24″ o.c. rainscreen furring concerns

Getting ready to start a house for a customer, double 2×4 walls, etc. We left the exterior side 2×4 @ 16″ oc due to rainscreen furring concerns.
I’m beginning to question whether we can move to 24″ oc on the outside wall and use our rainscreen furring 24″oc…?? Furring will be 2×4 KD lumber, mainly because we can get 2×4 cheaper than 1×4 and it’s not that much more effort.
So can the furring go to 24″oc and not have problem with the clapboard siding going crazy?
Thanks
GBA Detail Library
A collection of one thousand construction details organized by climate and house part
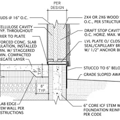
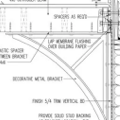
Replies
R. Mills,
Every siding manufacturer publishes installation instructions. Since different brands of lap siding have different profiles and thicknesses, there is no single answer to your question.
Some types of siding can be installed on 24" o.c. furring strips, while other types need the furring strips to be spaced 16" o.c. So check with the siding manufacturer. Most siding manufacturers post their installation instructions on the Web.
Western Red Cedar claps, wrcla says it can go 24", I was looking for real world experience
R. Mills,
There may be more than one source of information on the web, but here is what I found ("How to Install Western Red Cedar Siding" from the Western Red Cedar Lumber Association):
"Siding should be nailed into studs or blocking at maximum of 24 inches on center when applied over wood based sheathing and 16 inches on center when siding is installed without sheathing. In instances where an air space between siding and sheathing is desired (see rain screen wall construction) nail siding to furring strips. Maximum spacing for furring strips is 16 inches on center. Spacing for furring strips should match the spacing of the studs."
A trick you can use is to utilize wide boards for your strapping. With Wood siding I think you will be fine. Buy Plywood sheathing and rip it into Wide strips. For even more Protection use pressure treated plywood for your strapping.
Aj
At some point when you increase the width of your strapping, you don't really end up with a rain screen. Our code puts the limit at anything over 8% of the wall. Wide strapping also introduces wide areas of contact between it and the siding, which are not separated by a WRB and where rot is most likely to occur. Stick with narrow strapping and space it appropriately would be my advice.
Going to use 2x4's for furring, area of concern is the wood siding spread out to 24" oc furring spacing
Unless you are trying to distribute the load on semi-rigid exterior insulation like mineral wool boards to avoid crushing there's no advantage to using anything that wide. 3/4" x 1 1/2" strips of plywood or wood are all that's used here.
There will never be rot with wide or narrow pressure treated strapping.
I wouldn't trust the junk plywood we have around here to hold any type of fastener.
How about horizontal strapping? That is sometimes done.
https://www.greenbuildingadvisor.com/blogs/dept/qa-spotlight/what-s-best-approach-rainscreen
Lucy,
You are on to something with that! We may be able to make it work..
How will horizontal strapping work with clapboard siding?
double post
Malcolm,
Horizontal, then vertical strapping is what I had in mind. That would let me make the vertical spacing whatever I wanted it to be 16" in this case
A lot of builders here do that with cedar shingles rather than use one of the meshes. A bit more work but, as you say, gives the control back to you on spacing and yields a very well vented wall.
I just want to be able to look at these houses we're building in 40 years and they still be in great shape. My dad at 78 is able to do that now, something to be proud of.
In that respect I like rain screens for two reasons. They increase the longevity of your siding, but also isolate any rot that may eventually occur from your sheathing and framing.
Sidings such as hard-plank and hardi-panel will require a 16" o/c layout for warranty. They can have a tendency to wander if the rain screen spacing gets too far apart. Other sidings, such as a thicker cedar bevel siding may stay more straight. Board and batten siding will usually require 12" o/c spacing for other reasons, of course. In general, best practice requires that the rain screen is at 16" o/c and more importantly, that the rain screen attaches directly do studs behind the sheathing (which is really why you're asking this!)
Aside from that, what would be your reason for switching to 24" o/c? Cost would be a legitimate reason, purely to save on the number of studs required. However, if you are doing it to improve R-Value. A true-wall R-value calculation (taking into account thermal bridging of studs), indicates that there is not a very measurable difference between 24" o/c and 16" o/c framing in a double stud wall. For example, if I model a 10" thick, 8' tall, 50' long double stud 2x4 wall (with no window or door openings), the actual surface area percentage of framing in that wall of lumber vs. insulation is 10.8% at 24" o/c, and 14% at 16" o/c. The true, modelled R-values of those two walls is 35.16 @ 24" o/c and 34.17 at 16 " o/c. And that is if BOTH interior and exterior walls are framed at the specified o/c spacing. (This is admittedly an optimistic framing percentage, as often if one has many openings the framing percentages would realistically be higher, perhaps +/-17% at 24" o/c and close to 20% at 16" o/c. Still, the difference in R-value between the two is pretty negligible.) The real benefit comes from the amount of pure insulated space between the two walls, and the fact that the thermal bridging has been eliminated.
Having your studs at 24" o/c means that your floor joists, wall studs on both floors, and roof trusses should all be required to stack directly above one another (or within 1.5"), which adds time for layout. A 16" o/c wall stud layout means that your floor and roof elements can land wherever they want on the plates irregardless of other loads. However, making your interior and exterior walls in the assembly have the same spacing means you can save a lot of time on your actual stud layout, as they are identical and can be traced across all the plates at once, which should compensate for the time required to stack your components at a 24" o/c layout.
It is throwing a few more things in the fire, but if R-value is your main concern, perhaps that will help lessen it's weight in the decision, as the stud spacing really has little effect!
By the way, the horizontal strapping on the wall first can create little "ledges" for bulk water that finds its way behind the cladding to sit on. It is less ideal than the straight vertical rain screen approach. However, if you don't get a ton of rain in your area and/or you have large roof overhangs and/or you are meticulous in your flashing and penetration detailing, then having the effect of a ventilated rain screen cavity is probably sufficient, even with the first layer on the sheathing being horizontal. Personally, would feel much better about my siding fasteners going through rain screen, sheathing and into a stud, rather than just through one layer of rain screen and then floating in space behind it. . .
Burke, A large proportion of the houses built here are framed at 24" o.c., and while some builders use 'true framing" , that is aligning the structural elements vertically, most don't, and our code doesn't require it.
Malcolm,
I hope they use double top plates, not single top plates.
Of course. "Advanced framing" using single top plates is essentially a novelty. Our code specifies that regular, (non-point) loads can be carried by the top plates at 24" oc. because there simply isn't an issue in doing so. And what floor system would allow you to align you joists with 24" o.c. framing? The only real benefit to "true framing" is ease of installing services.