1. Window square footage? 2. “Effective R-value”?

Hello, and a big thank you to all the experienced voices out there who contribute to this blog. We are trying to design a 1700sqft timberframe (slab on grade zone 6A southern Maine). We are looking at windows and after reading this blog for weeks there doesn’t seem to be real consensus on how much window area to put on a south wall. I agree that envelope design may have won out over passive gain, but I also agree with some writers that a sunny room just feels better, and it is hard to quantify that. Is there a general ballpark to shoot for? 6%-10% seems to be bantered about–I assume they mean window area to floor area, but is that total window area or just the southern wall? Our original number was 15% total window (.15×1700=255sqft) area with 50% (120sqft) of that on south wall, based on another source we read. Is that too much? Too bright? Too hot?
Second question regarding wall design: I have spoken to one designer from Canada who speaks of “effective r-value.” His wall design calls for (going from inside to out): timberframe–sheet rock–2×4 wall with fiberglass bats–sheathing–2″ Quik-therm MPI–1×4 strapping–siding with effective r-value 23. His thoughts are that “effective r-values” are actually lower than r-values just summed up by the components, and that Canada is heading down that road of real world testing. He said he is having good results with his wall. Having read numerous articles about double walls, SIPs, air-blower testing, I am not sure how to make a decision. It seems that in this age of super insulated and net-zero, that wall seems thin. If so, would swapping sprayed in foam for the fiberglass batts be a good alternative to raise r-value? Can foam be sprayed on the back of sheetrock? I was hoping to get some feedback from the community on this wall and if it will be appropriate for southern Maine. Thanks in advance for any help on this.
Bob Young
Scarborough, Maine
GBA Detail Library
A collection of one thousand construction details organized by climate and house part
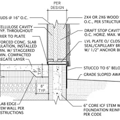
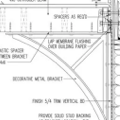
Replies
A 2x4 wall with batts and half-inch gypsum and half inch sheathing comes in at about R10 after thermal bridging of the framing is factored in. Adding up the R values of the other continuous layers to the R10 for the basic wall is usually pretty close.
Being Type-I EPS, at 2" the QuickTherm tests at about R7.8 when the average temp through the foam is 75F, but R9+ when the average temp through the foam is 25F. With an air gap between the foil facer and the siding with the addietionl air films the facer gives it another ~R1 of performance, and if you add in the siding + interior & exterior air films it's another R1+.
Add it all up and it's an effective "whole-wall R" in the R220R23 range when it's 0F outside. In a Scarborough ME location it's wintertime average would still be R20-R21, and plenty of dew point margin for R13-R15 batts in 2x4 framing. With foil facers on the foam you do NOT want to use sheet polyethylene vapor barriers, foil or vinyl wallpapers, or any other low permeance materials on the interior. Latex paint is fine.
Bob- our pretty good house is in Whitefield Maine. Floor area is about the same as you are contemplating. We have about 325 square feet of window area, or about 20% of floor area. About half is on the south side. We've never experienced overheating. On some sunny winter days, it gets to high 70's, but sitting around in a t-shirt when its 10 degrees out is fine with us. A sunny room just feels nice.
Our walls are double stud, about R42, ceiling about R70. I agree with Bill that you'd be happier with 2x6 studs (filled with cellulose?) and enough exterior foam to keep the sheathing warm enough.
Are you using an architect? Lots of good ones in our state.
If you want more R value, add more external insulation and consider 2x6 framing on 24" centers. The last thing you should do is add closed cell spray foam to the stud bays. Why avoid the spray foam? First, you don't want to sandwich your sheathing with impermeable foam. Second, the flow of heat through the studs lowers the effective R value of that part of the wall (the framed part) so much that the extra R value and extra cost of the foam is largely wasted.
See https://www.greenbuildingadvisor.com/articles/dept/musings/how-design-wall, especially the section titled "2x6 walls with exterior rigid foam".
Wow, that was fast.
Bill, thanks for the link--it was exactly the kind of info I had been looking for on GBA. I had been leaning toward 2x6 but this designer is pretty insistent 2x4 is enough. Maybe he is thinking primarily in terms of code, which is usually a minimum.
D.Dorsett--thank you for your evaluation of this wall design. I am still unsure if this is adequate for Maine? My hope is that a small woodstove, a minisplit and some solar gain will be enough to get this house through a winter. From my reading it seems that air tightness is as important as wall design, and if it is sealed up properly maybe the 2x4 is adequate, but 2x6 is better.
Stephen--thanks for the feedback from your current home experience--real world feedback is invaluable. Is the south side close to due south? I have seen your name in these blogs before as you worked through the process. We are trying not to go down the architect road, as our aim is to build a simple decent, tight middle of the road retirement home, and the fees for an architect seem out of our league. I think with a little help from this blog and GBA and all its contributors we will be OK. Thanks again to all!
Bob- Our house is oriented about 15° west of south. Let me know if you have questions or want to see it in person.
My first reaction to this post was, "What is Quik-Therm MPI?"
It turns out that this is a brand name for a type of foil-faced EPS (expanded polystyrene).
