12 x 24 pending cabin plans help, please

All comments welcomed and appreciated – first time post: 12×24 getaway cabin with electricity in zone 2/3 wet/humid (central Georgia). Interior-to-exterior: reclaimed 3/4″ barnwood walls – advanced framed 2×6 stud walls 24″ O.C. with 3″ polyiso between studs – 1/2″ exterior plywood – DOW weathermate plus – 3/4″ vertical rainscreen – 4×8 T1-11 or fiber cement.
2×6 rafters with same 3″ polyliso with reclaimed tin attached directly to rafters for ceiling.
Small bathroom with toilet/shower/sink with quality ‘poot sniffer’ vent fan – will have a well – intend to go with tankless electric unit for heating water.
3/4″ T & G plywood subfloor over 2×8 PT joists with same 3″ polyiso insulation in joist bays.
Please assume a tight building envelope. Does anyone see any major issues?
Window question: I have 5 new Marvin ‘exterior door’ fixed transom windows: Any potential problems using them as ‘exterior’ windows, assuming professional installation/flashing?
This cabin will resemble a Derksen building, but with improved techniques.
Critical comments are appreciated – thank you.
GBA Detail Library
A collection of one thousand construction details organized by climate and house part
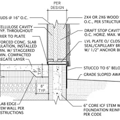
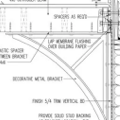
Replies
Brad,
The main problem with your plan is that you intend to cut your rigid foam into narrow strips and to insert the strips between your studs and rafters. If you do that, you will find air sealing more difficult, and you will cut the thermal performance of your insulation significantly, by introducing so many thermal bridges.
Please don't cut up your polyiso into narrow strips. Instead, install a continuous layer of polyiso on the exterior side of your wall and roof sheathing.
It's also worth mentioning that metal roofing shouldn't be installed directly to the rafters. It should be fastened to plywood roof sheathing, OSB roof sheathing, or skip sheathing (purlins) -- usually 1x4s or 2x4s, installed 24 inches on center.
Thank you for your VERY quick reply and I understand! A few follow-up questions, please: If we install the 3" polyiso (4x8x10 foot) to the exterior per your site instructions, is the 2x6 framing a bit overkill on a getaway cabin? Using 2x4 framing and insulating the stud bays with fiberglass batts would save $ and time. any issues with using the leftover 3" inside the 2x4 stud bays then fiberglass batts once the 3" runs out? I wasn't clear on my initial comment on reclaimed tin roofing - that will be aesthetically used on the interior ceiling, nailed directly to the rafters, with insulation in the rafter bays, then sheathing, 3" polyiso, purlins then metal roofing.
As for the fixed transom windows (2' x 5') - should there be any installation issues with them being used as 'picture windows' on the exterior (again assuming proper flashing and installation)?
Thanks again for your consideration - this site is a great source of information and I'm anxiously awaiting my first copy of Fine Homebuilding.
Brad,
2x4 studs are perfectly adequate from a structural perspective to hold up a single-story building.
The minimum code requirement for the R-value of walls in climate zone 3 is R-13. Here at GBA, we often advise builders to exceed minimum R-value requirements. If you install 3 inches of polyiso, it will have an R-value of about R-18 or R-19, so you will easily meet minimum code requirements even if you don't install any insulation between your studs.
If you decide to install insulation between your studs, you should choose a vapor-permeable insulation so that the wall assembly can dry to the interior if necessary. That means you should choose fiberglass batts, mineral wool, or cellulose -- but not polyisocyanurate. (You want to avoid sandwiching your plywood sheathing between two layers of vapor-impermeable foam).
If your transom windows were designed for interior use, they may not be a good choice for installation in exterior walls. Softwood window frames can rot quickly when exposed to the weather, especially if interior glues or finger-jointed lumber were used to manufacture the window frames. Moreover, such windows were not designed to shed rain.
Martin - they are exterior transom windows with sloped sill wood/aluminum cladding on the exterior side and natural wood on the interior. I was concerned they did not have nailing flanges. They are new-in-box (given to us) and appear to be designed to go with a certain Marvin door assembly. Wanting to make sure these would not be a problem/out of the norm for a competent framer. We are attempting to use as many found/reclaimed/begged materials as possible.
Thanks for the heads-up on NOT sandwiching the polyiso.
Still OK with advanced framing 24" OC with the 2x4's?
Again - appreciate your quick replies.
The reason you don't want to waste the high R/inch polyiso as cavity fill is that with 3" of (R1.2/inch = R3.6)wood covering ~20% of the cross sectional area of the AF wall, the heat flux through at 15% framing is exceeds the the amount of heat moving through the R18-ish center cavity foam. The "whole wall" of your stackup (with R1.5 added for the sheathing + siding + interior planking) of the 3" cavity fill is R11.5. Just two inches of foam sheathing, leaving the cavities empty would give you R13.5- higher performance with less insulation.
Fill the 2x6 framing with R20-ish fiber and put just 2" of iso on the exterior would yield better than R26 whole-wall, more than double the 3" of cut iso between framing.
With 2x4 framing you'd have to drop back to 16" o.c. to get roughly the same structural capacity of 2x6 24" o.c., but it's about the same raw board feet of lumber. With 3" of exterior iso and R13-R15 batts in the cavities you'd be at about R30 (nearly 3x the performance of a cut'n'cobbled iso wall.) If using batts, with a planking interior it's good to use something vapor-permeable as an interior side air barrier (housewrap, rosin paper, kraft paper are all fine.) Using asphalted kraft facers on batts for ease of installation is OK- they're at least semi-permeable (more permeable when wet) but isn't really a sufficient air barrier, especially if you're using fiberglass, which can put micro-particles of glass suspended in your room air if not adequately constrained by a truly air-tight construction. (Using smart vapor retarders as the interior air barrier would be expensive and unnecessary.)
Under no circumstances should you use polyethylene sheeting anywhere in that stackup. Similarly, foil-facers on batts are extreme vapor retarders that would create a moisture trap. Unfaced fiber is best, but nothing more vapor tight than asphalted kraft facer can go into that wall.
Brad,
It should be perfectly OK to install the flangeless windows you describe.
Concerning your question about whether a "competent framer" understands how to flash a window rough opening, I would say, "I depends." In general, I would say that just because someone is an expert at framing, doesn't necessarily mean that he or she knows anything at all about window installation.
I have no problems with your decision to use advanced framing, as long as you can satisfy your local building inspector. Note that some types of advanced framing assume the use of 2x6 studs. Of course, 2x4 studs can also work, as long as all structural issues have been addressed. If you aren't sure about the structural integrity of your frame, consult an engineer.
Here is a link to an article with more information on advanced framing: The Pros and Cons of Advanced Framing.