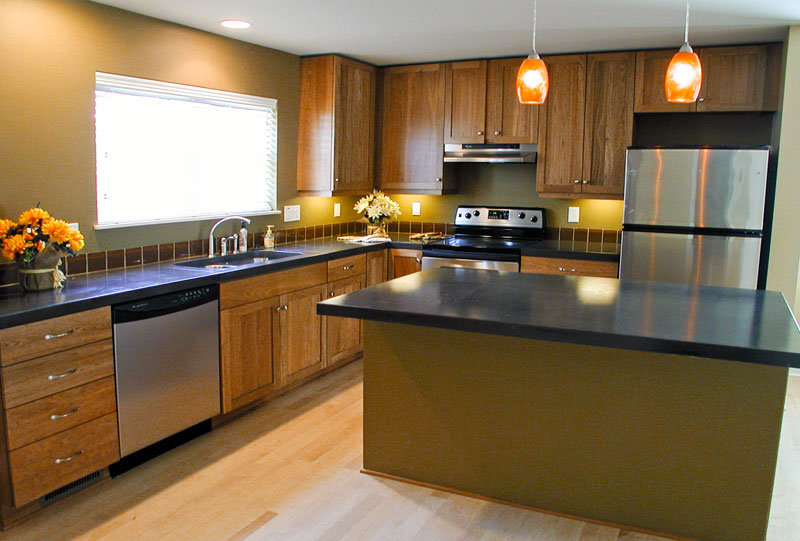
Image Credit: Joshua Lloyd
Image Credit: Joshua Lloyd Notice how the house wrap id folded up above the window so that it can weather lap over the flange after the window is installed. Green window installation is all about good sealing. The priority here is shingling the waterproofing materials and bonding them together. The students wrapped the rough sills with self-adhesive flexible flashing and installed a backdam to make sure that any water that seeps in has a way to get out. After caulking the opening and setting the window, installers bridged the top and side window flanges and the house wrap with a self-stick waterproof membrane. They then folded down the loose house wrap at the top and sealed it to the membrane with tape.
Image Credit: Roger Beck **Ready for the deck** The first floor is framed with I-joists and OSB rim stock. Keeping stormwater on-site. Student workers fill a 6-ft.-deep drywell with stones after lining it with filter fabric. Downspouts from both the garage and house lead to the well via underground connectors in trenches. An overflow pipe goes under the sidewalk to the street, but it should rarely see use, as the adjacent rain garden should handle the most extreme storms.
Image Credit: Roger Beck **It helps to have good mentors.** Multiple engineering and design firms offered their expertise to help a group of high school students and volunteers build this simple but effective new home. The insulation and air-sealing details used common materials but required serious commitment and cooperation to execute well. Grabbing Ohio's first LEED-H Platinum rating implies that they were pretty successful.
Image Credit: Toshi Woudenberg A sustainable suburban garden takes shape. Drought-resistant native wetland plants begin to take root in the new garden. More ornamental plants mean less lawn (although the chosen variety of turf requires no irrigation and little mowing). Both reduce paved area, thereby helping filter pollutants and protect the watershed.
Image Credit: Roger Beck **Expected to provide big savings.** *HERS rating: 27.* This simple but attractive two-story house looks like very much its older neighbors but combines time-tested enclosure details with solar hot water and electricity in a very affordable package. ** A speed square helps keep the cut clean** If you have trouble cutting a straight line, use a C-clamp to hold your speed square in place for use as a saw guide.
Green building experts and high school students partner to put a solar powered home on a Columbus, Ohio, infill lot
Betsy Pettit, GBA advisor and consultant to this project, points out that we’re in a dynamic time. “Push the envelope,” she remarks, “because what’s new now will be normal sooner than you think.”
