2-part spray foam: Store-bought kit or professional application?

New home build in CZ 6A. While discussing my cellulose insulation requirements with a local supplier, he tried to sell me on spray foam for both the rim-joist and below-slab in the basement in addition to the cellulose for my walls. I explained to him that sub-slab spray foam was likely out of our budget and that if I did spray foam in the rim joists it would only be a thin coat for air sealing purposes, and that I would probably do it myself with a store-bought 2-part foam kit.
He made some claims to back up his argument:
1. He claims sub-slab foam is a superior way to go, and that no EPS panel job would offer the same continuous layer or air tightness.
2. He claims that store-bought 2-part poly foam is inferior in quality and performance to what the professionals are using, and that he’s been called out to “many” jobs where this inferior foam has had to be removed and re-done by his team.
I didn’t argue with him, but my thoughts are:
1. Spray foam could cost MUCH more per R/sqft (he claimed about $3/sqft for R10) than an equivalent EPS foam board installation below slab, and this could be significant in a 1700 sqft basement. Also, judging by the spray foam wall jobs I’ve seen, the inconsistent applied thickness of the foam could lead to widely varying concrete slab thickness unless considerable effort was put into leveling it before the pour.
2. A friend of mine is using Dow Froth Pak 2-Part poly foam to do his home’s rim joist area, and he’s impressed with it. I read up on the product and it gets excellent reviews, is not prohibitively expensive, and it’s an R6/inch closed cell foam. If care was taken to ensure a proper installation I would think this foam would work well, no?
Are my thoughts reasonable, or does the insulation guy have valid points?
GBA Detail Library
A collection of one thousand construction details organized by climate and house part
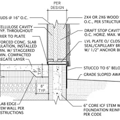
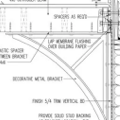
Replies
Lance,
I side with your analysis. When it comes to sub-slab foam, using rigid foam is easy and sensible. The environmental cost of using EPS (especially reclaimed EPS) is far less than the environmental cost of using closed-cell spray foam.
Here is a link to an article on insulating rim joists with two-component spray foam kits: Marc Rosenbaum: Basement Insulation: Part 2.
If you have a spray foam job that is any bigger than insulating rim joists -- a job that involves an entire wall or ceiling -- it certainly makes economic sense to call up a spray foam contractor.
I agree with Martin, EPS is a fine choice for sub-slab insulation.
Regarding the DIY foam kits, I’ve found them consistently disappointing, both in terms of yield and foam quality, despite following application guidelines carefully. If you do go this route, pay close attention to kit and substrate temperatures and skin/eye/respiratory protection. Another option is to use blocks of foam board (possibly scrap EPS from the slab, though I find foil faced polyiso much easier to work with), sealed in placed with single-component foam.
So I ended up using the leftover foam from my friend's Dow Froth Pak kit to insulate/seal the rim joist area of our mechanical room. Overall I am pretty impressed with the product. It applies very quickly and does a visually good job of blocking some rather large gaps. The cured foam is fairly firm and dense; trimming it with a knife reveals a very fine texture that is nice and uniform. It is pretty rigid when cured. Perhaps this would be an issue as the building moves with temperature and humidity changes?
I have absolutely no experience with any professional spray foam products so I can't comment on how they compare. I did notice that both my local Lowes and Home Depot carry a different brand of 2-part foam product called "Touch'n Foam". Perhaps these are the kits that don't perform as well? No idea. He bought this Dow kit at Rona (we're in Canada).
The rim joist was only accessible in this area, the rest of our town house basement is finished. I'm hoping to have cured two cold spots on our kitchen floor; the two corners where the kitchen protrudes out from the back of the house. When I pulled the fiberglass insulation out it was FULL of mouse droppings and tunnels that the little critters had made. No wonder... there were three places where I could see daylight coming in! The rim joists appeared to be nothing more than flooring I joists butted together at 90 degrees with the resulting gap leading out to the back of the house wrap. Spectacular.
Hopefully with this area air sealed and a little better insulated I'll notice a cozier kitchen floor. It seemed like a pretty good use of some leftover foam.
For our new house build I have been planning all along to use 3" R12 EPS foam panels below the basement slab. If reclaimed product is available at the time of our build I will definitely look into that option.