) It appears to be a walk-out basement, with a lot of exterior above-grade surface area and window area. It's loads are probably pretty small- maybe even within the capacity range of a half-ton ductless head like the Fujitsu 7RLS, but it's definitely not going to be able to just "coast" when it's -1F outside. But a head in the basement is also not going to be able to adequately heat & cool the first floor either.
An accurate load calculation from an engineer (and NOT an HVAC installer) would be necessary to figure this out.
I am trying to find someone to run the numbers for me. I will update when I get it figured out. Are there any articles you can reference for a centralized exhaust/HRV?
Thank you,
I've got someone working on the resnet calc for me. Since then I have made a couple of changes. The home is exactly 1900sq/ft above grade with a 800sq/ft basement. We adjusted the walls to 2x4 and the most economical batt is R11. It was also suggested that I switch to EPS for the exterior since the cold weather performance and degradation of the polyiso isn't worth the cost. The cost difference to upgrade to the 27K BTU tri-zone minisplit is negligible (three 9K heads, one per level). My walls are reduced to R27 above grade (R16 foam + R11 batt), R19 below grade, and R16 slab. Initially do you think the mini split will still work? I hope to use an electric fireplace as back up heat.
Any articles referencing the Aldes total home system?
Thanks,
Brandon,
I visited the Aldes web site and I couldn't find any reference to a ventilation system called the "Aldes total home system."
Can you be more specific? Aldes sells HRVs, ERVs, and exhaust fans.
Here is a link to an article on ventilation options: Designing a Good Ventilation System.
http://www.bathroomfanexperts.com/product.php?product=174684
There's the link. The 200cfm is overkill but I think it can run at a lower volume.
Any comments on the insulation? If I increase it will be more cost effective to add an additional layer of 2" EPS versus increasing the stud cavity. The cost will be nearly $1600 more which almost covers the HRV/exhaust expense. Not to mention more foam complicates the stone ledge. The resnet calc will answer more but I'm trying to keep my structural engineer informed of any changes.
Thank you for all of your help and I look forward to sharing the progress.
Brandon,
That's a ducted HRV system, with constant airflow regulators in the bathrooms to adjust exhaust rates from bathrooms when bathrooms are in use. It should be a good system -- but similar (though not identical) systems can be installed with rival HRV brands.
Alright, we decided to go with 6" exterior EPS +R11 2x4 walls for the exterior, basement is 4" EPS +R13 2x4 walls, slab perimeter R10, subslab R20, Roof R50'ish at the heel and R70'ish for the rest. When performing manual J/D does the engineer take into account total wall performance with 2/3 of the insulation on the exterior? Should I specify that? I just don't want the equipment oversized.
Martin, thank you for commenting on the HRV I'm realizing I don't need a set up with boosters. Checking city code I think they default to the 2015 IRC not the ASHRAE requirements. Utilizing continuous exhaust in the 5 bathrooms and kitchen means I need 125cfm continuous. Is there a general rule of thumb on oversizing the HRV so it can run in "boost?" I have two awning windows in the kitchen so I'd like to try the recirculating exhaust hood versus vented with makeup solution. Thank you all for your help.
Brandon,
Q. "When performing manual J/D does the engineer take into account total wall performance with 2/3 of the insulation on the exterior? Should I specify that?"
A. Whether or not the person who performs the Manual J inputs the correct R-value data for the walls depends on whether the person doing the Manual J is conscientious. (There are a lot of sloppy Manual J calculations out there.) Certainly, you should provide an accurate description of your wall assembly, including any exterior rigid foam details, to the person you hire to do your Manual J.
Q. "Utilizing continuous exhaust in the 5 bathrooms and kitchen means I need 125 cfm continuous."
A. If you are using bathroom exhaust fans to provide your ventilation requirements (either to meet ASHRAE 62.2 or to meet code requirements) -- creating a so-called exhaust-only ventilation system -- the minimum continuous ventilation rate has nothing to do with the number of bathrooms. It is calculated according to formulae provided in the ASHRAE standard and the code book. For more information, see Designing a Good Ventilation System.
Q. "Is there a general rule of thumb on oversizing the HRV so it can run in 'boost'?"
A. Here's the advice provided by Barry Stephens: “We want continuous ventilation at medium speed to be at about 50% of the airflow capacity of the HRV.” For more information on this issue, see Does a Home with an HRV Also Need Bath Fans?
"When performing manual J/D does the engineer take into account total wall performance with 2/3 of the insulation on the exterior? Should I specify that?"
A year or so ago I reviewed a Manual-J on a very high-R house that had all code-min default settings plugged into it, complete with the professional engineer's stamp on it. The complete building plans had been submitted to that firm, but they (apparently) ignored everything but the gross size dimensions.
A second Manual-J on that house performed by a different engineer including multiple appendices detailing the U-factor calculations for the non-standard framing and insulation details.
Bottom line, don't just assume they will get it right. Pay attention to the details of the report, and ask lots of questions.
Thank you for the advice I will make sure they take into account the wall details.
Martin, I may have come across wrong. I want to exclusively utilize an HRV for the exhaust. I attached a screenshot of the 2015 IRC section. I'll check with my mechanical engineer but my interpretation is that the bathrooms require 20cfm of continuous exhaust each and the kitchen requires 25cfm continuous, the 125cfm total overrides the 75cfm requirement according to the first table.
Thank you,