In 2005, when this house was conceived, it was novel in many ways. It sometimes puzzled the building inspectors, who looked to their code and wondered if solar thermal actually needed a permit, and if so, was the inspection for plumbing or electric? Did the solar preheat storage tank actually satisfy Manual J? But by now, this house, built as infill for an older Columbus neighborhood, reflects standard green practice: It’s built on a 2-ft. module; it has advanced framing, thoughtfully sized HVAC, and both soy foam and exterior XPS insulation; PV panels on the roof send energy back to the grid; it has polyethylene-wrapped, isolated footers for water protection; and it scores a 27 on the HERS index.
Weekly Newsletter
Get building science and energy efficiency advice, plus special offers, in your inbox.
And yes, it was built by a group of teens as part of a program initiated by builder Roger Beck, technology education teacher at a suburban Columbus high school. They became so engaged in the project that they worked weekends and vacations, in snow and subfreezing temperatures.
Partnerships make the abstract tangible
Beck started a hugely successful foundation called Home B.A.S.E. (short for Building Academic Skills and Experiences), which guides students in building affordable homes. So far, the program has put up 11 such homes. This one became part of the housing initiatives of the Columbus Housing Partnership (CHP), following previous collaborations with Habitat for Humanity. Beck also pulled in partnerships with contractors, building materials suppliers, and consultants (such as Pettit of Building Science Corporation), and received generous donations of all kinds. Building America funding from the U.S. Department of Energy even found its way into the mix.
For this project, Home B.A.S.E. gave 19 high school seniors firsthand experience in building, collaboration, and larger social issues. So far, more than 20 tours have influenced other local building projects and inspired groups from intern architects to the NAHB, from the National Church Residence Council to the Master Gardeners of Franklin County.
Thinking inside the box
Though it’s green, the house is still standard construction—and traditionally styled. “This is such a great renovation!” is the most common compliment about it, even though it’s a new build. Contractors didn’t have to go out of their way, or even out of their comfort zone, to provide services—although they learned a thing or two themselves.
It was built with off-the-shelf products, systems, and processes. These included flooring, tile, doors and triple-glazed windows, insulation, Tyvek house wrap, self-adhesive waterproof membrane, and carpeting (a remnant from a local hotel job). It’s got a poured-concrete foundation, wood framing, clapboard, and a pitched roof. What made the difference was that these elements “were used in concert with each other, like a system,” says Beck, “along with off-the-shelf human intelligence.”
“We met all our goals,” says Josh Lloyd, an LEED AP intern architect who volunteered on every aspect of this project. “And it feels good to be in because we have excellent indoor air quality and spectacular energy savings.”
Getting to LEED
LEED-Platinum certification came about because using the materials and people systematically “put them over the top,” says Beck. Joe Sullivan, design architect of record, modified typical CHP home plans in consultation with Pettit and Beck—for example, by stacking the plumbing—to fit their green building scheme. Lloyd worked out the details with BSC and Beck and rolled out a detailed set of construction documents. They reconfigured the framing from 2x4s on 18-in. centers to 2x6s on 24-in centers, eliminated double top plates, and used 94-1/4-in. studs. With fewer cuts for lumber and flat goods, .86 lbs./sq.ft. of residue went to the landfill, despite becoming the Dumpster for other community projects. The team also beefed up the insulation to R-31 and added subslab insulation and flashing.
The schedule slipped, so prefabrication became part of the mix. This gave the kids a chance to really think about how things went together. The class framed the walls off-site in the high school shop. On site, they wound up wearing caulking because they sealed everything: sills, band boards, electrical boxes, and ceiling penetrations. They learned how back dams on windows greatly reduce water infiltration, and why using fiberglass-faced drywall deprives mold of a food source. They replaced the backdraft dampers in the bath fans with spring-loaded versions to improve the heating system. And although it didn’t count toward LEED, the entire project was run on power from portable solar cells.
