1 1/2 story — need help with insulation

How to help a homeowner? It’s a 1 1/2 story home built in 1949.
The kneewalls have exposed fiberglass batts. I don’t know about the floor yet.
The rafters are 2 x4s with fiberglass batts between the ceiling and the roof.
There is a limited budget to do upgrades. What could you be done that is worthwhile for the second floor? The roof is newer and insulating the exterior of the roof is not an option. Lowering the ceiling is out too.
GBA Detail Library
A collection of one thousand construction details organized by climate and house part
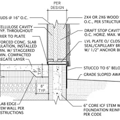
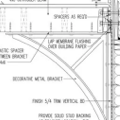
Replies
Robert,
Energy retrofits aren't magic. They cost money.
Fixing this house the right way requires bringing the woefully inadequate roof insulation up to modern insulation levels. You don't mention where the house is located, but the 2006 IRC requires a minimum of R-30 in climate zones 1, 2, and 3. In climate zones 4 and 5, you need R-38, while in climate zones 6 through 8, you need at least R-49.
Right now, the roof has about R-11 or R-13 insulation. And that's a generous guess.
If the homeowners don't want to lower the ceiling, the only way to add the required insulation is on top of the existing roof sheathing. That means installing a new roof.
And if you are installing a new roof, it's a good idea to get a structural engineer on board to assess the existing 2x4 rafters. My guess is that the new roof will require new rafters, either sistered to the existing rafters or on top of the existing roof.
Robert,
One more point: if the homeowners qualify for low-income weatherization assistance, they should definitely take advantage of the program.
The low-income weatherization program provides free energy retrofits to qualifying homeowners. While the program may not pay for a new insulated roof, the weatherization crew will come up with a customized list of cost-effective weatherization measures and will perform the necessary retrofit work.
We are looking to expand our business in get into auditing and energy effiency upgrades. I have done a lot of self study for years and have taken some online courses for auditing and installation. I am in homes on a regualr basis and see many deficiencies. A common one is the 1.5 story as descibed, a 3.5 in batt in the cieling. Its an expensive fix to correct that.
I am in Zone 5a in Neb. Low utility costs and low green movement. There is a lot of skepism from the public on the savings and benefits of upgrades to existing homes.
I would like to invest in a blower door and all the equipment necessary to do audits but there is just not a market for the services here. I know many projects do not require all the testing, like the one mentioned above. A great starting point for this house is the attic, both air sealing and insualtion levels.
Robert,
I think given the circumstances outlined in your question you may already be describing the best possible scenario ;)
In all honesty, I dealt with the same problem in my house, and ended up building in. I made a composite furring strip (2" polyurethane foam + 2x2 furr framing), screwed that to the 2x4 rafters, inserted continuous vent chutes from the soffits to a ridgevent, and had the entire cavity filled with closed-cell spray foam. This makes for a near thermal bridge-free, vapor and airtight assembly with an R-value in the mid 30s. With an 8/12 roof pitch I sacrificed about 3" of interior space to the thickened package. This solution was reviewed by a structural engineer to make sure it does not compromise the 2x4 assembly.
Not cheap, not ideal, but given the circumstance a very viable solution that lead to a very comfortable half-story with slightly less than ideal ceiling height. As so often in life, something's gotta give and you have to decide what that is. I agree with Martin that there is no magic (and cheap) bullet here.
You must address the area between the knee wall and the wall line of the first floor as well. The ceiling joists are typically underinsulated with air leaking under the knee-wall. I pressure tested this same type house before a remodeling project and the ACH50 was right at 10.
Tim's solution would cover the air leakage associated with knee walls.
On a limited budget, I would start with backing up the knee walls and sealing the joints with foam. Use either Thermoply (cheaper) or 1.5" Thermax (better). Be sure there is a top plate on the knee wall and install a baffle at the top to prevent wind washing through your cathedral area. Under the knee wall - block between the ceiling joists and fill all gaps with foam. Air seal at all ceiling areas (from above if possible and below where there is not access). Down the road can look into adding insulation. Won't be "as good as new" but will enhance the performance dramatically.