16×16 Studio Build – Climate Zone 6A

I am in the process of getting some plans together to build a 16×16 studio space located in NS, Canada. I will be using electric heat. I have decided on most of the assemblies but just wanted to see what others would think.
-Foundation will be a slab on grade, insulated with 2″ XPS – many slabs this small around here are built without any frost protection, good idea? There will be a vapour barrier on the under side of the slab as well as compacted crushed stone, etc…
-Wall assembly from interior to exterior as follows; Gypsum wall board, 6mil poly VB, horiz. strapping, 2×6 stud @ 24″ O.C. w/blown cellulose, exterior sheathing, tyvek, vertical strapping, finish cladding (undecided). The reason for the strapping on the inside is for sound proofing as it will be a music recording studio, and when I net the studs for cellulose, I will strap over the netting to prevent the cellulose from pushing the Gypsum wall board.
-Roof assembly (asphalt shingles) single slope (3:12) with pre-engineered truss-joists @ 24″ O.C. My plan here is to install cellulose as well, and make my own roof vents (on under side of roof sheathing) from plywood and strapping to create the space so I can fill it (vent baffles would be to hard to seal). I will use the same method of strapping and netting as on the wall assembly.
As an overall assembly does this sound good? I am worried about some detailing – the VB to come wrap around the slab, and under the sill plate to connect with my interior VB; should I bother? All of the other details seem pretty straight forward to do from the sill plate up around the ceiling plane.
Any insight would be greatly appreciated, and if I left out any information my apologies, I will post it up if needed.
GBA Detail Library
A collection of one thousand construction details organized by climate and house part
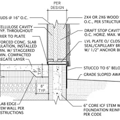
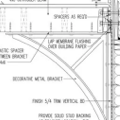
Replies
Mark,
Sounds minimally OK. It's definitely NOT a good idea to build a slab in zone 6 without frost protection, and the 2" of XPS is the minimum required for that climate (it also must extend a total of 4' vertically downward and/or outward).
The cross-hatched cellulose walls should offer the code minimum R-20 but I would advise leaving out the poly vapor barrier since most cellulose manufacturers discourage its use (cellulose works best when it can breathe, use a vapor retarder primer instead).
The IECC requires a minimum of R-49 for the ceiling, which would require at least 13" of dense-pack cellulose. Do you have that much depth in the truss-joists? If not, I would recommend building your vent cavity above the framing with a double layer of sheathing separated by strapping.
Putting a capillary break between concrete and wood framing is always a good idea. Be sure to air seal this joint as well.
You won't get much acoustic isolation from horizontal strapping unless you use resilient channels.
Dear Mark,
I would consider placing the poly VB between the 2x6 studs and interior strapping. To co-ordinate with this, I would do everything reasonably possible to keep the wires, electrical boxes and plumbing (if any) within the furring cavities and outside of the 2x6 framed and poly-wrapped wall cavities. This will help to keep the VB continous. Use standard (non vapour-retarder) paints on the drywall so the furring cavity can dry toward the inside.
The 2" insulation under the slab is definitely needed, and I would consider thickening it if finances allow. In addition, provide lots of insulation on the slab edges and wings of insulation under the finished grade adjacent to the slab, sloping away from the slab. The detail between the slab edge insulation and wall framing must be carefully considered and executed to stop water, insects and flow of heat.
Truss joist on the roof is good - The deeper the better. In Ontario, the code requires a 2.5" minimum space between the underside of the roof deck and insulation. I would consider adding 2x3 or 2x4 purlins on top of the joists (across the joists) or sleepers (along the joists). Place them on the flat for easier nailing and an excellent surface to attach roof decking. Then, working on the inside, use the underside of the top chord of the truss-joist as the nailing surface to attach boards to make the vent space, which would then be about 3". This board should be fairly vapour-permeable, I would think. Both plywood and OSB are pretty vapour impermeable. I'm actually not sure what would work best here - I would think wood-fiber board - but I've never used that stuff before.
Lyndon
Oops, my answer was posted at the same time as Robert's and it seems to be in contrast to some of his points - I hadn't read it yet.
LT
I agree with Robert about the insulation values. I'm working on a Passive House in the Toronto area and the design calls for roughly about R60 walls and foundation, R100 roof, R 20 under the basement slab. Of course, there is the high-performance south facing windows, with proper overhangs to go with those r values.
Sorry, I didn't know much about cellulose insulation.
LT
I agree with Robert, you should go with ADA in a marine climate. These folks have really mastered ADA and the details with ACH50 numbers under 1.
http://www.energetechs.com
Thanks for the advice everyone. I have not ordered the roof joists yet, so I can specify the depth; I think 14" would do the job.
As for the slab, I will do a thickened edge slab and skirt out or down for frost protection. The local building inspectors claim that frost protection is not needed on a slab less than 600SqFt, only supporting one level; any insight?
I will ditch the poly, and instead of strapping the wall I will staple the cellulose net back slightly to prevent the bulging out to far, and that way air tight drywall approach is much more simple. Is vapour retarding primer readily available at most building supply stores?
Mark,
Moorcraft Latex Vapor Barrier Primer Sealer (or SuperSpec) 260 creates a less than 1 perm film with a single coat. I'm sure other major paint brands have also come out with similar products now that codes require only 1 perm retarders.
While there's little reason to build a frost-protected foundation for an outbuilding. Any building that must remain plumb and level and has utility connections that can be disrupted should be on a foundation or slab that isn't going to heave.
However, soil must contain at least 5% silt and be saturated with water in order for frost heave to occur. If you're building on well-drained gravel, then there's little worry about frost heaving.
Thanks Robert, your advice has been great and well appreciated.