Lessons Learned
“Amazing things can happen when someone quietly makes up their mind to do something for the next generation,” says Pettit in praise of Beck's dedication. Pettit herself became involved through family connections and her roots in this town. For Beck, this project is first and foremost a social enterprise—the fact that it’s a house is almost incidental. His student builders learned more than isolated things like recycling or using the car less; they acquired a deep interest in larger, crucial issues like energy conservation, environmental responsibility, poverty, and an immediate sense of one's personal ability to affect them. Some have gone on to demonstrate this in remarkable ways.
Sullivan credits this project with introducing his firm to green practices that it now embraces, including advanced framing, the use of light-colored roofs, and total-cavity fill insulation. He echoes others when he observes that they learned that green design doesn’t have to be its own aesthetic—it can blend right in. Beck learned that builders are generally experts at what they do, and if they shift their focus to a greener way of doing things, it comes out just as well that way.
Lloyd is spearheading a statewide competition for affordable green homes. Contract Lumber, which provided framing materials, is now carrying FSC wood. Even CHP, initially worried that 2x6 framing would result in higher costs and that maintaining the home would be unwieldy, is now offering green affordable homes as part of its portfolio. “It’s important for projects like this to be designed well," says Sullivan, "because they’re so price-sensitive.”
The great blog that chronicles this build concludes, “Our building partnership believes that managing that risk should reduce the probability of: being hurt financially by rising energy prices, not being able to afford the aggregate cost of the home over the life of the mortgage, building failures, unhealthy buildings, and the effect of our consumption on our planet.”
Further Resources
Read more about this project at: homebase07.blogspot.com
General Specs and Team
Location: | Columbus, OH |
---|---|
Bedrooms: | 3 |
Bathrooms: | 2.5 |
Living Space: | 1495 |
Cost: | 150 |
Additional Notes: | **Project completed:** August 2008 |
Project initiator, manager, contractor, teacher: Roger Beck, Home B.A.S.E. Foundation Owner: Columbus Housing Partnership (CHP) Consulting engineers: Betsy Pettit, Building Science Corp.; Hasbrouck Engineering; Hoy Surveying Renewable energy consultant: Green Energy Ohio Architect: Joe Sullivan, AIA, Sullivan/Bruck Architects Project coordinator/LEED consultant: Joshua Lloyd, Associate AIA, LEED AP, Phillip Markwood Architects Interior design: Cynthia Grauduss, Grauduss Architecture and Design Major materials donors: The Contract Lumber Corporation, The Home Depot, Edward Mooney and Moses Insulation
Construction
Foundation: 4-in. concrete slab over 2-in. XPS foam (R-10); 8-in. poured concrete walls; 2x4 wood studs on flat and spaced 24 in. o.c.; 2-lb. soy-based spray-foam in bays (R-23)
Walls: 2x6 studs at 24 in. o.c.; 2 in. closed-cell soy foam and 31/2-in. dense-pack cellulose; 1/2-in. OSB sheathing, caulked and sealed; house wrap (Tyvek); 1-in. XPS foam, horizontal joints flashed; fiber-cement siding with air gap (R-31 total)
Windows: triple-glazed, U=0.19, (Gilkey)
Roof: 2x4 trusses at 24 in. o.c.; 14-in. cellulose insulation in attic; 3/4-in. plywood sheathing; waterproof membrane; standing-seam metal roof (R-49)
Energy
- Building envelope and ducts very tightly sealed (.15 NACH)
- Airtight drywall installation
- Comprehensive insulation: sprayed foam, cellulose, exterior and subslab XPS
- Fluorescent and LED lighting throughout
- Simple form and massing done on a 2-ft. module
- highest-rated Energy Star appliances
Energy Specs
Heating/cooling: 97% AFUE gas furnace (Bryant); 13.5 SEER air conditioner, 12 kBtu (Carrier)
Water heating: 40-gal. tank; 34,000-Btu evacuated-tube solar collector (Apricus); on PEX central distribution panel (Manabloc).