Robert,
First, the phrase "effective R-value" has no agreed-upon definition, so the term is best avoided. (In fact, deceptive marketers often use the phrase "effective R-value" to mean almost anything they want. As a general rule of thumb, when you read the phrase "effective R-value," it makes sense to distrust the thermal performance claims that follow.)
In the U.S., R-value is defined by federal law (16 CFR 460). Manufacturers, distributors, and installers of insulation are required to adhere to the legal definition of R-value in all marketing claims. All methods of measuring R-value are refined by ASTM. These definitions have a purpose; they are established to prevent insulation manufacturers from inventing new tests that favor the materials they are pushing. (For more information on this issue, see Understanding R-Value.)
It's OK to talk about "whole-wall R-value." Whole-wall R-value is a measure of the performance of the entire wall assembly. If you're talking about a wood-framed wall, the whole-wall R-value is generally lower than the R-value of the insulation materials installed between the studs.
Talking about changes in the performance of insulation materials at different temperatures is tricky. We can't really say that the R-value of polyiso drops as the temperature drops, because R-value is a material constant defined by law. We can, however, say that the thermal performance of the polyiso is worse at lower temperatures than it is at higher temperatures.
Robert,
In the early 1980s, designers of passive solar homes developed rules of thumb to determine the area of south facing glass for a so-called passive solar home.
These rules of thumb varied depending on what book you happened to be reading, but here is a summary:
If the house doesn't have any extra interior thermal mass, the area of the south-facing glazing should be 6%, or 7%, or 8% of floor area of the house.
If the house had extra interior thermal mass, the area of the south-facing glazing could be as high as 12% or 13% or 14% of the floor area of the house.
Some passive solar advocates even made complicated tables that provided different recommendations for different climate zones.
I think you should take all of these rules of thumb with several grains of salt. I recommend that you choose your window area based on aesthetic considerations rather than thermal considerations. A window is not a heating appliance.
To learn the basis of my advice, you should read these two articles:
Study Shows That Expensive Windows Yield Meager Energy Returns
Reassessing Passive Solar Design Principles
Hi Martin,
Thank you for the reply. After reading the link Bill sent (in response 1 above) which references a good article you wrote regarding a solid basic cost effective wall for the masses. I was uncomfortable with the idea of a single 2x4 wall in New England and what I have read so far confirms it. i guess the only thing I am not crazy about is hanging that much framing on a timber frame. It seems excessive, as it is not structural. Can you point me to any links for cost effective simple walls for timber frames? Thanks again for your time.
Robert,
Q. "Can you point me to any links for cost-effective simple walls for timber frames?"
A. In general, if you want cost-effective and simple, don't use a timber frame. As far as I know, there really isn't a simple way to answer the "how to I wrap a timber frame?" question. In almost all cases, you end up building a second frame to hold the insulation -- and the second frame is robust enough to make the timber frame unnecessary. The timbers end up being expensive wall art and ceiling art.
Briefly, most timber frames are wrapped in SIPs. Many of the SIP-wrapped timber-frame homes from the 1980s are now being repaired due to moisture problems that developed at the SIP seams. Proceed with caution, and with your eyes wide open.
"I am still unsure if this is adequate for Maine?"
From a moisture risk perspective the stackup is perfectly adeequate. thermal performance point of view a 2x4/R13 + R7.8 (or R9-ish, counting the thermal benefit of the foil facer), works just fine.
In zone 6 (most of Maine) it needs an absolute minimum of R7.5 on the exterior for dew point control to be able to skip the interior vapor retarders. R7.8 isn't exactly rockin' huge margin, but it works:
http://publicecodes.cyberregs.com/icod/irc/2012/icod_irc_2012_7_sec002_par025.htm
From an R-value code minimums perspective it's close, per IRC 2012:
http://publicecodes.cyberregs.com/icod/irc/2012/icod_irc_2012_11_sec002.htm
ME spans zone 6 & 7 so code-min wall would be R13+ R10 continuous, or U0.048 (R21 whole-wall). With only R13s you might be just shy of U0.048 even with the benefit of the foil facer and extra air films, depending on the actual framing fraction. But If you installed R15 in the cavities instead of R13 it would make it, so long as the 3/4" air gap between the foil and the siding is guaranteed. Without the gap it would still come up short.
Call it a marginally code-minimum assembly with acceptable moisture resilience.
Thank you all. You have given us enough food for thought to rethink the notion of a timber frame. We love the aesthetic but closing it in does seem problematic, redundant and expensive. This short discussion has been most helpful.
For example, if you took a R-50 wall assembly and installed a 15% glazing ratio of dual pane (R-3) windows. That R-50 wall assembly would drop down to a whole wall average of R-15. That is a 70% reduction in R-Value. Now, take that same R-50 wall assembly and install a 15% glazing ratio of a triple pane (R-8) windows. That R-50 wall assembly would now have a whole wall average of R-28.
Of course that whole wall average is not factoring things like thermal bridging, air sealing, etc. It's just a general example. The point is windows are always the weak link in a building envelope.