2×6 wall design

I am currently in the design phase of building a house in northern Alabama. I would like to use 2X6 walls on 24″ centers and Zip Sheating. In a typical situation which option would my money be better spent:
Option 1: Spray foam the walls with double pane windows.
Option 2: Zip-R (R3) sheating with rockwool/cellulose and double pane windows.
Option 3: Rockwool/cellulose with triple pane windows.
Or some other combination not listed? Obviously I want to keep the wall design within a certain budget.
GBA Detail Library
A collection of one thousand construction details organized by climate and house part
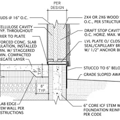
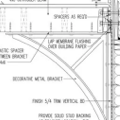
Replies
Spray Foam (Option 1) and triple-pane windows (Option 3) sound more expensive to me. You might consider if rigid foam on top of Zip-R would be less expensive. That way you have more choice of what foam to install.
Triple pane windows make no sense at all in climate zone 3. A double pane with two low-E coatings, one on surface #2, the other on #4 (the surface in contact with the indoor air) would be a big upgrade at a much lower cost than triple panes. In most houses that upgrade would have more impact than adding the R3 ZIP-R.
Table 2 of this document recommends as a starting point a whole-wall value of R20 as the potential sweet spot, (you'd be there with R3 ZIP-R) and sub U0.30 windows with an SHGC less than 0.3 :
https://buildingscience.com/sites/default/files/migrate/pdf/BA-1005_High%20R-Value_Walls_Case_Study.pdf
The window upgrade to a double low-E double pane with an SHGC <0.25 and an U-factor <U0.25 would likely have a bigger effect a lower cost than ZIP-R.
With an argon fill Cardinal Glass LoE-366 (surface #2) + i89 (surface) #4 comes in at about U0.20 at center glass, with a an SHGC of about 0.25 which would be pretty good. For west facing windows LoE-340 (#2) + i89 (#4) would have about the same U-factor but a very low SHGC of 0.17. That's just the center-glass numbers. With the framing and spacers factored in the whole window assembly's U-factor goes up a bit and SHGC falls a bit, so in a real product you might expect LoE-366 + i89 to run about U0.23-U0.24 with an SHGC in the low 0.20s which is fine.
A standard ZIP and R23 rock wool would almost hit R20 whole-wall, and might actually hit it if the full-on Advanced Framing/Optimum Value Engineering approach were taken to the framing design, minimizing the amount of doubled-up framing anywhere that could be avoided, with windows & doors & rafters all aligned to the extent possible with the 24" stud spacing, advanced framing corners, etc.
Dana has really served up your question above but for you and others, if you are up for learning an (free online) energy modeling program, take a look at http://www.beopt.nrel.gov.
Peter
If you go with the very aggressive lowE coatings like cardinals 340, I strongly recommend you go see such a window in person before committing to it. LoE 340 is pretty dark, you’re getting into a range with a pretty big visual hit (low VT) with that coating. It is great if you have solar gain issues, but otherwise you’re trading off a lot of VT for the slightly increased insulating performance.
Bill
That is a very good point when going for SHGC less than 0.20. The LoE 366 + i89 is probably a better choice for most people.
With adequate shading factors on the east and west exposures and over hangs on the south facing glass even a high gain LoE 180 +i89 might be the sweet spot, but at a SHGC >0.5 it could lead to a big bump in cooling load if the shade factors are suboptimal. That would lower heating energy use noticeably, but could increase cooling energy use by even more unless properly shaded during the cooling season.
Dana's overall point with the glass is a good one: Select different coatings for different windows. He bases it primarily on direction, which makes sense. But you can also select lower SHGC and lower VT glazing for windows in rooms where daylighting makes less difference and where glazing sizes are selected more for external aesthetic fenestration reasons than daylighting and/or interior views. Few builders will offer the option of different glazing options for different windows because it makes their job more complicated, but there are good reasons for doing so.
If you're going to switch up glazing type by orientation (recommended only for fine tuning it to the max), make sure the windows are different sizes- make it difficult for the installers to screw up putting low-gain windows on the south side and high gain windows on the west, etc.
Good point, but you do still want the house to look good from both outside and inside. There are some truly ugly, though highly efficient houses out there.
You can minimize the ugliness by making the windows fit architecturally. You only need a small size difference like an inch or two to key the windows to a particular spot, or intentionally use them differently in different spots (like floor to ceiling on one side, but over counters in another).
Another big rule is make sure all the windows in one visual plane (like one wall, or on both sides of a corner in the same rooms) are the same. If you use, for example, a mix of both LoE 180 and LoE 366 on the same wall, the difference will be VERY noticeable and will look strange. If the different coatings are used in different rooms, where they can’t be seen together at the same time, the difference probably won’t be noticed. Remember to think about this from both the inside and the outside of the house.
Bill
Better options?
A couple of personal opinions –
1. Regarding foam between the studs – don’t do it. There have been articles about this on GBA (e.g. https://www.greenbuildingadvisor.com/article/installing-closed-cell-spray-foam-between-studs-is-a-waste, and read the comments), and a week doesn’t go by that Dana and others point out the folly of that approach. Thermal bridging, environmental impact, durability concerns, plus that fact that spray foaming operations are operator and weather dependent with very high rework costs all make spray foam installations in walls a dubious decision. And notice that I haven’t even mentioned cost yet. I’d pick cellulose or rock wool between the studs, but really anything but spray foam.
2. I just went through the process of replacing a bunch of windows. The point about VT is a good one. And I agree with others that triple pane windows do not add value equal to their additional cost over double pane in most climates. The one exception that I would make to this is if you live in a noisy environment, e.g., on a roughly paved road with high traffic. Then, the extra cost of triple panes can be worth it, and then some.
>”The one exception that I would make to this is if you live in a noisy environment, e.g., on a roughly paved road with high traffic. Then, the extra cost of triple panes can be worth it, and then some.”
That’s not exactly true. Triple pane windows don’t necessarily make a drastic reduction in sound transmission. If you want sound reduction, your best option is laminated glass, followed by different thicknesses for the panes in a double pane assembly (like one 1/4” pane and the other 1/8”). Some manufacturers are able to offer triple pane windows with different thickness glass panes to improve the sound deadening properties of the assembly.
The best option would be a triple pane assembly with a thick, laminated center pane, but I haven’t found anyone willing to quote that option.
Bill
Thanks for all the replies that was extremely helpful.
The window recommendations above sound like the best options. I was referring to open cell foam in the walls, which i'm still considering depending on the cost of the window specs listed above.
I assume in a milder climate that Zip R sheeting is not worth the cost?
Open cell foam is fine, but rock wool batts will outperform it if the stud bays are meticulously air sealed prior to insulating, possibly at a lower cost. Dense packed cellulose usually costs more than open cell foam or rock wool in my area. Cellulose has a few other advantages and is greener, but it's the same R-value as half-pound open cell foam. Rock wool is greener and higher R than open cell foam.
Whether or not ZIP-R is "worth it" depends on your performance goals and other options. Installing half inch polyiso on the exterior of ZIP (non-R) or CDX would deliver the same performance upgrade as ZIP-R which might also be lower cost.