HERS rating= 27
Annual energy use: N/A (house is being used as a showcase for green sustainable construction for two years
Annual utility cost: $767 (estimated)
Water Efficiency
- Low-flow 1.1 gal./flush pressure-assisted toilets (Gerber)
- Low-flow faucets
- Xeriscaping, native plants, minimal turf
- Dry well (stormwater dissipation)
- Rain garden sized for 100-year event (virtually all stormwater stays on-site)
Indoor Air Quality
- All finishes, sealants, and glues low- or no-VOC
- Donated blemished wood flooring
- No-VOC carpet
- Recycled-content ceramic tiles
- Bath fan timers
- Fan cycler installed on fresh-air intake
- Cabinetry made from FSC lumber
- Radon-tight sump
- Tightly sealed ductwork
- Integral footing form/foundation drain
Green Materials and Resource Efficiency
Alternate Energy Utilization
PV: 2 kW, grid-tied
Certification
*LEED for Homes:* platinum (89 of 85 required)
*Energy Star:* 5+ stars
11 Comments
Appliances?
Great story. What appliances are these?
waste management
I appreciated the comment about being the neighborhood dumpster. We're building a home that we anticipate will be the first LEED certified home in Wichita KS and we're having the same issue. The day after we put the dumpster on site, we discovered someone had put a dishwasher in it! Did you have any sucess in eliminating that problem?
waste management
We've have similiar problems on our sites. We will typically tarp the disposal bins which stops most people but we've also had to actually build 2x4 and plywood lids that are secured to the bin over night. Check with your disposal bin supplier, they may have bins with their own lids.
But how much does it cost per foot?
Affordable is a variable term, because I've seen 'affordable,' modular homes that are very expensive. The article failed to give the price per foot for the home.
Price per square foot
Dan,
The price per square foot is listed in the specifications sidebar (5th line down). The cost was $150 per square foot.
Impediments To Progress
It is a shame that the Worthington School administrators and board members kept adding impediments for the growth of this program instead of seeking ways to make it work. Unfortunately lawyers and administrators have big egos and since it was not their idea they could not be bothered. This home won a prestigious national award that Worthington Schools should be proud of but since the students involved wore hardhats instead of football helmets, the administrators were too busy spending taxpayers money paving parking lots and hiring more athletic staff.
Low or no-VOC in Paints, Sealants, and Glue
(•All finishes, sealants, and glues low- or no-VOC)
Where do you find these products? I am having trouble locating products , that I feel are safe. I found a ceramic paint I'd like, but there are no distributors in Kansas. Most wood flooring has lots of glue etc. Would really appreciate your help. Thank you.
Response to Bernie
Bernie,
Check out our Product Guide:
https://www.greenbuildingadvisor.com/product-guide/cat/paints-coatings
Costs?
Is the $150/sf the actual cash outlay, or does it include what it would have cost to pay for all the donated materials and labor? If the former, then the true cost to replicate the project would be significantly higher...
Costs?(2)
...reason I ask is:
1. I'd love to do something similar, but...
2. ...considering the current housing market: Zillow's got ~1000 homes for sale in Columbus at ~1500sf for <$150sf, most under $100, and as low as $26-$50/sf. You could do a heck of a lot of air-sealing, insulation, new equipment, and solar, for $186,000...
Not that I want the current crisis to suspend all innovative new construction, but it would be interesting to compare the great project outlined above to a LEED-platinum deep retrofit (with student labor, (volunteer?) experts, donated products? etc). I've seen at least one deep retrofit profiled on this site that ended up being more expensive than building new, which is really disappointing...there must be a better way...
Response to David Gregory
David,
You make a good point. In many parts of the country right now, existing houses are being sold for much less than the cost of building new, due in part to the huge number of foreclosed homes that are still on the market. In such areas, buying an existing home and fixing it up probably costs less than building new.
Log in or create an account to post a comment.
Sign up Log in